Paint to Sample.
Welcome to the world of colours.
911 GT3 (2023): Fuel consumption* combined (WLTP) 13,0 – 12,9 l/100 km, CO₂ emissions* combined (WLTP) 294 – 293 g/km, CO₂ class G , CO₂ class combined G
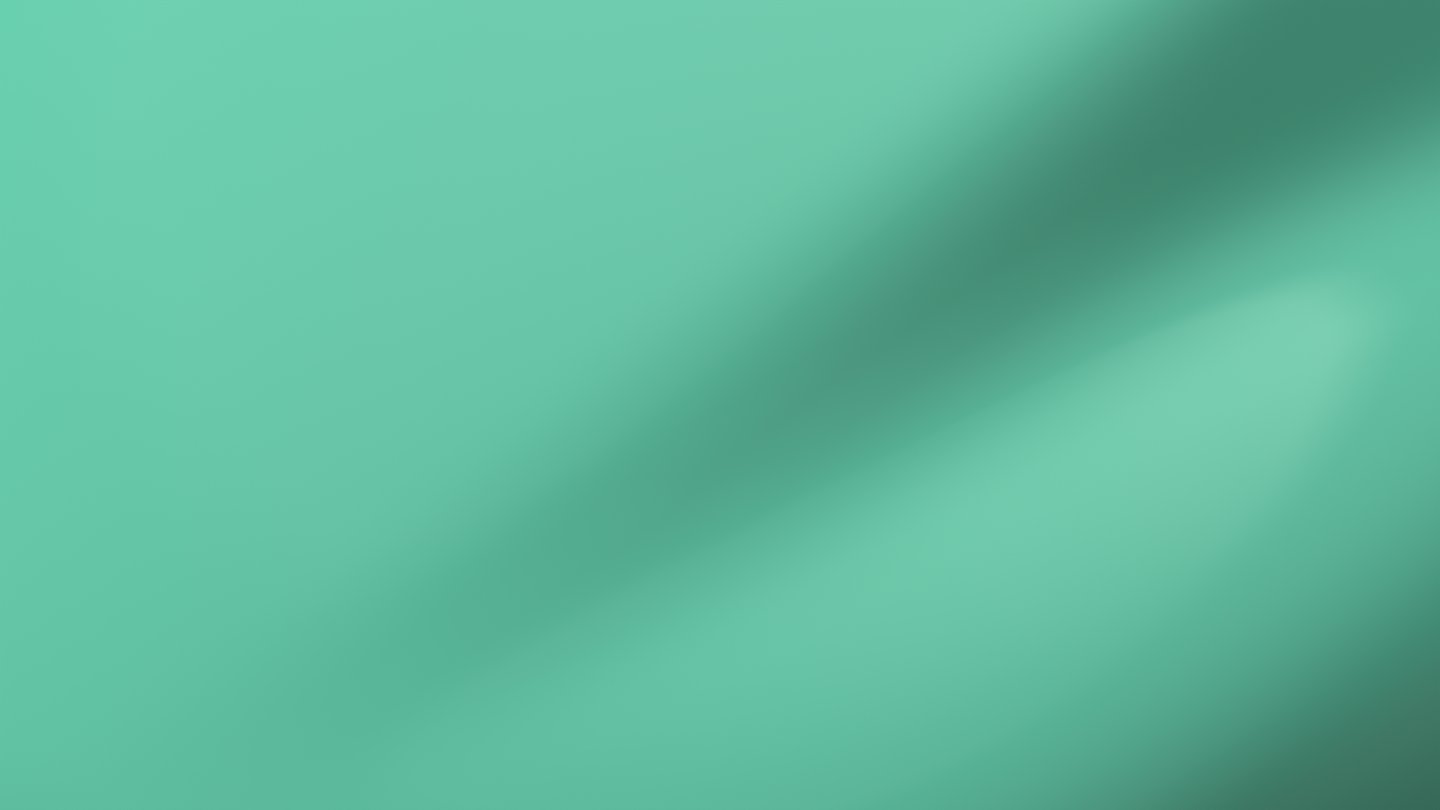
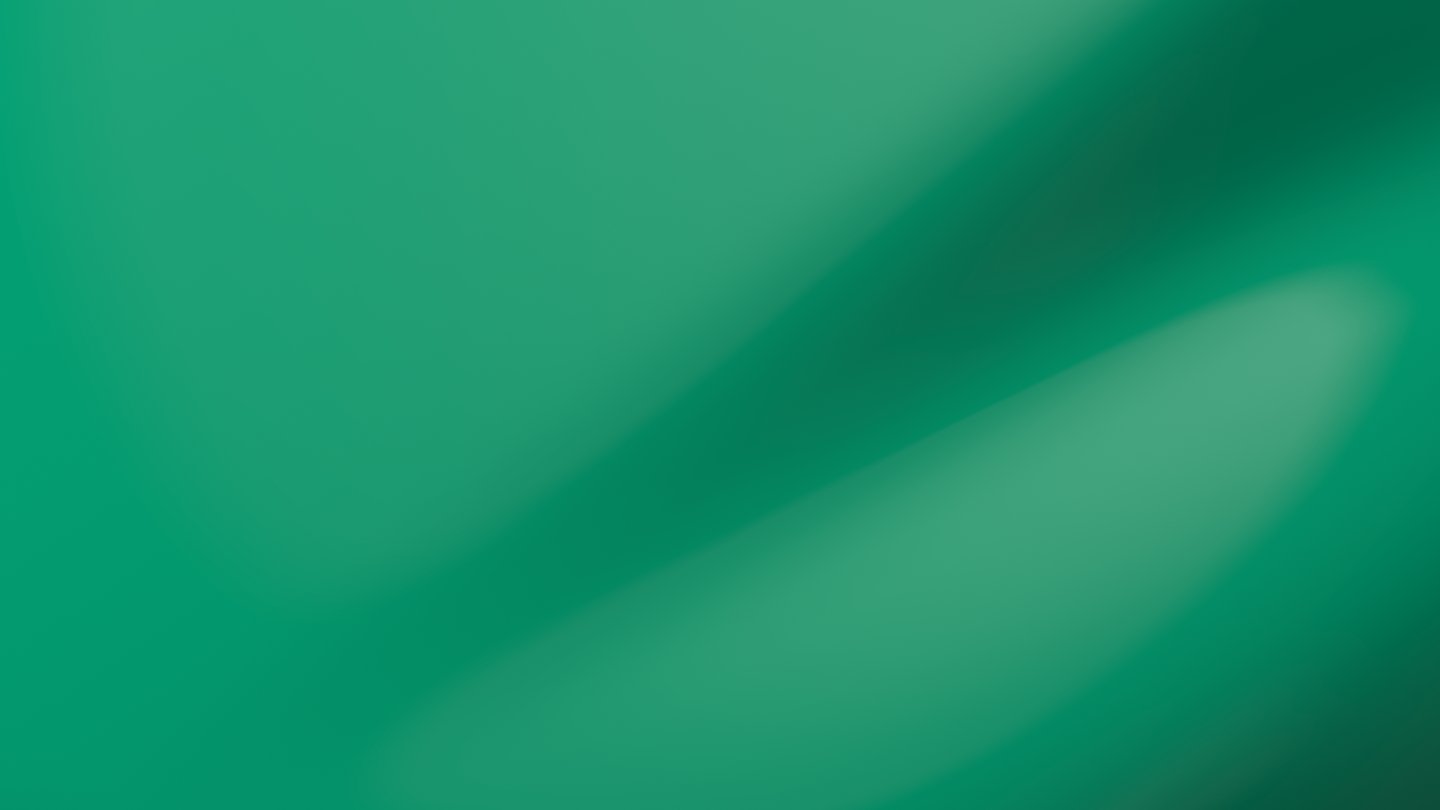
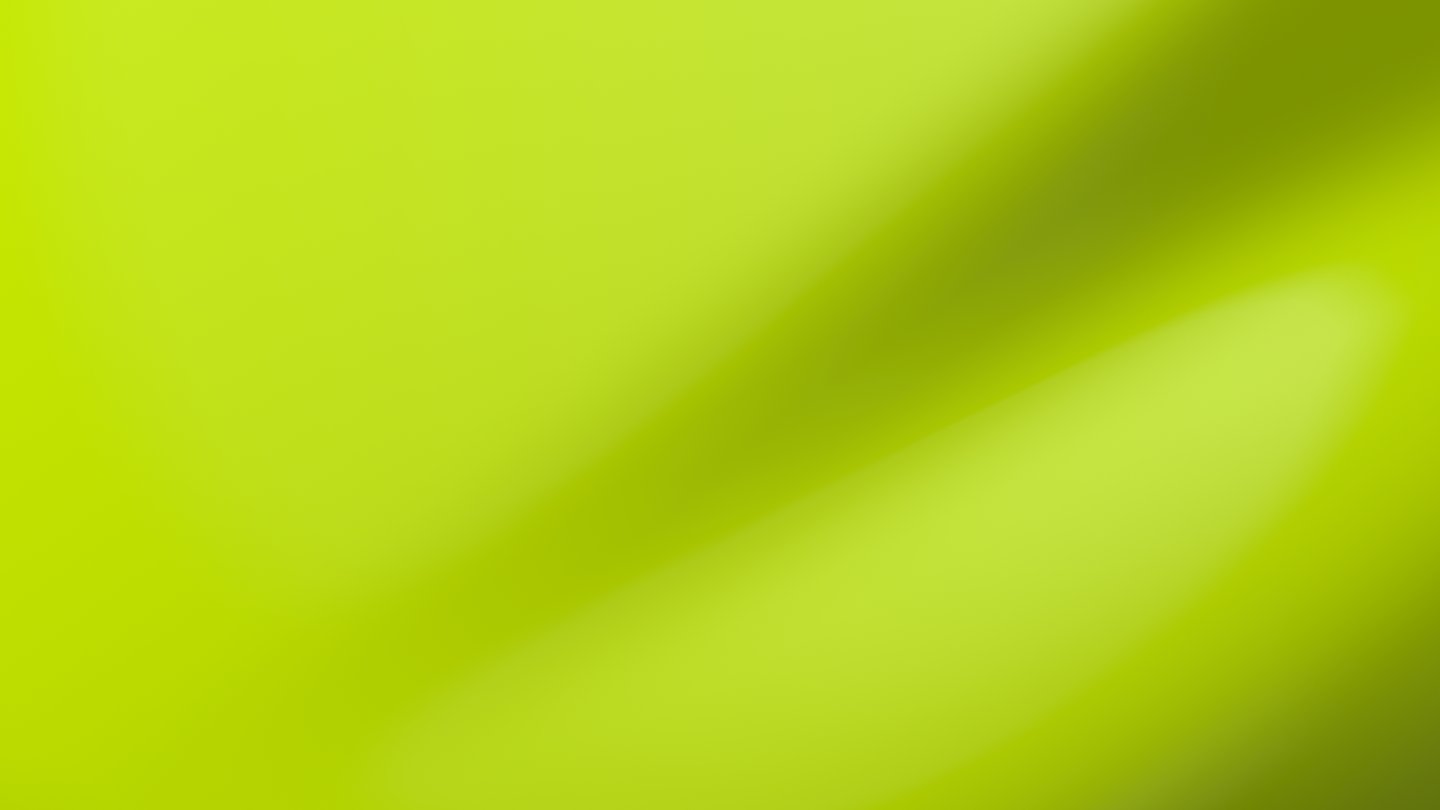
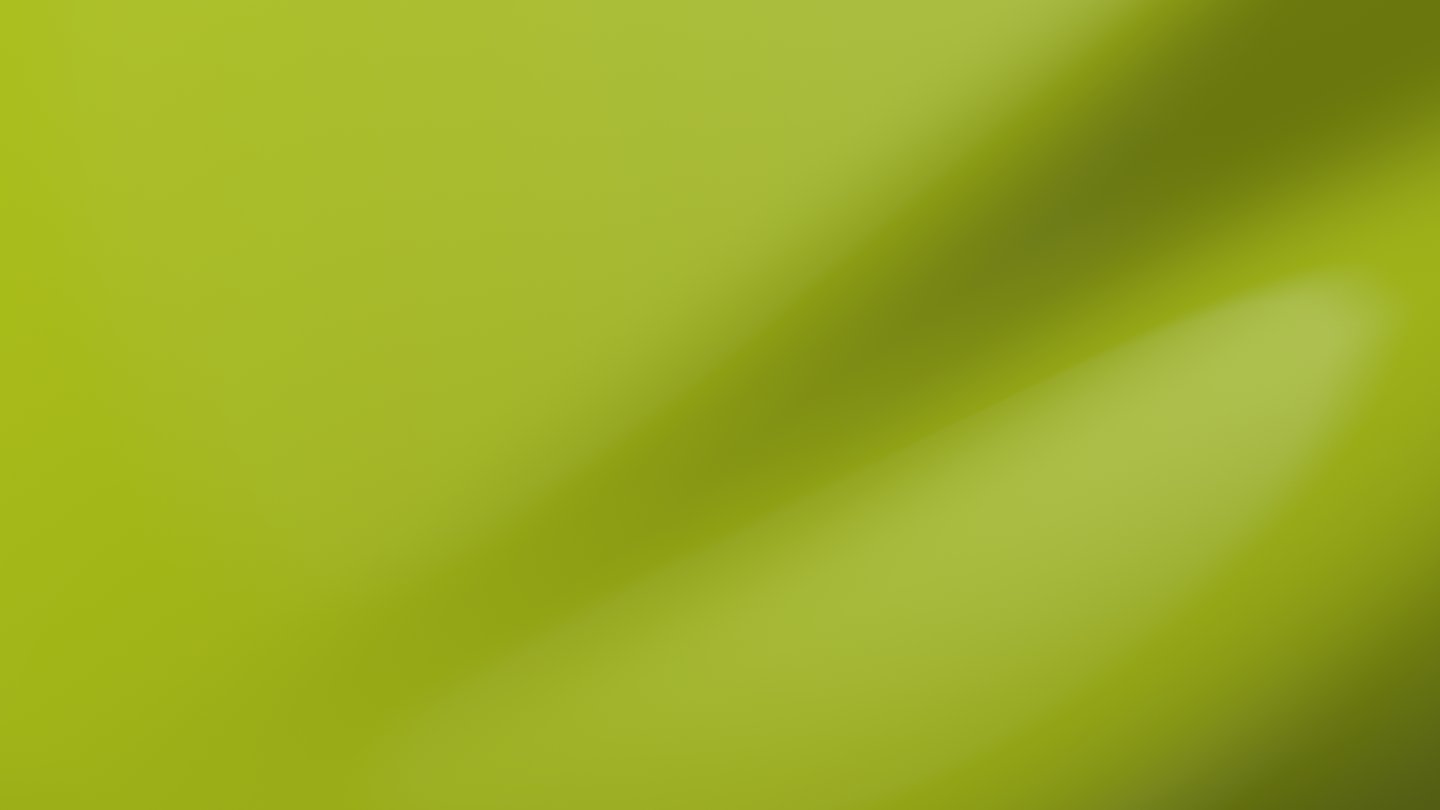
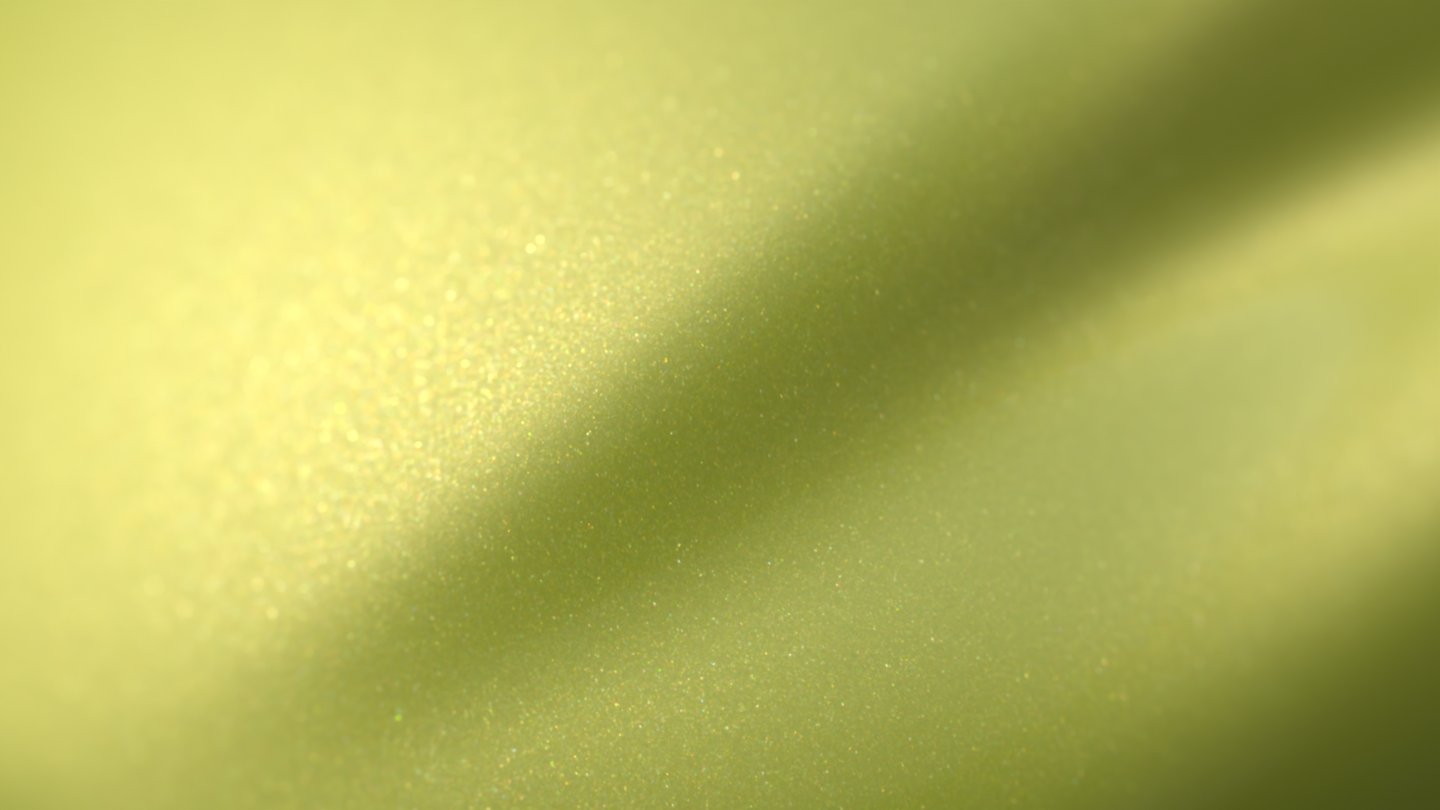
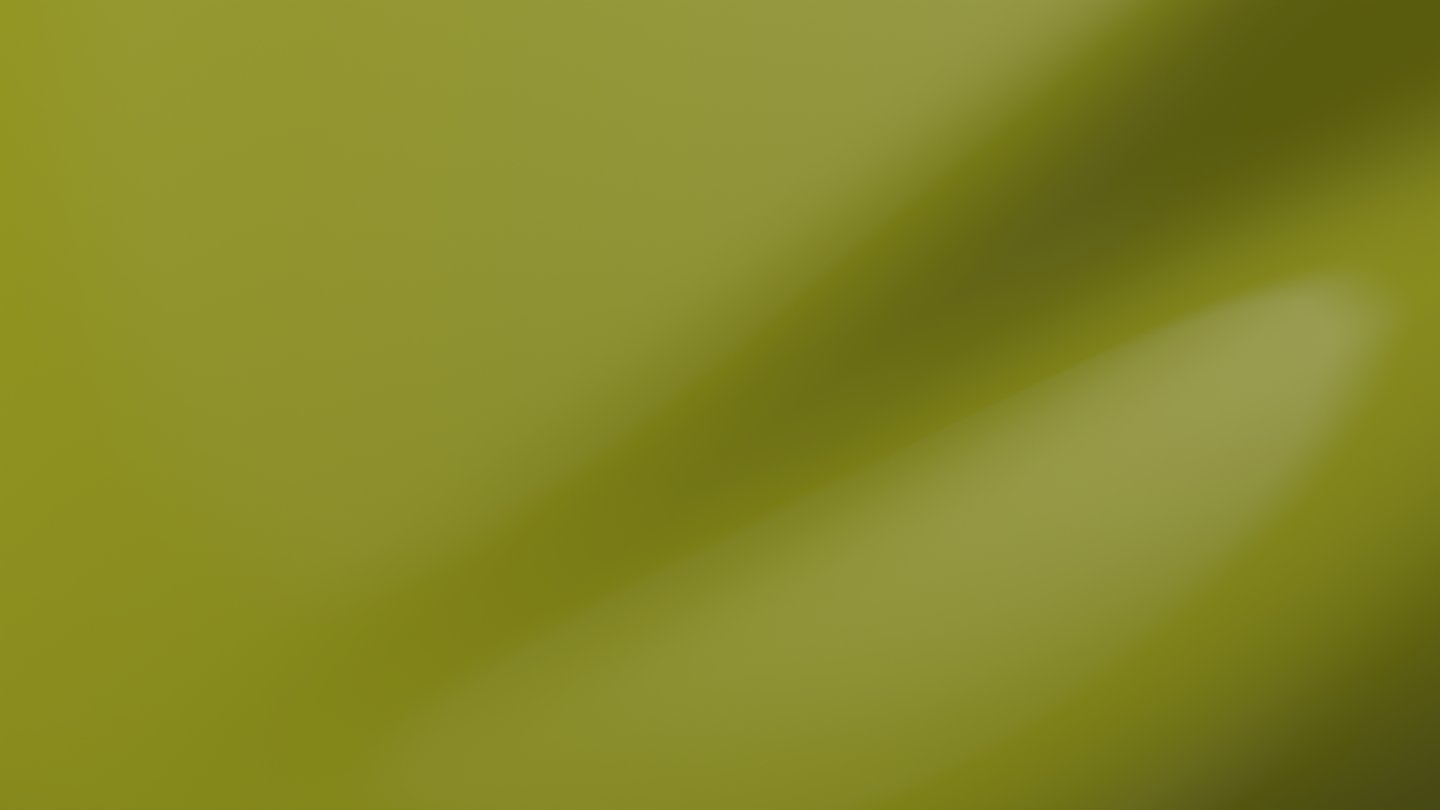
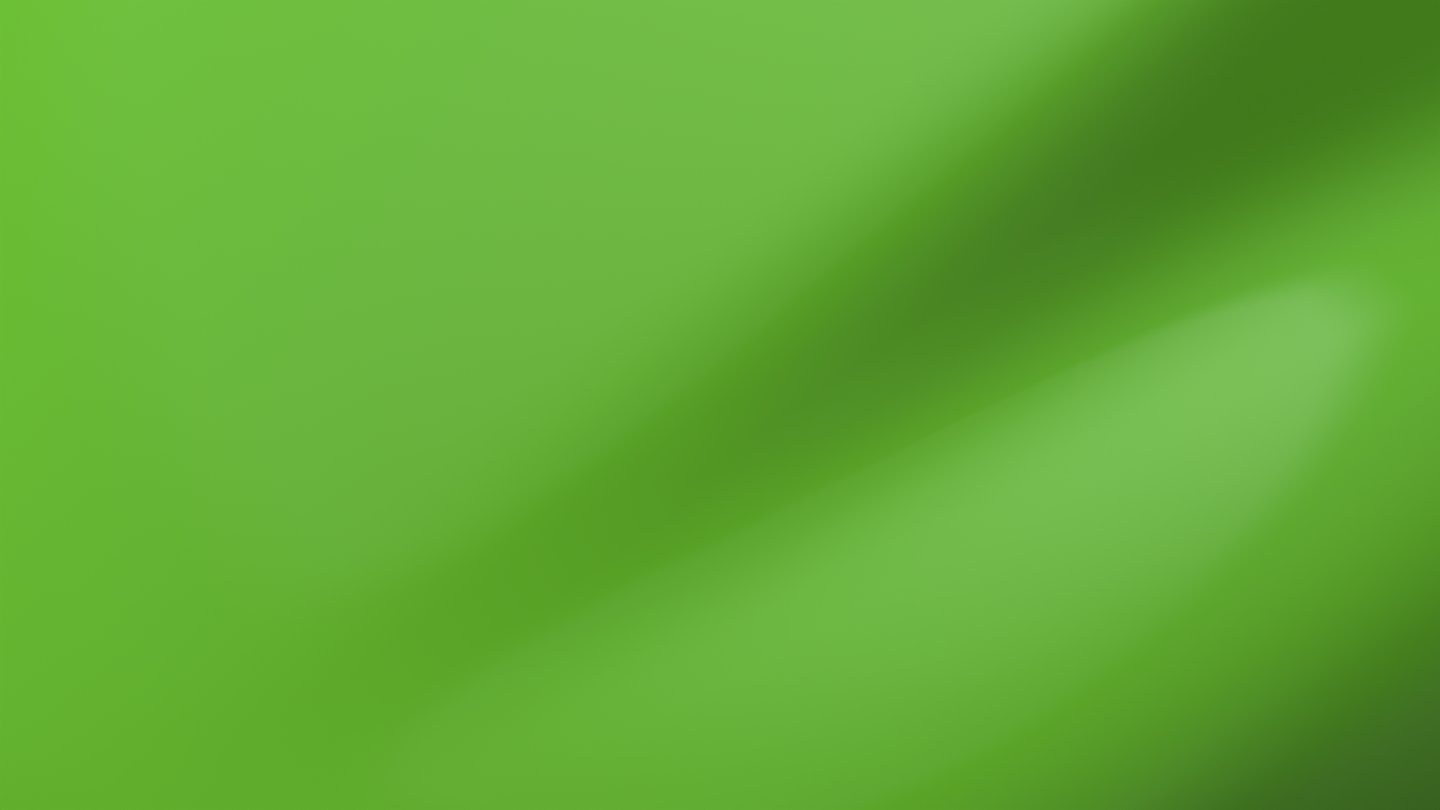
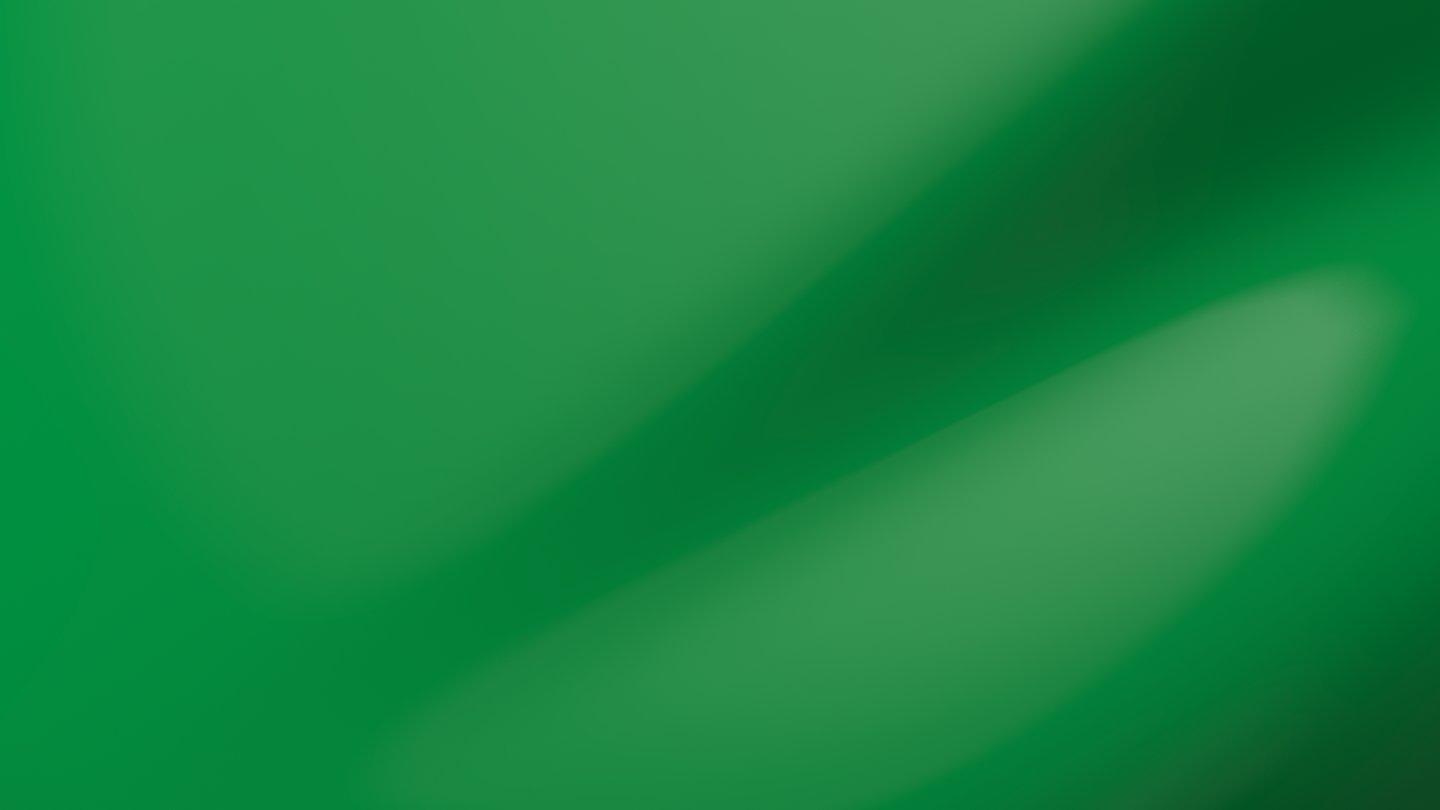
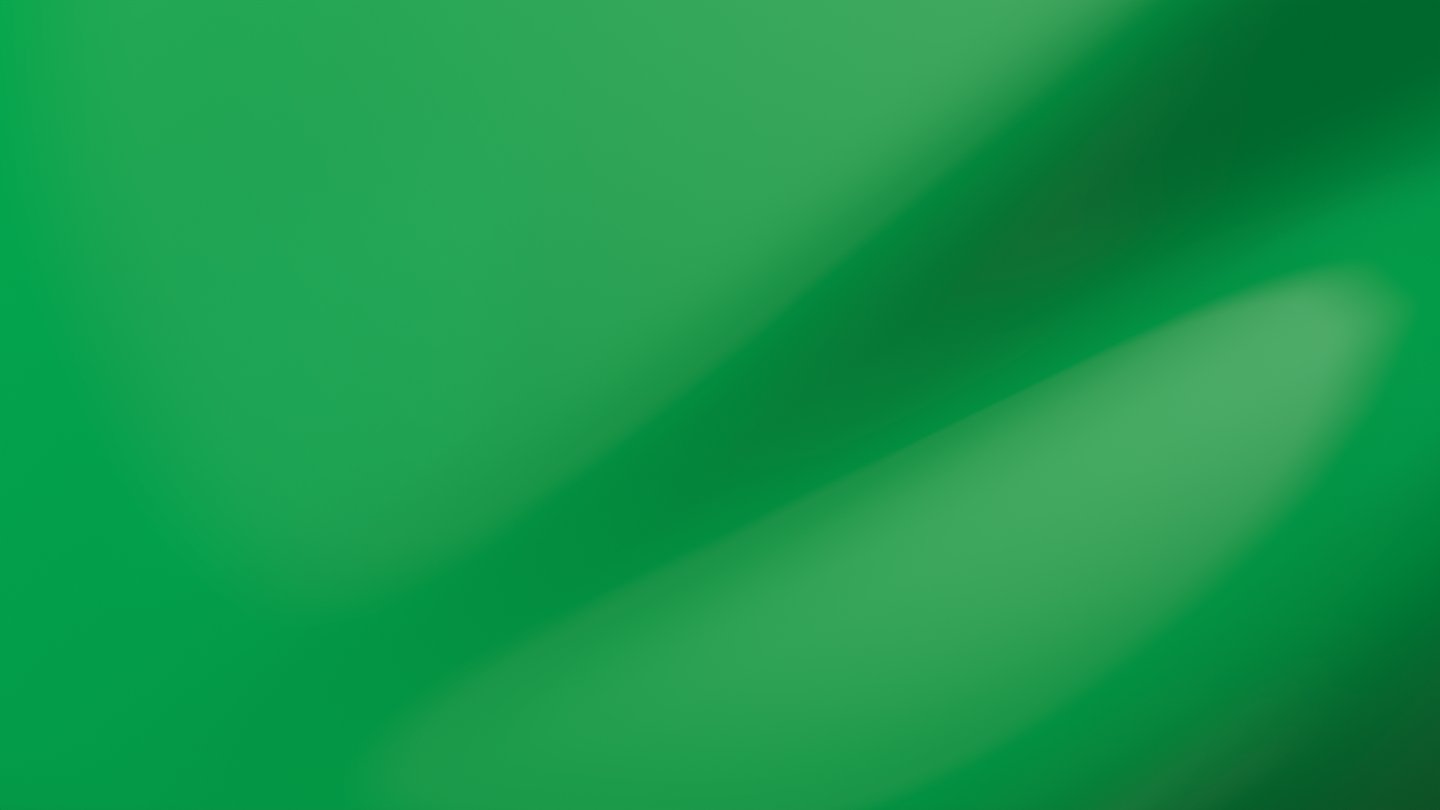
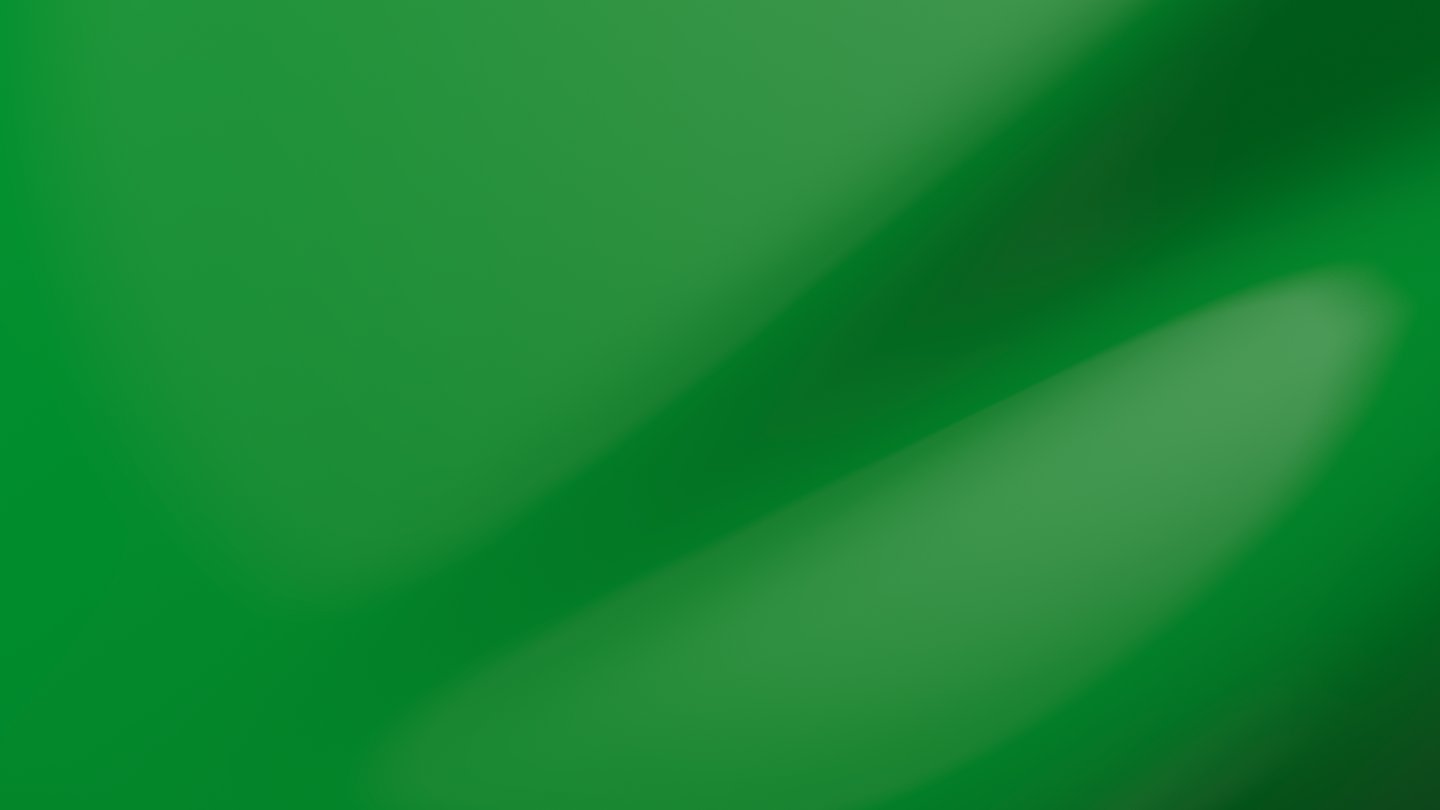
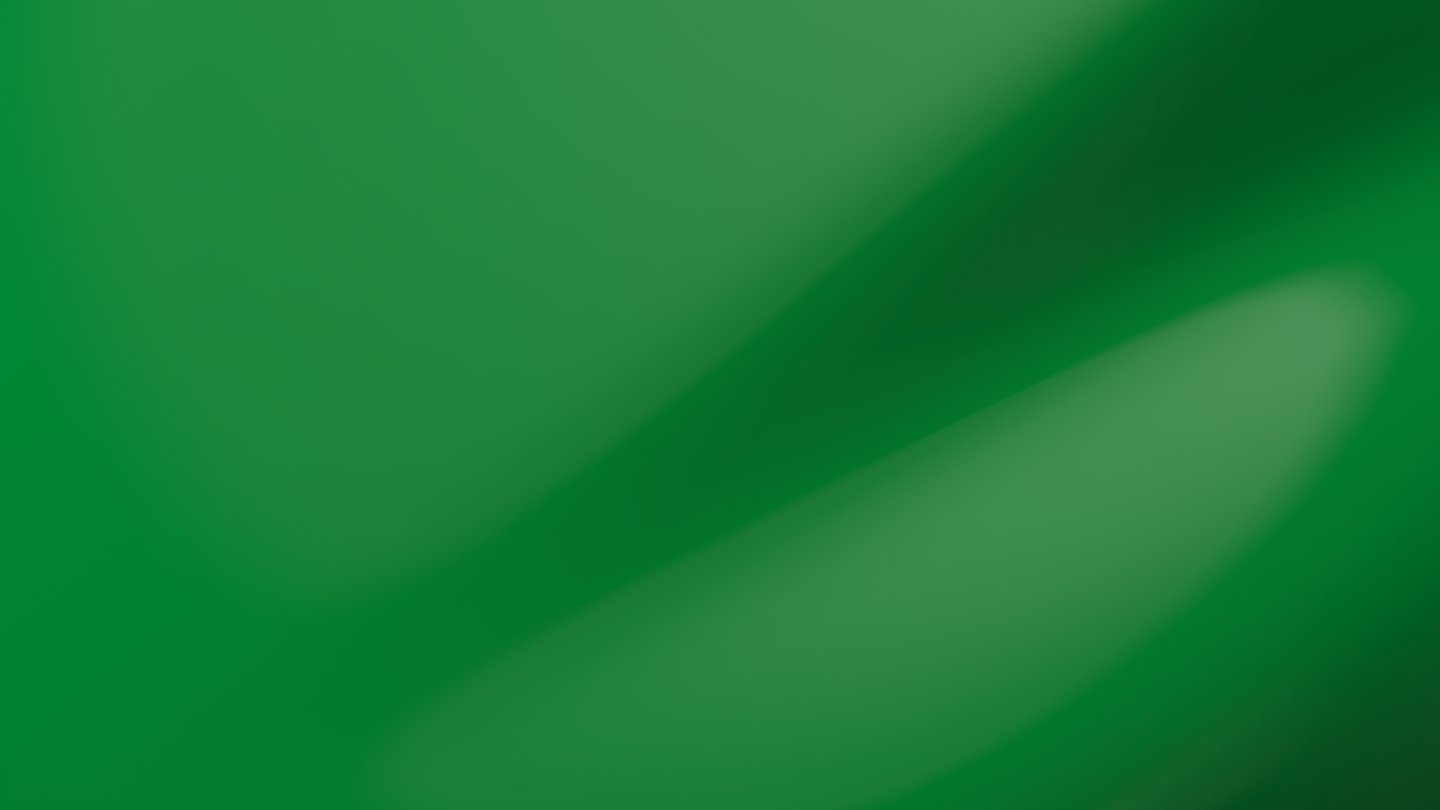
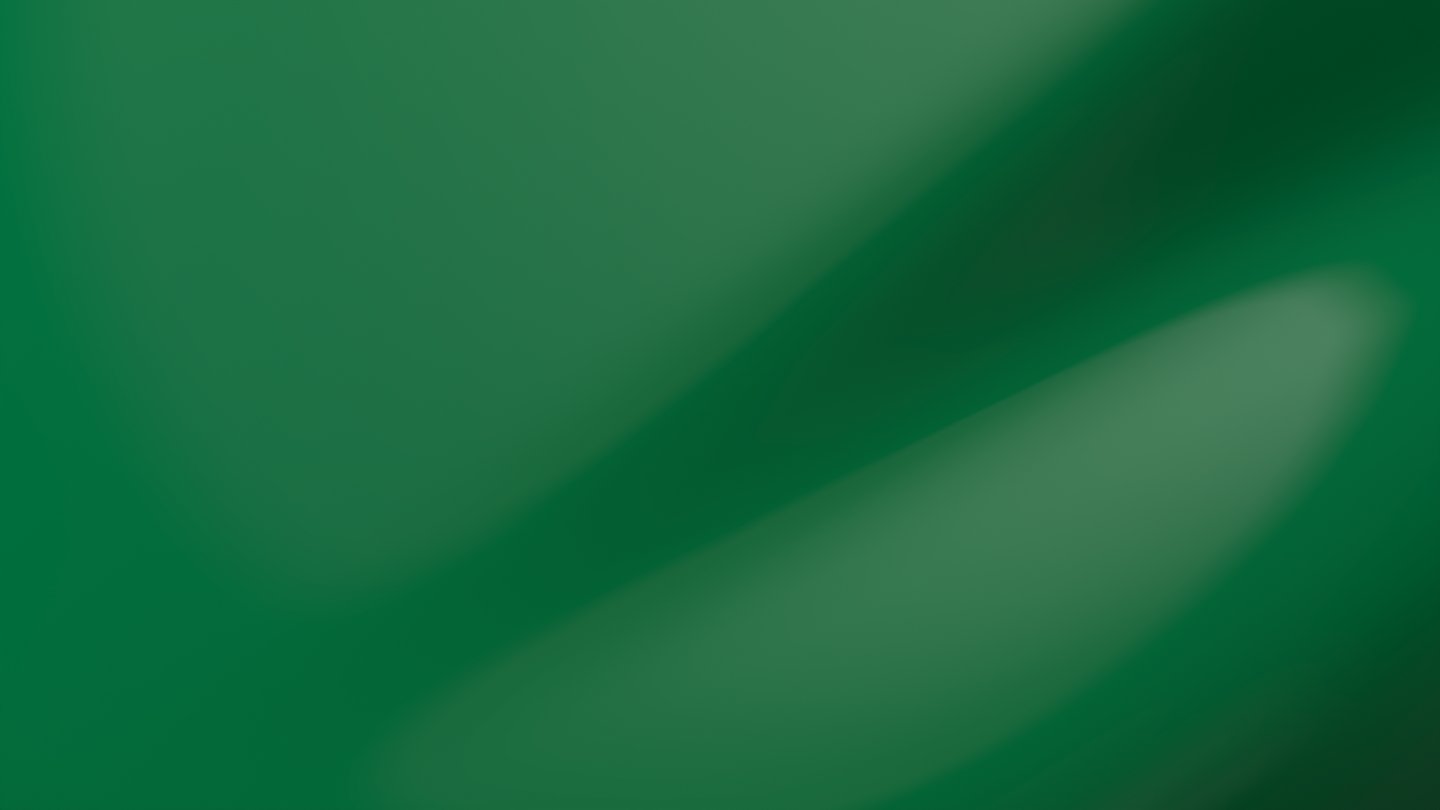
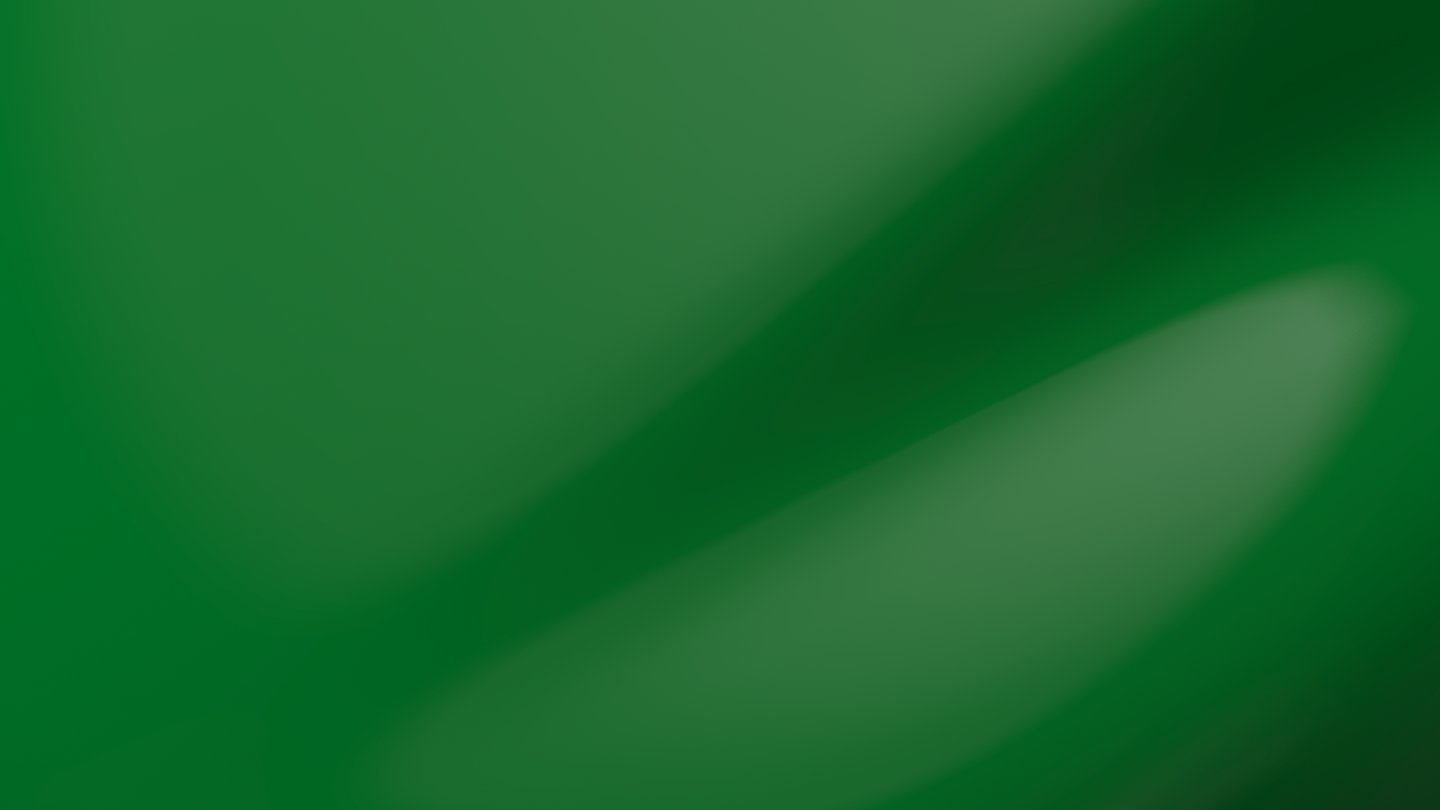
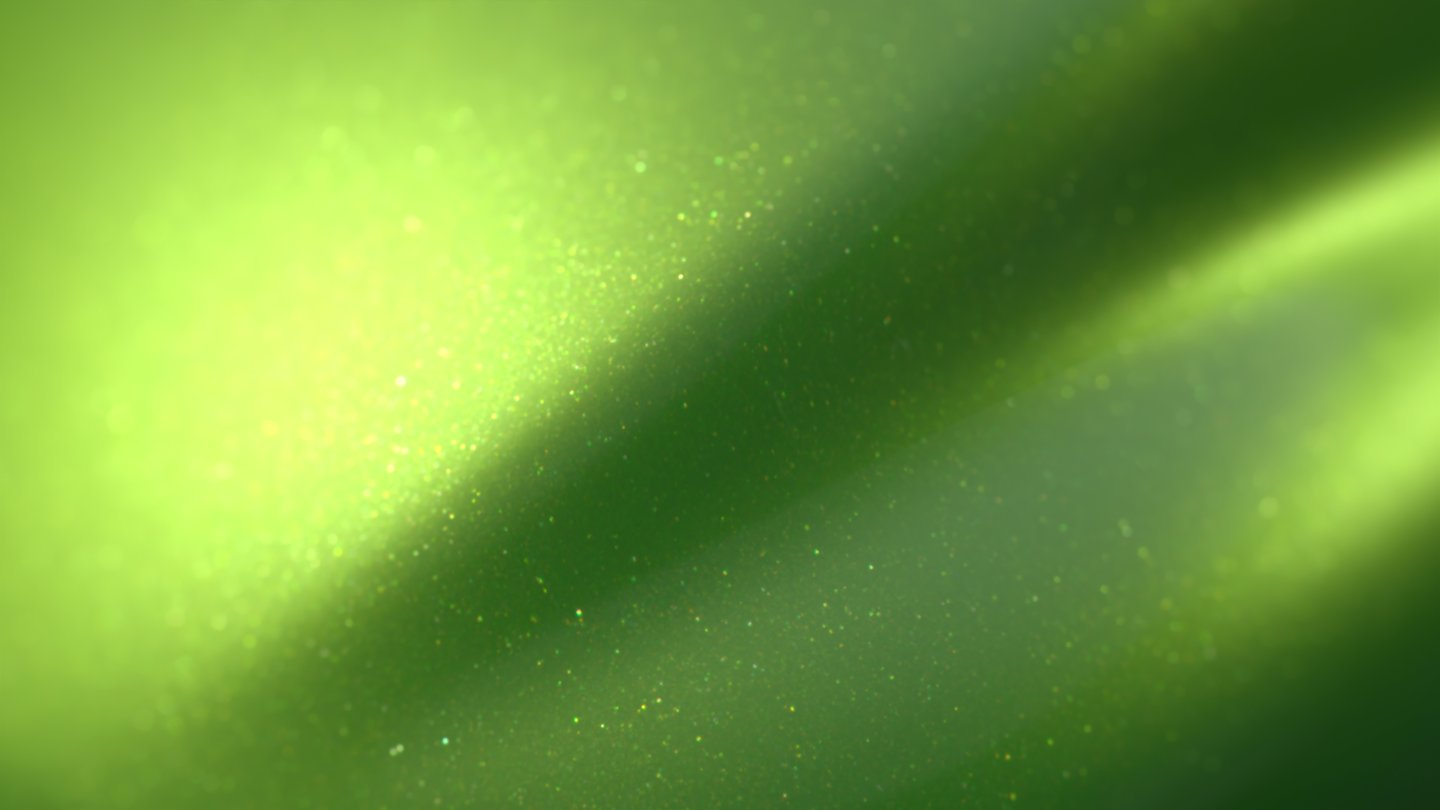
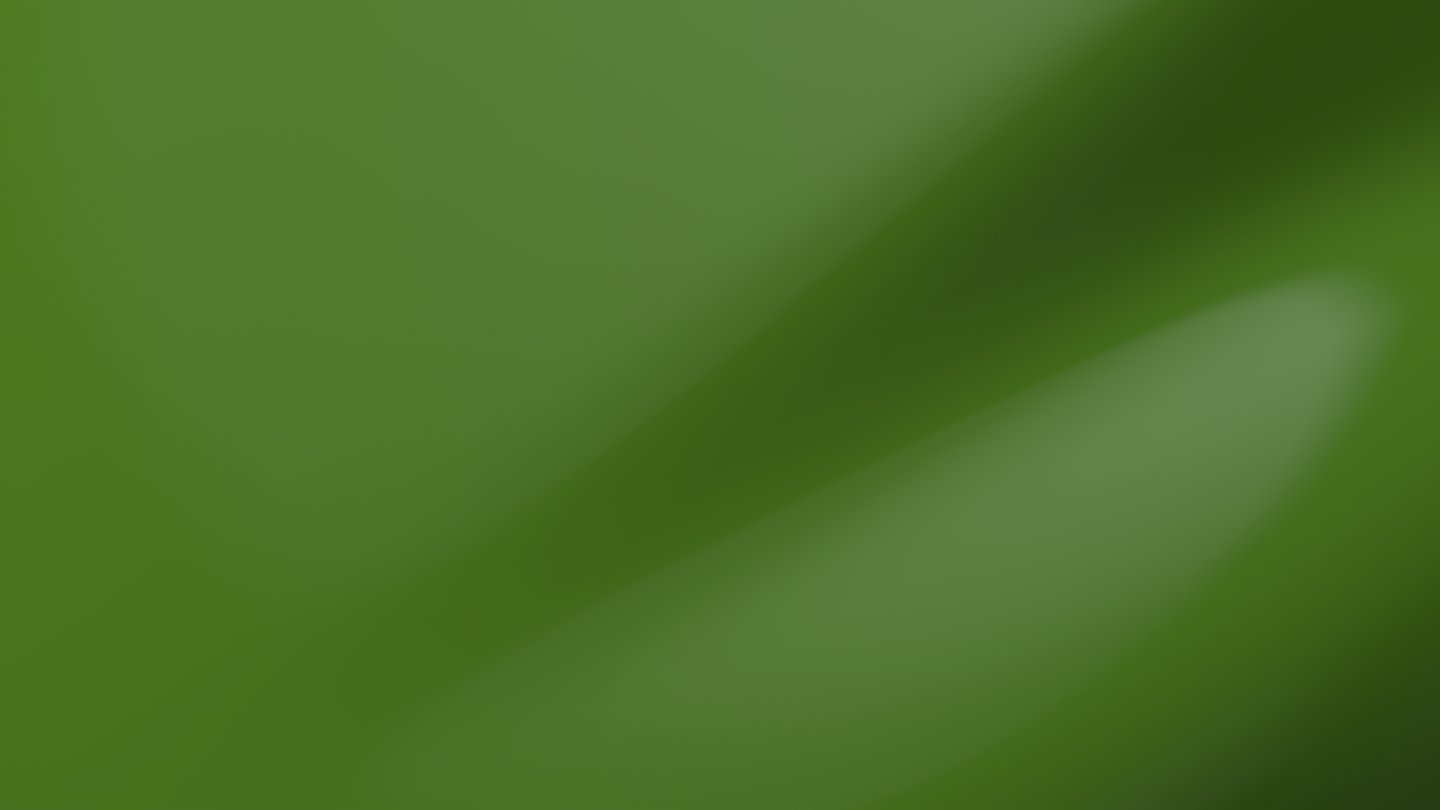

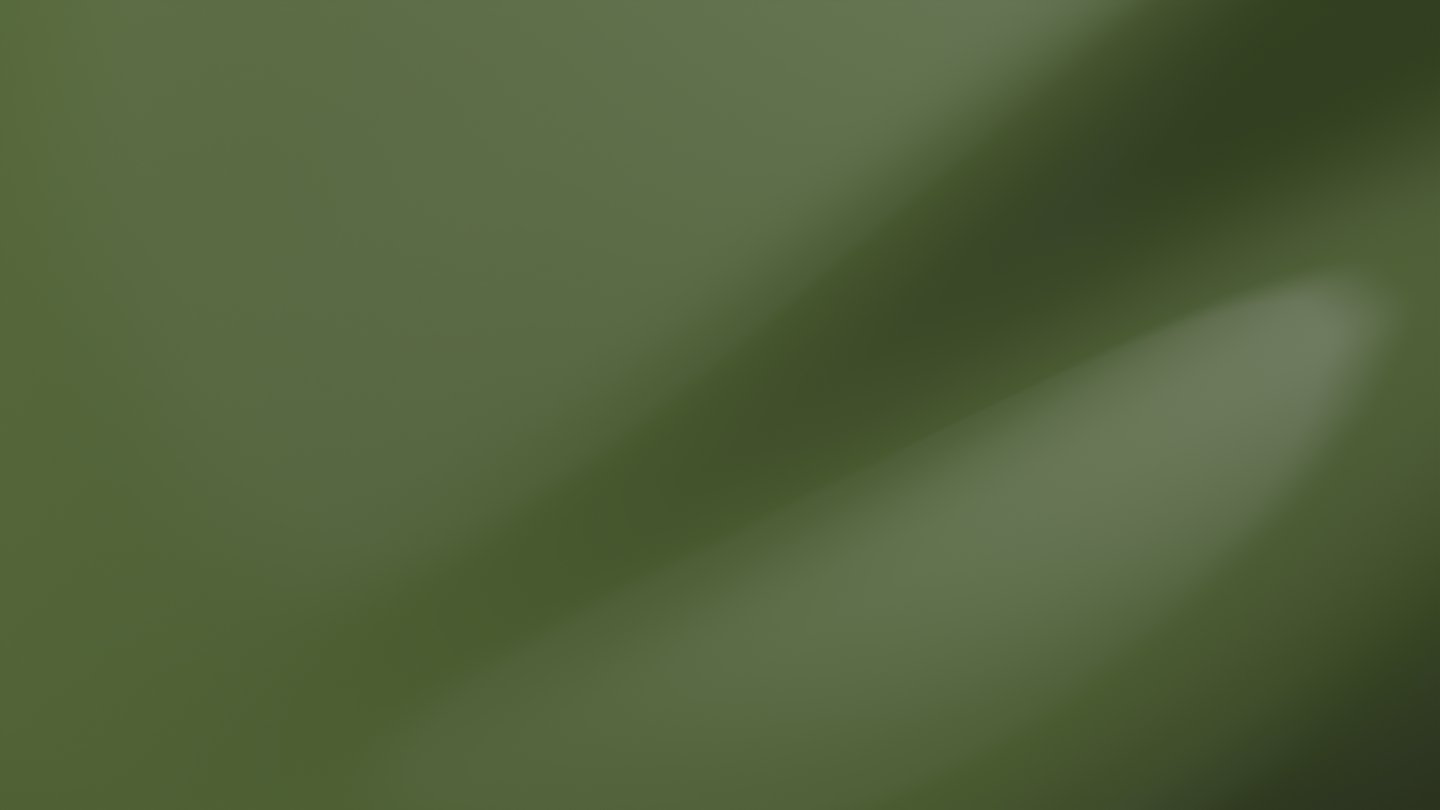
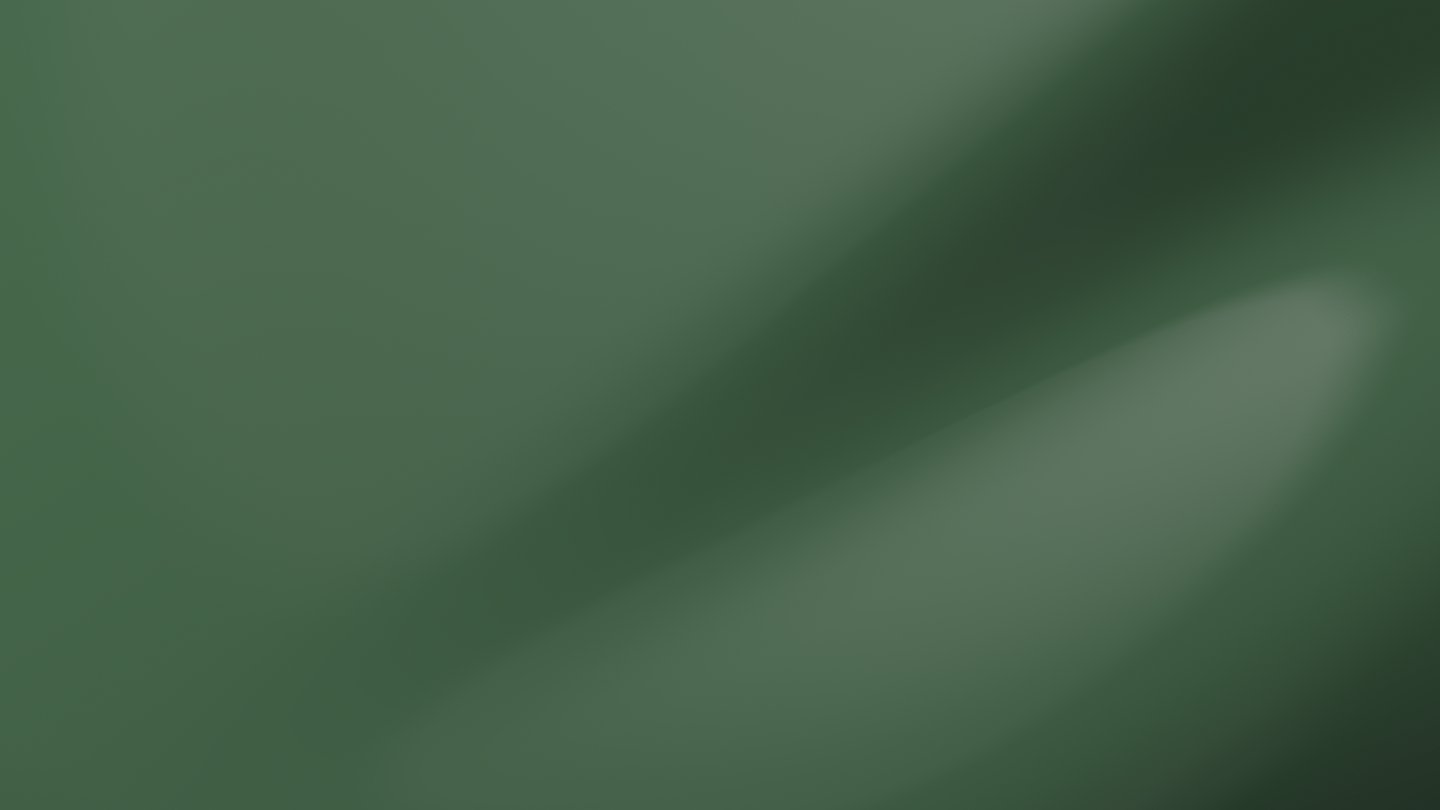
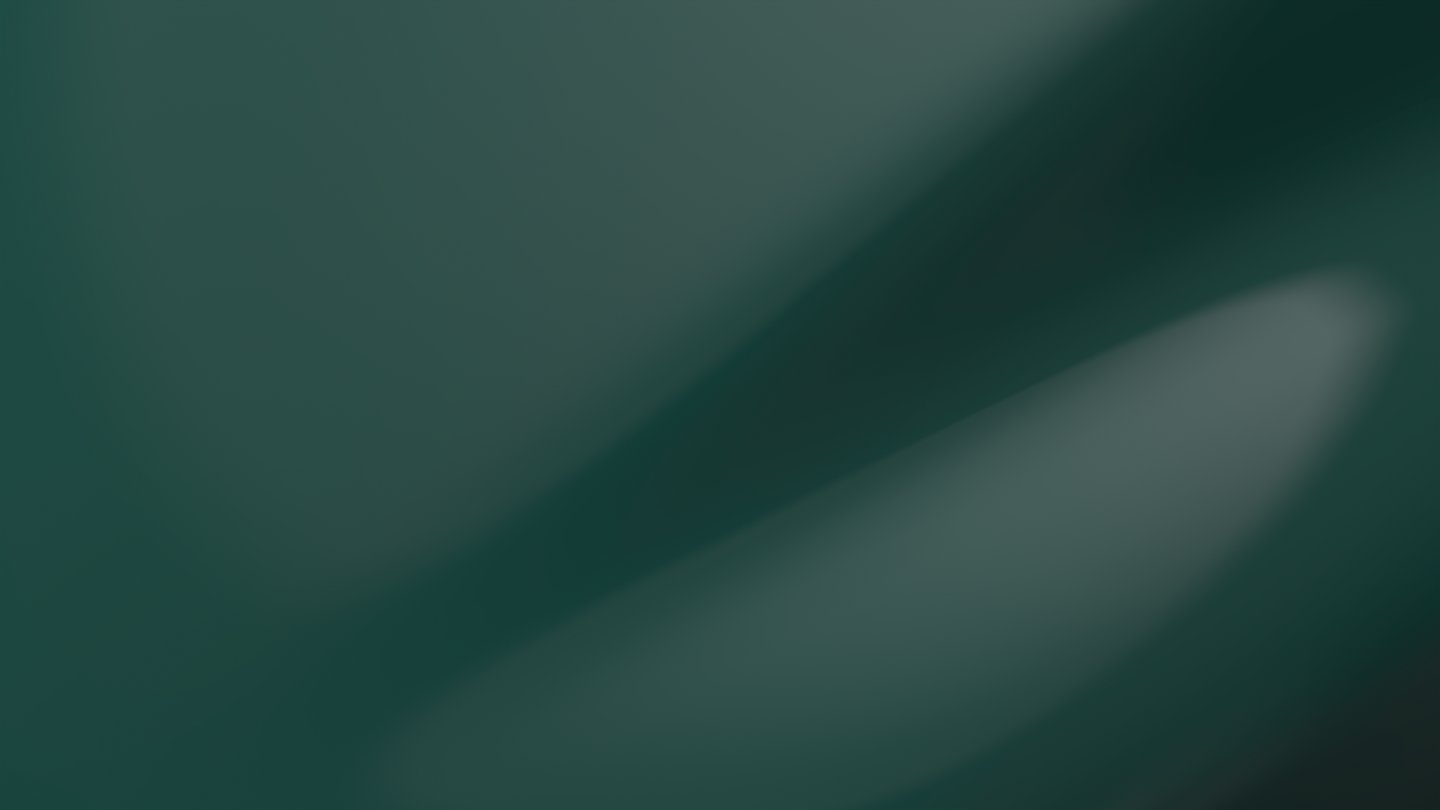
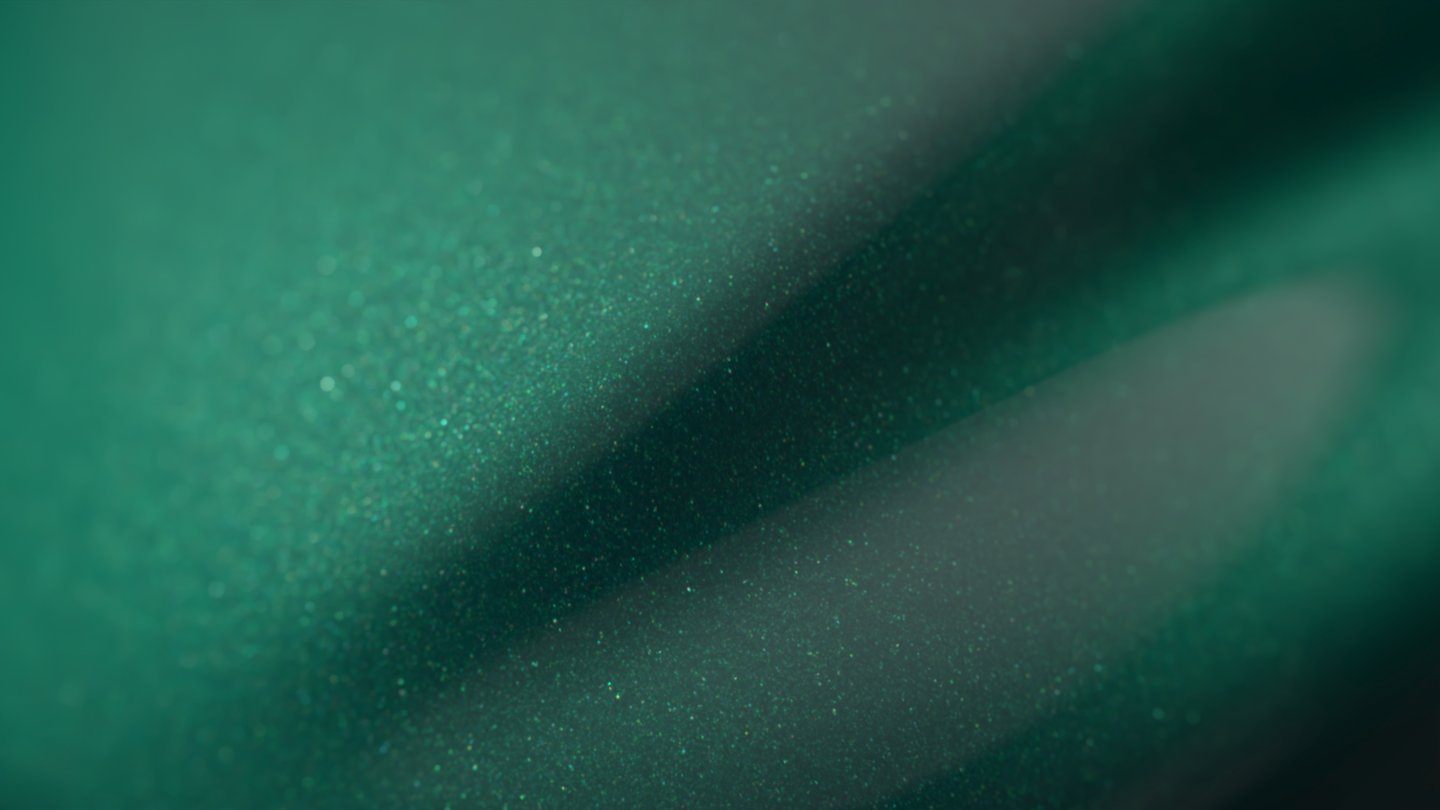
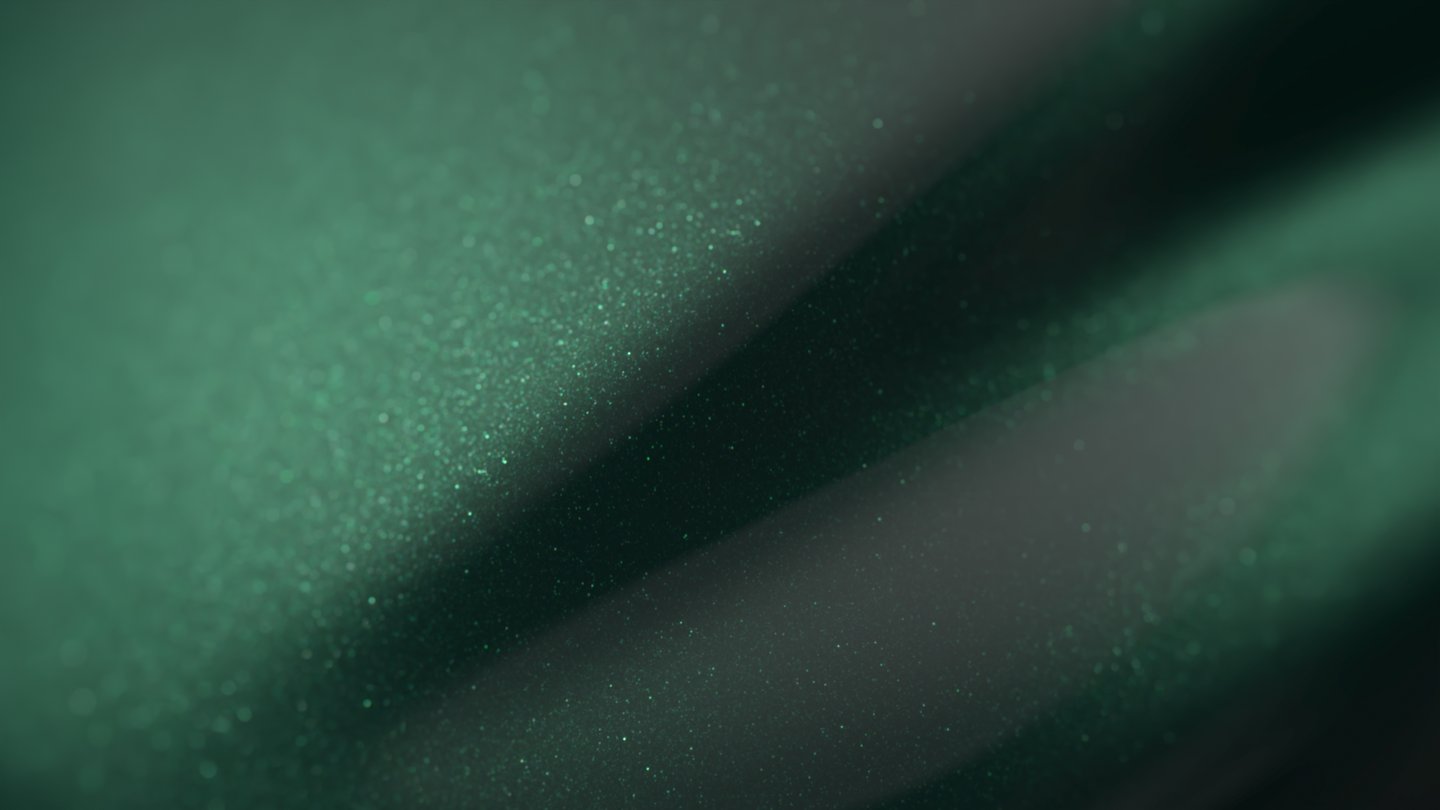
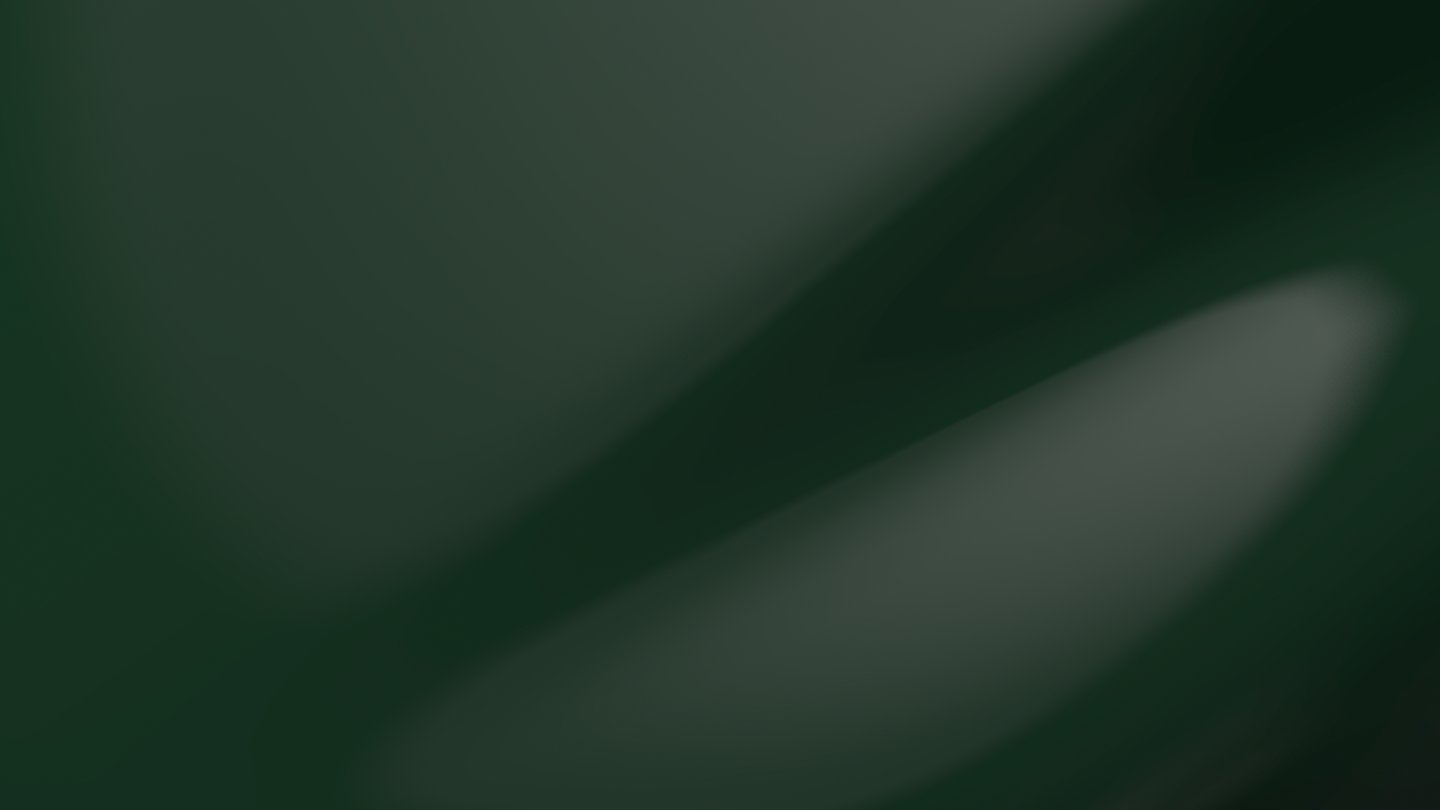
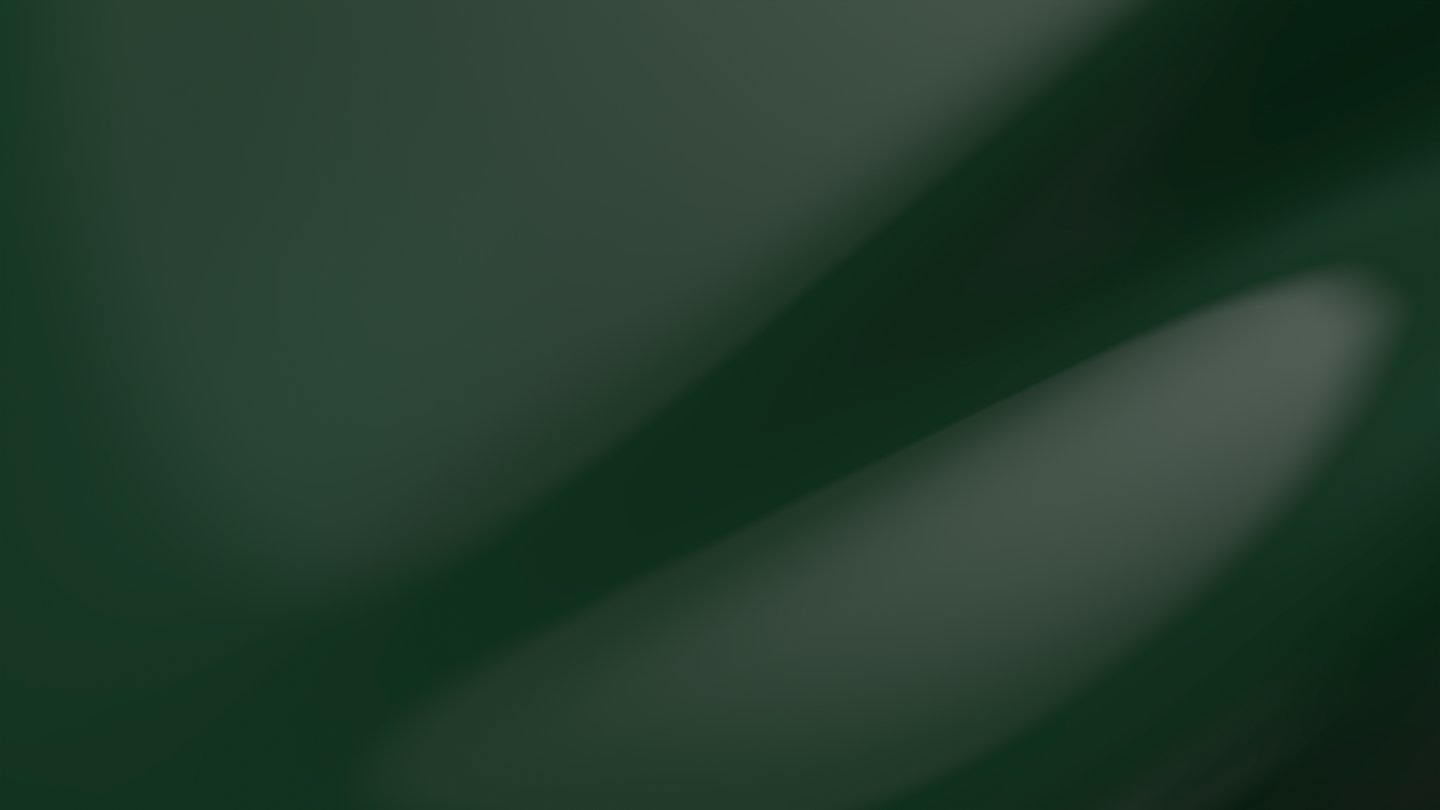
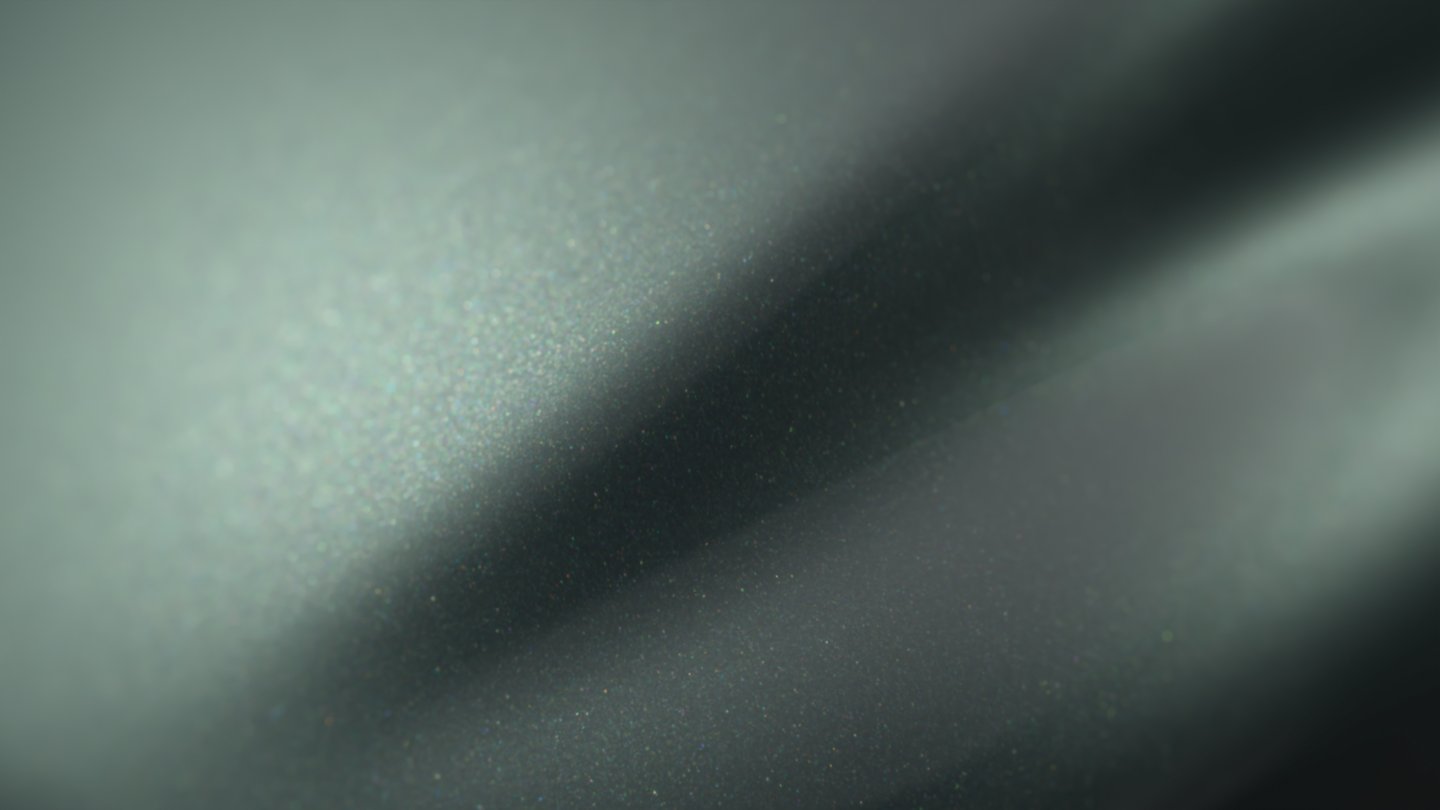
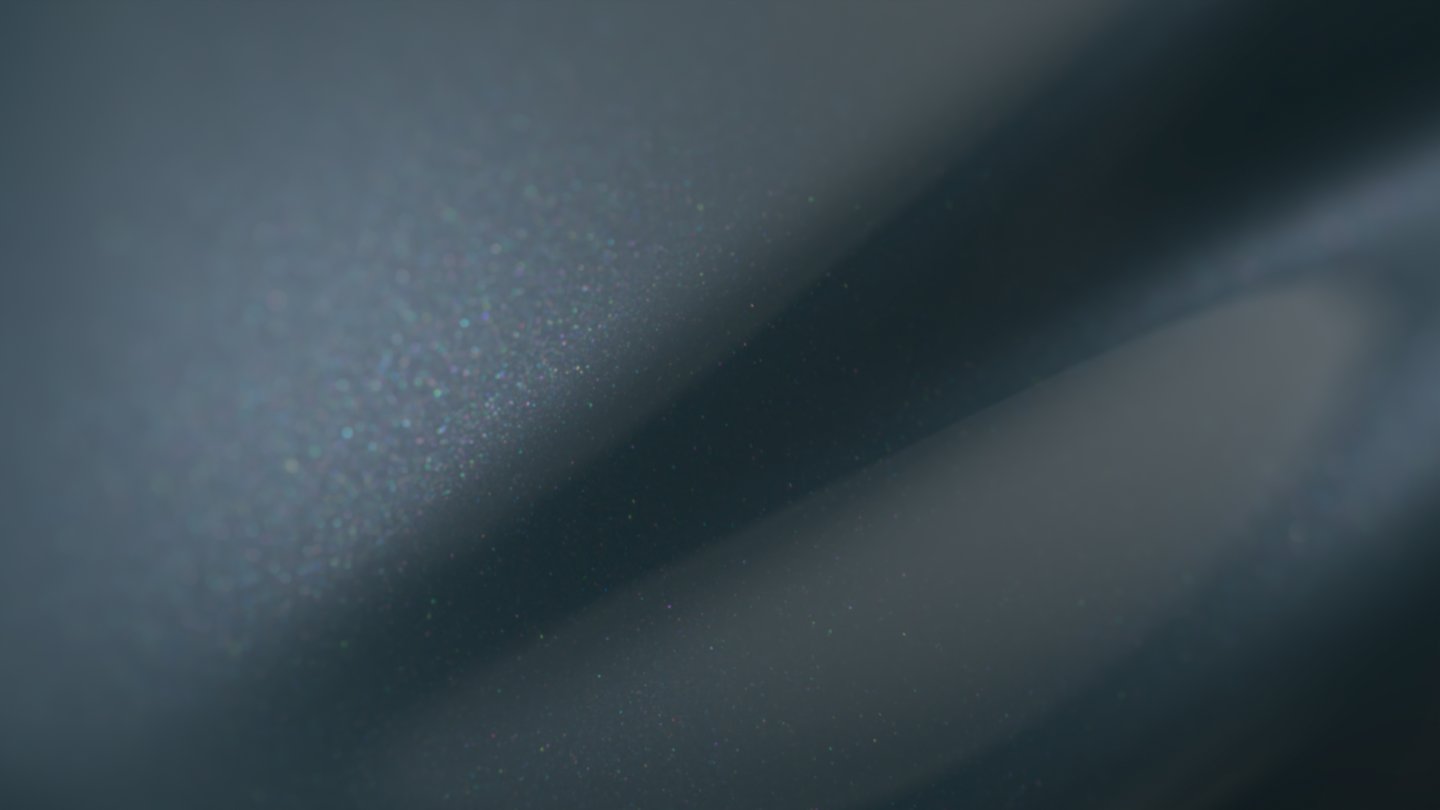
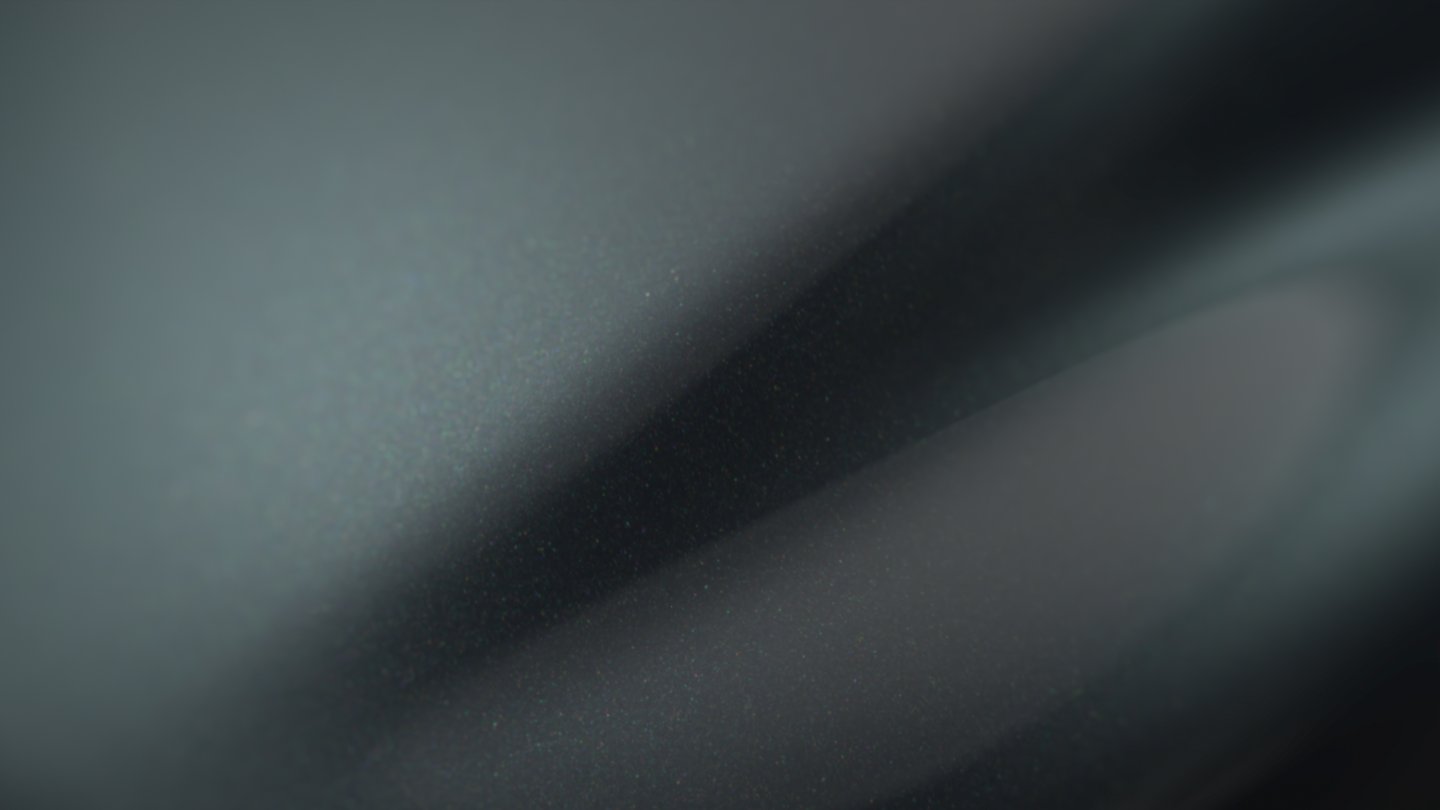
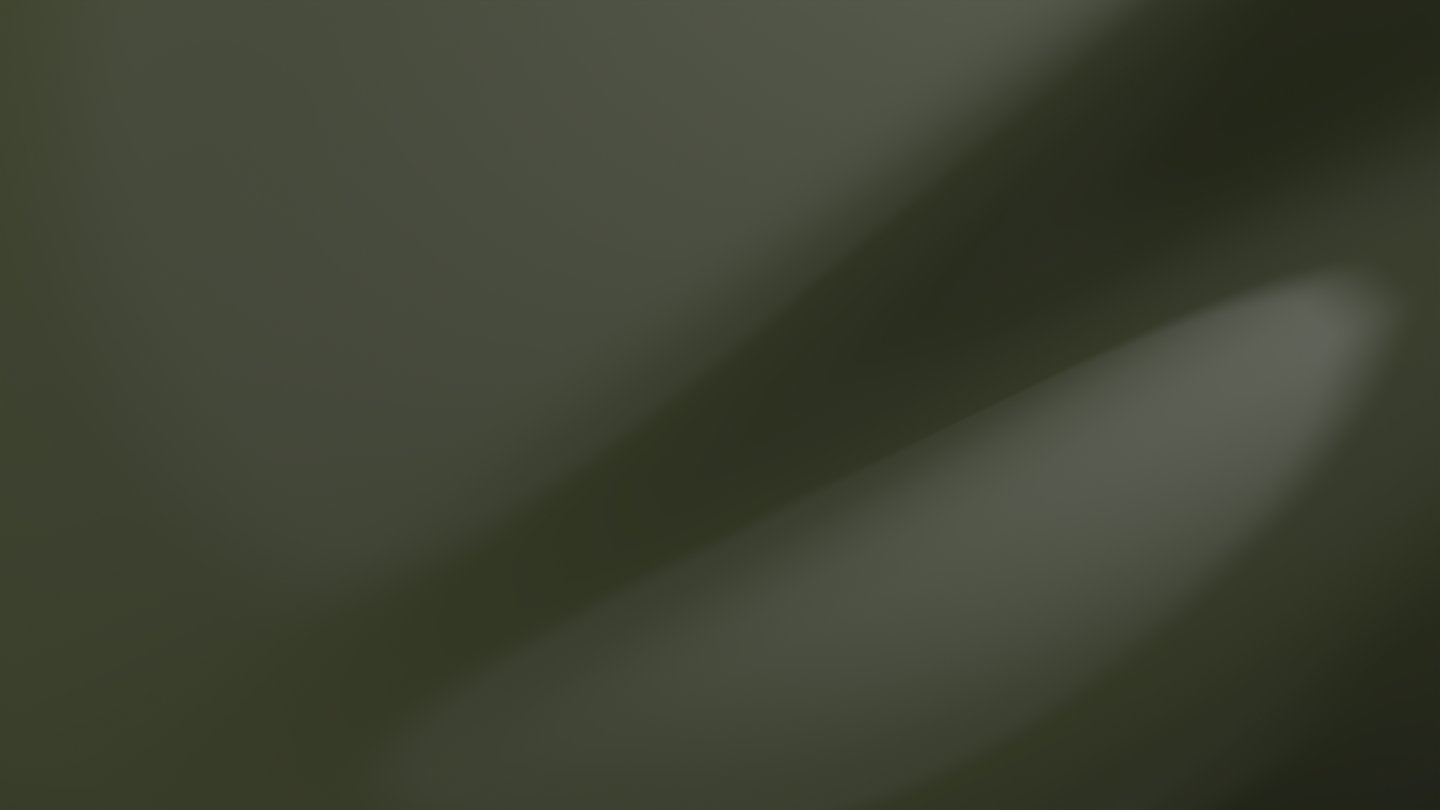
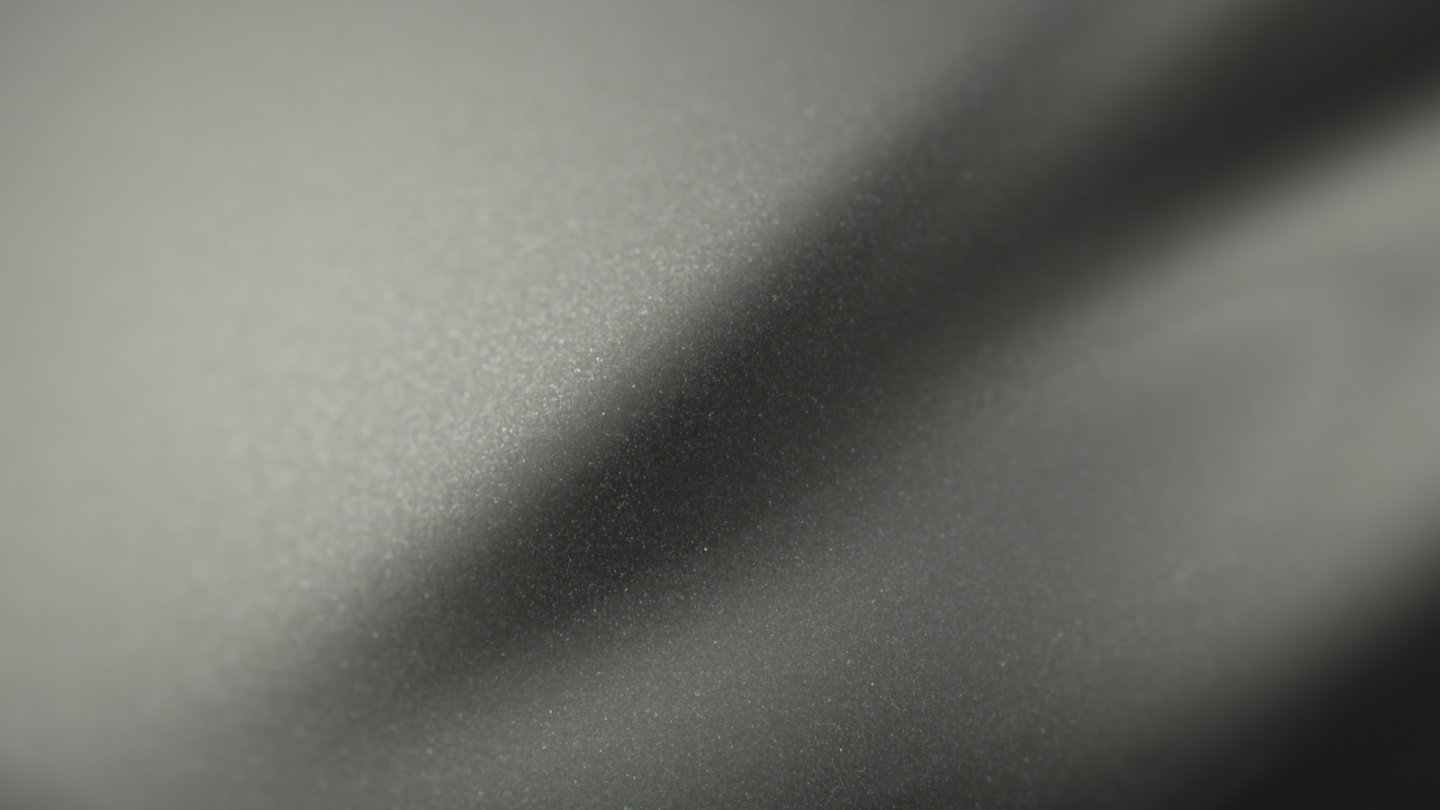
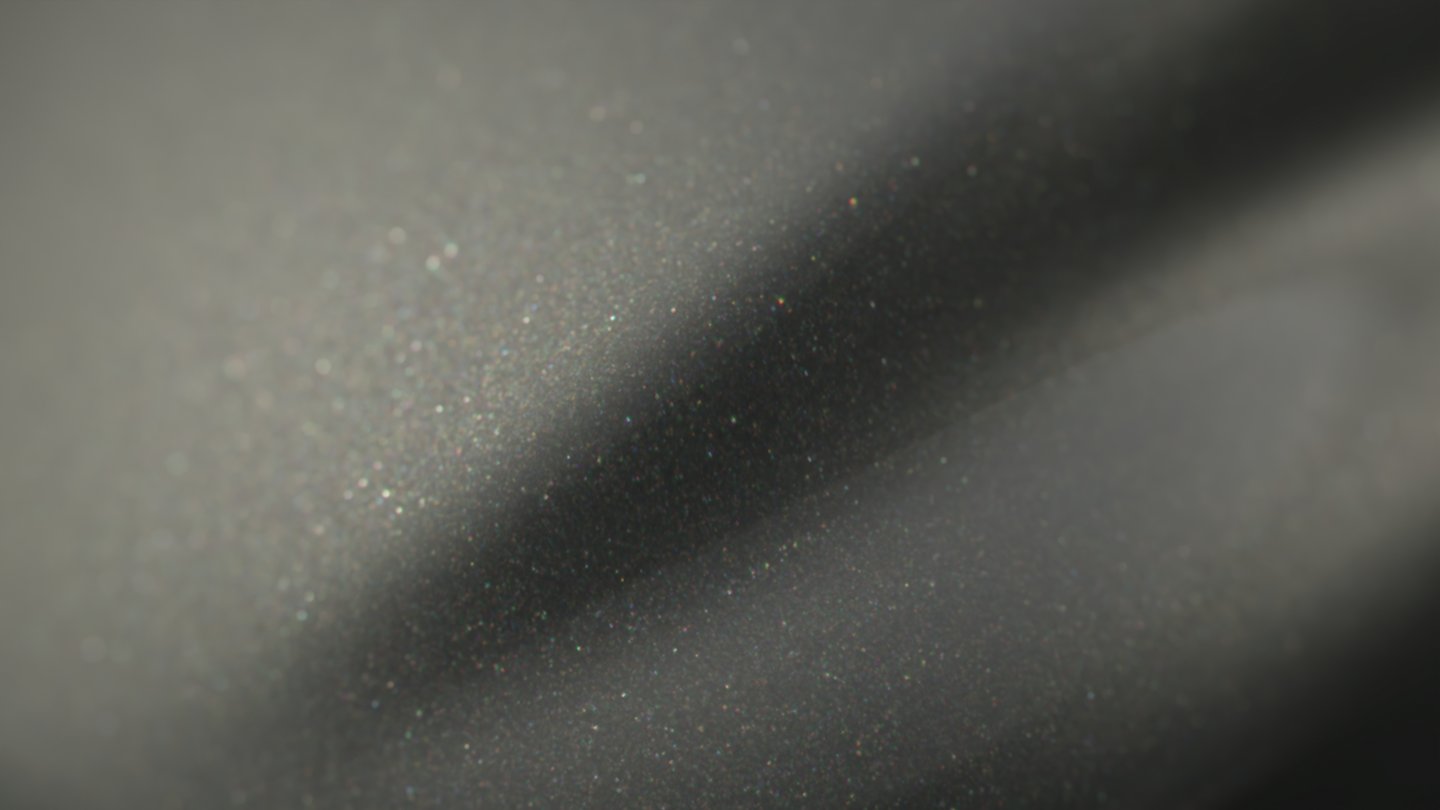
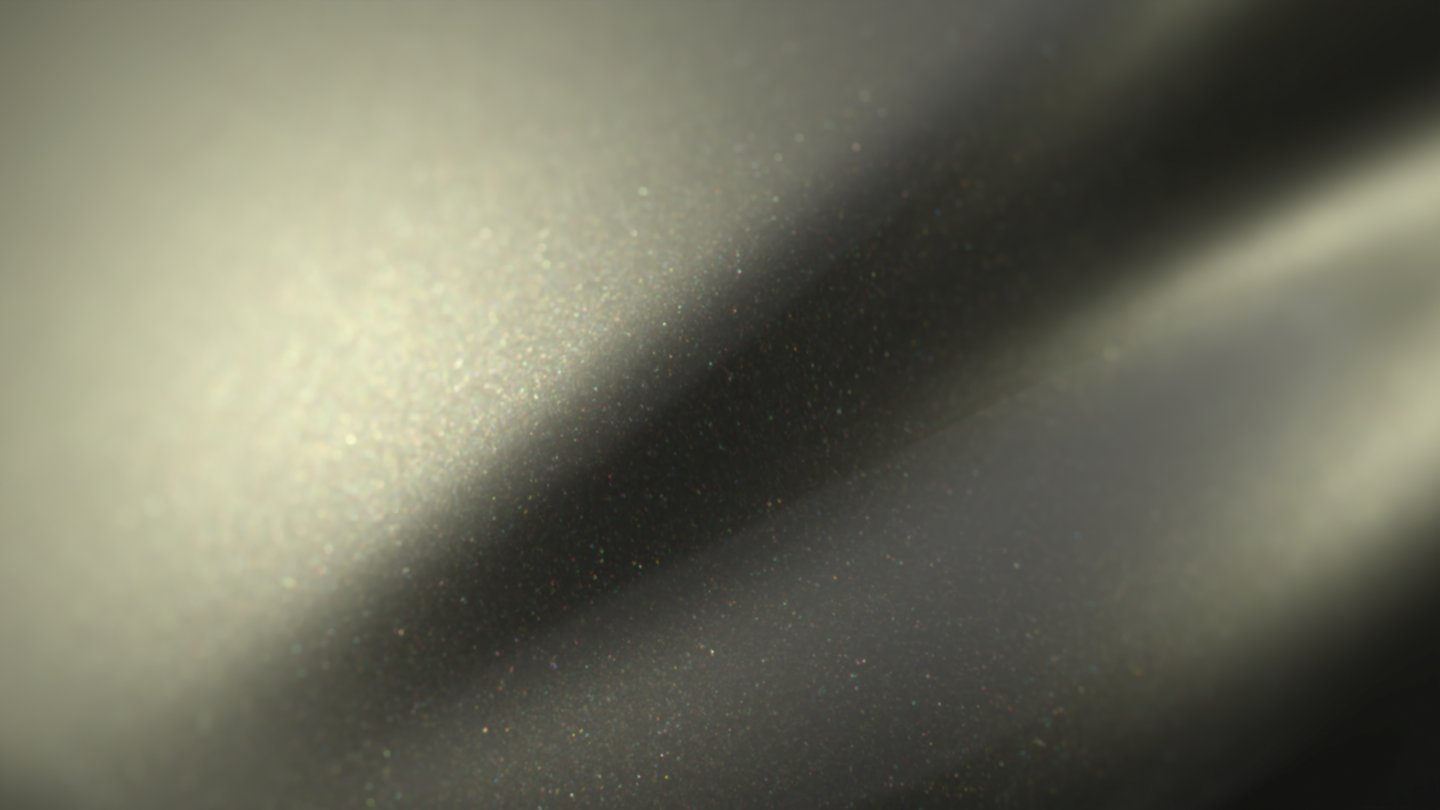
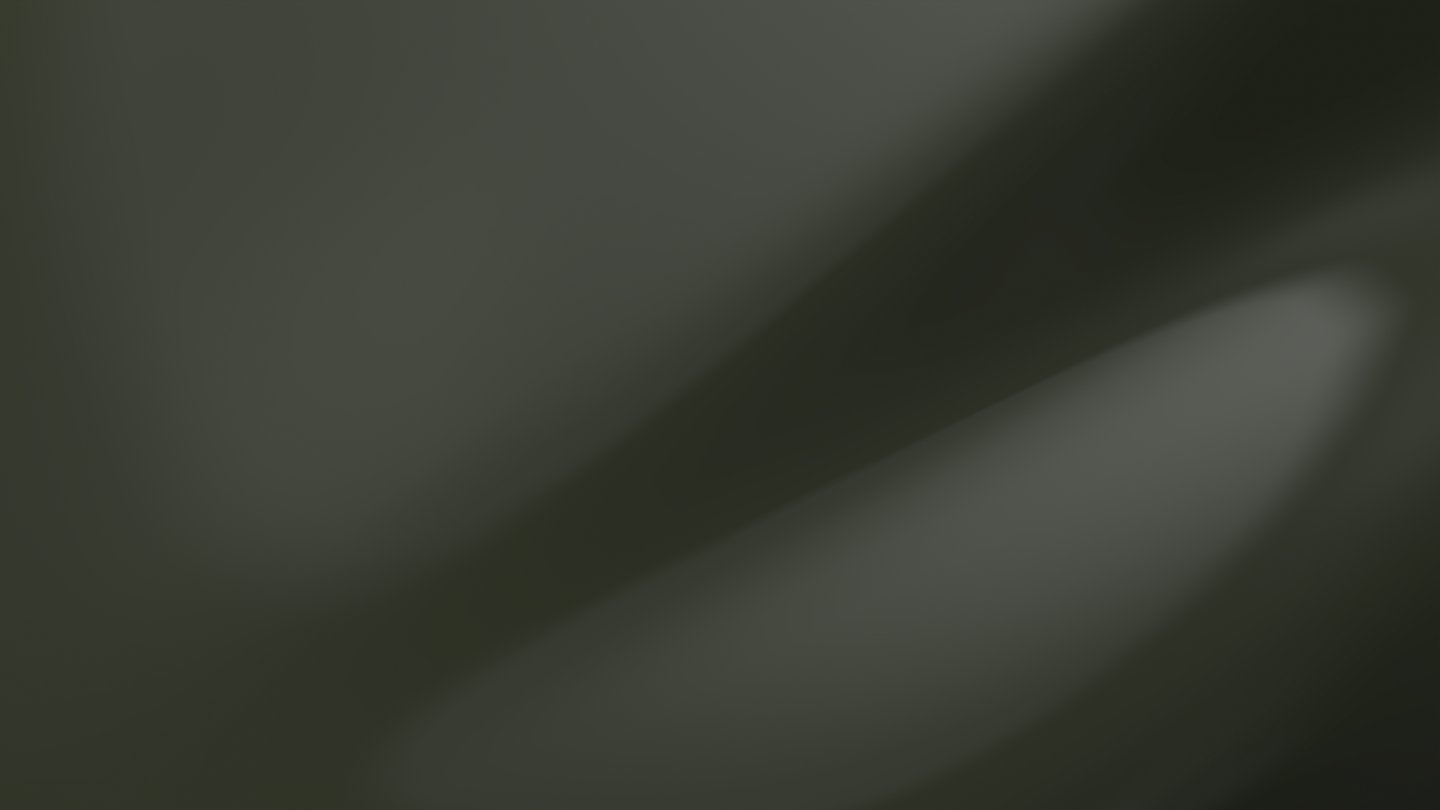
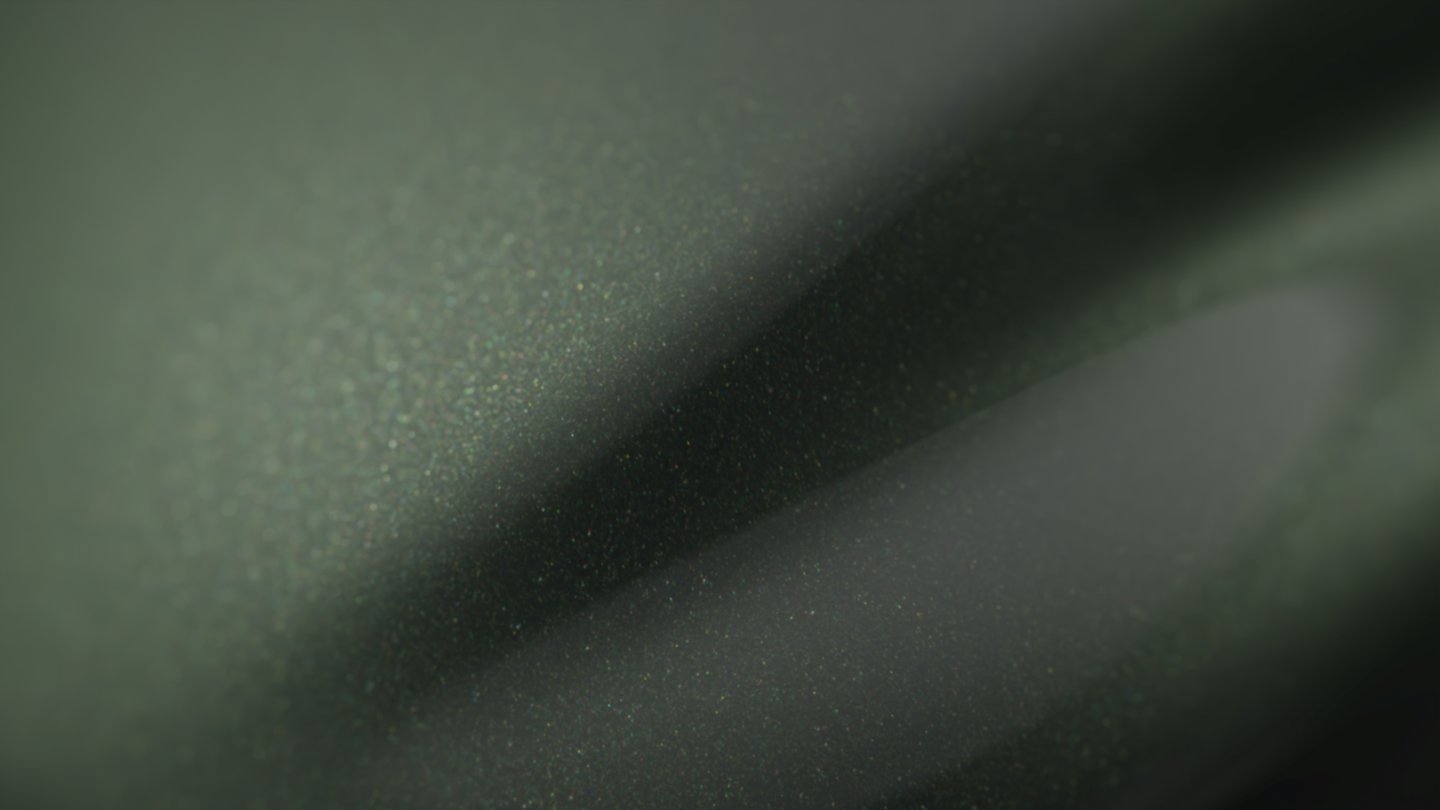
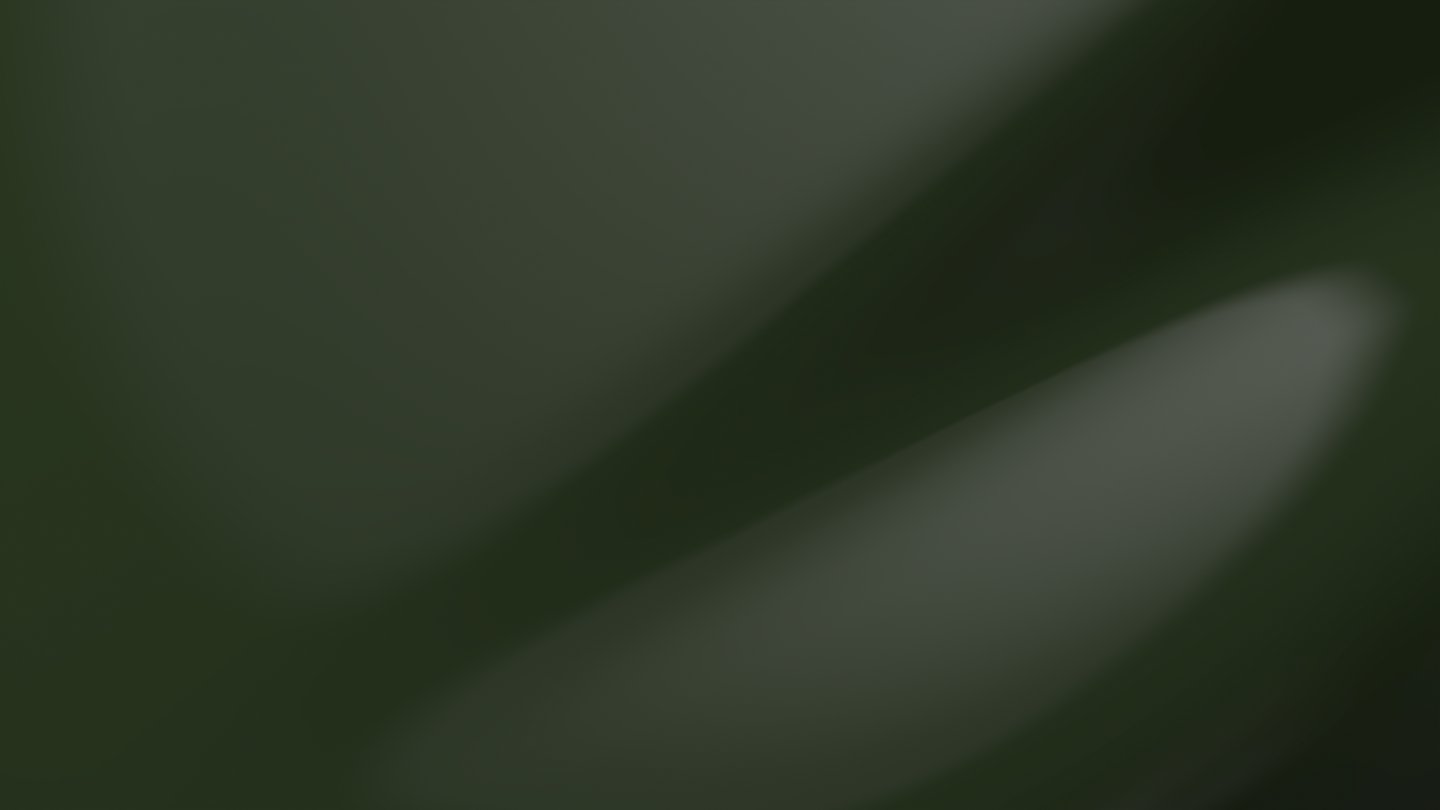

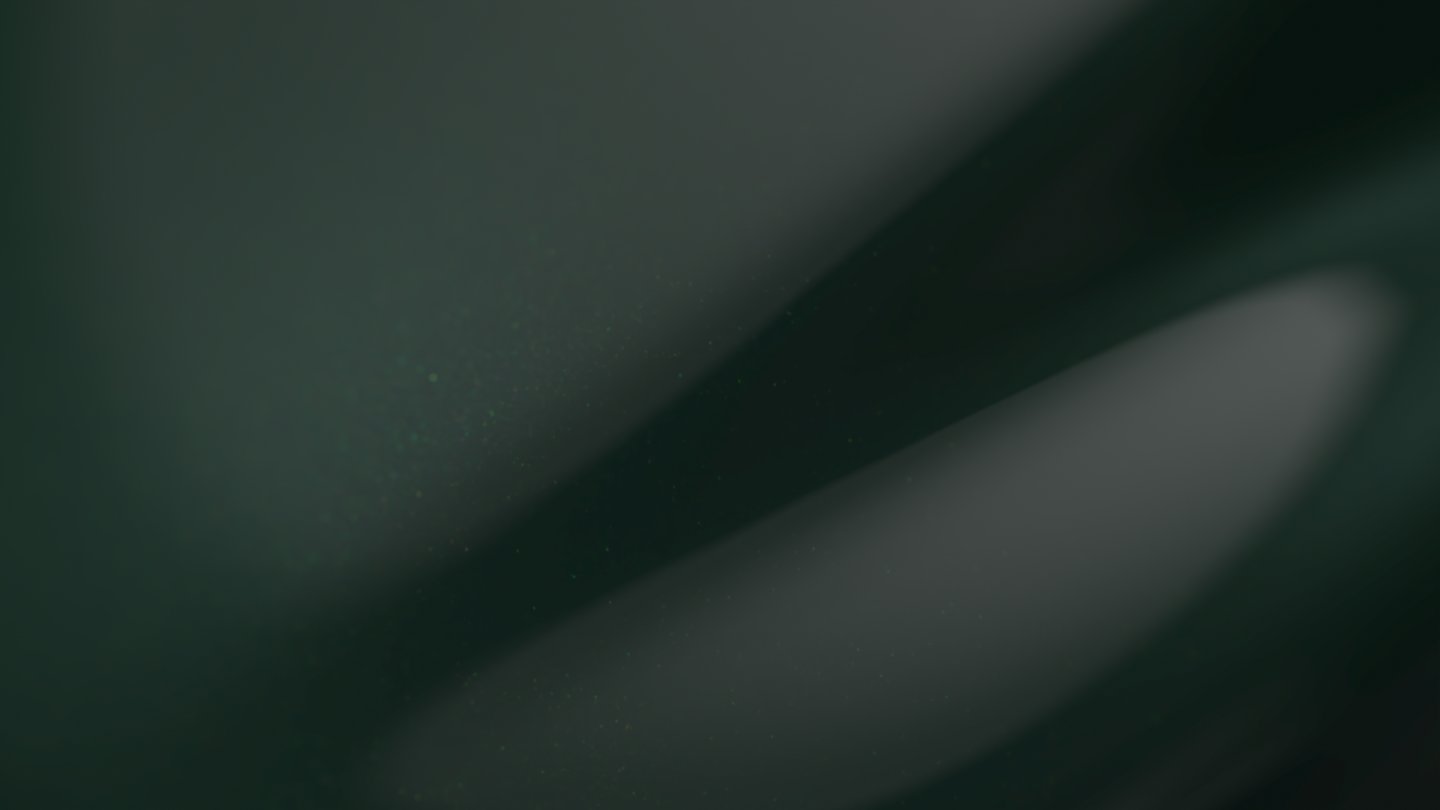
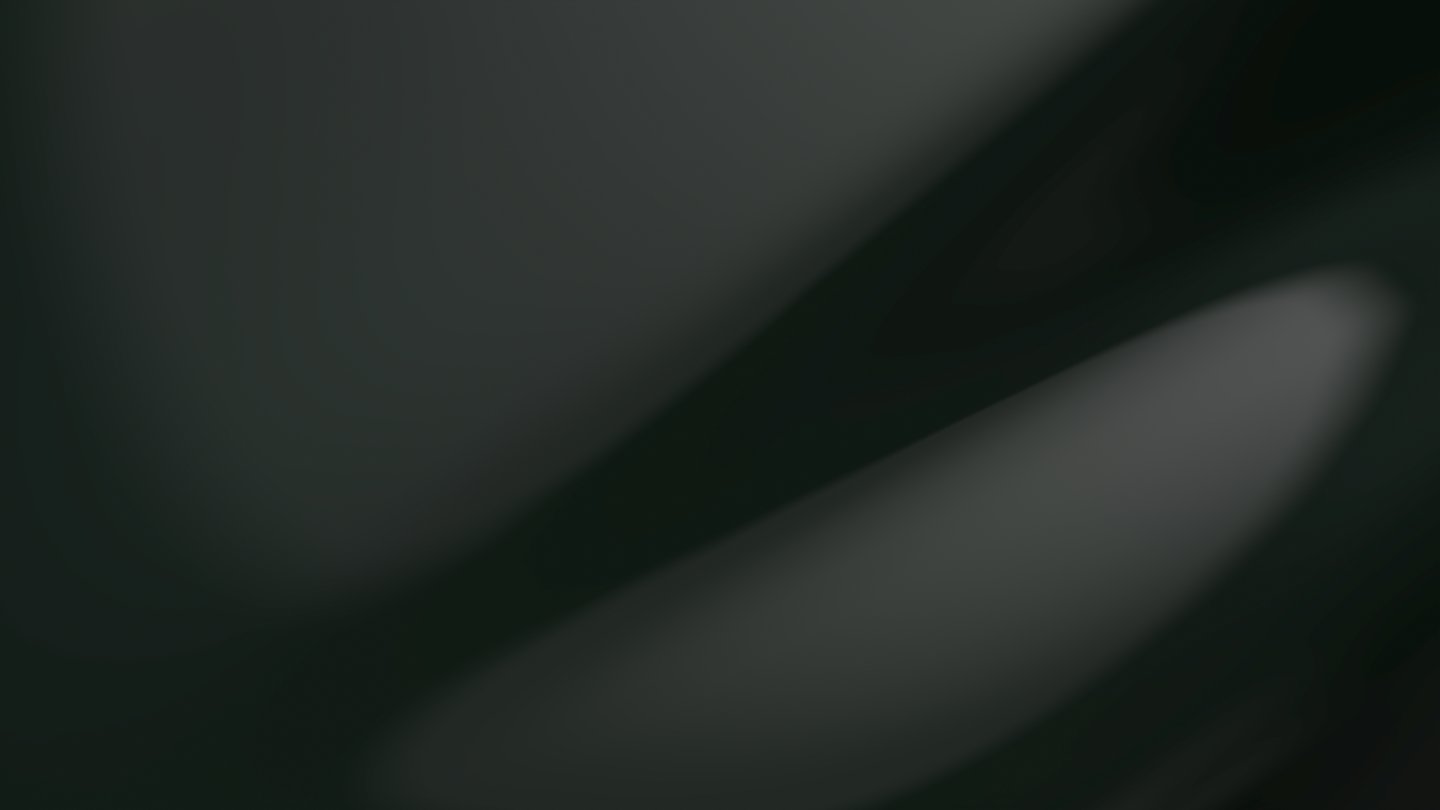
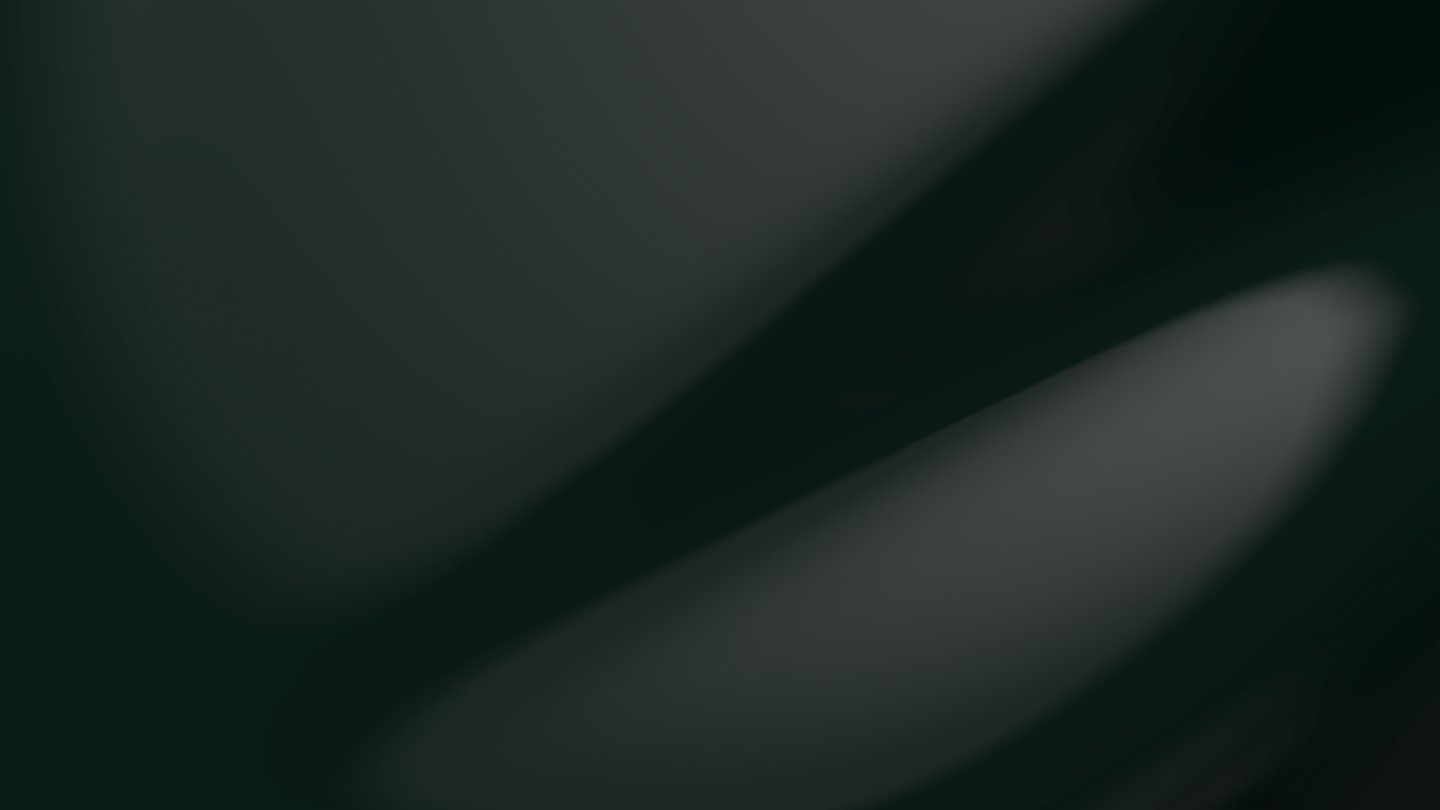
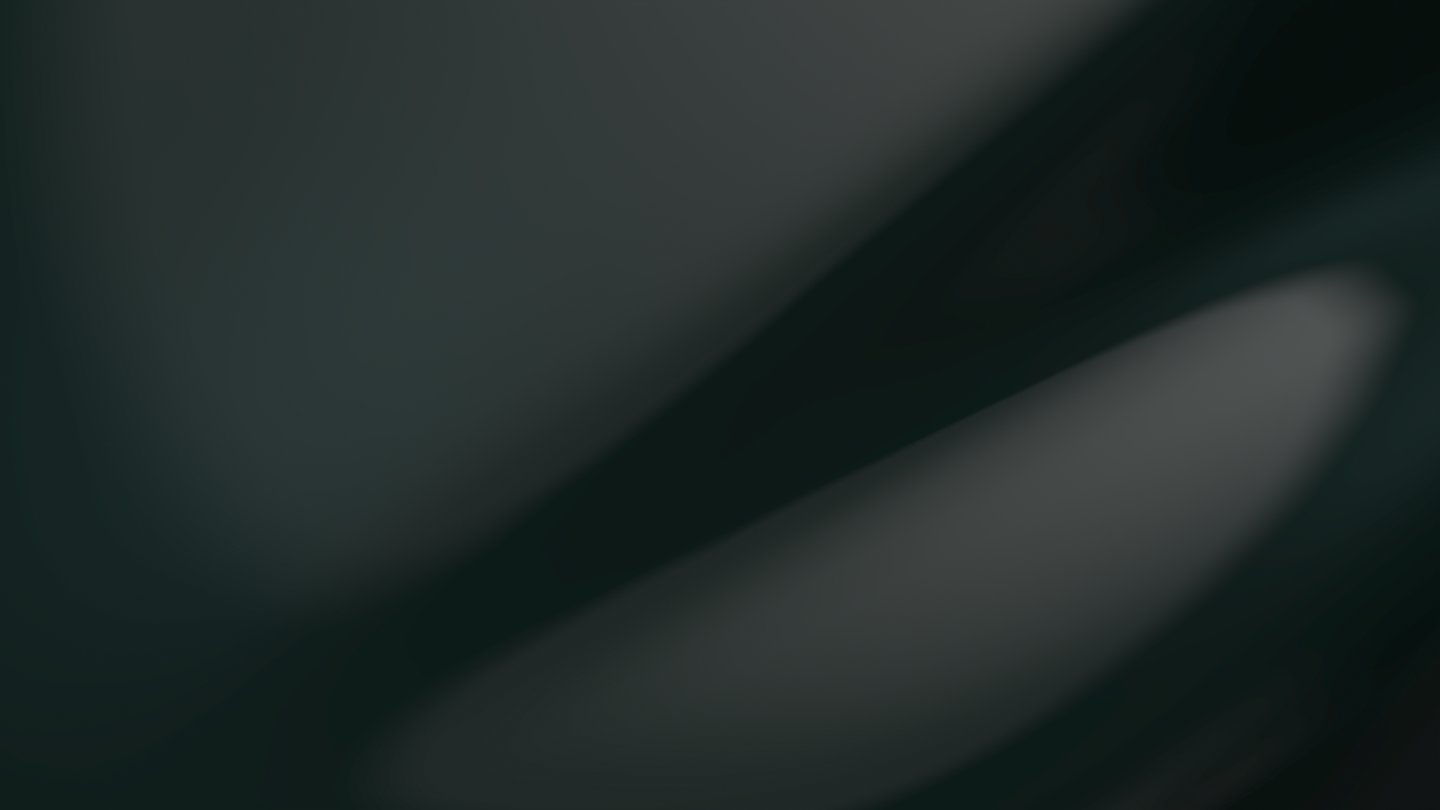
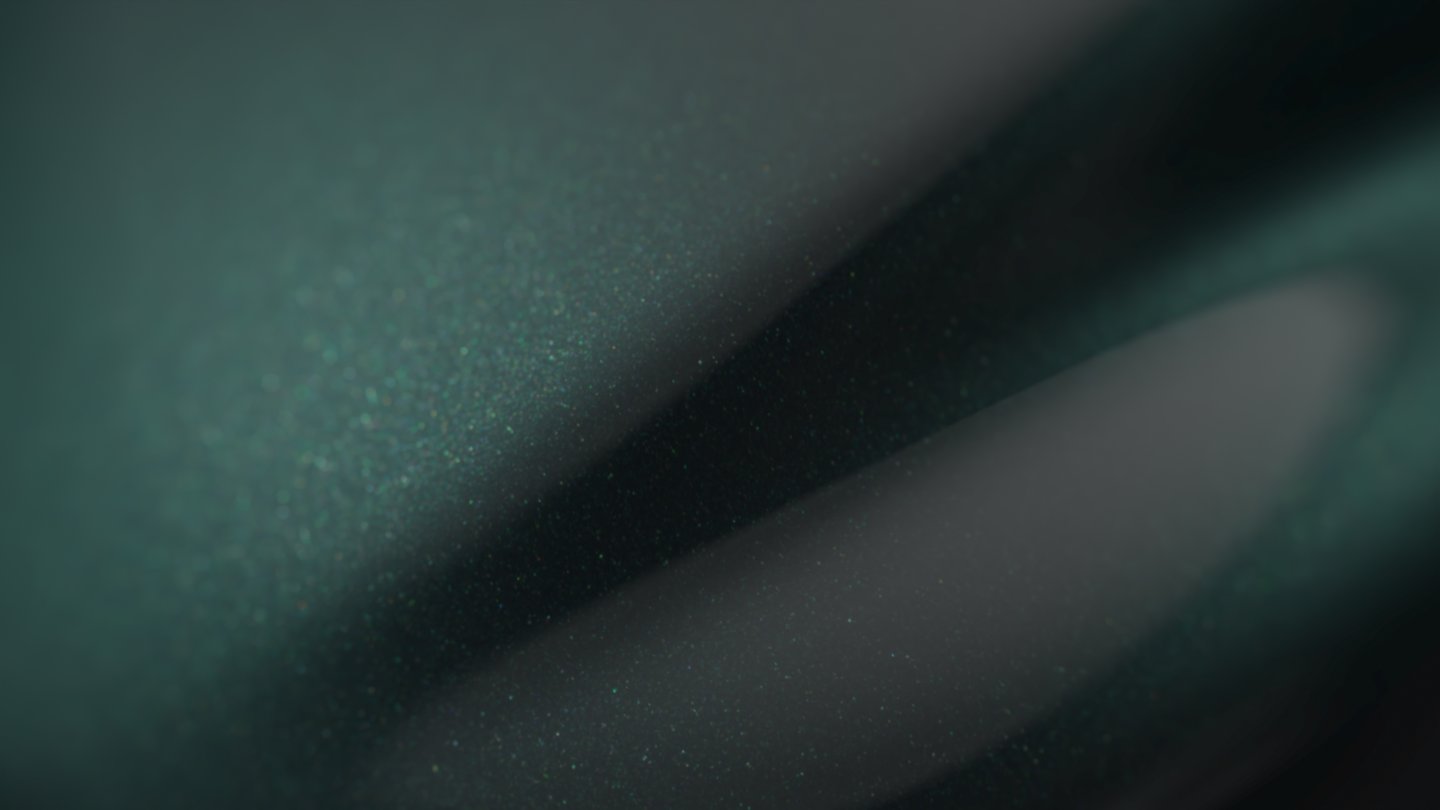
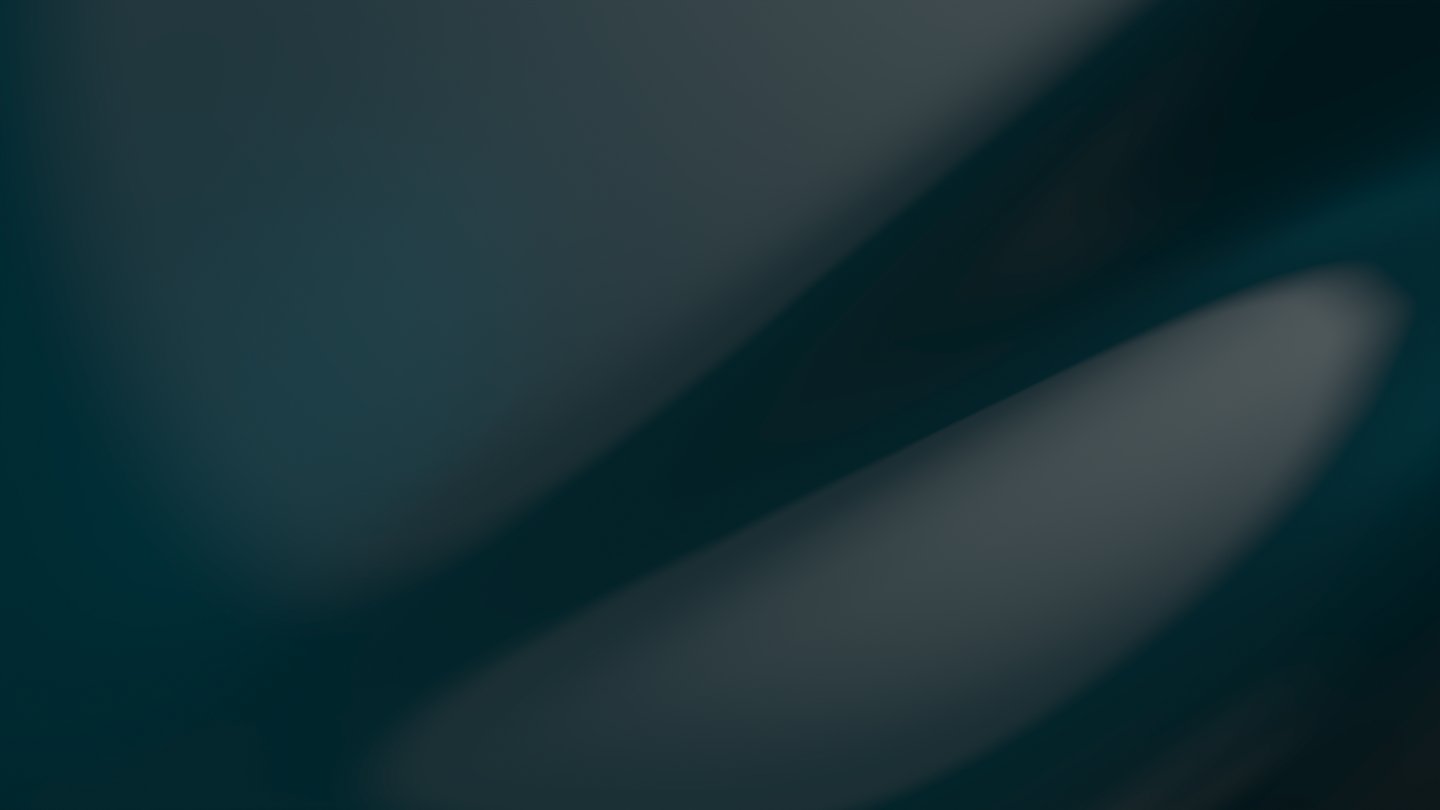

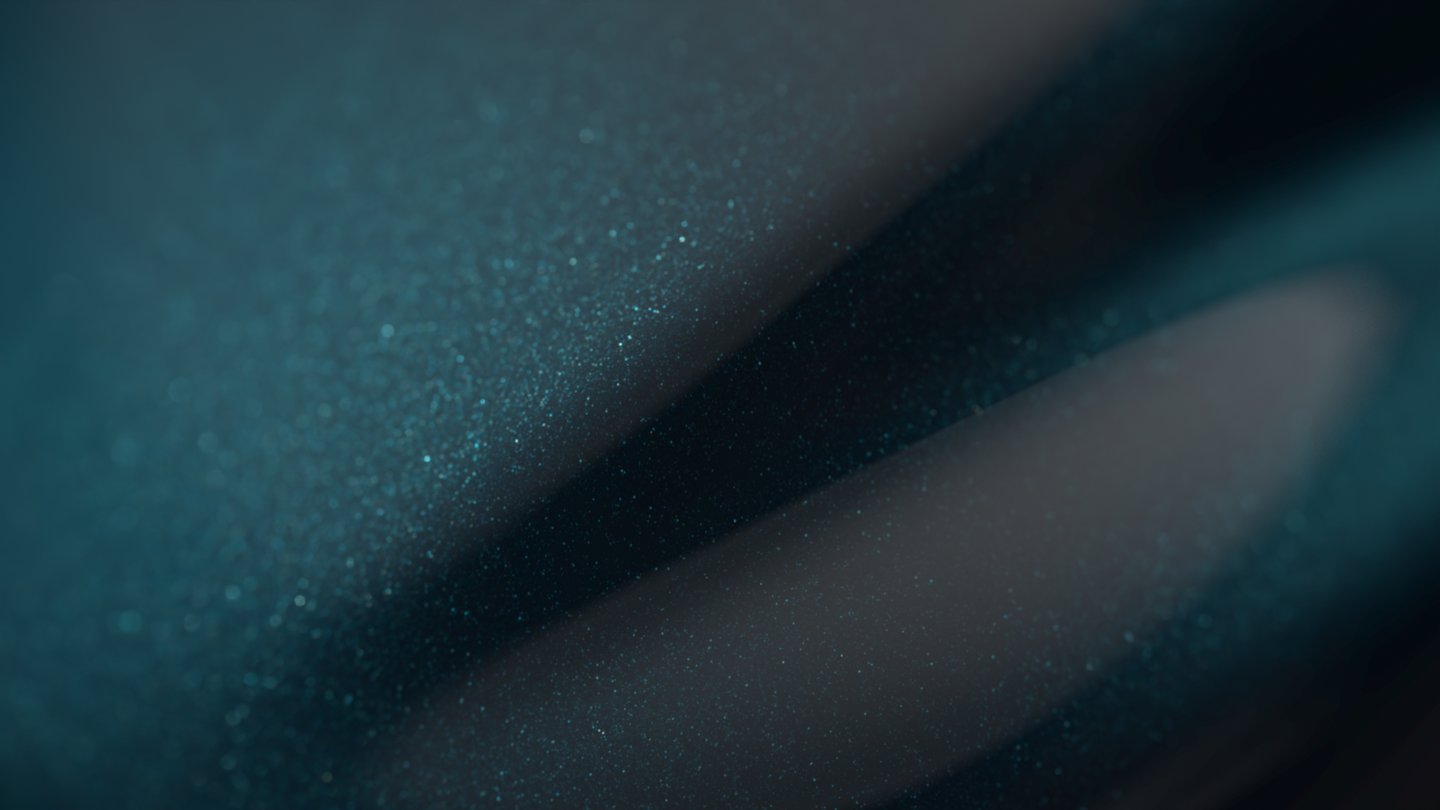
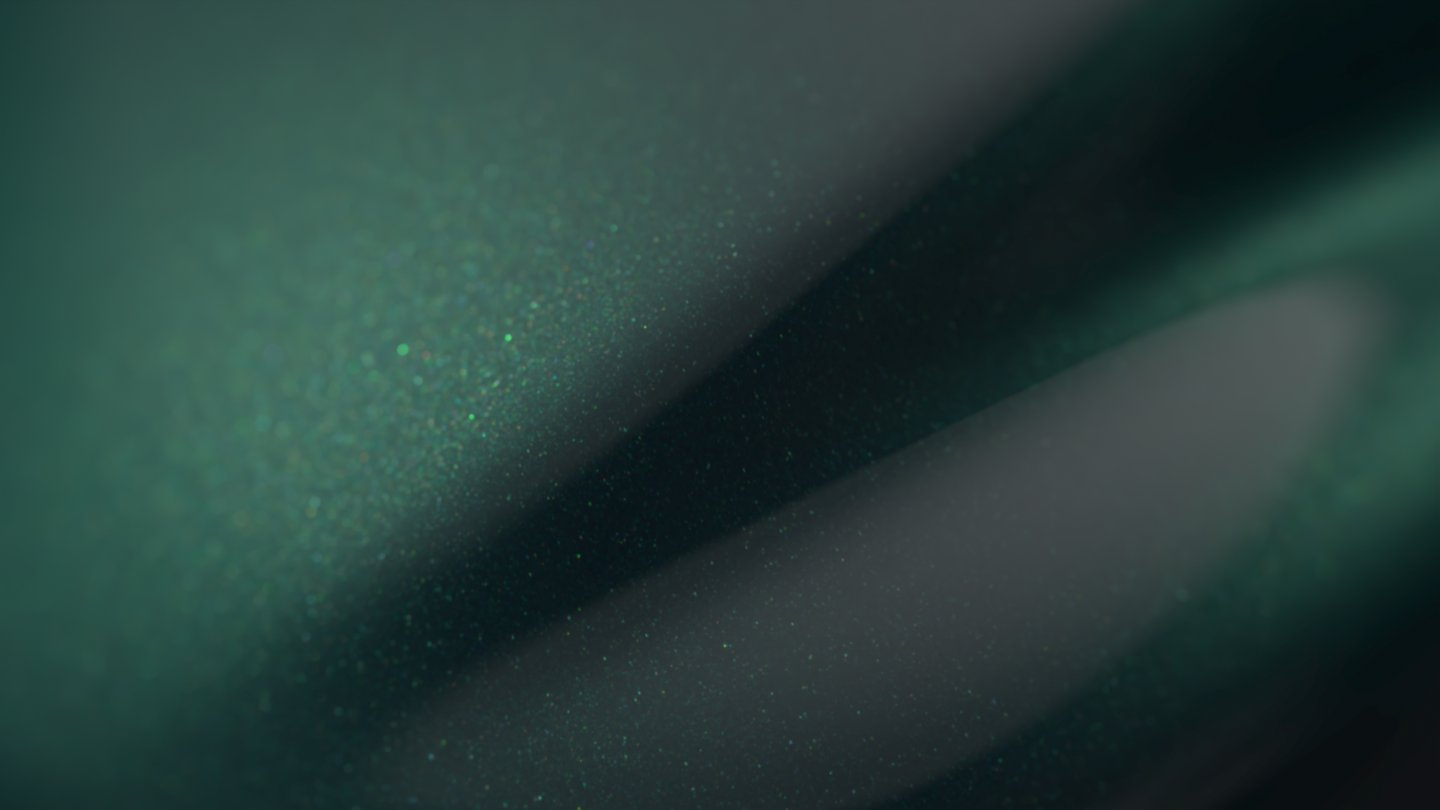
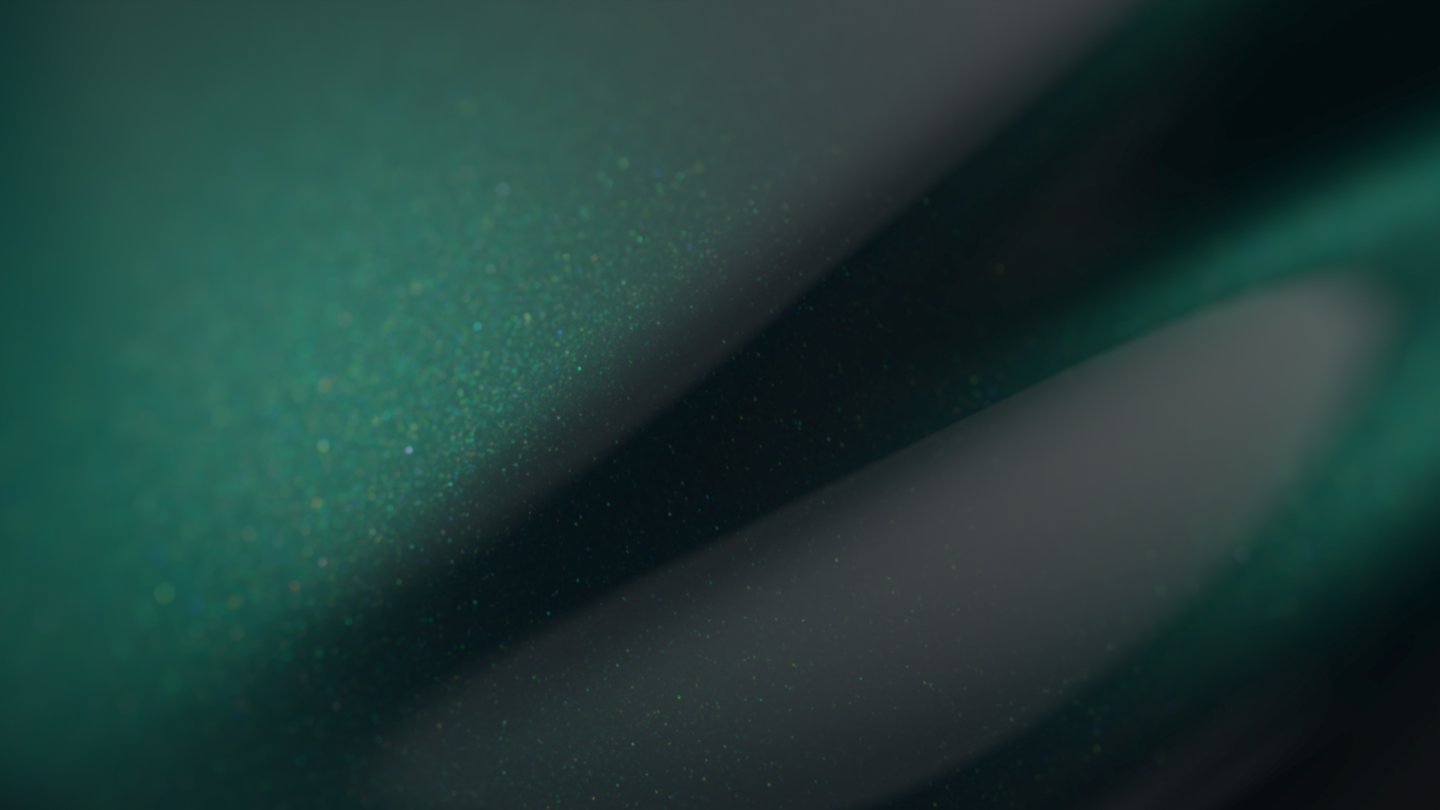
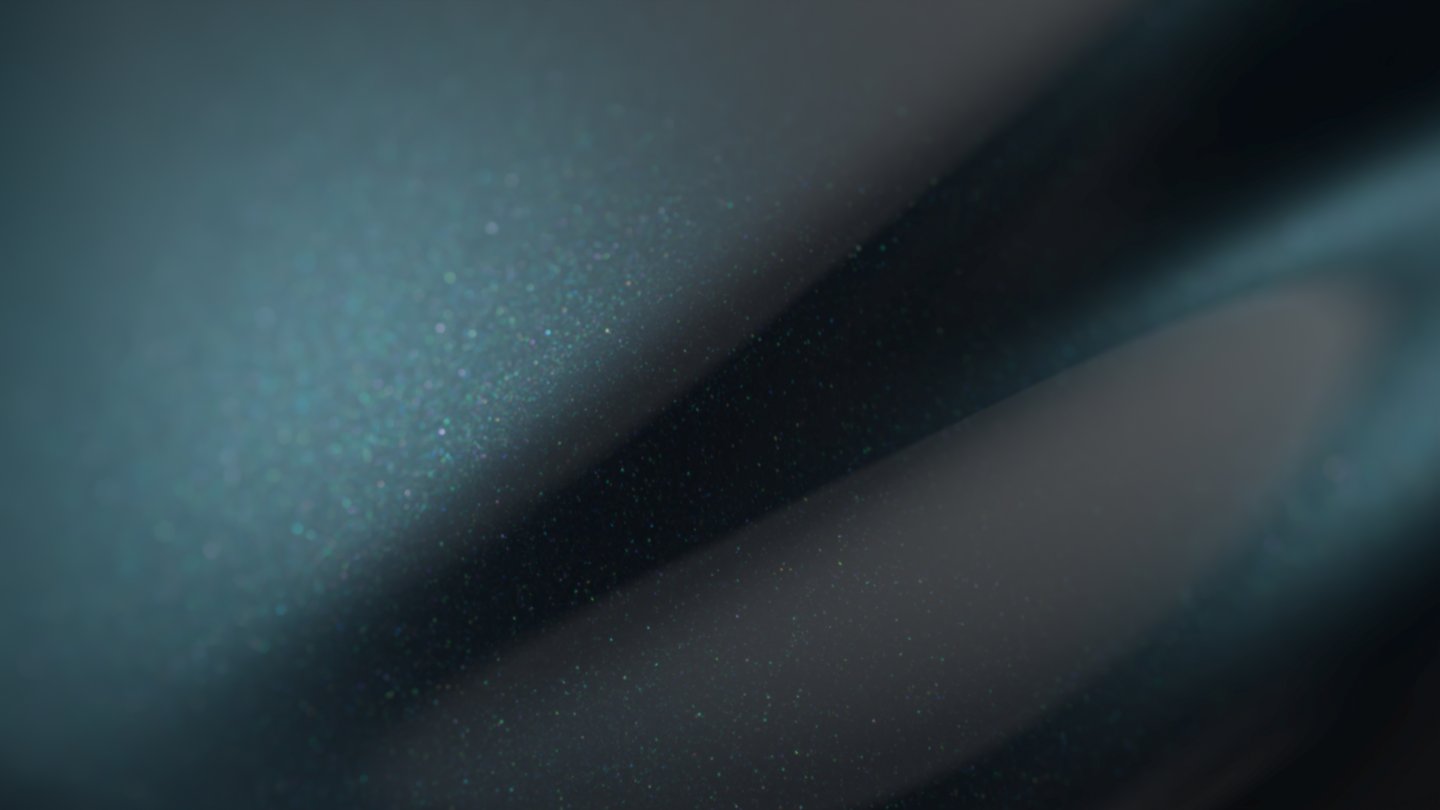
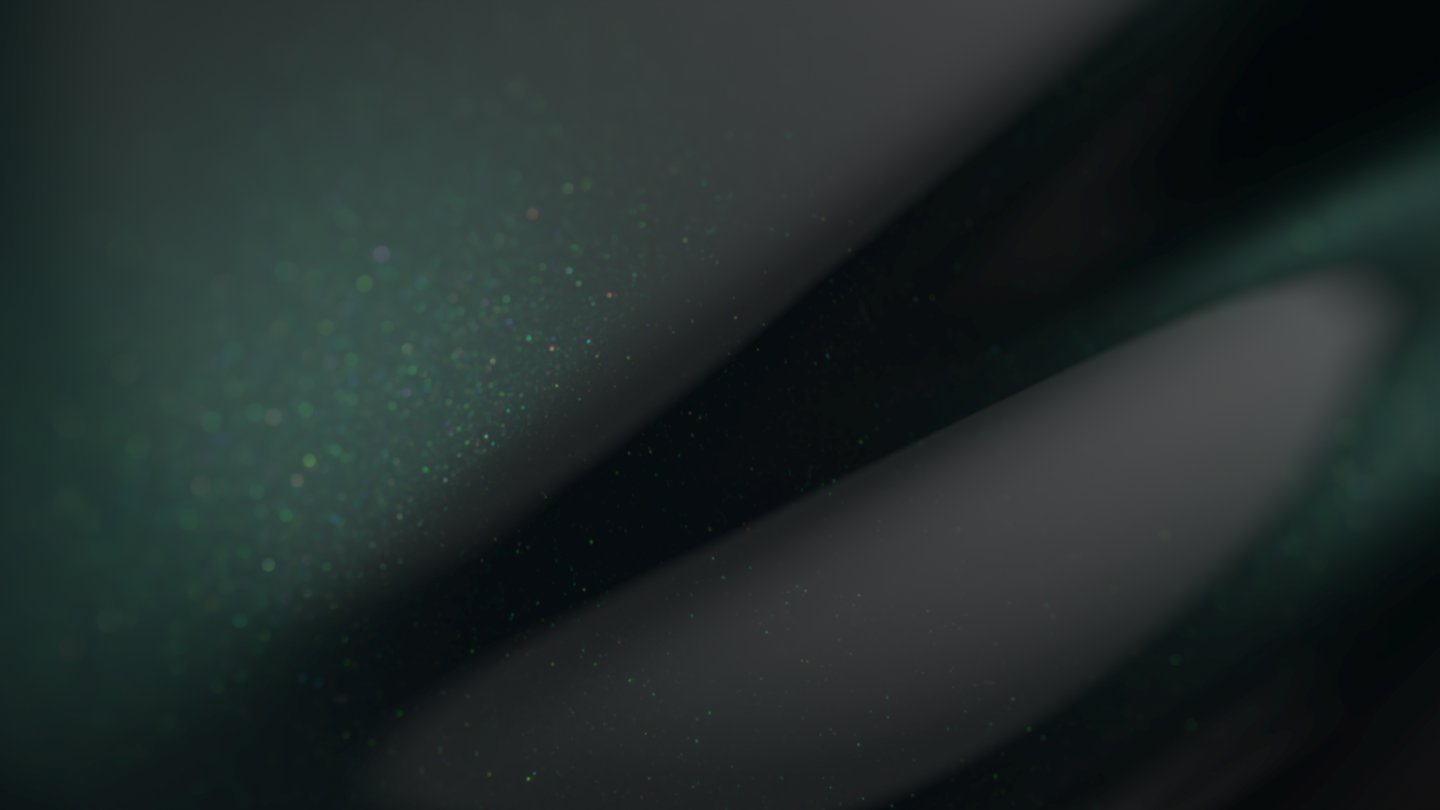
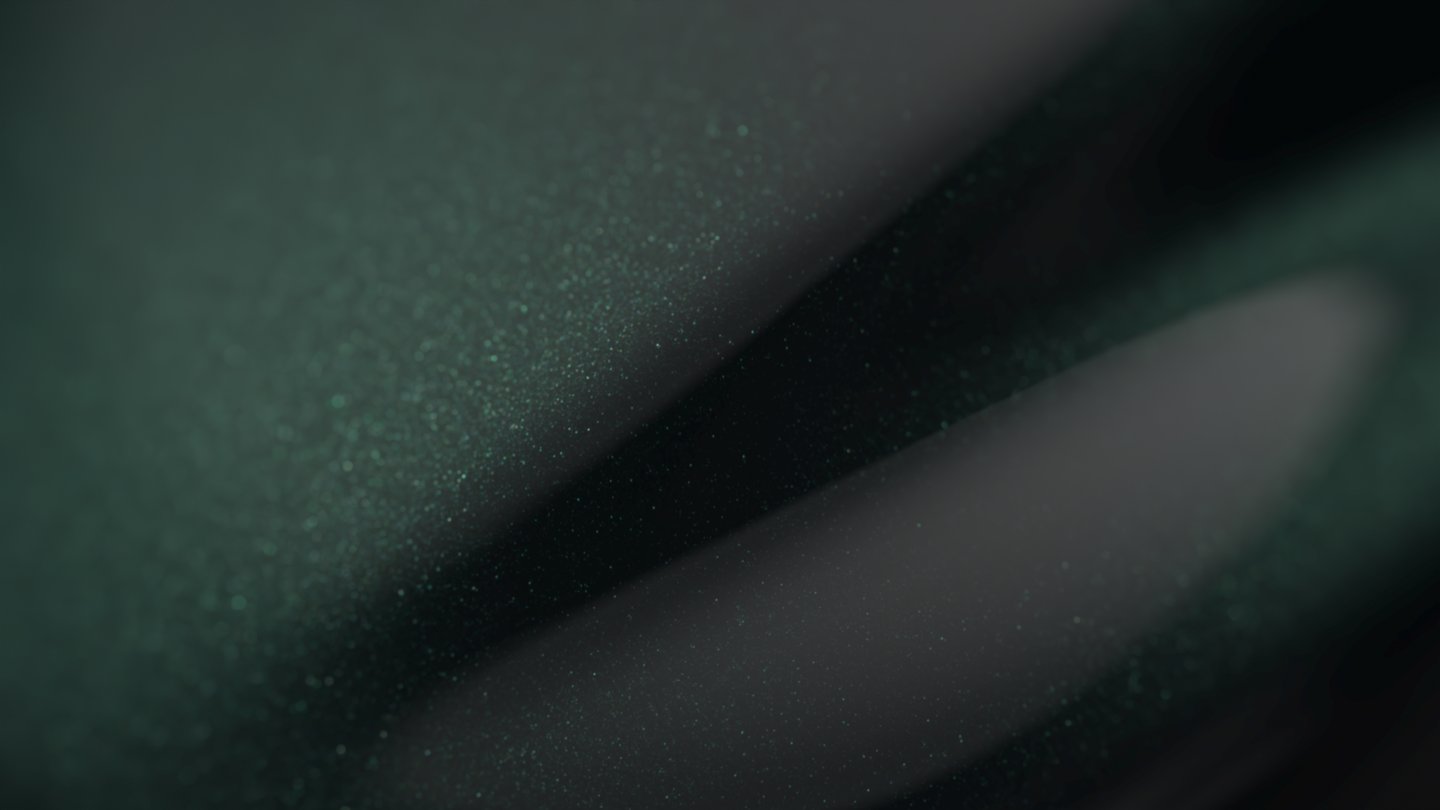
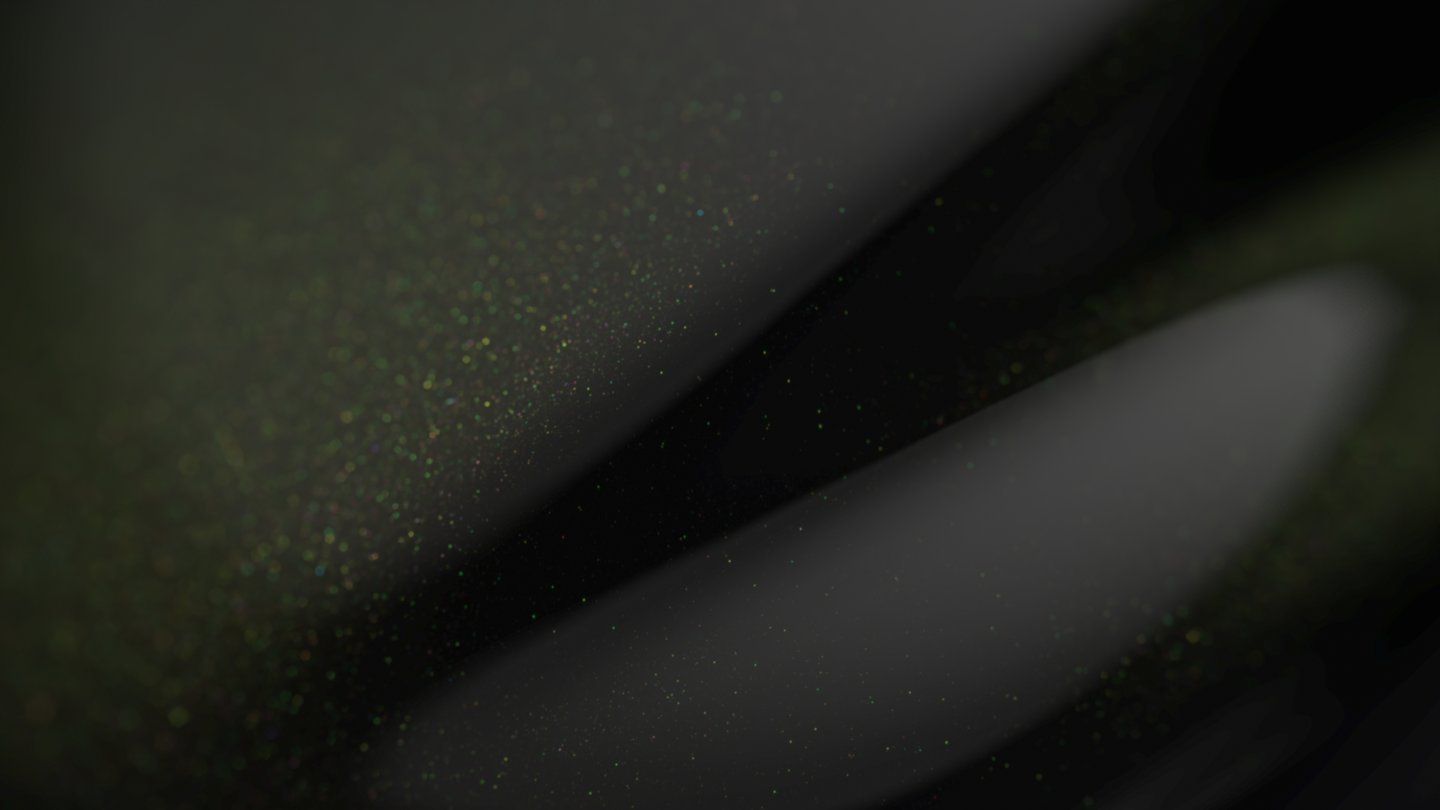
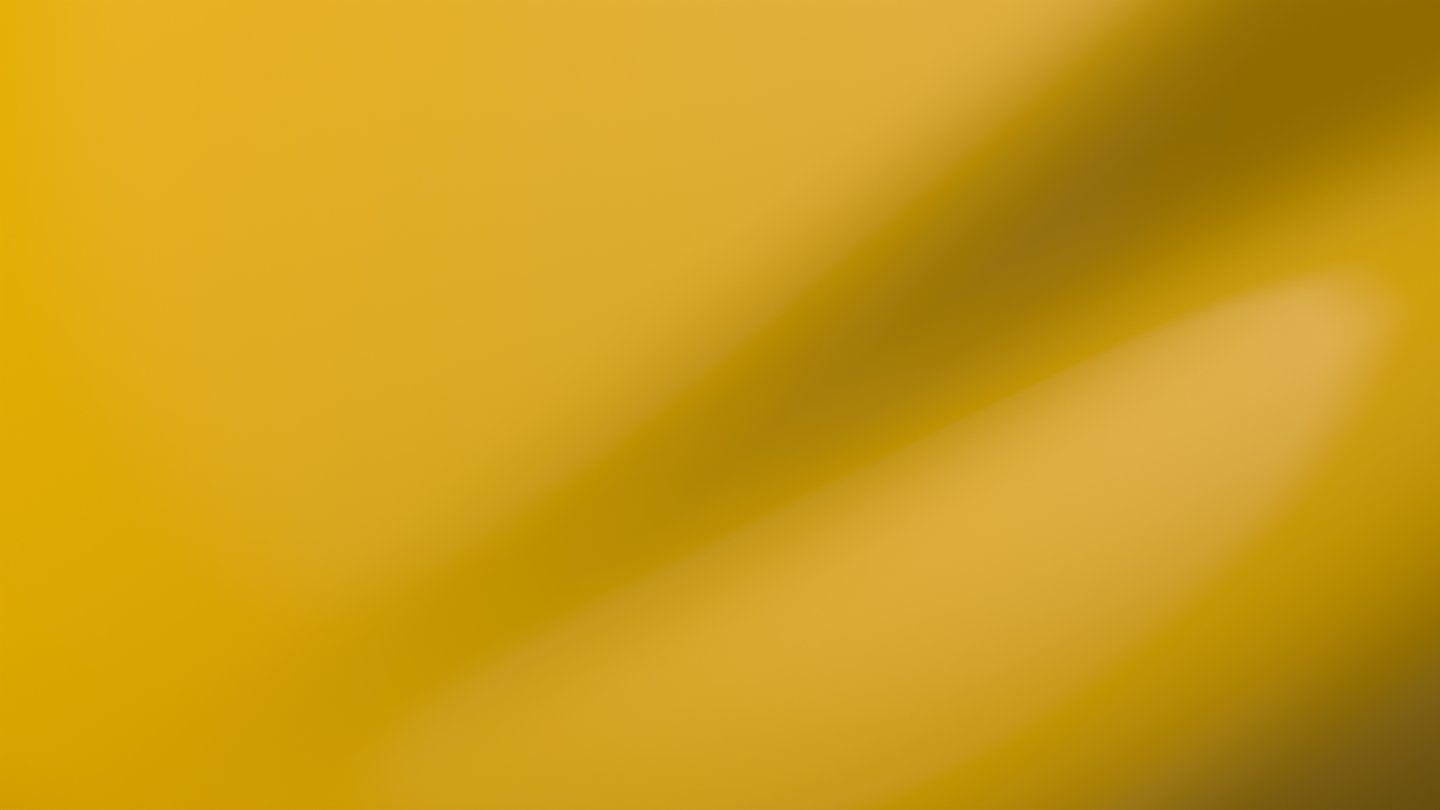

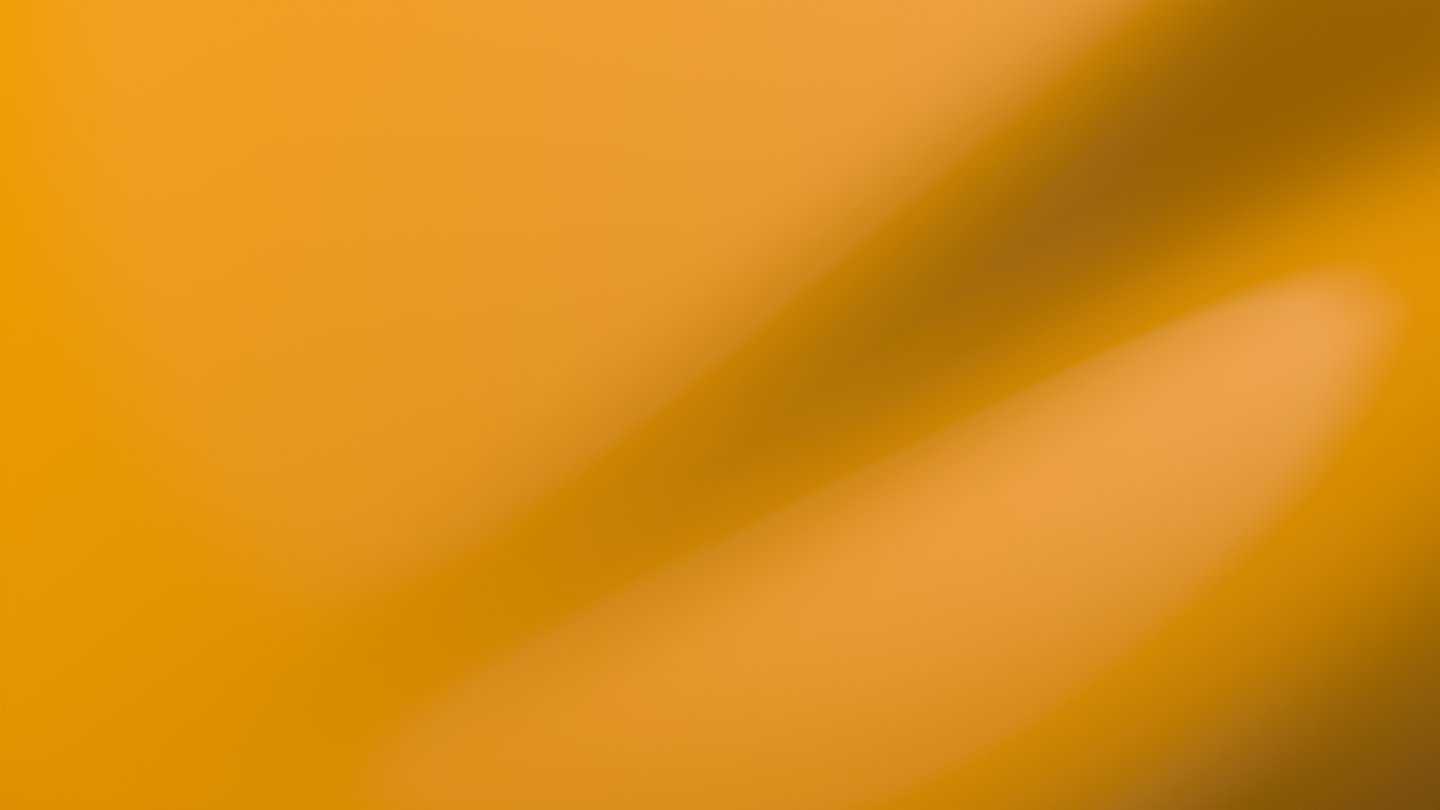
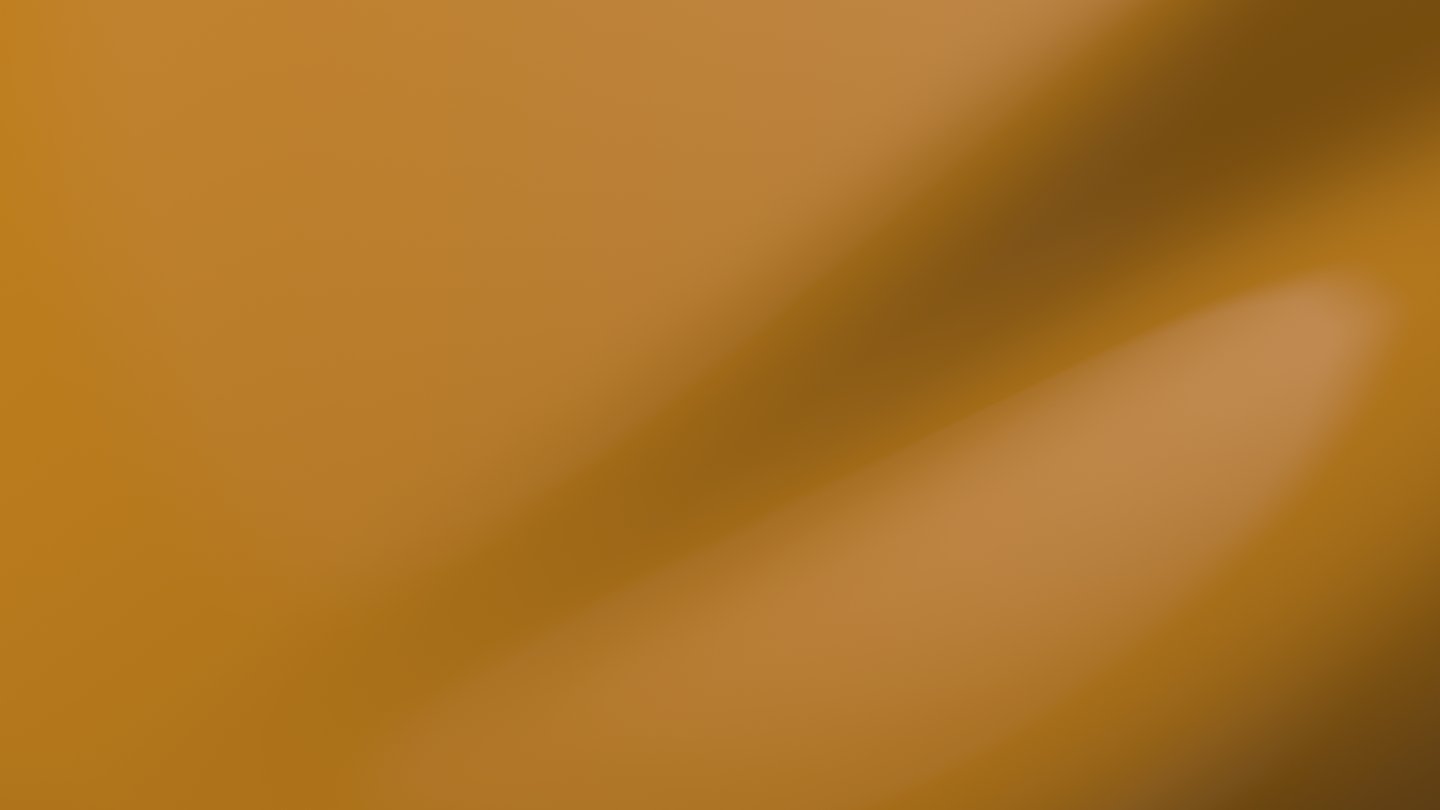
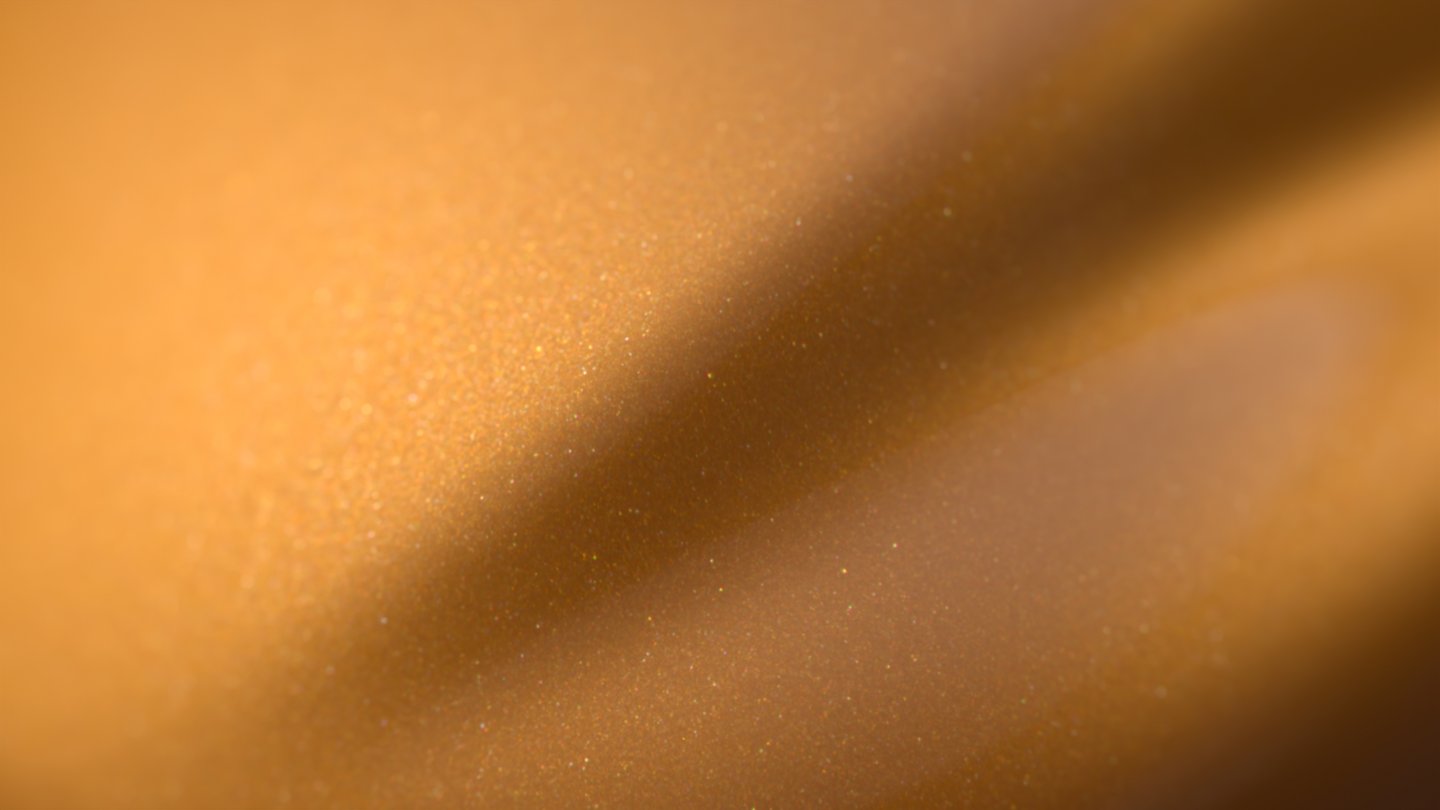
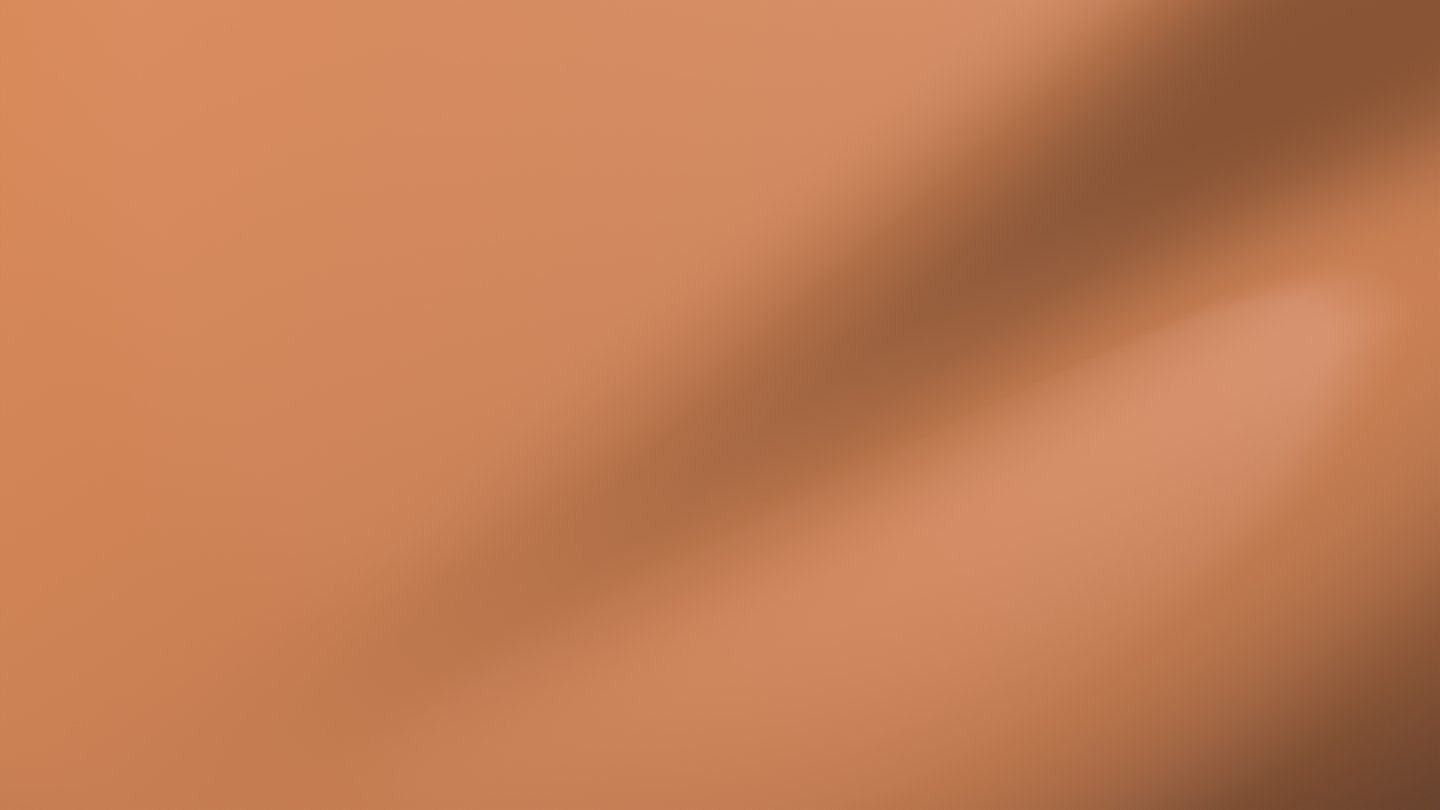
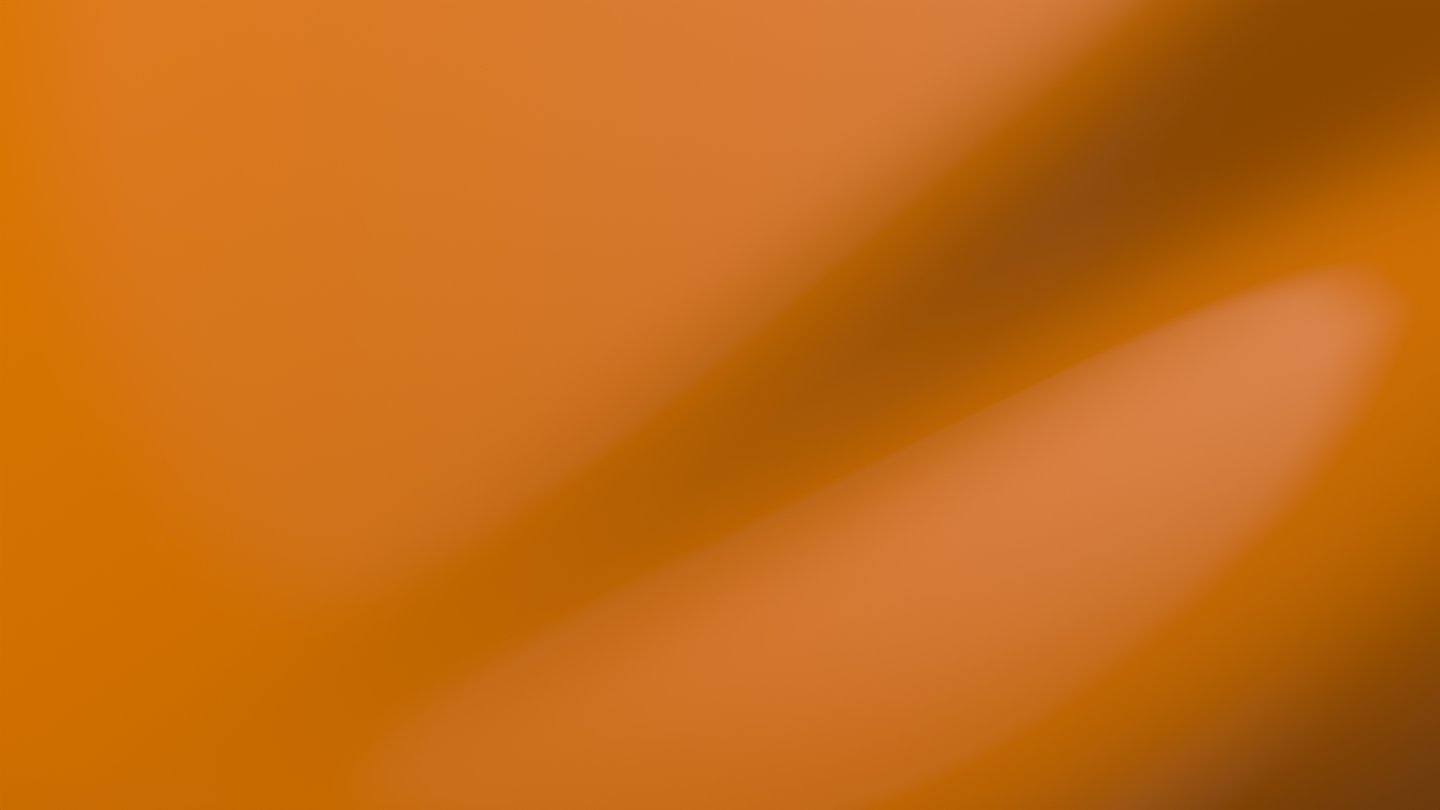
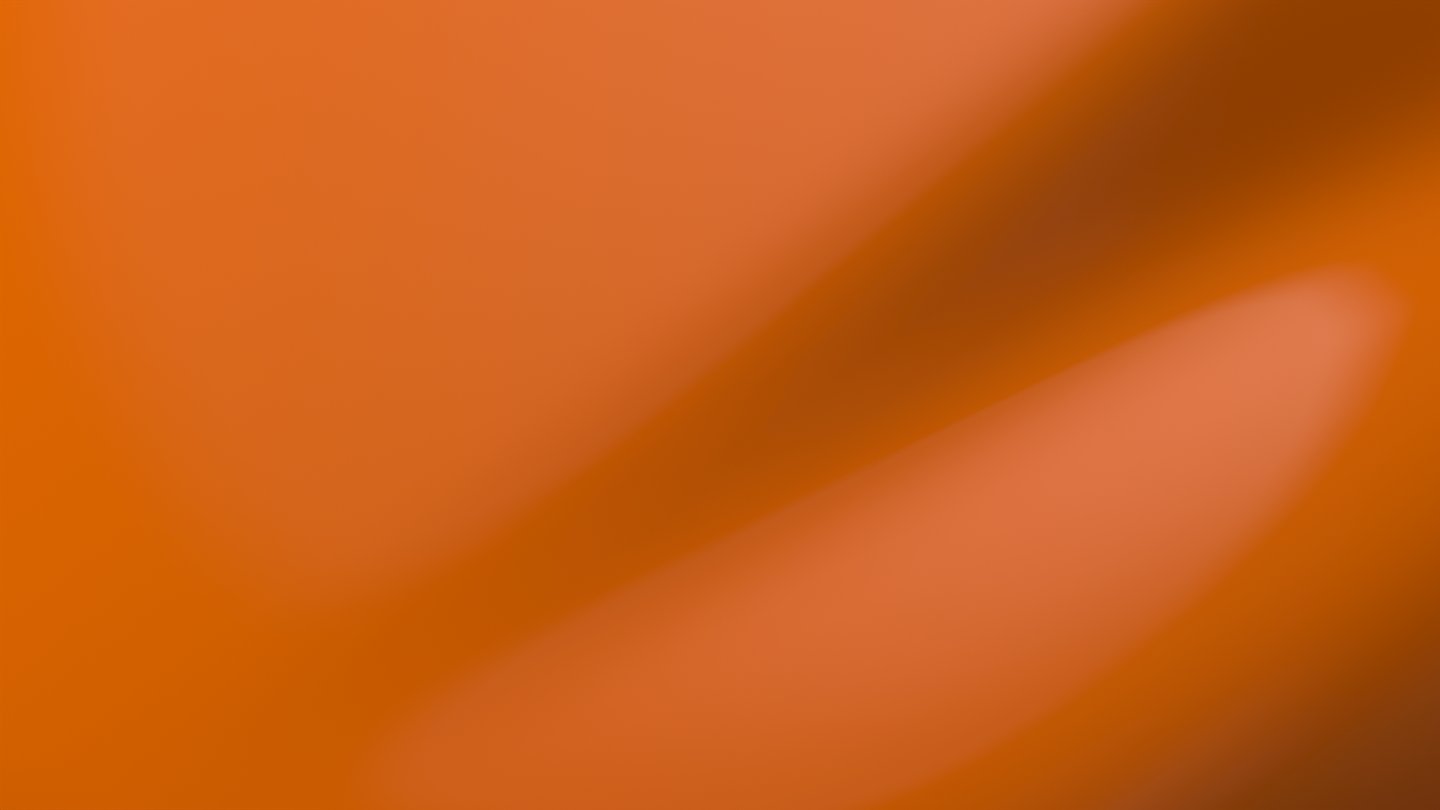
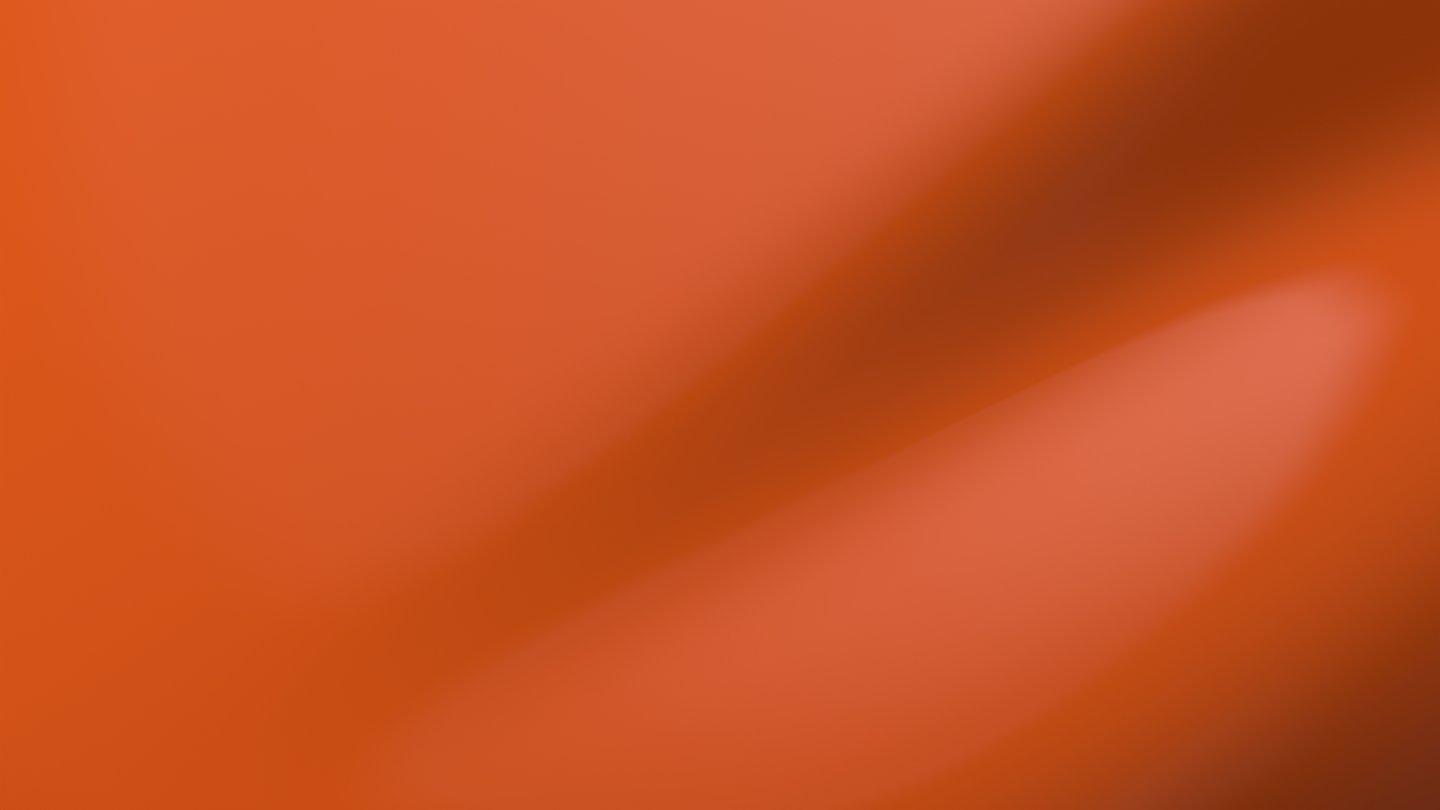

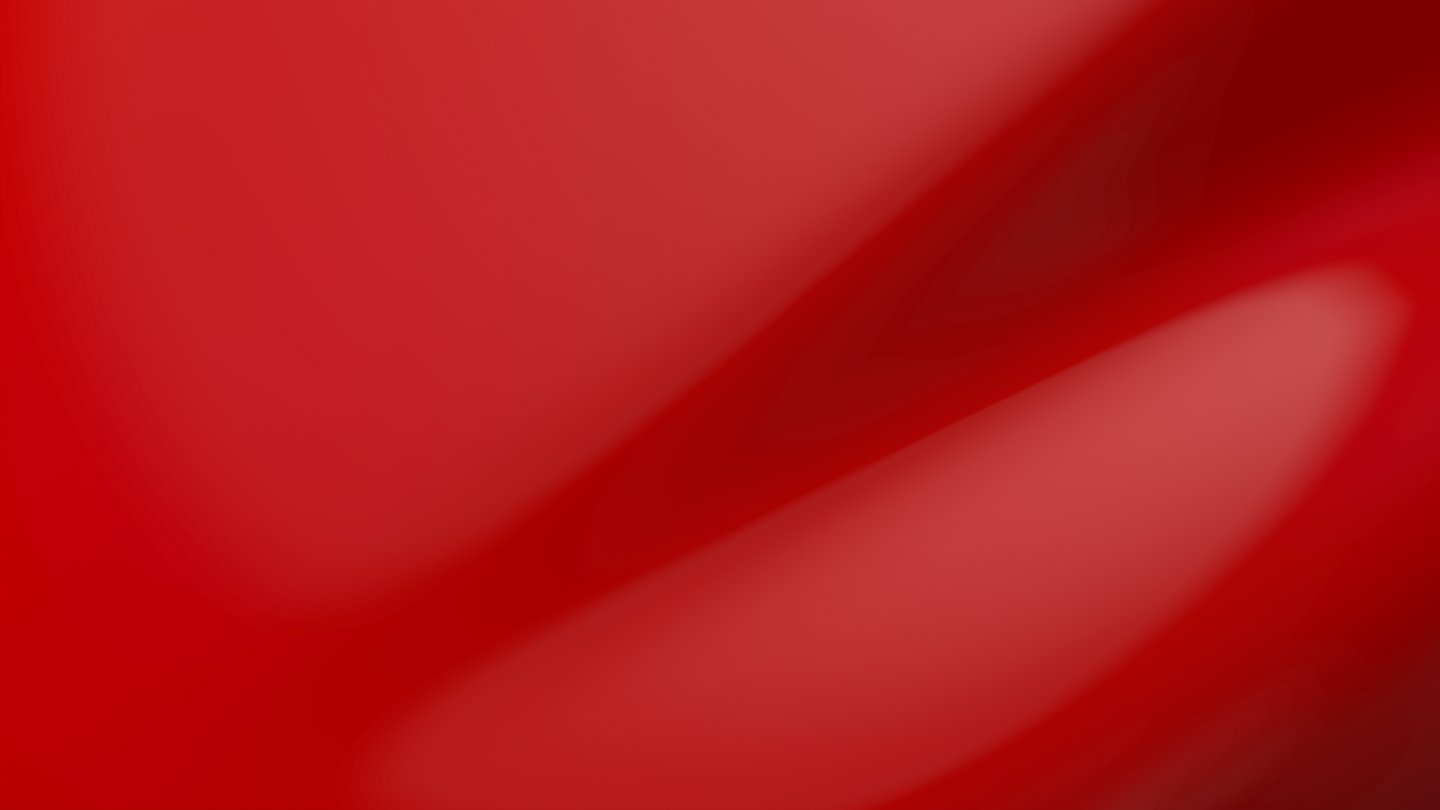
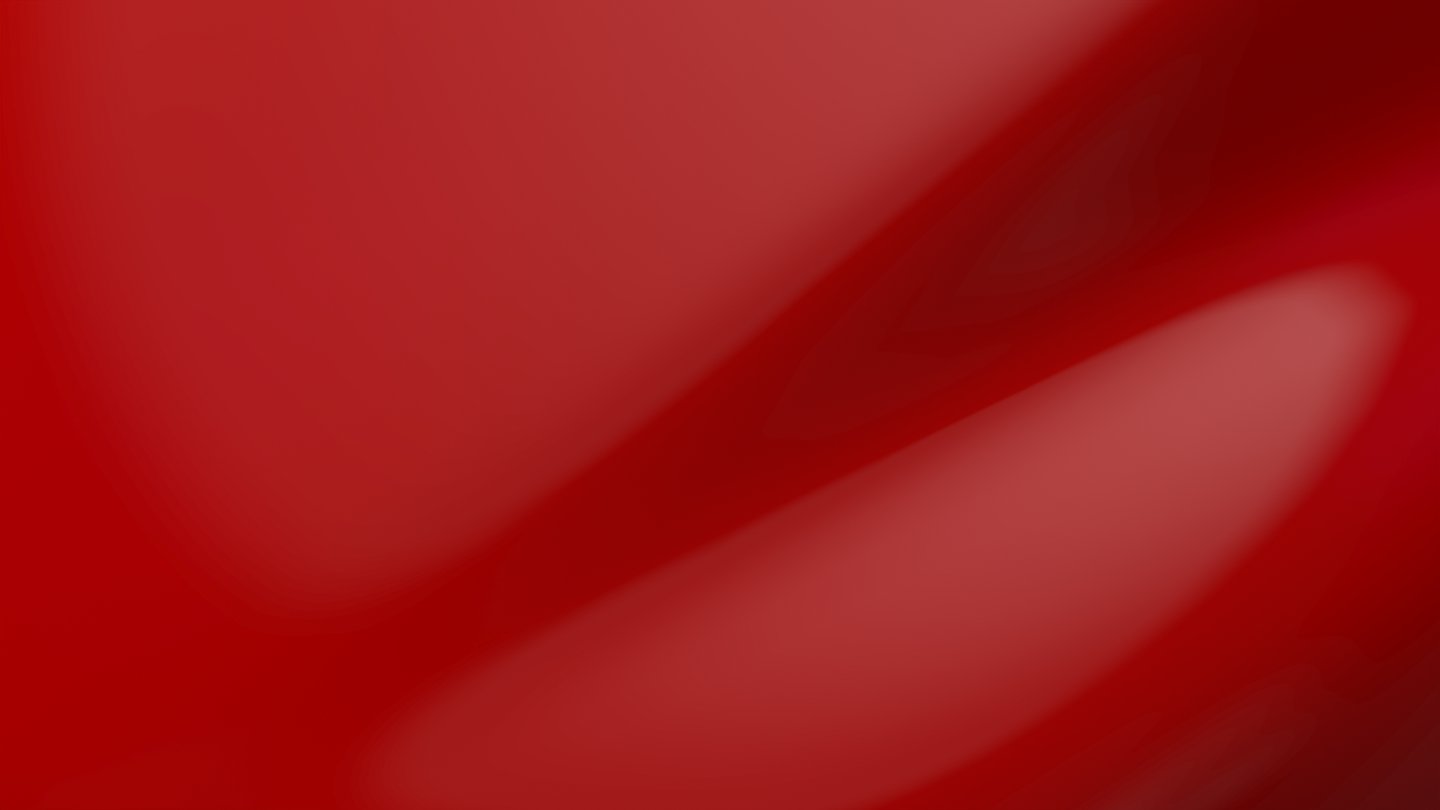
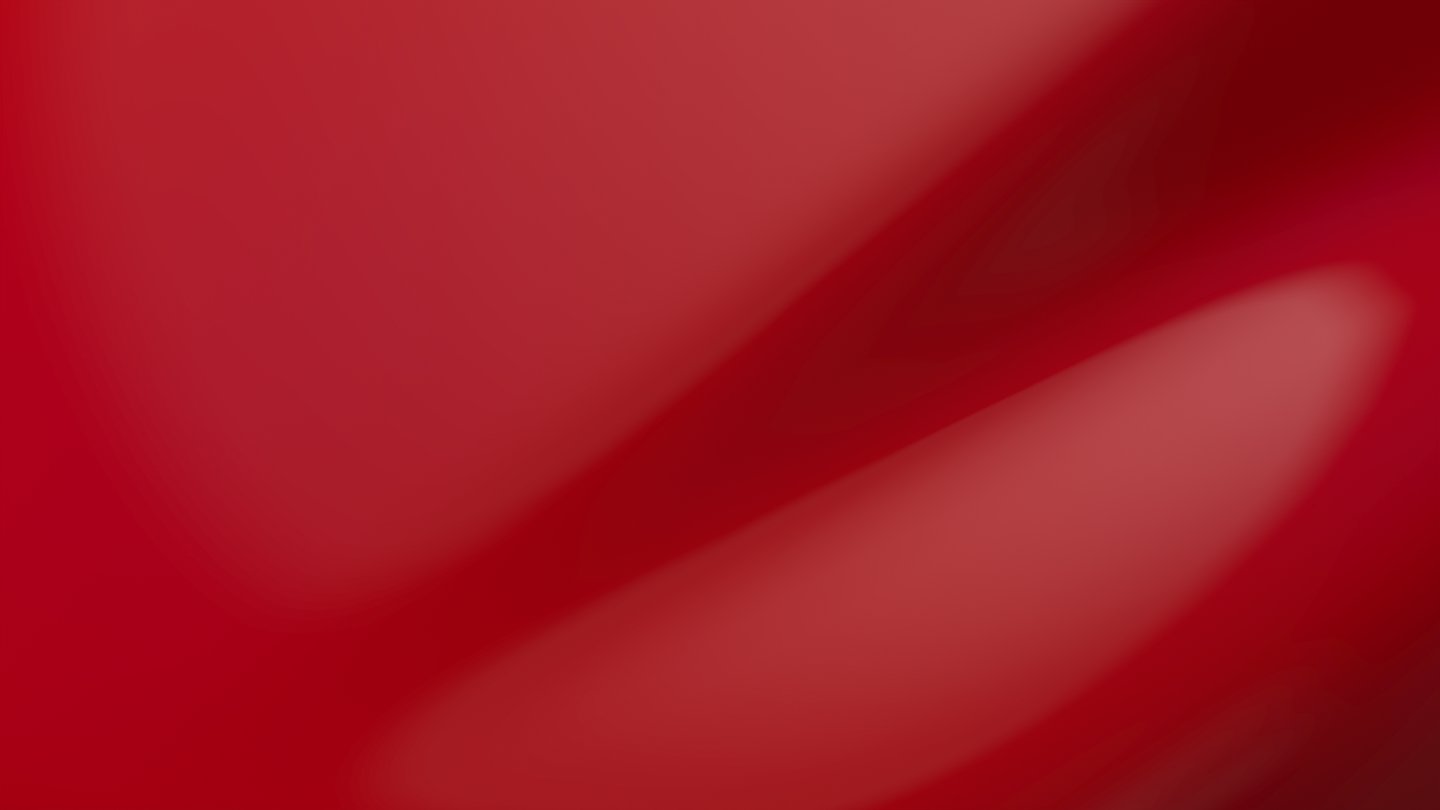
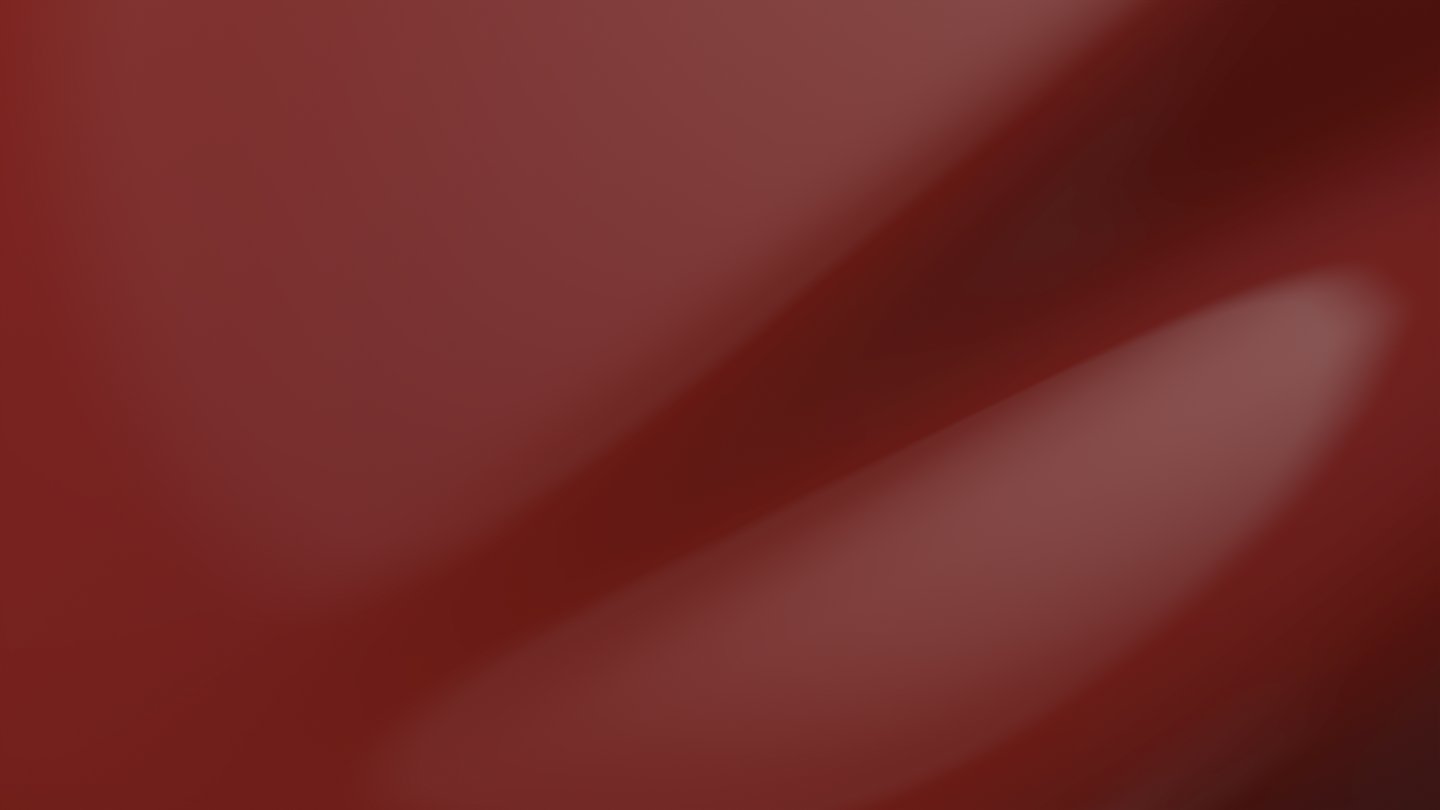
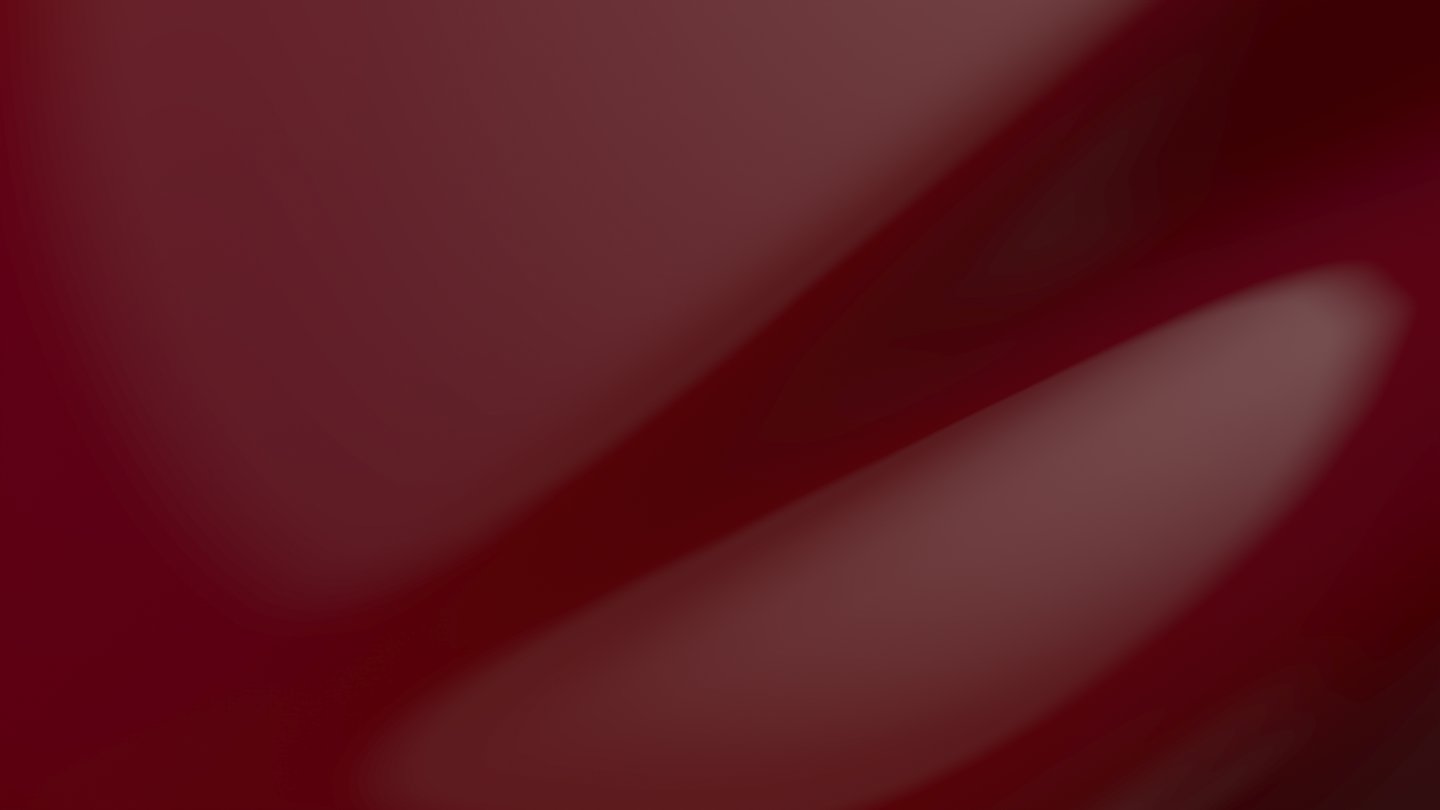
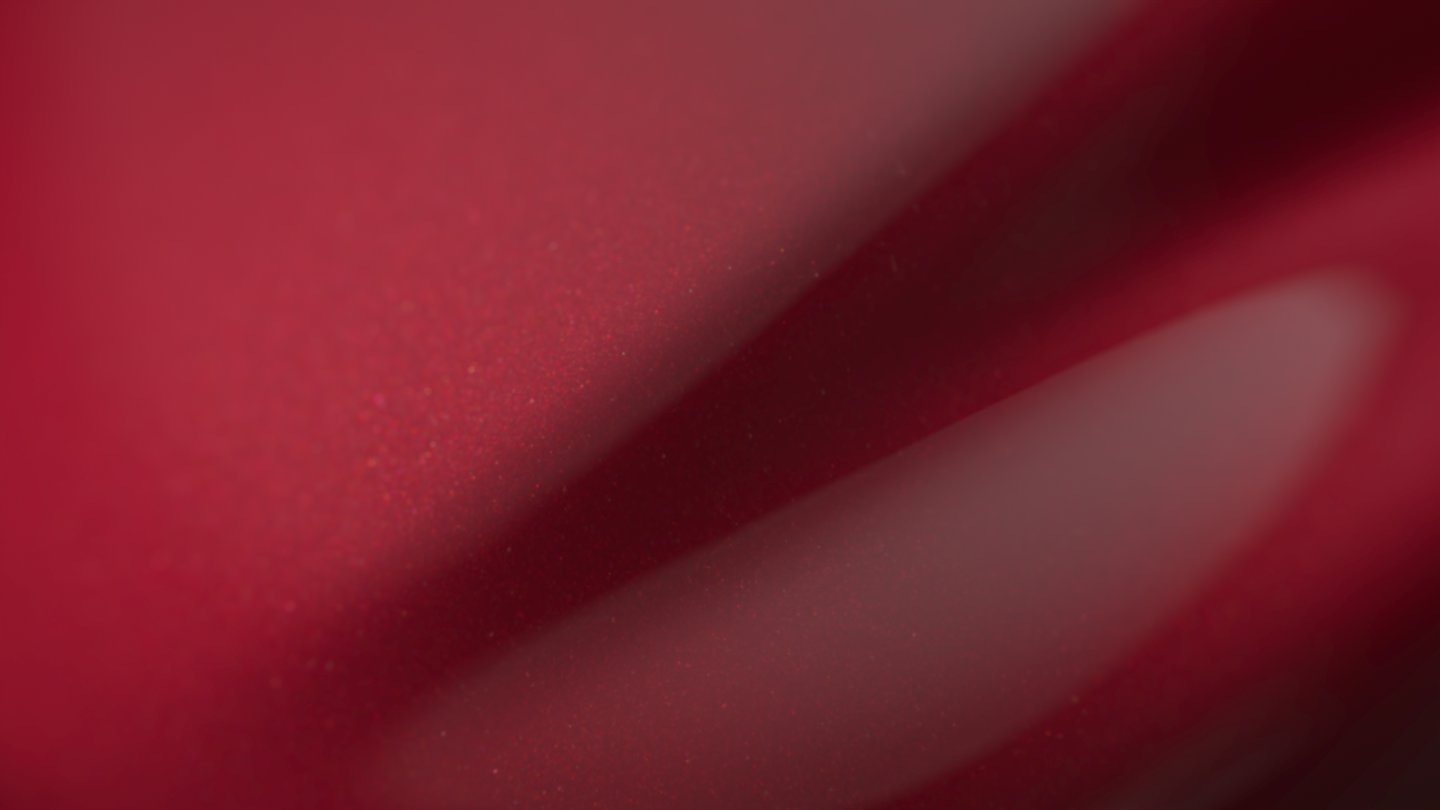
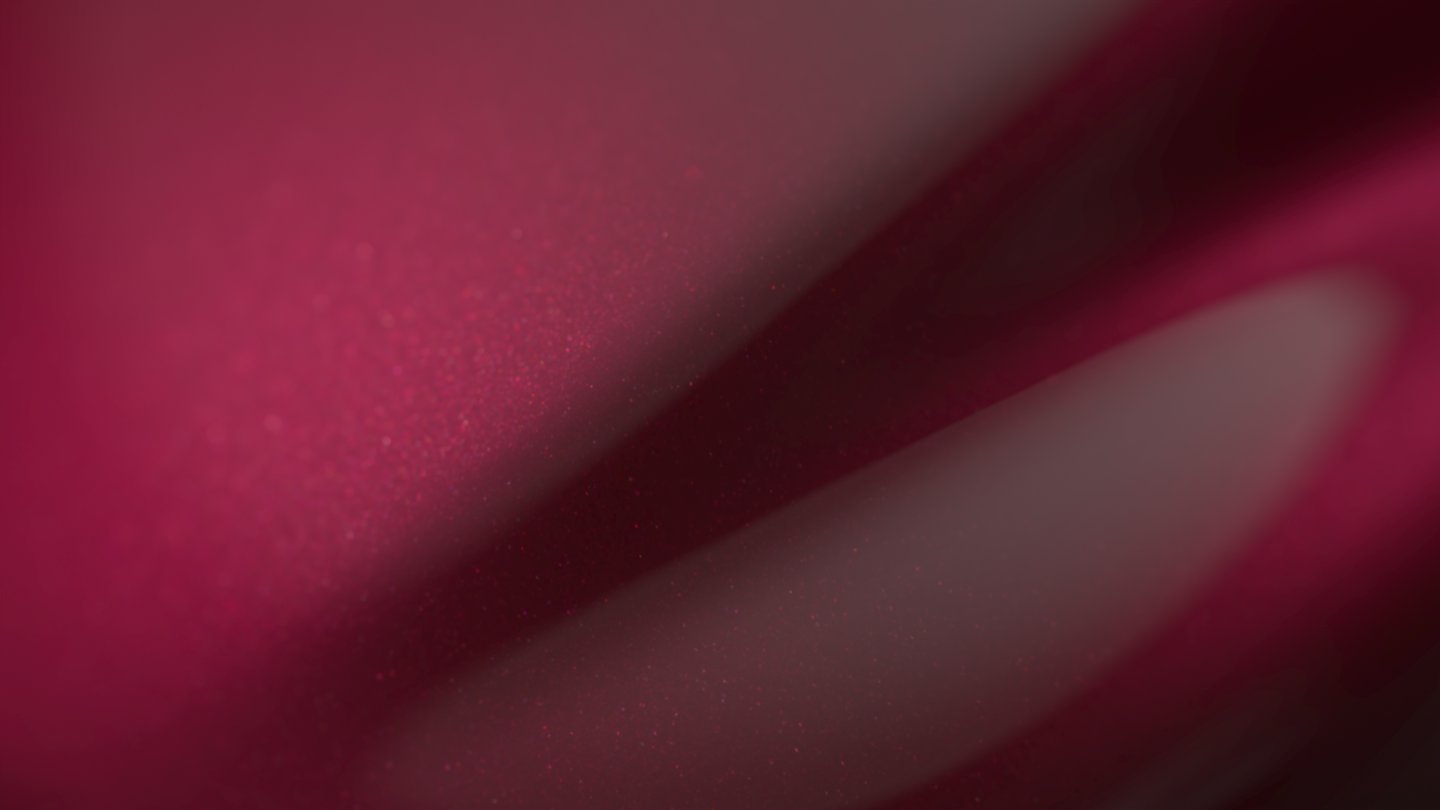
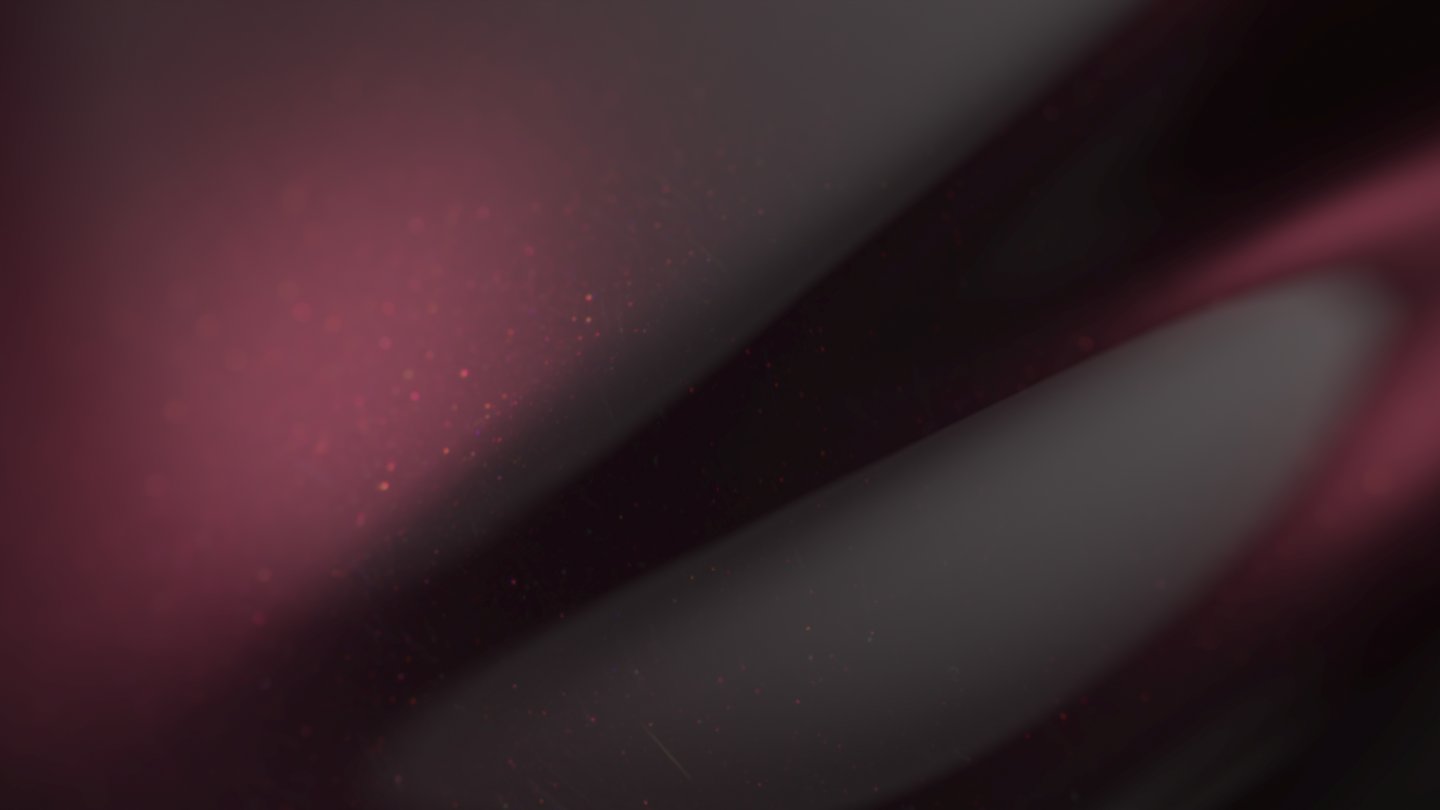
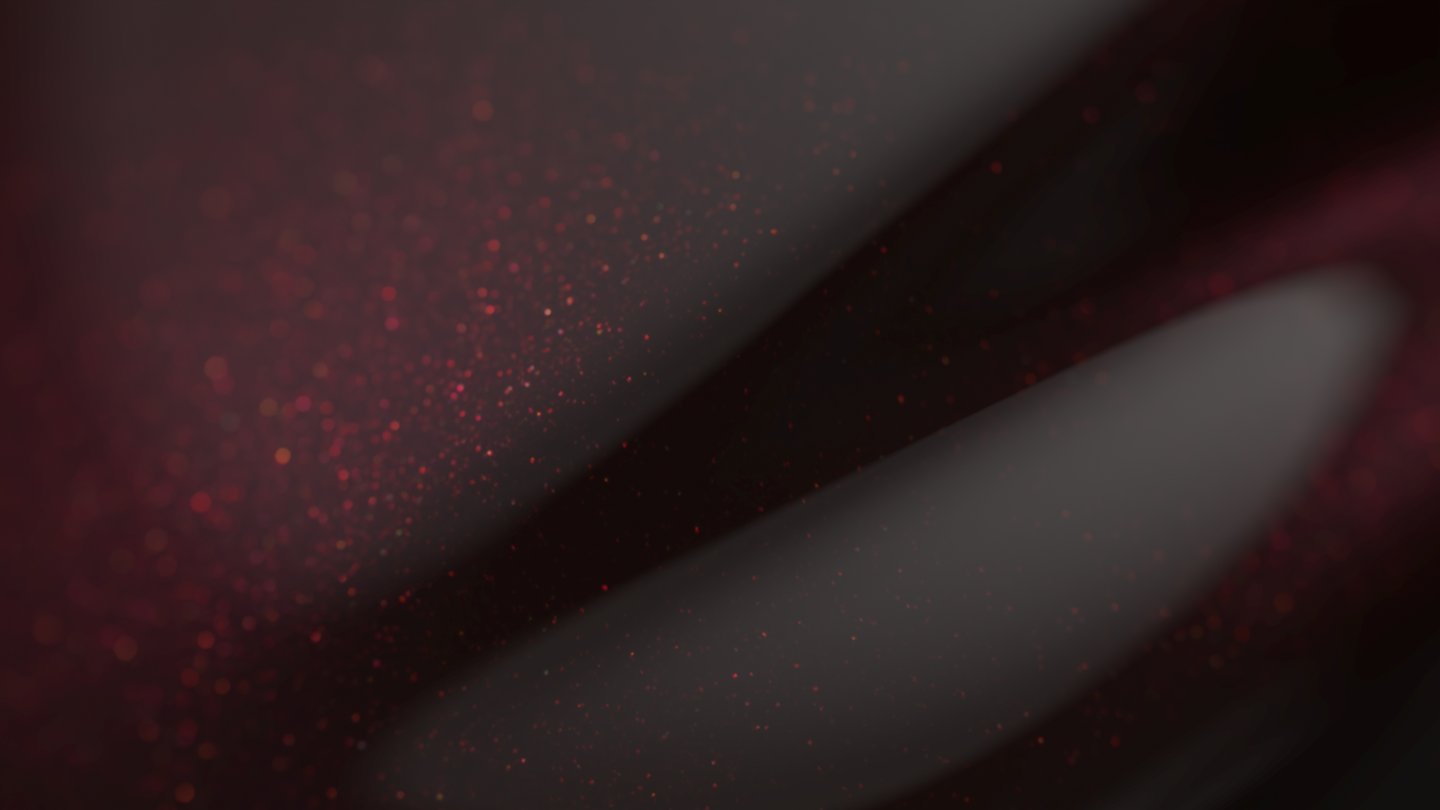
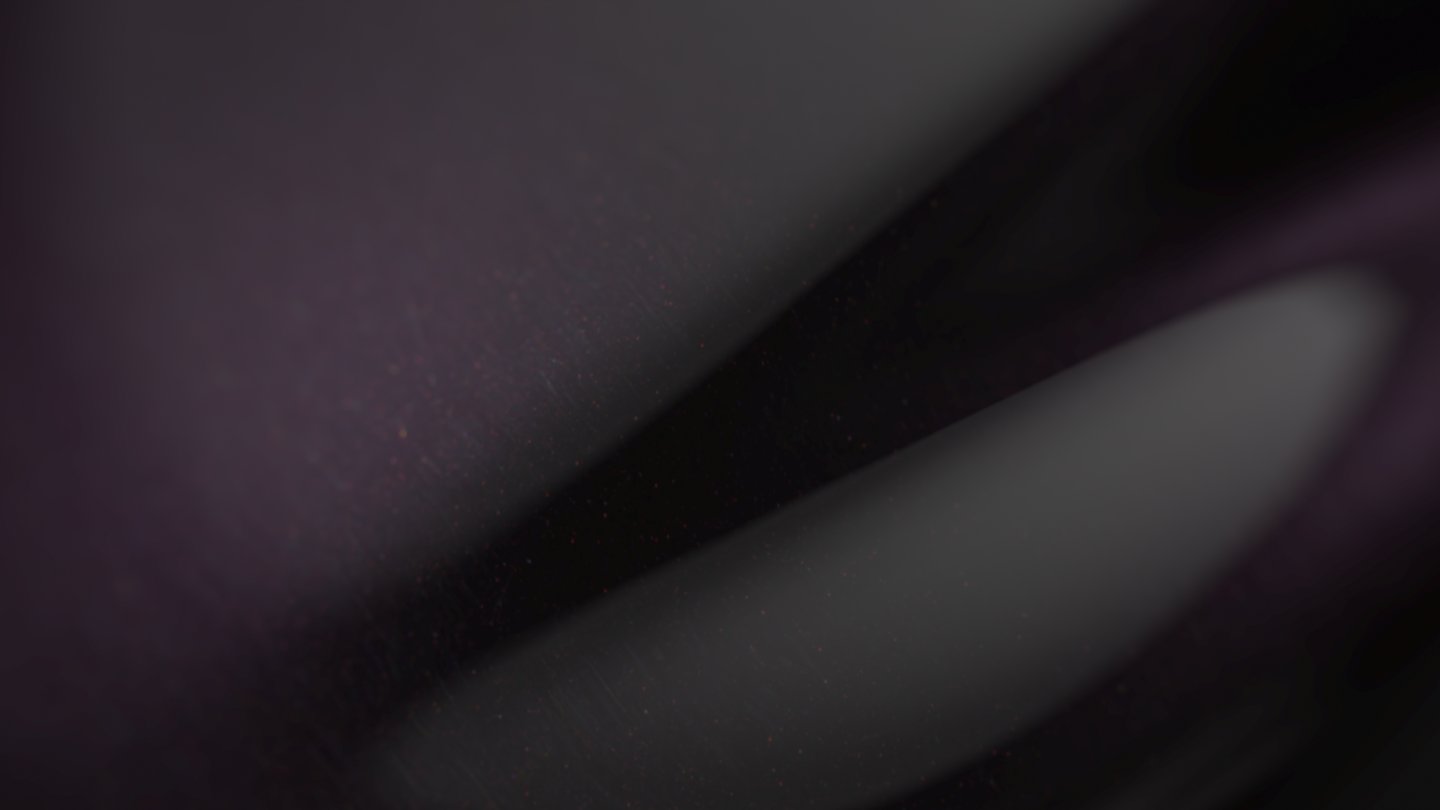
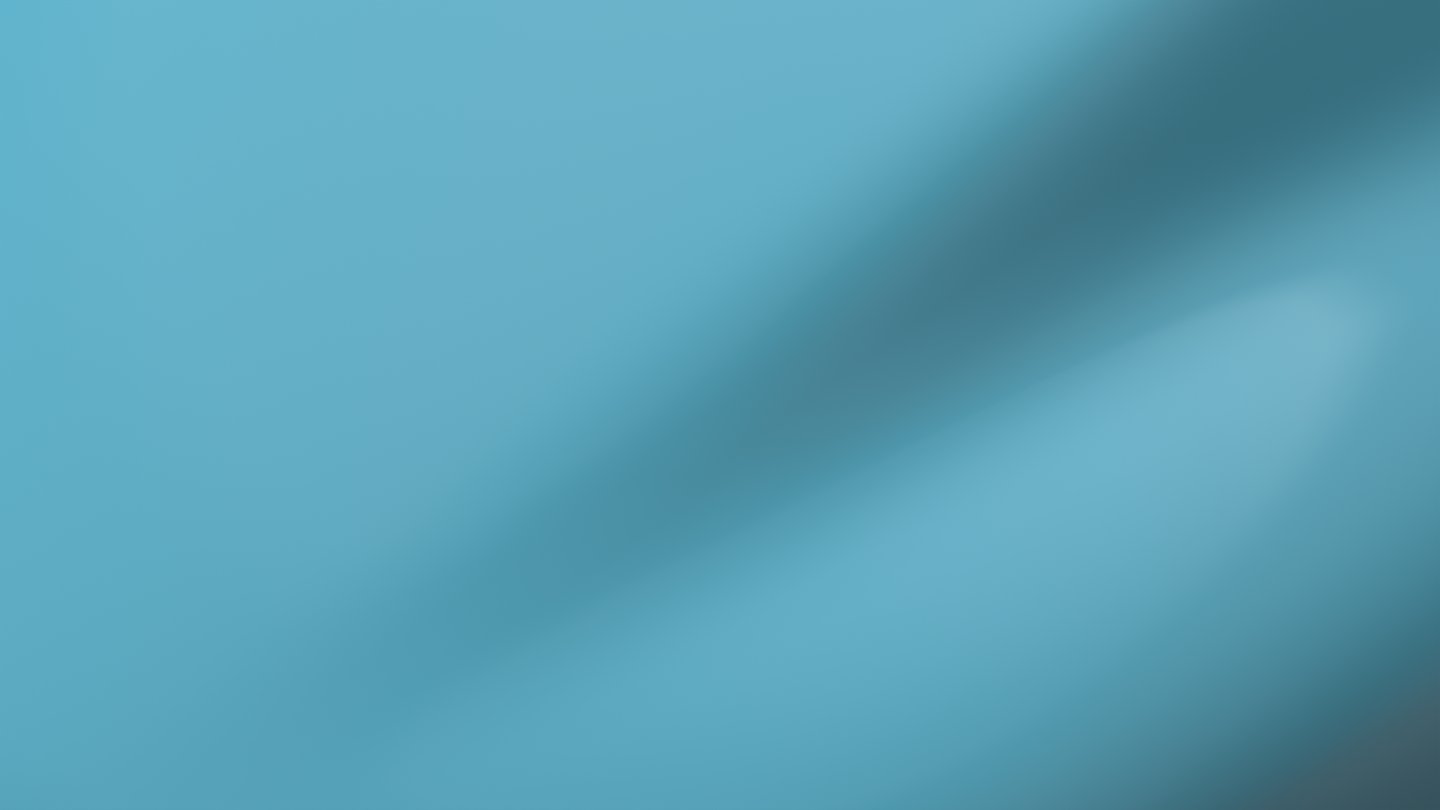
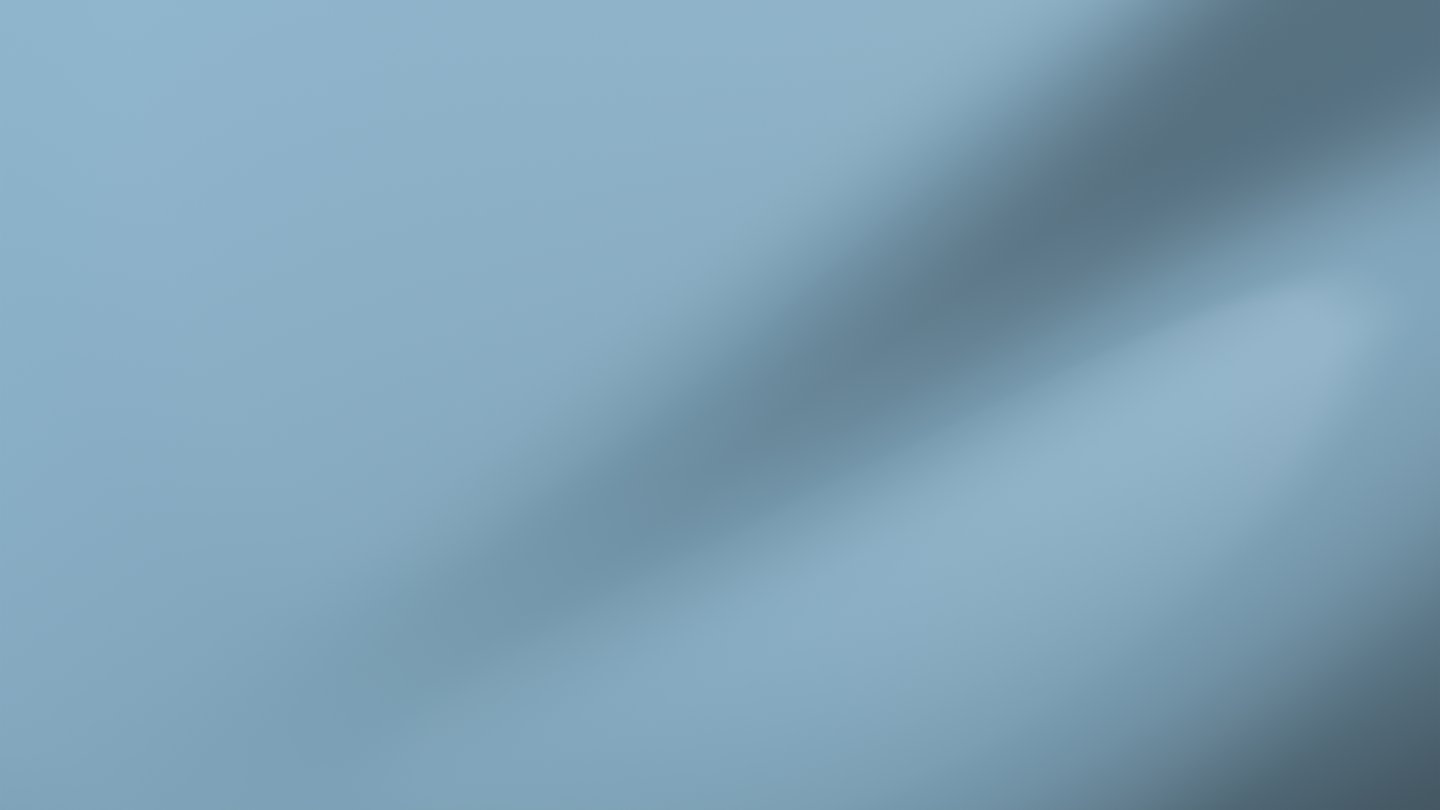
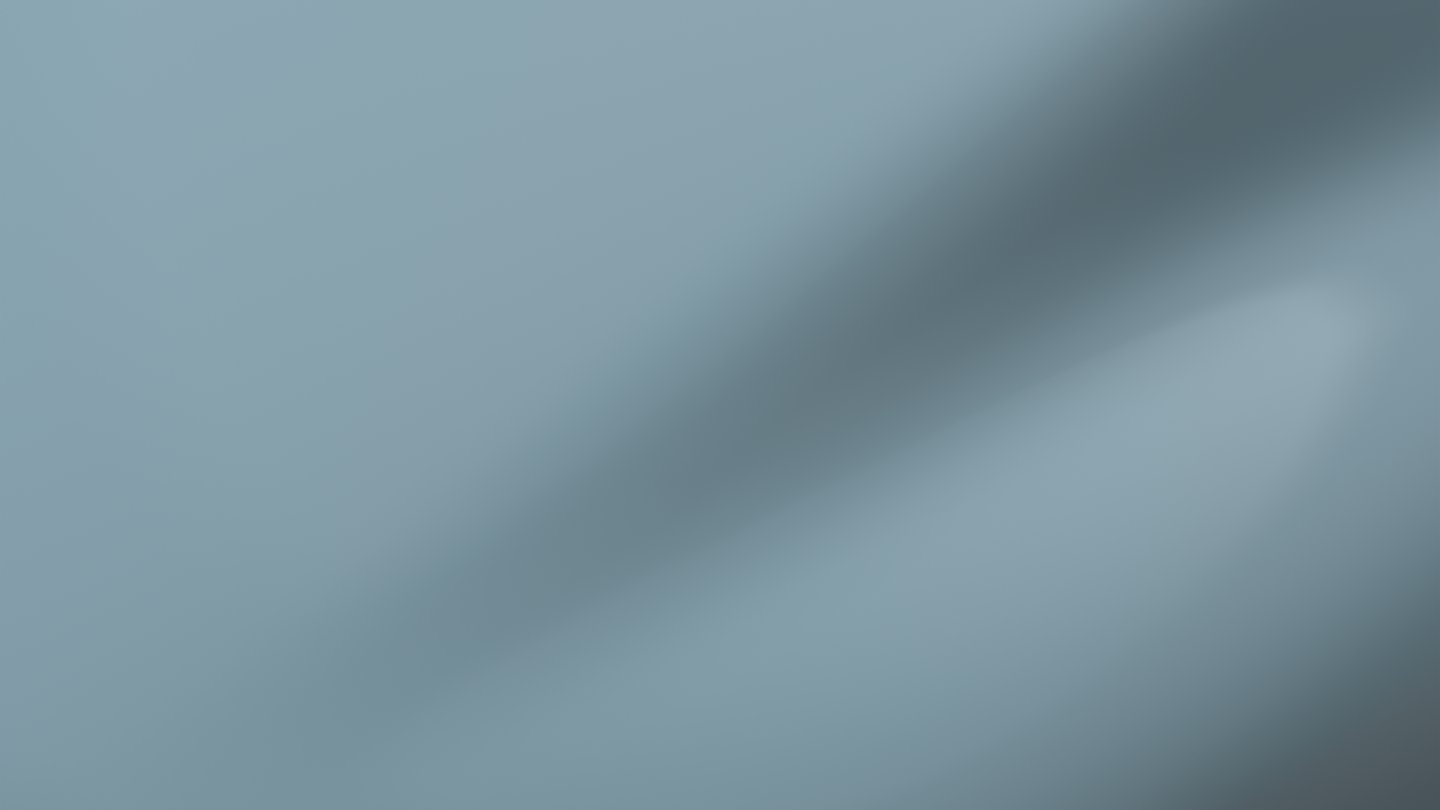
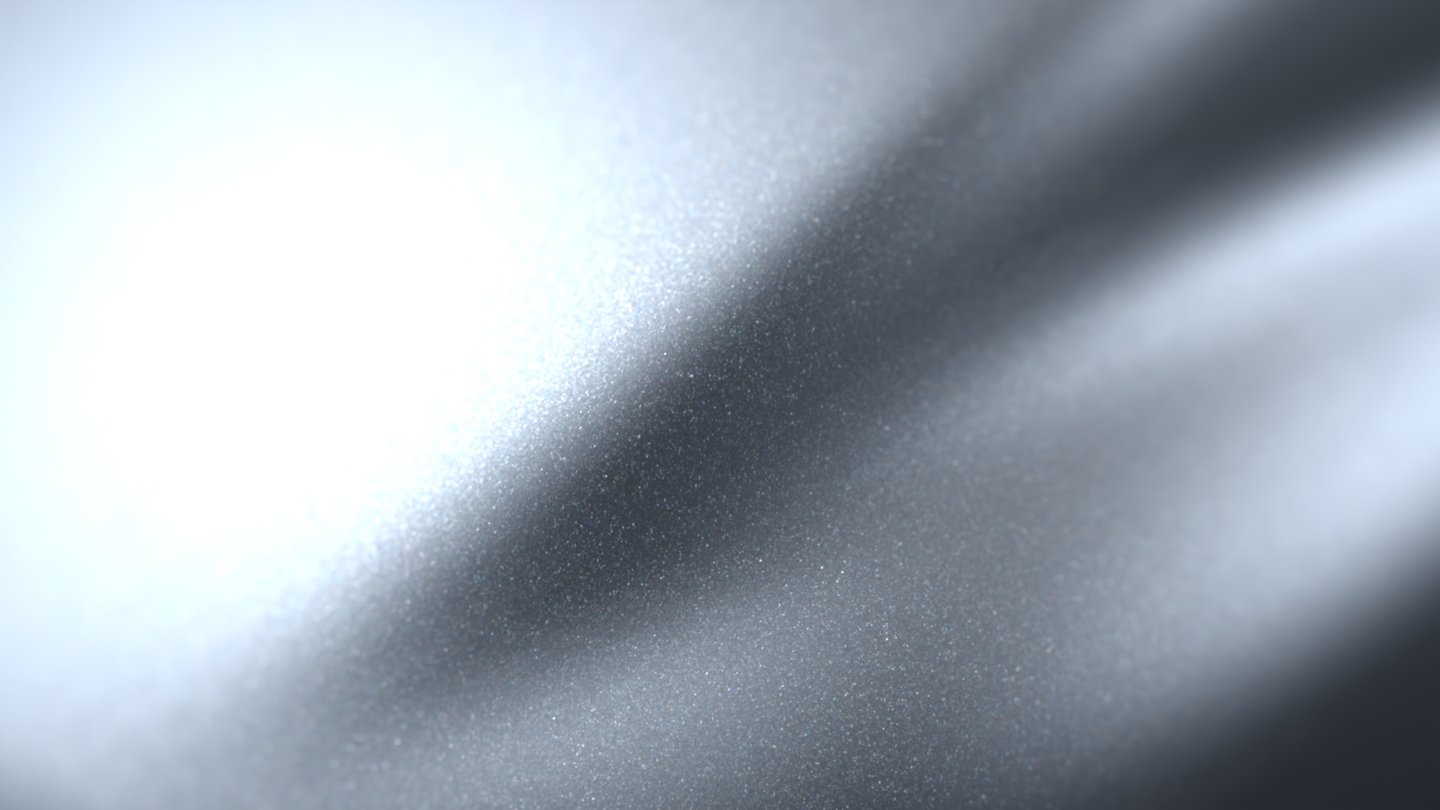
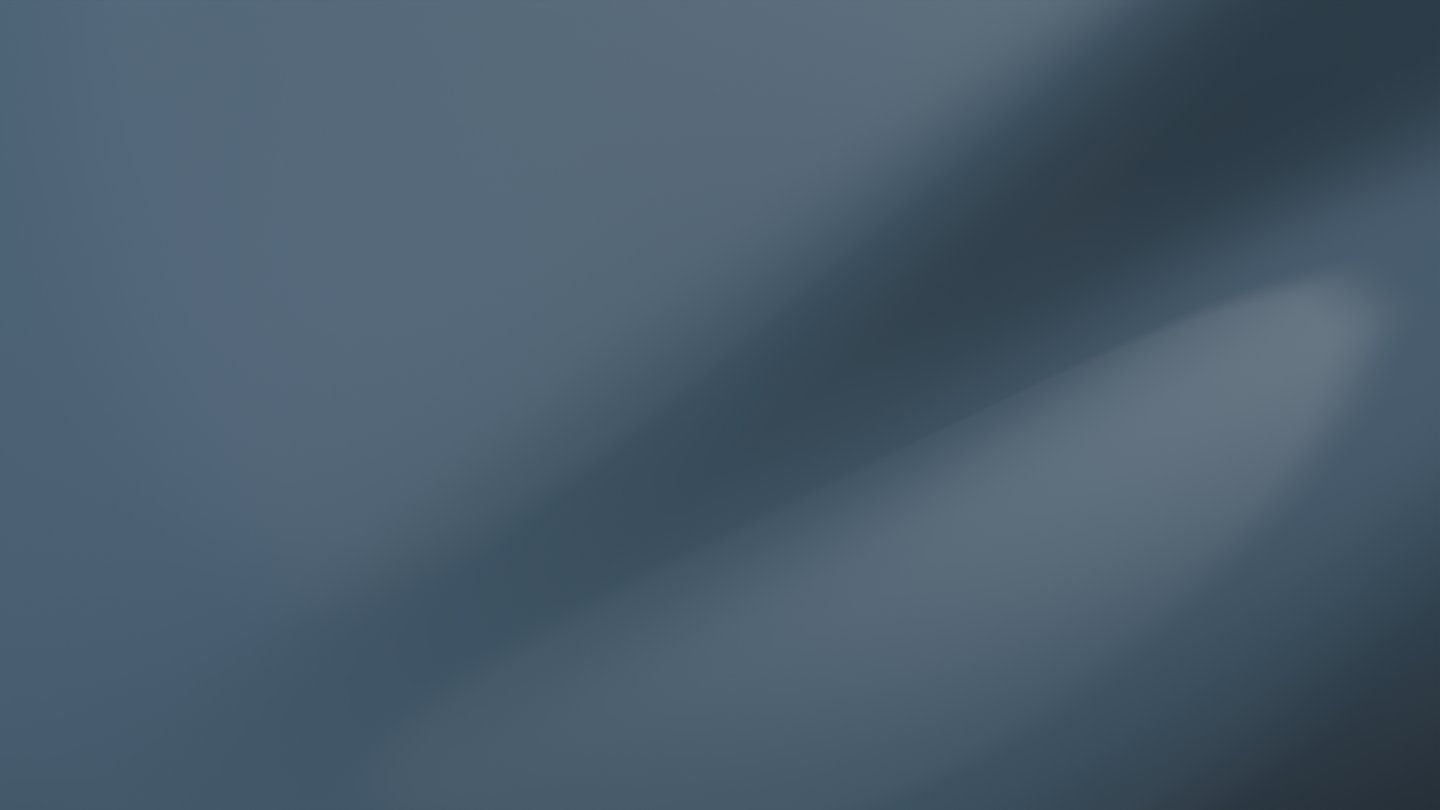

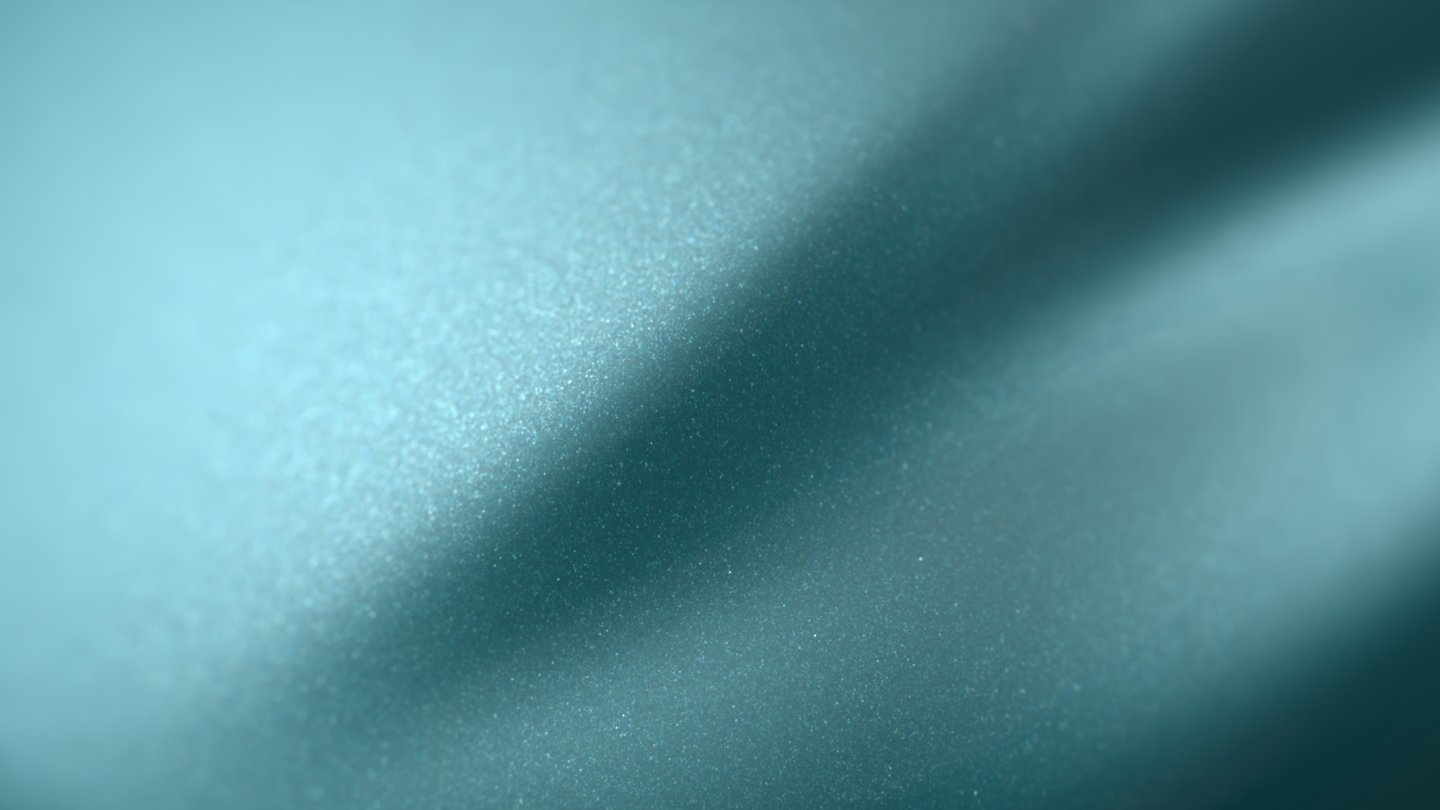
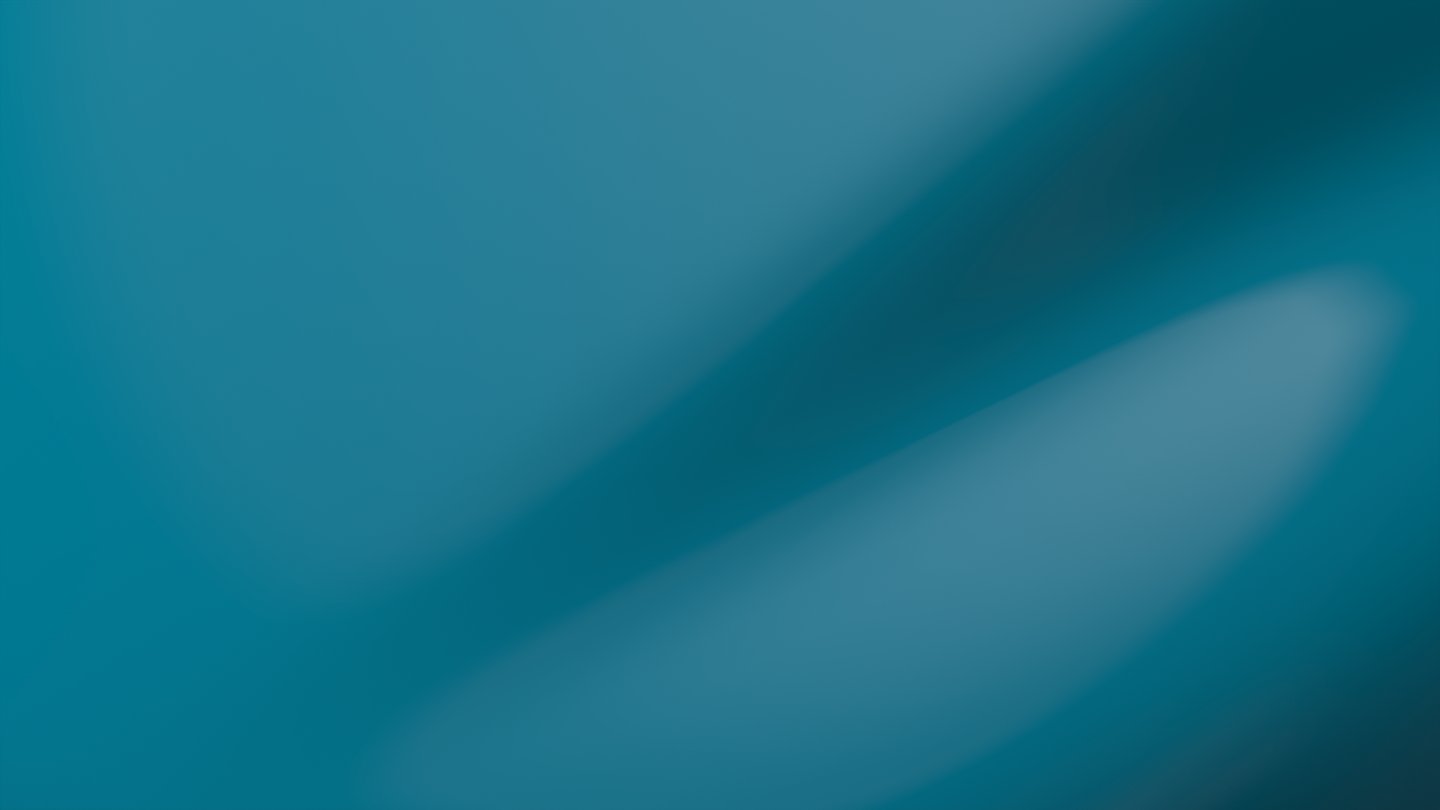
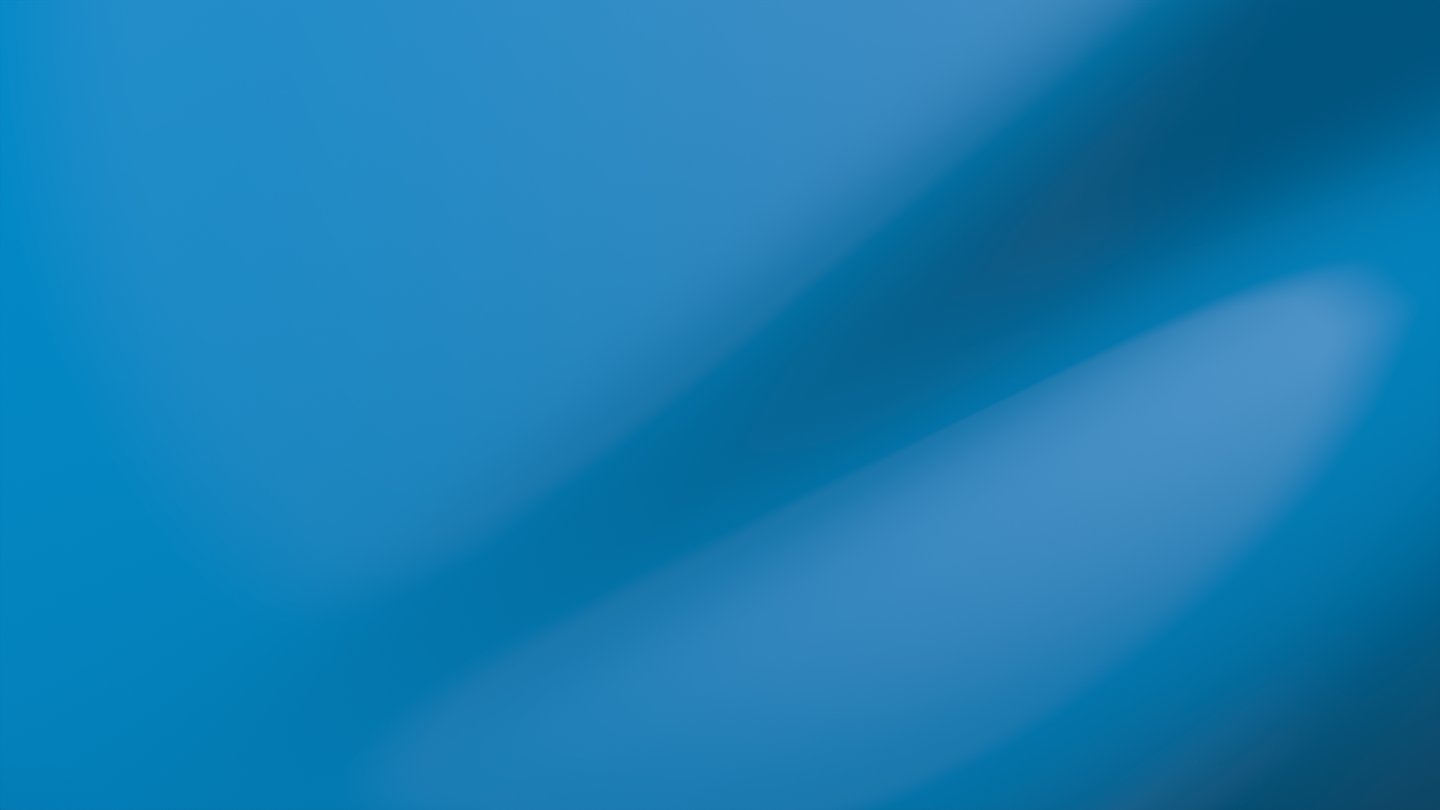
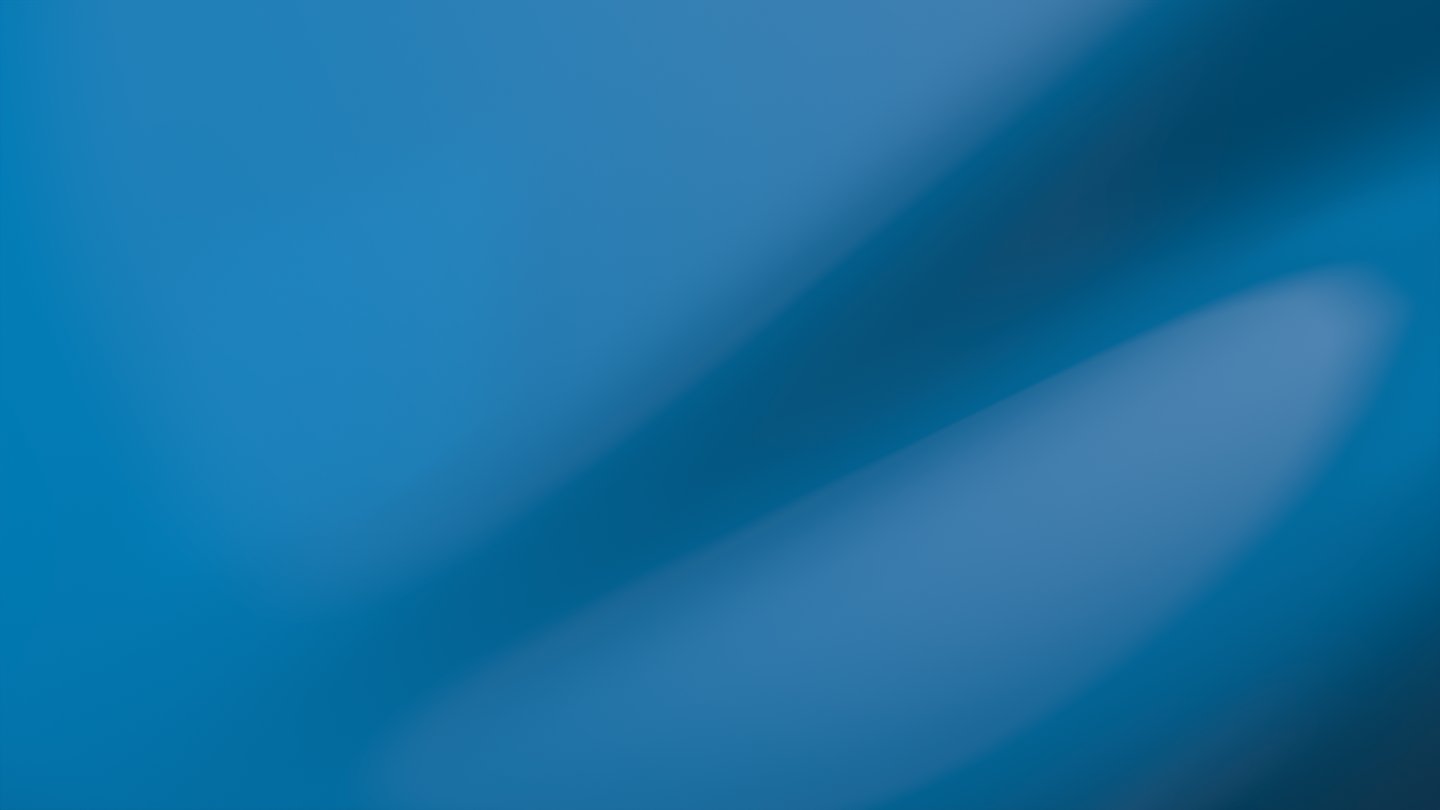
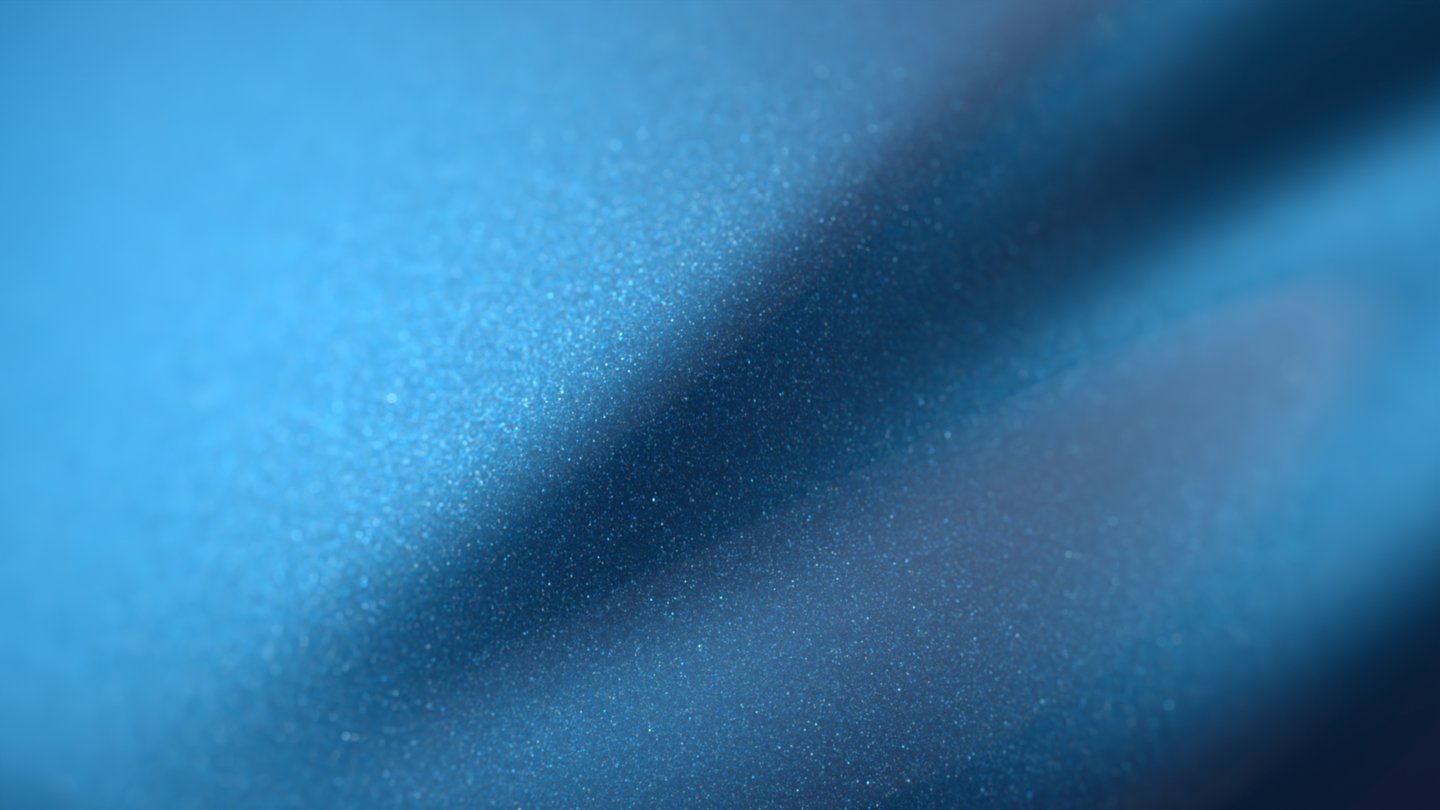
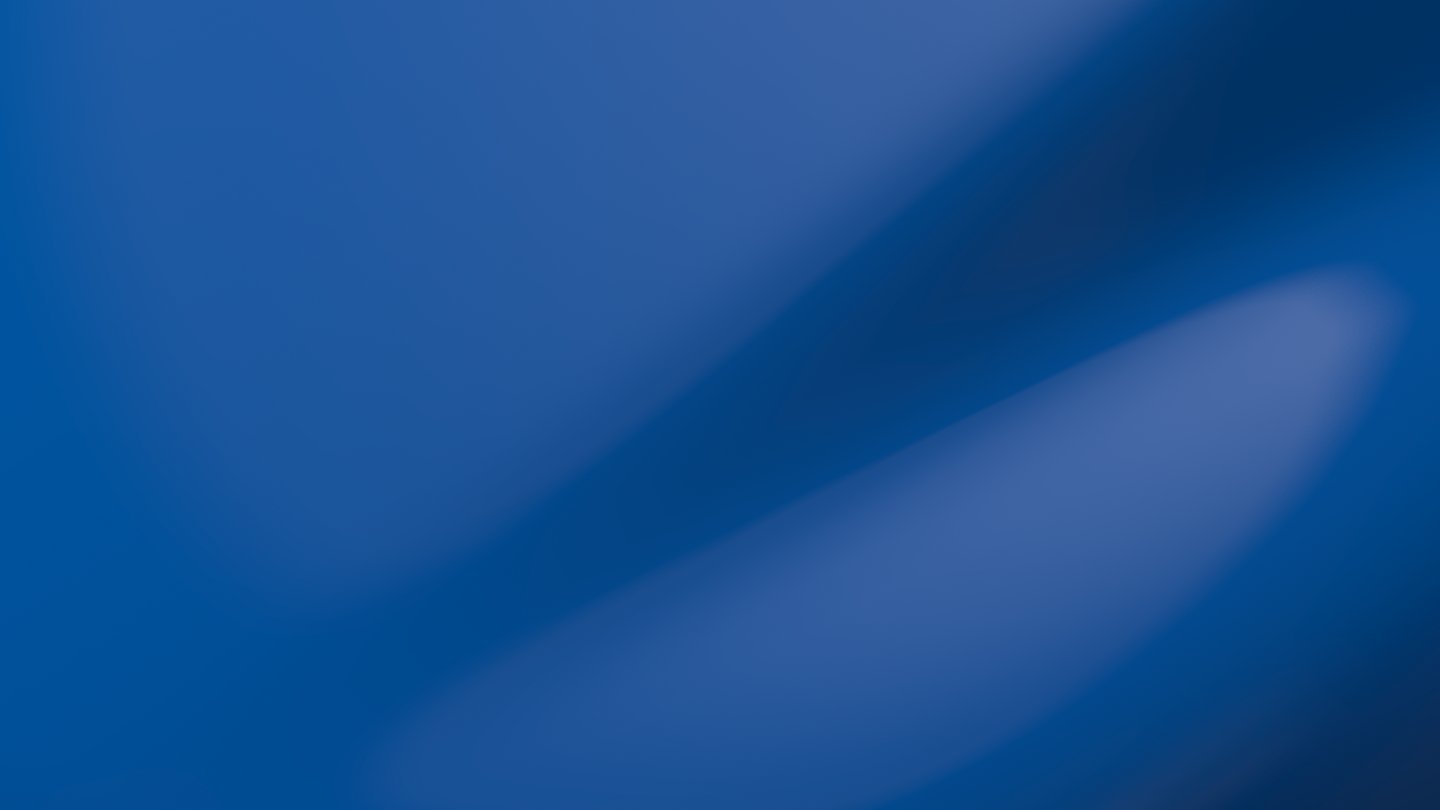
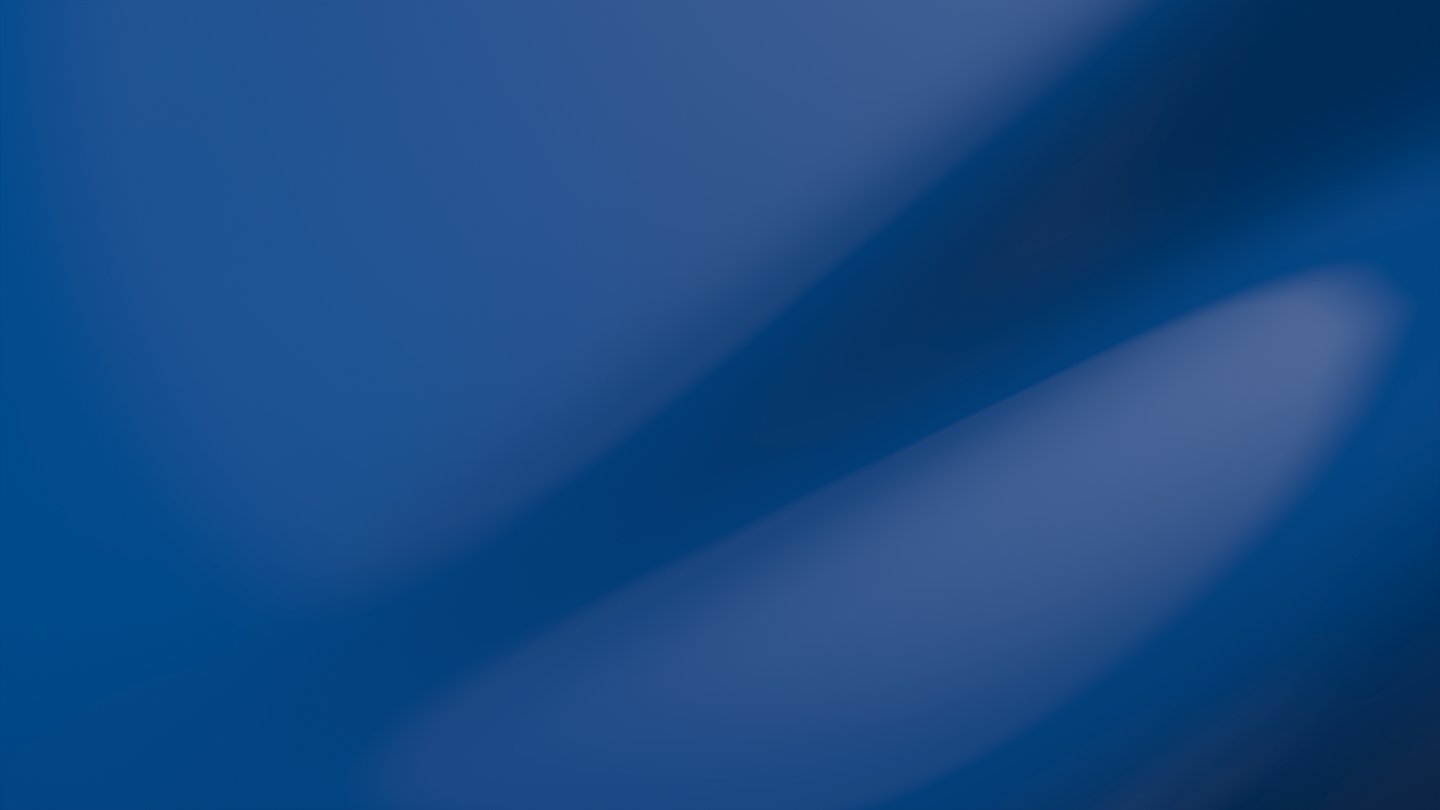
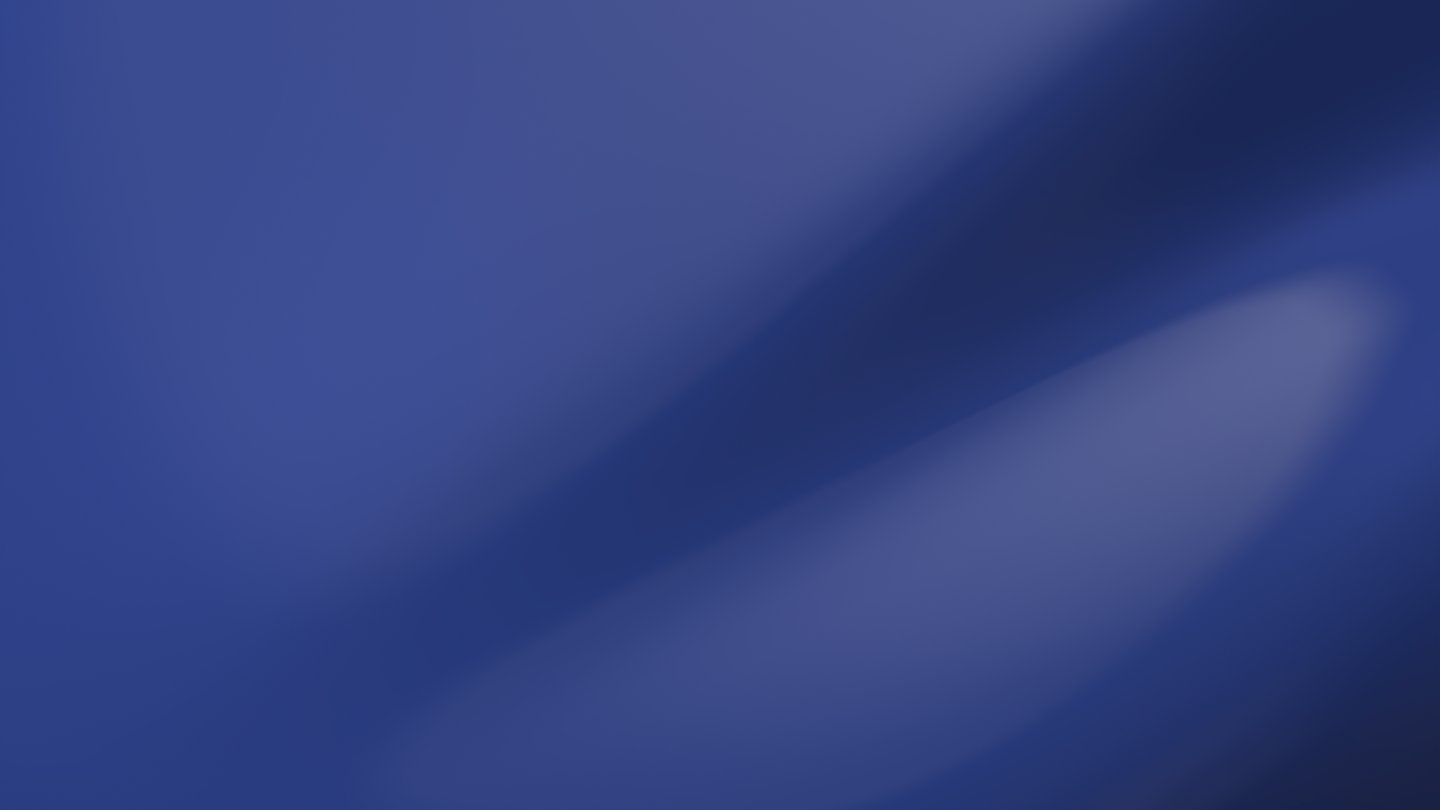
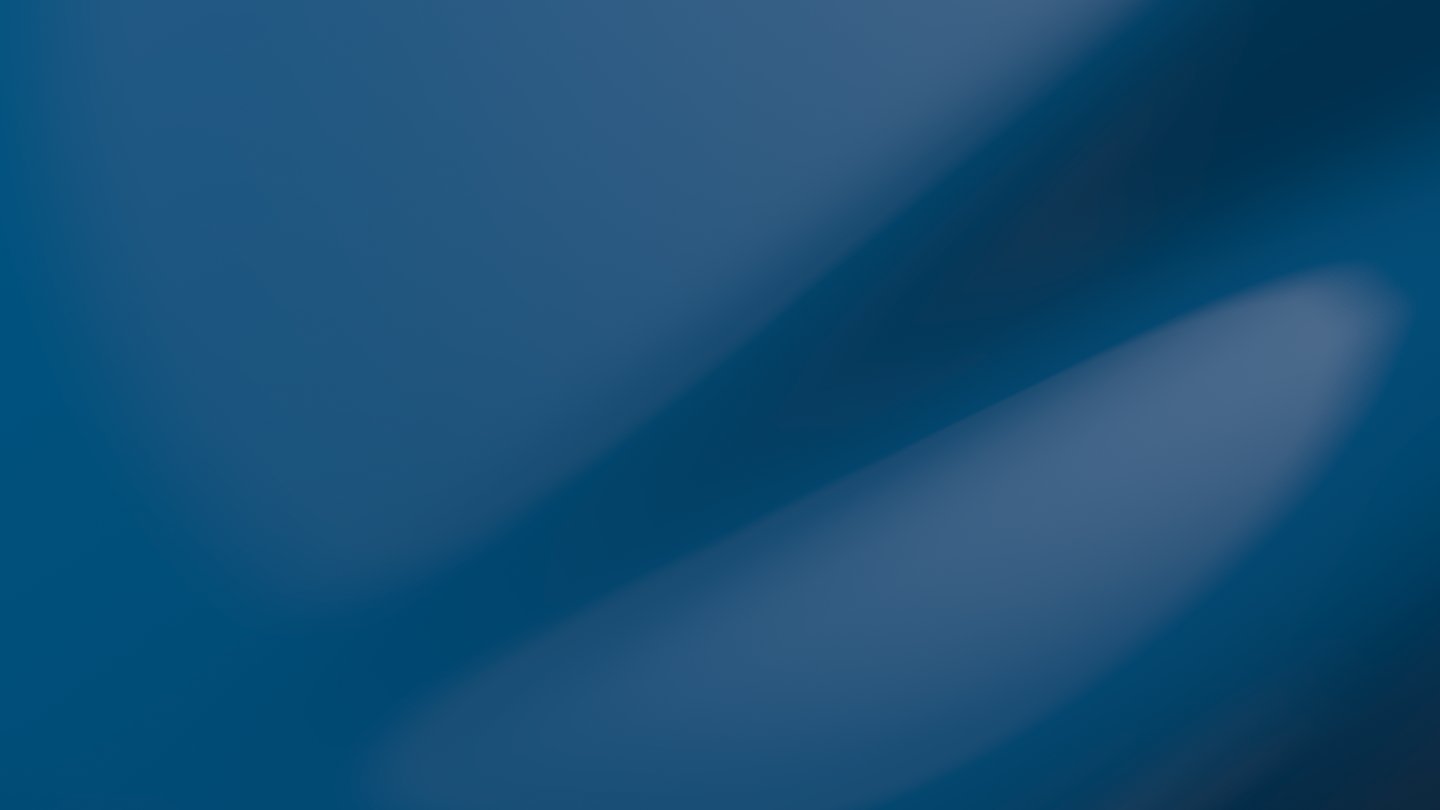
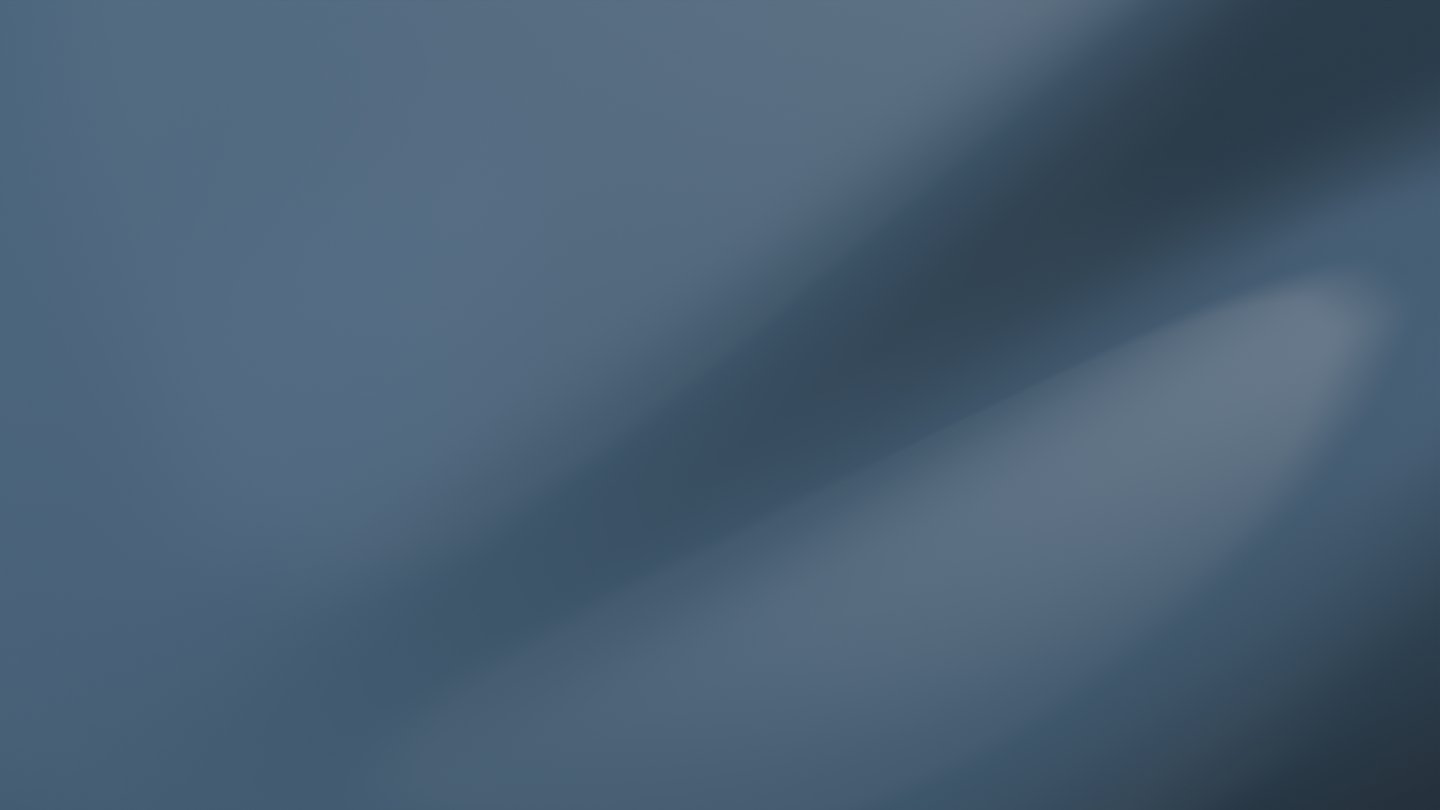
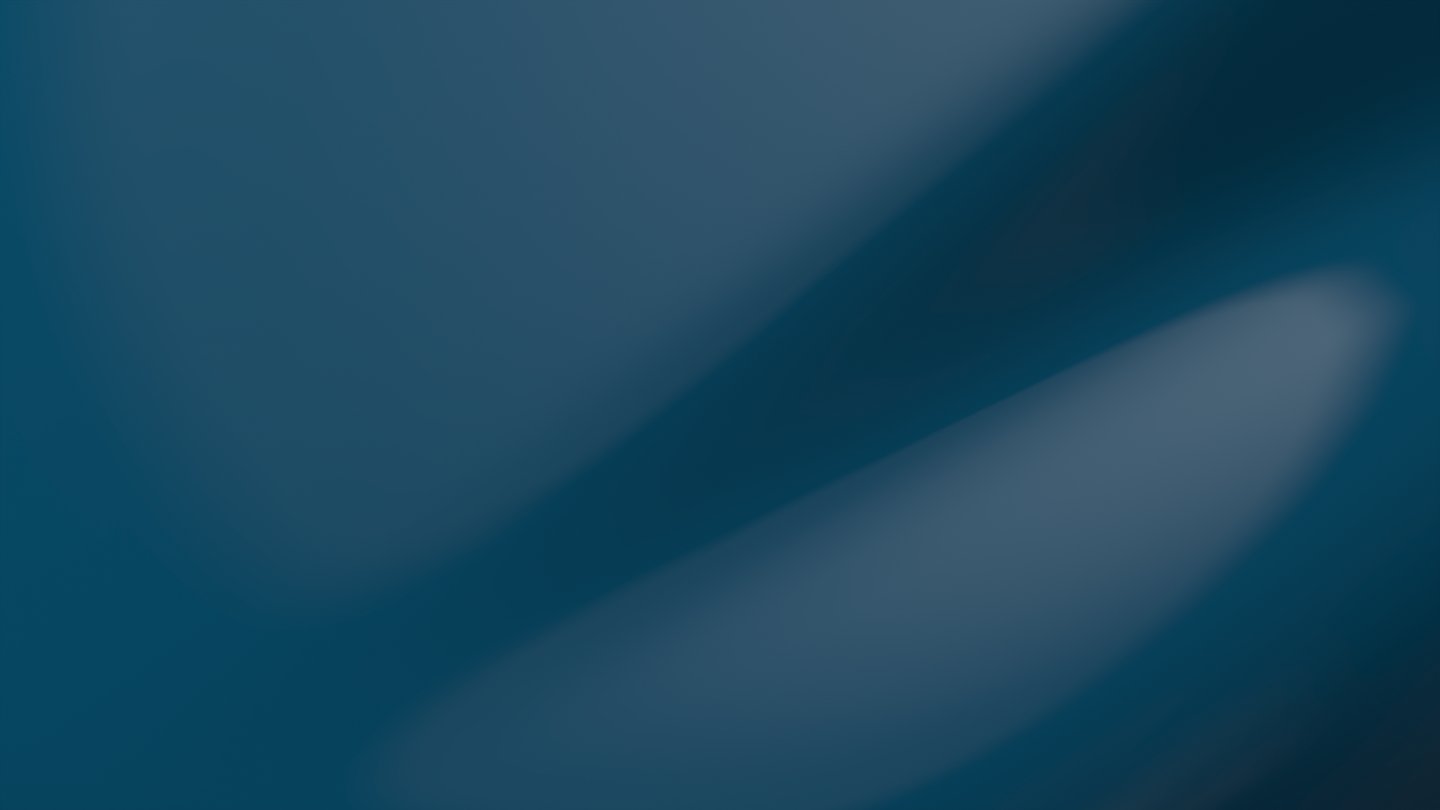
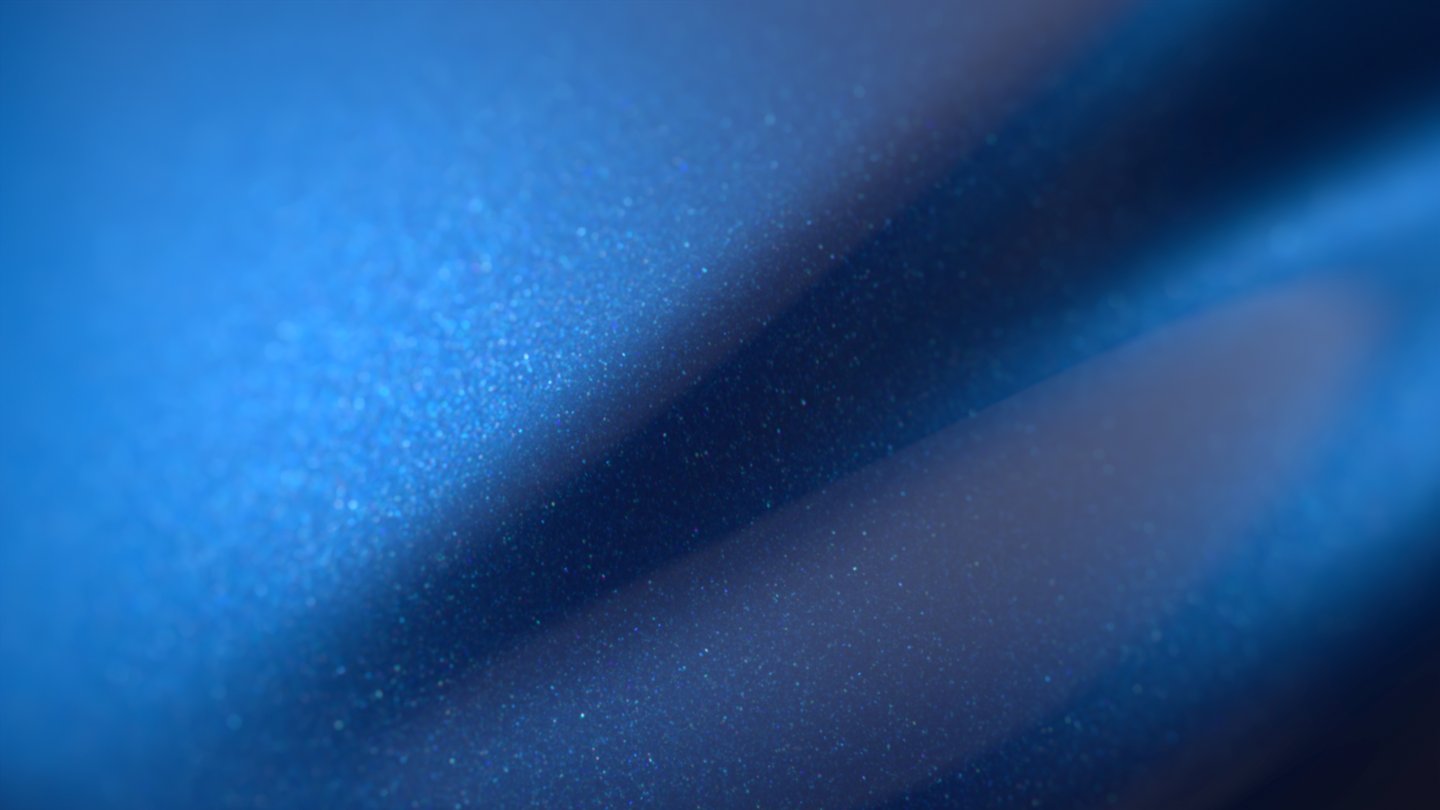
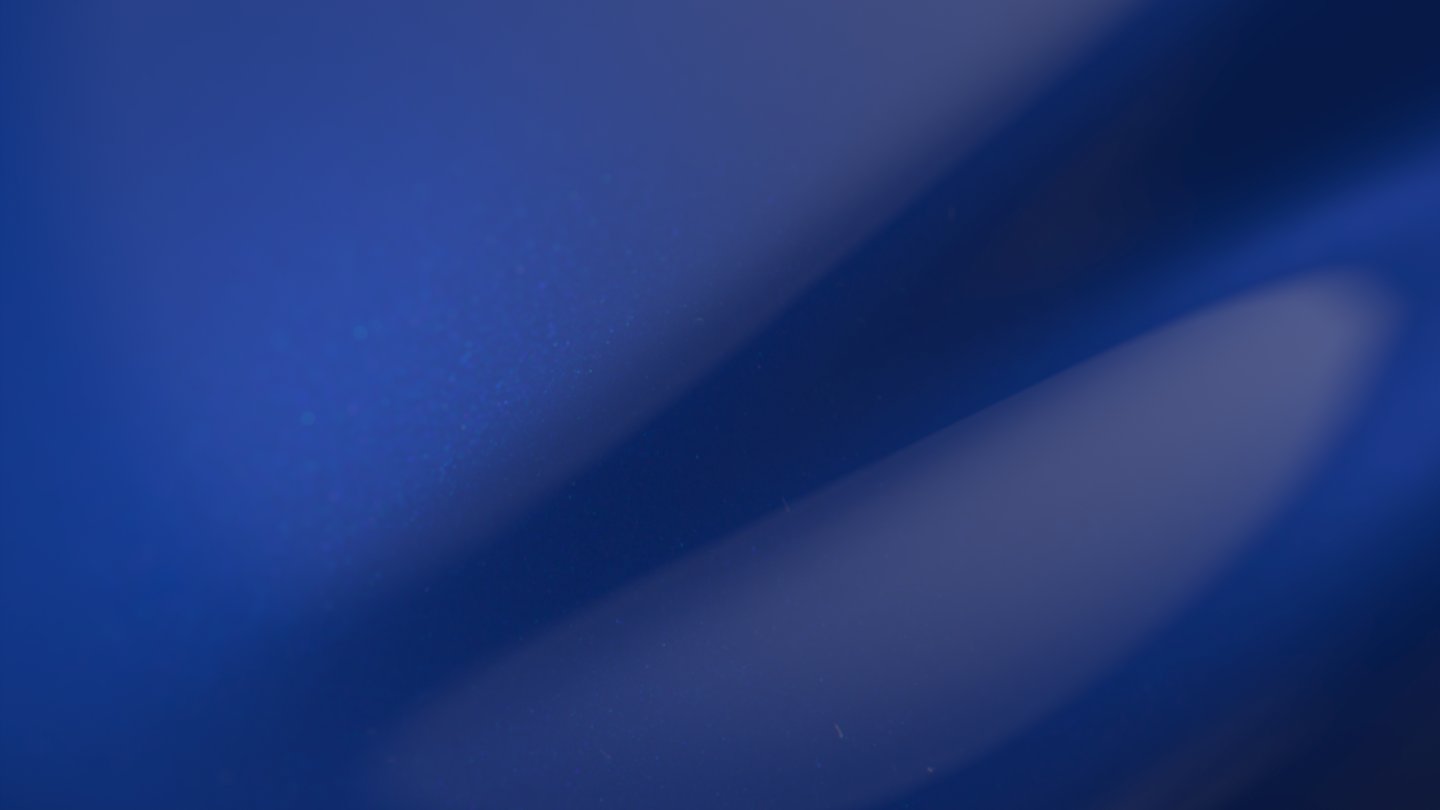
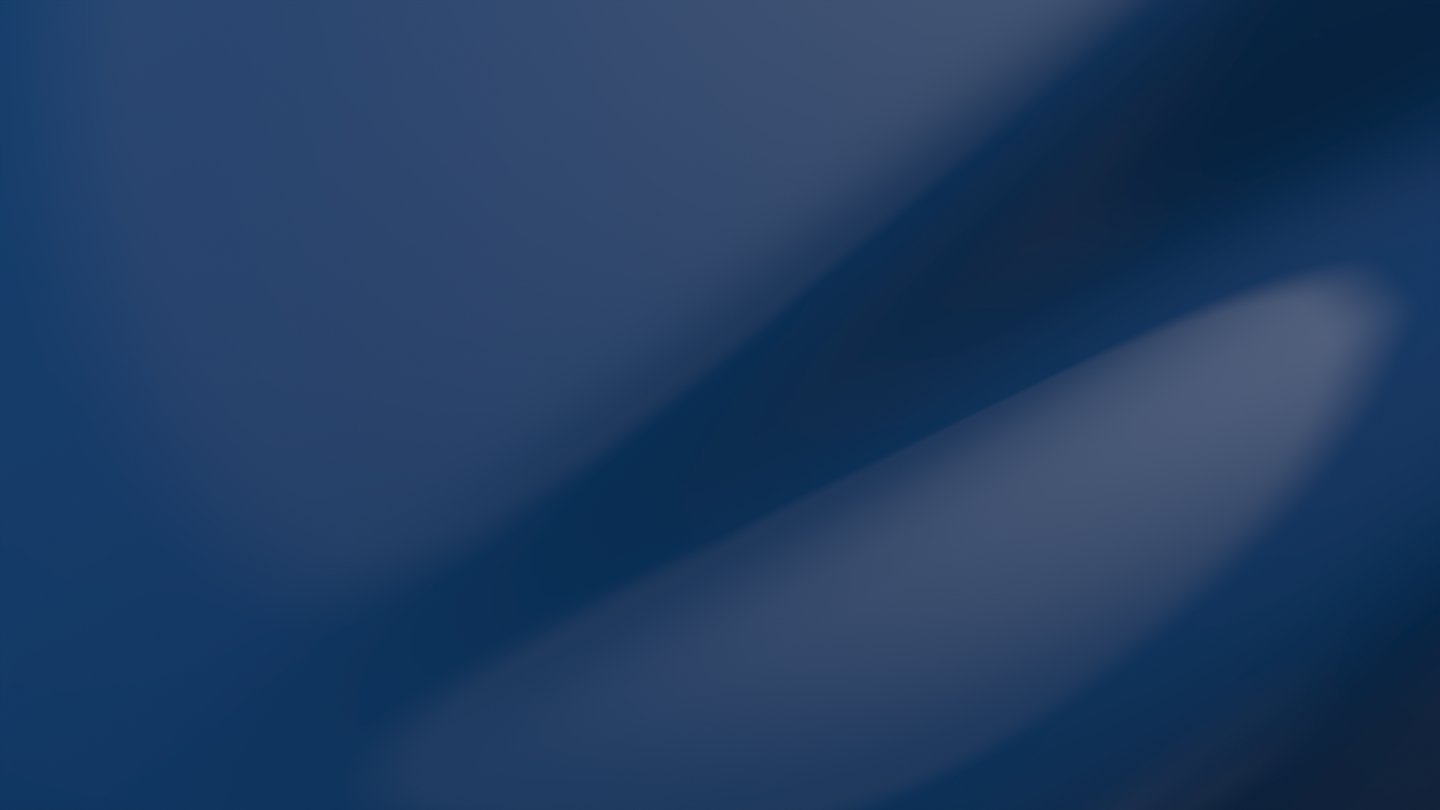
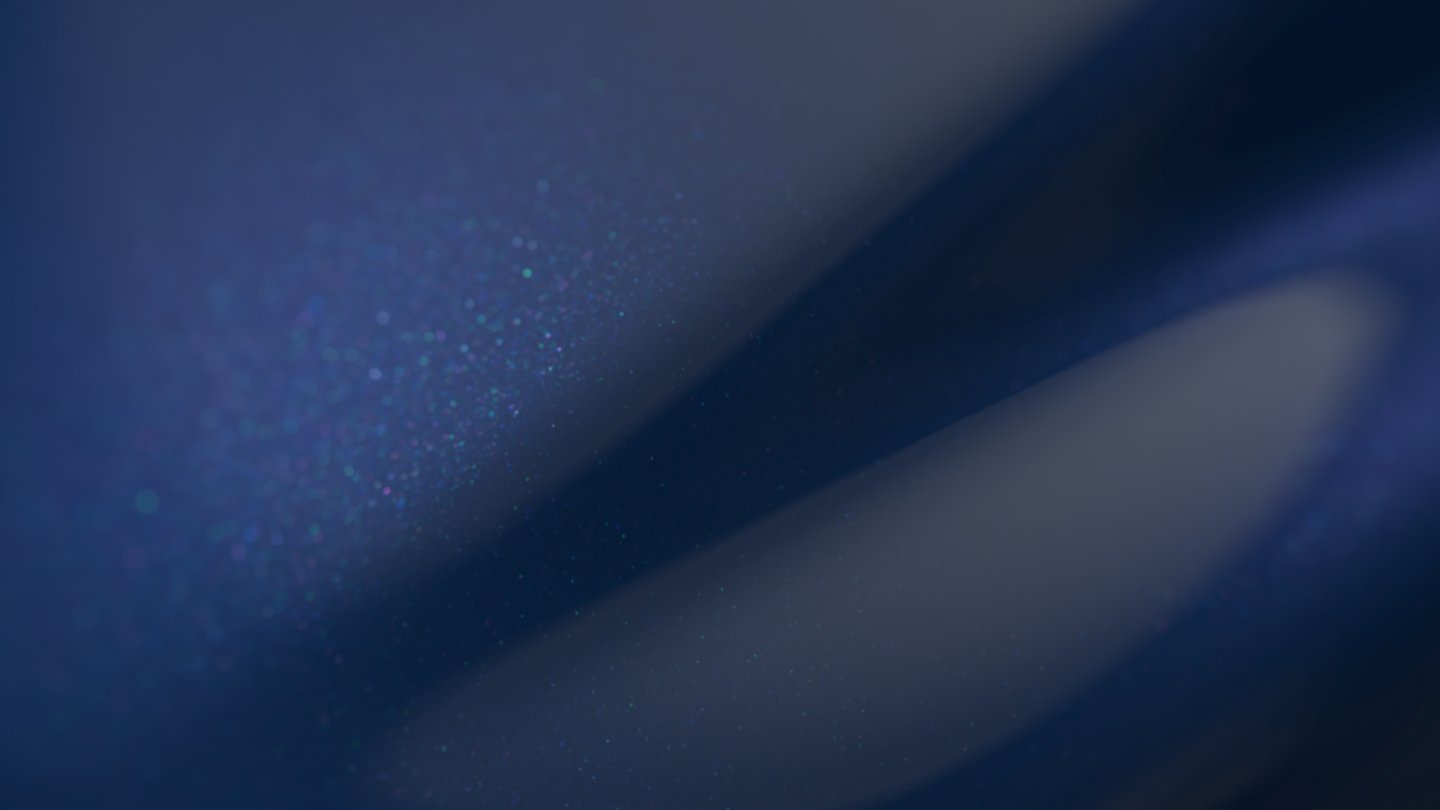
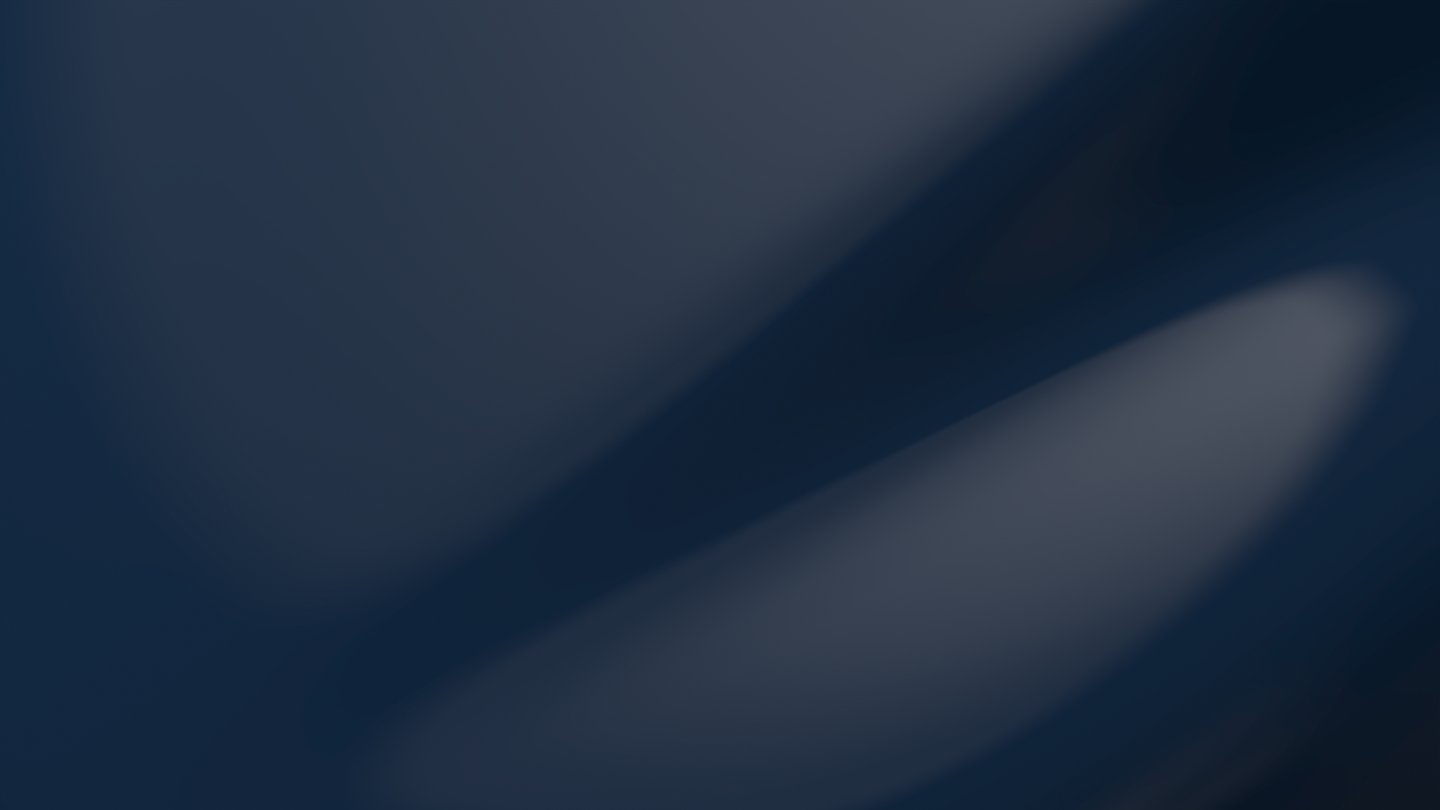
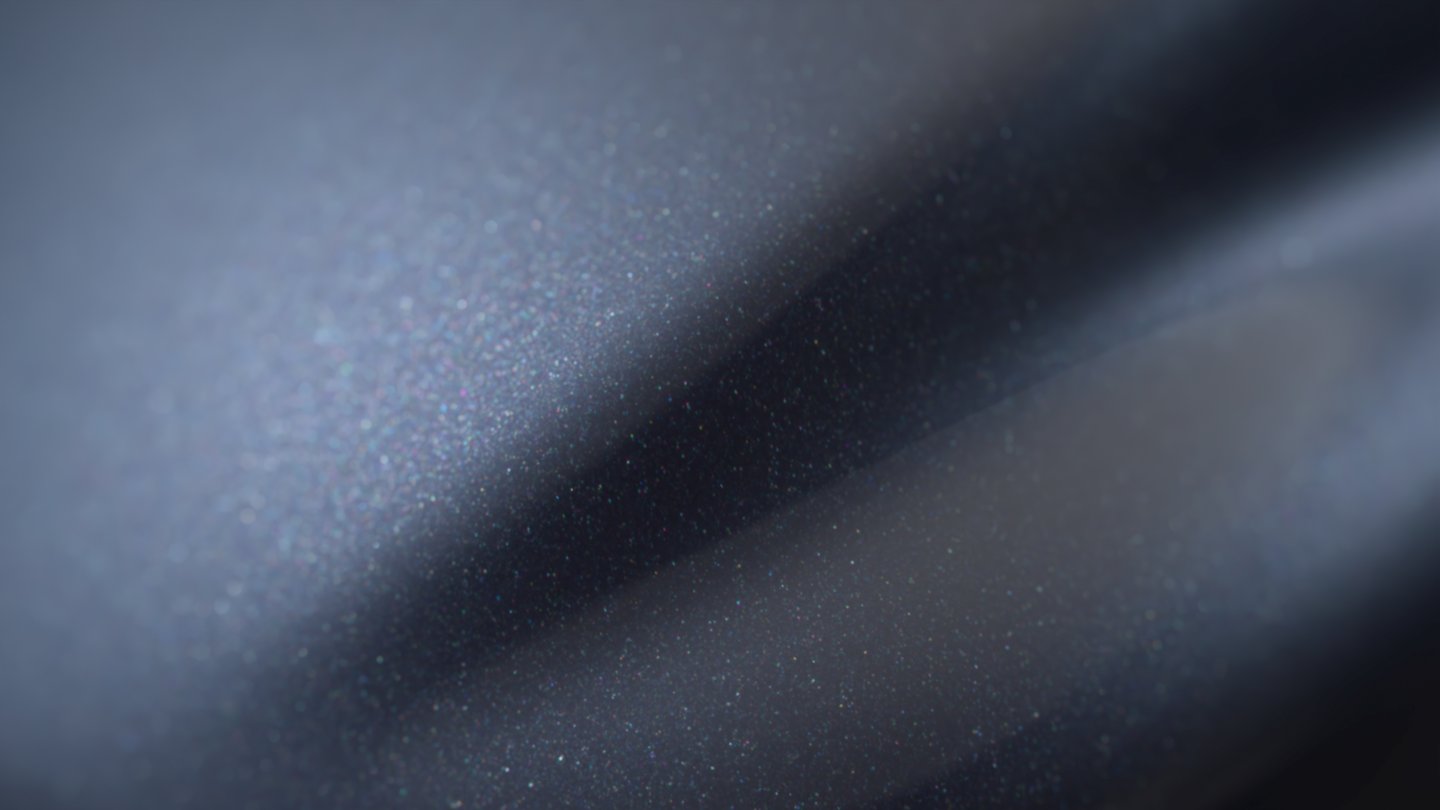
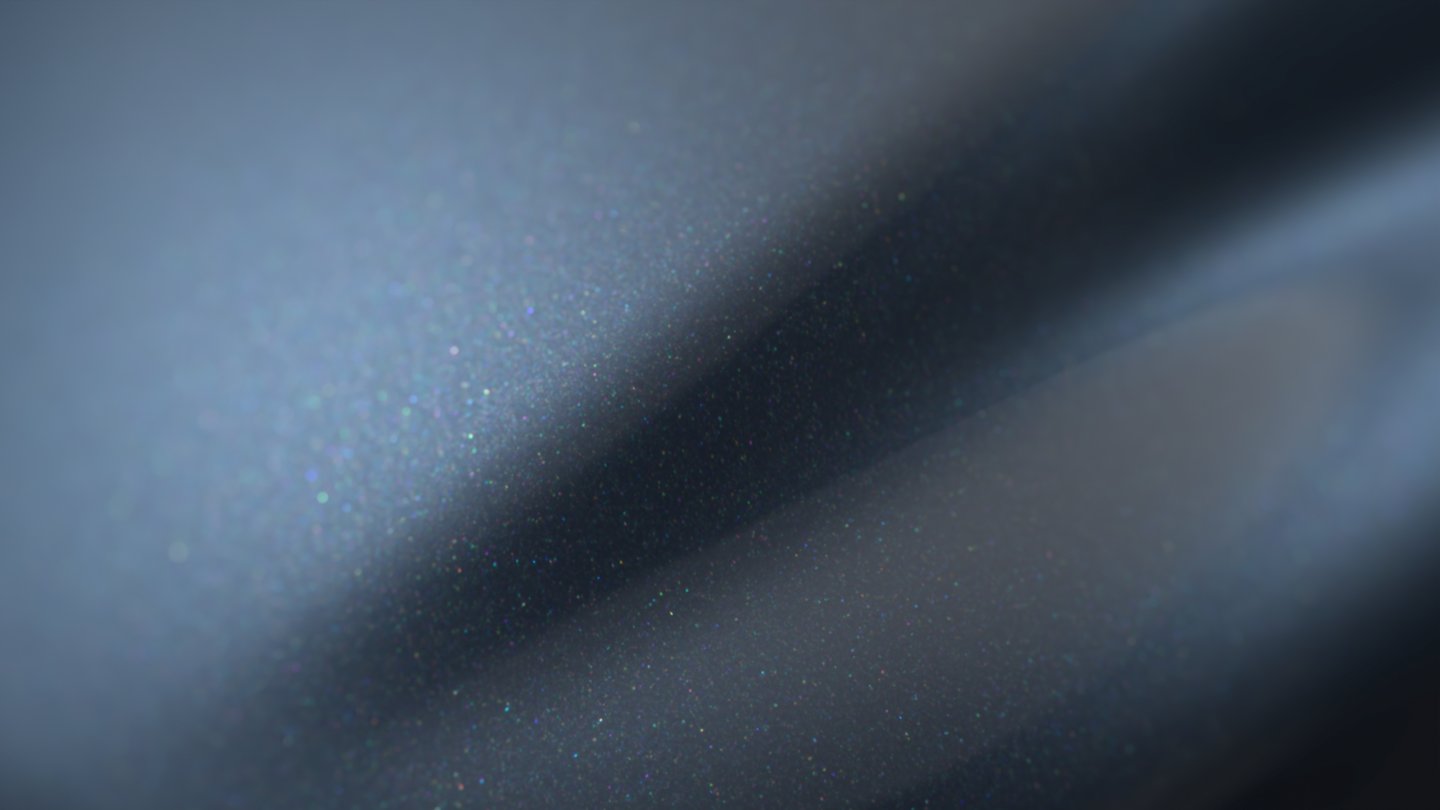
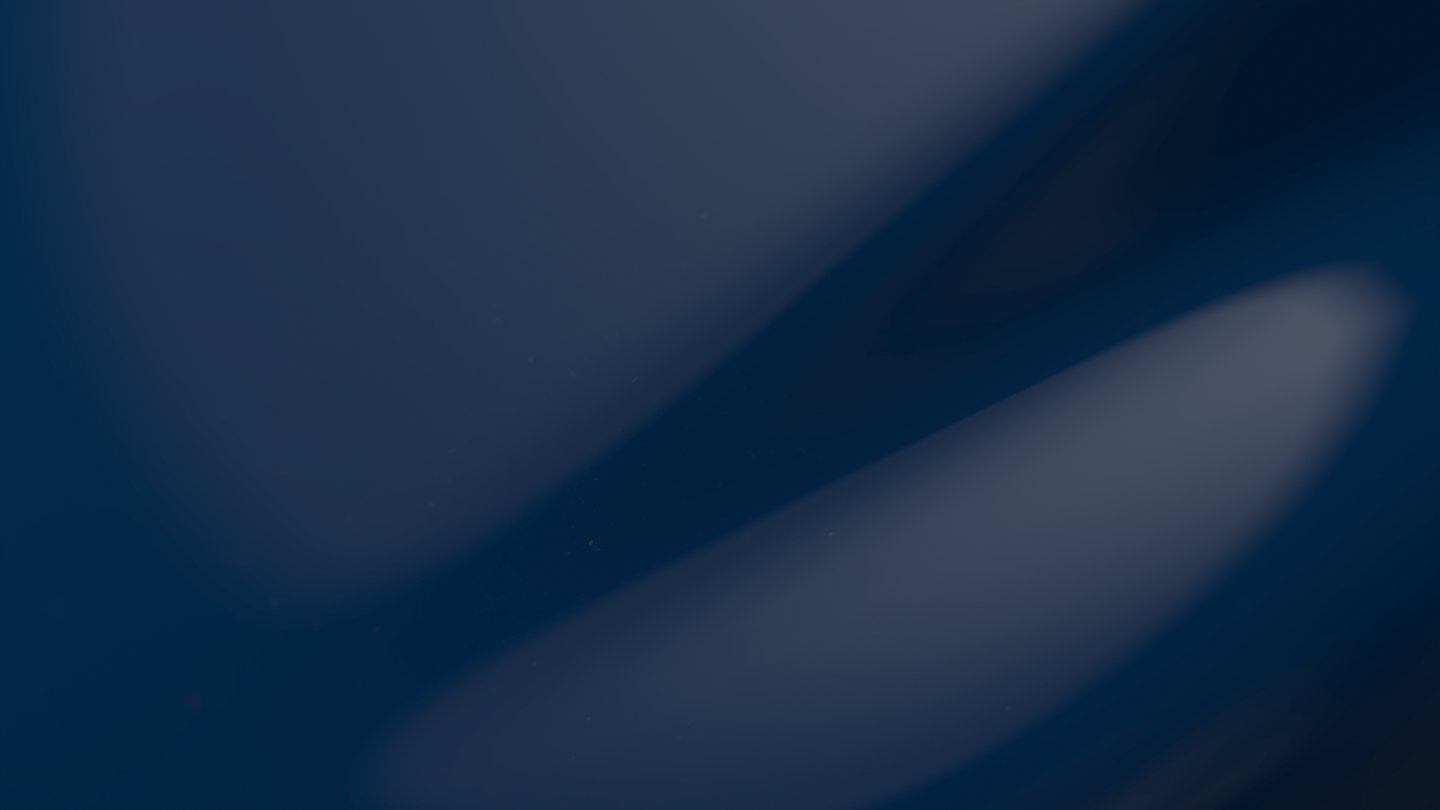
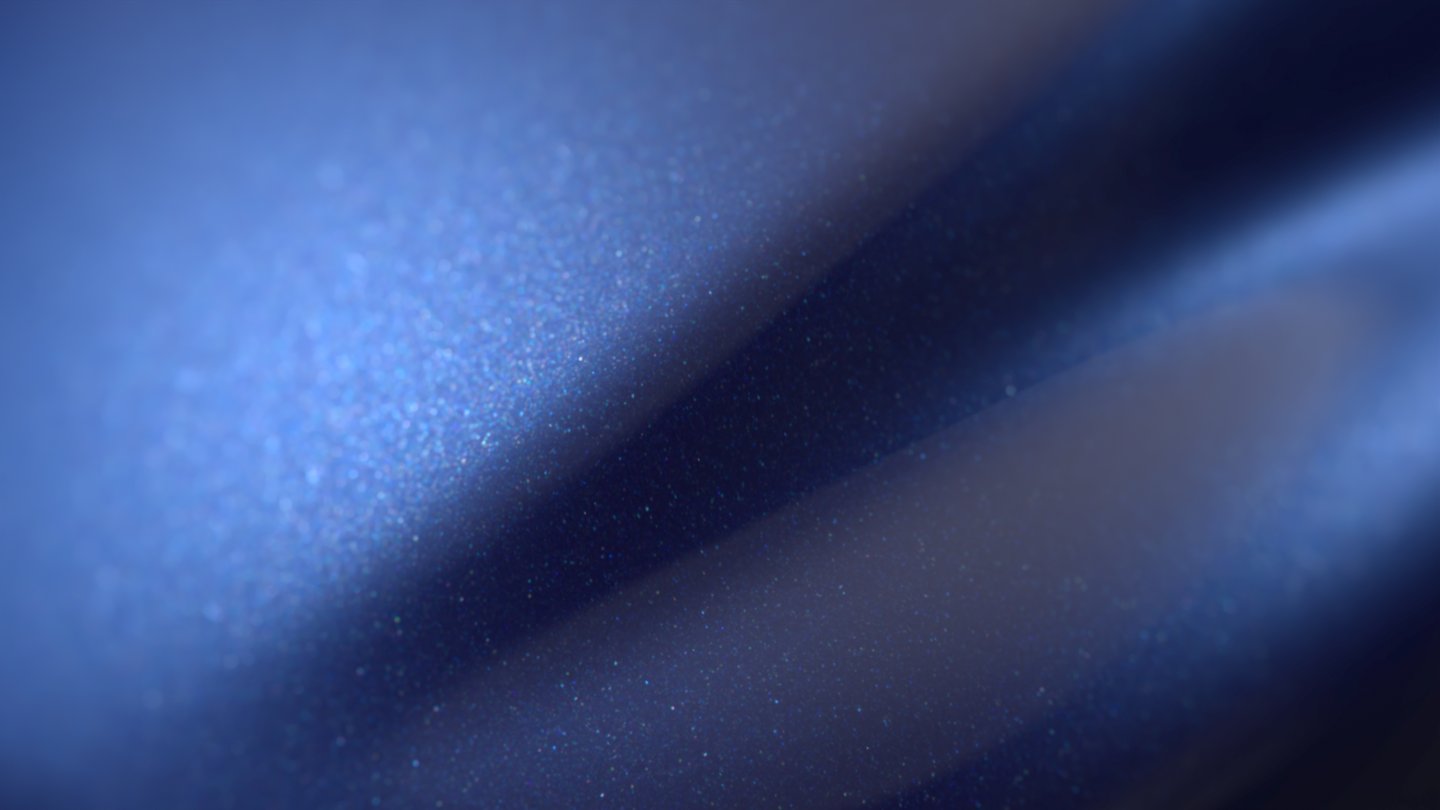
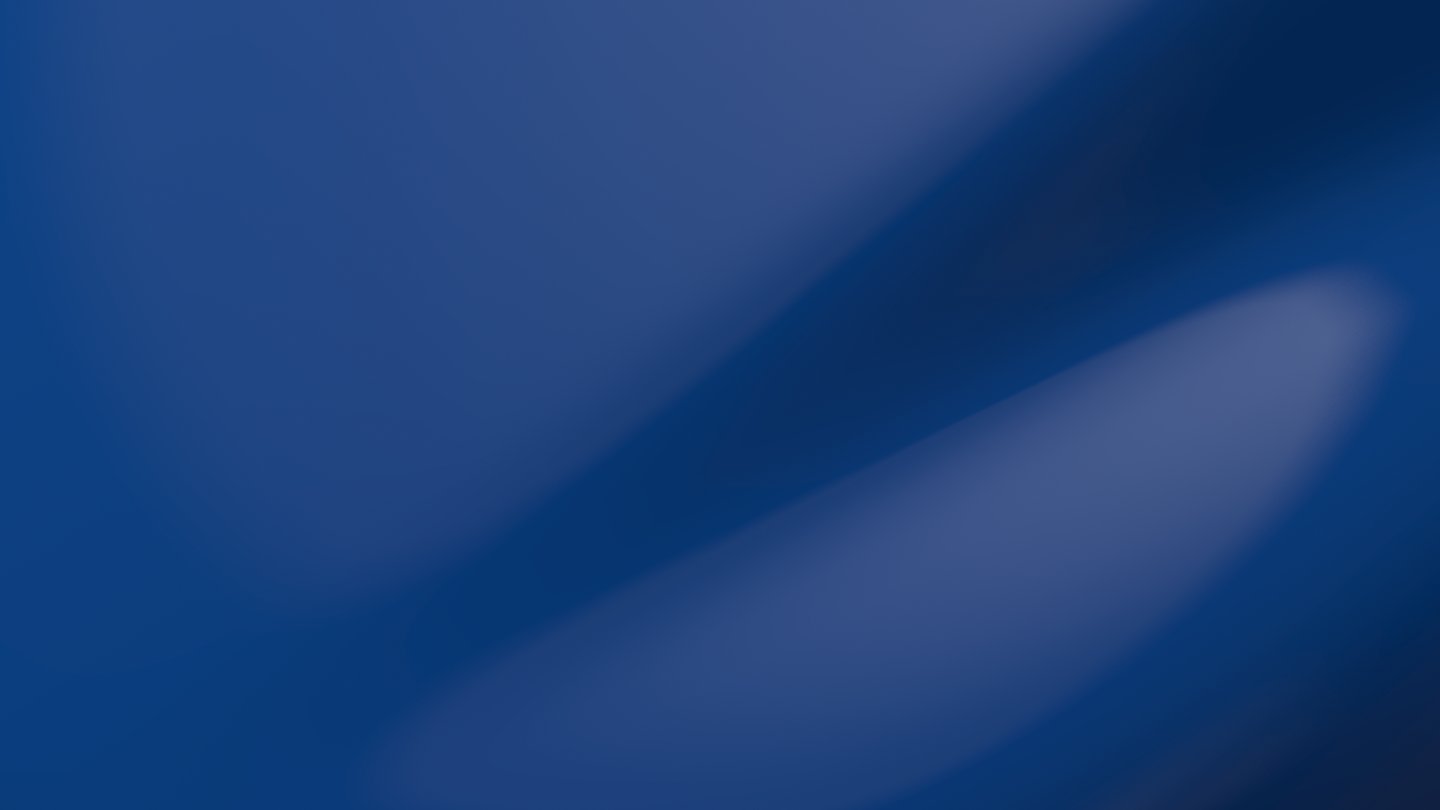
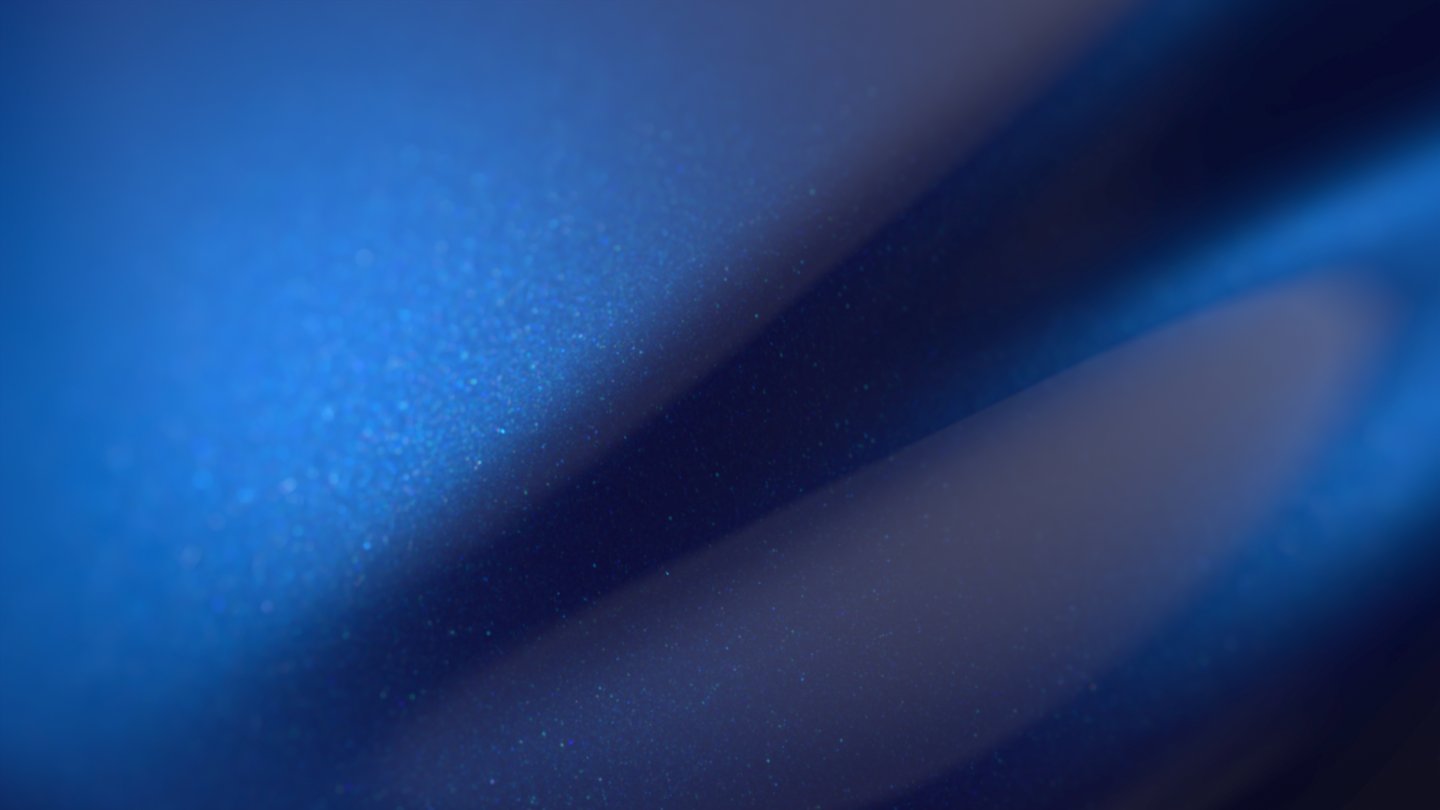
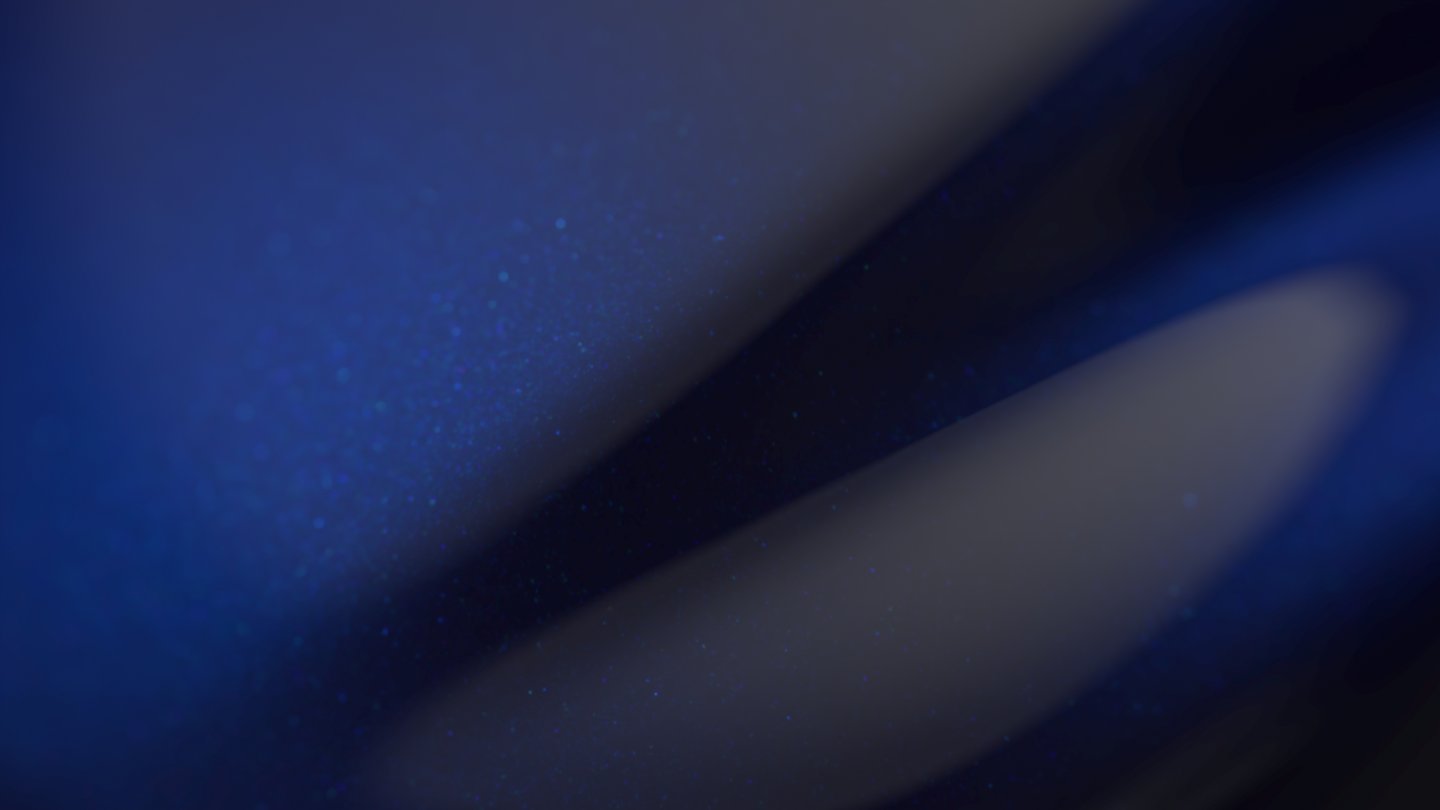
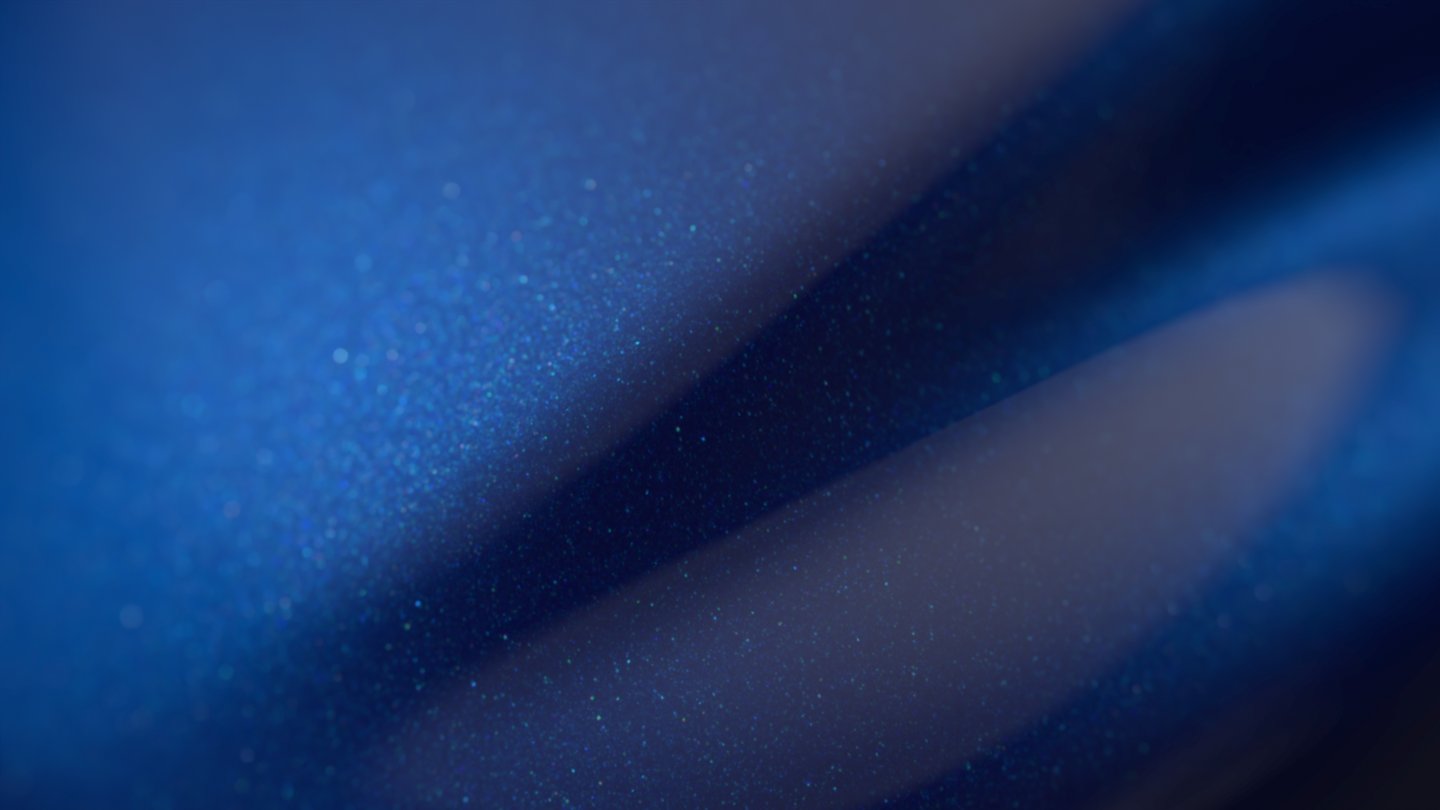
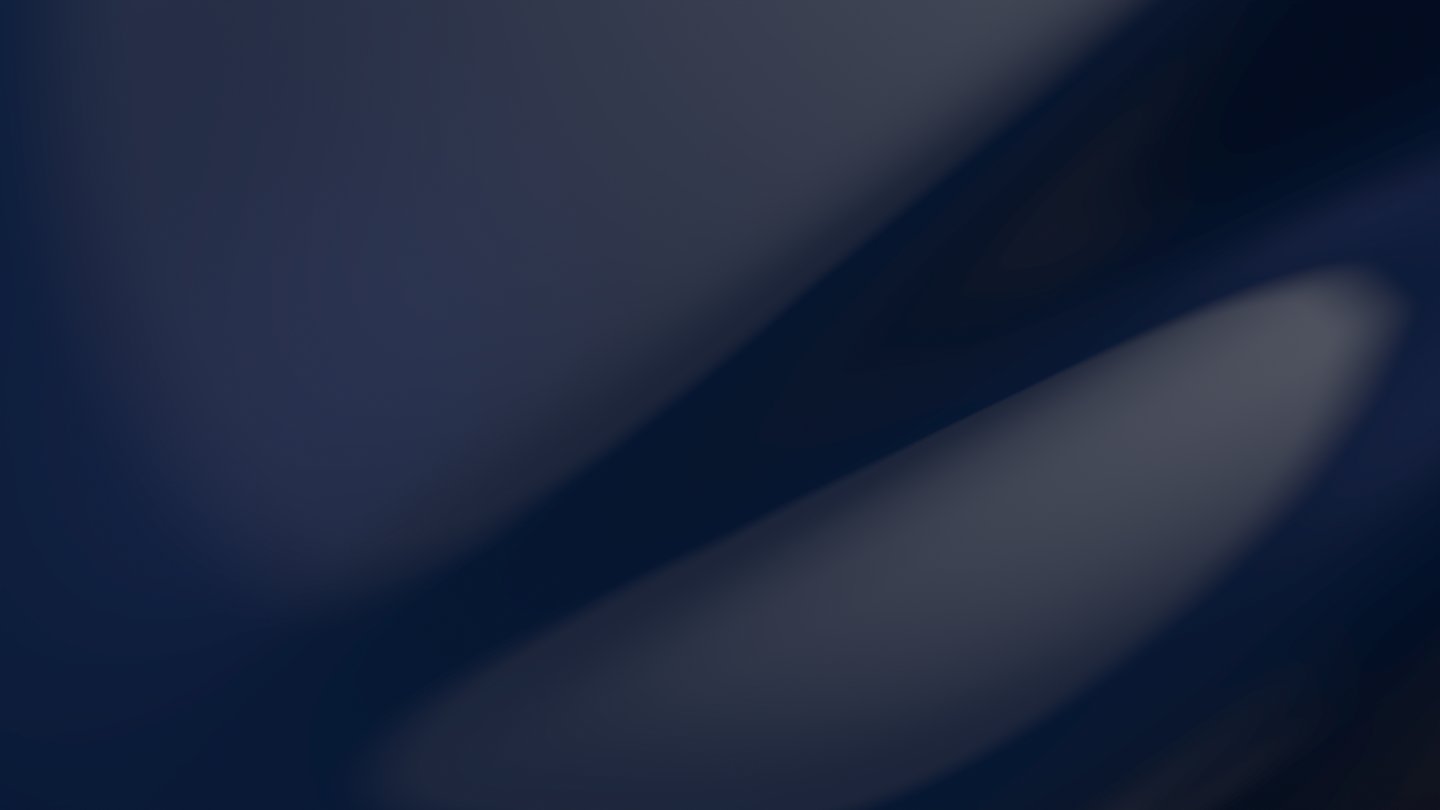
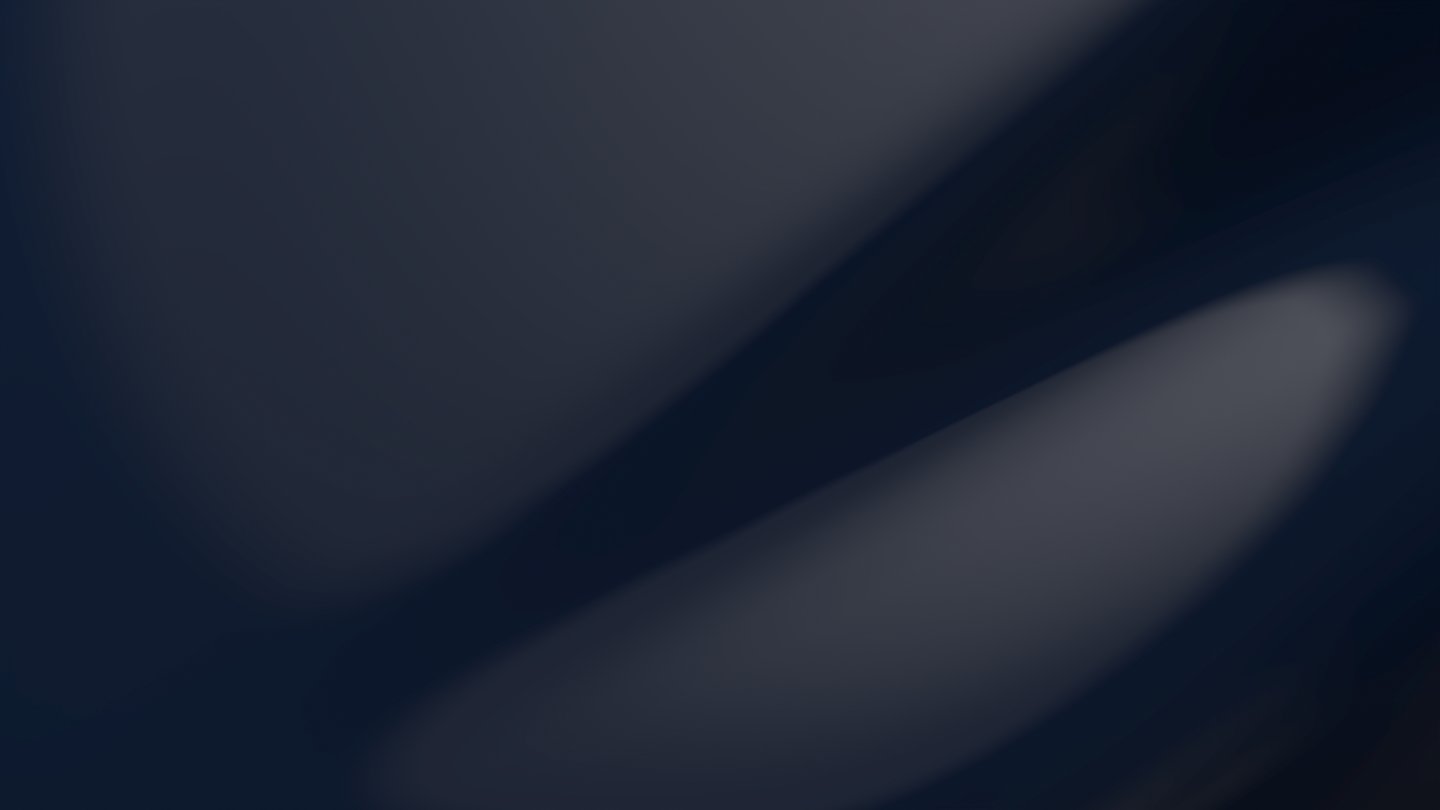
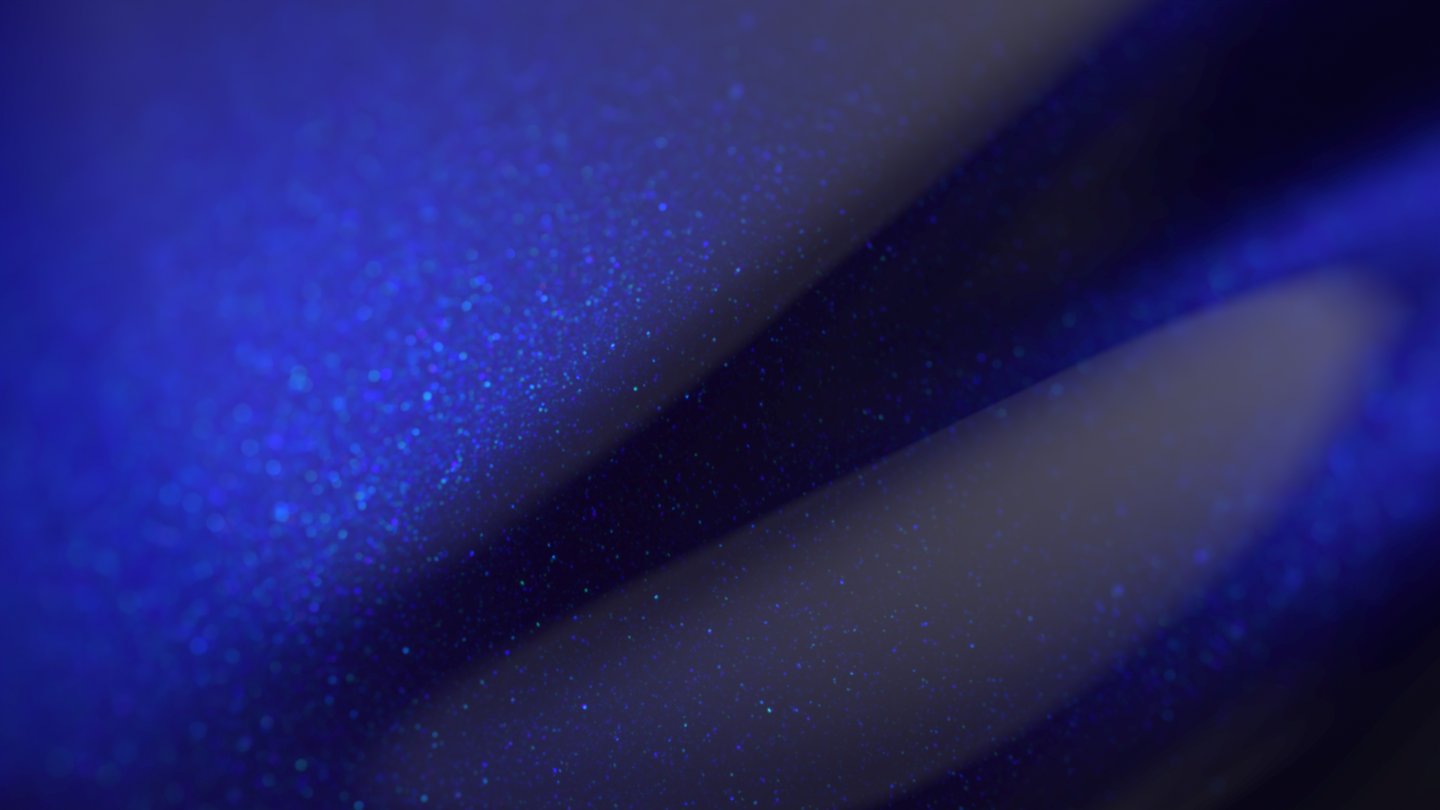
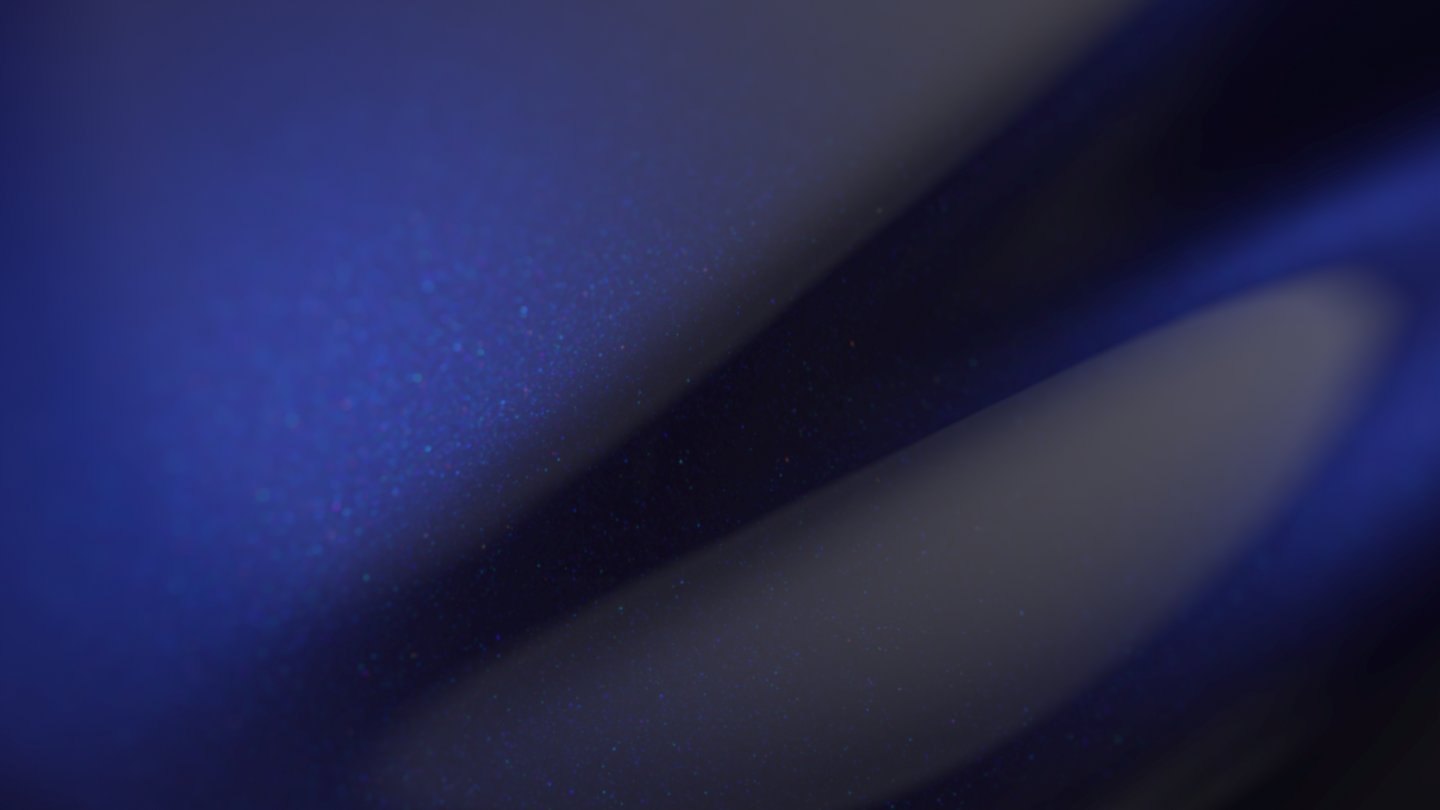
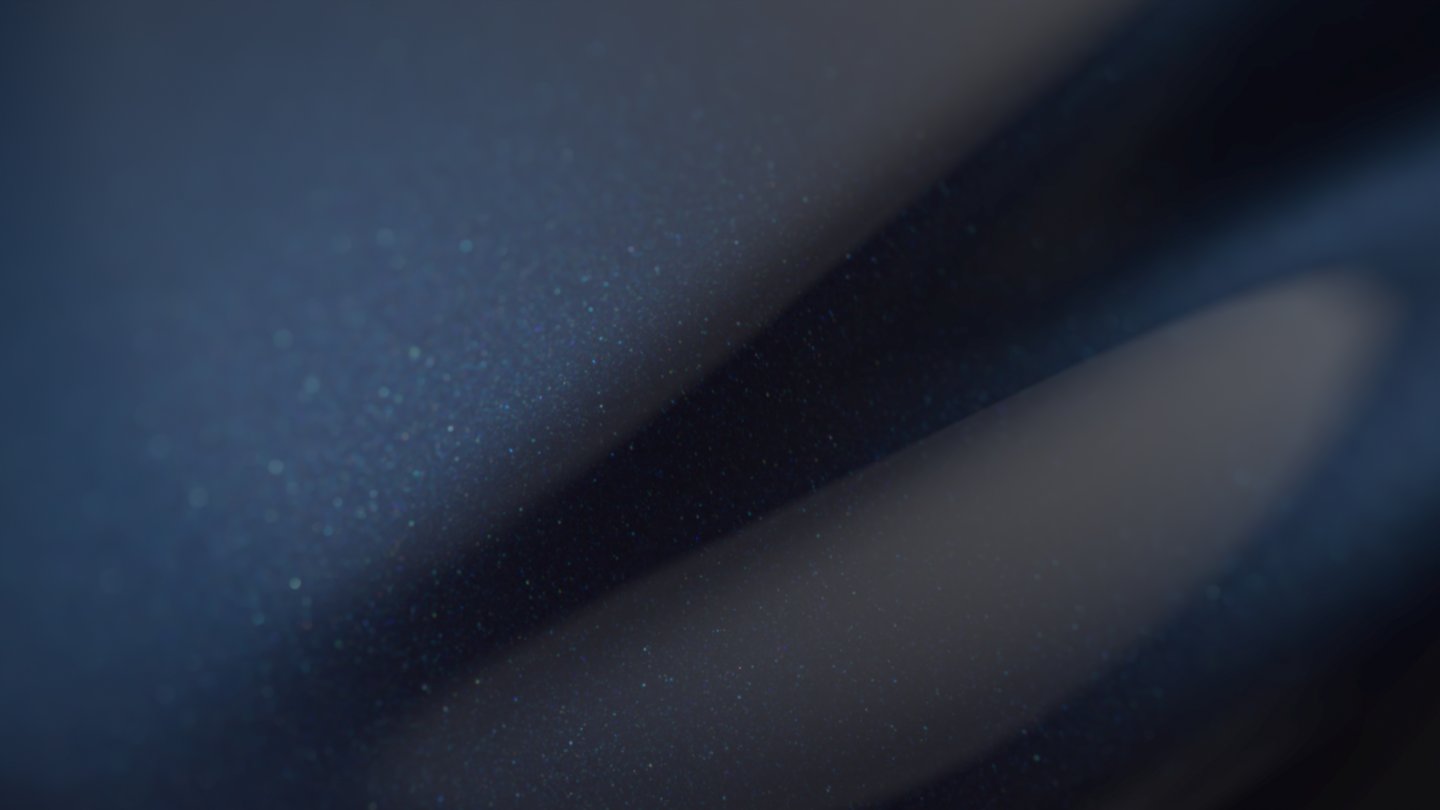
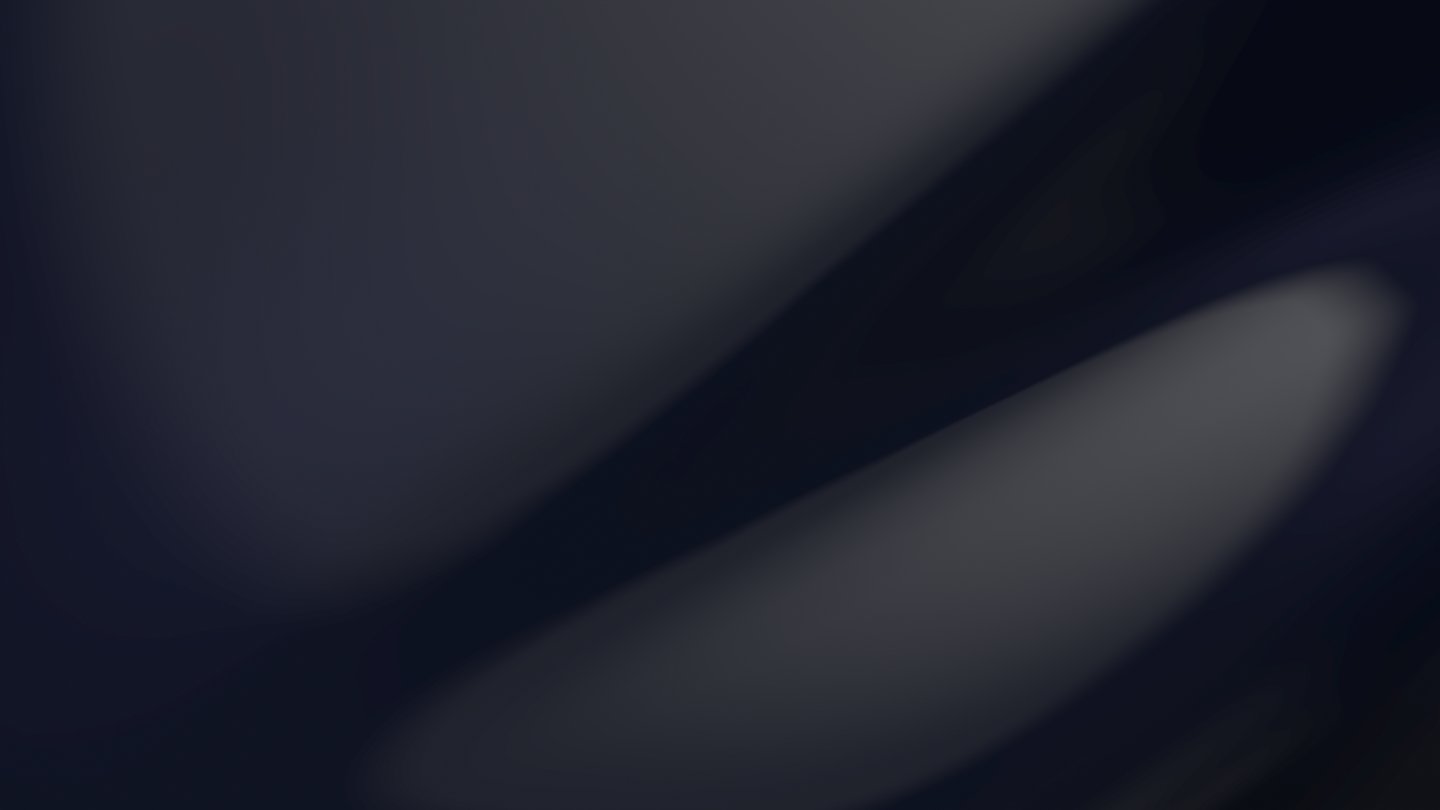
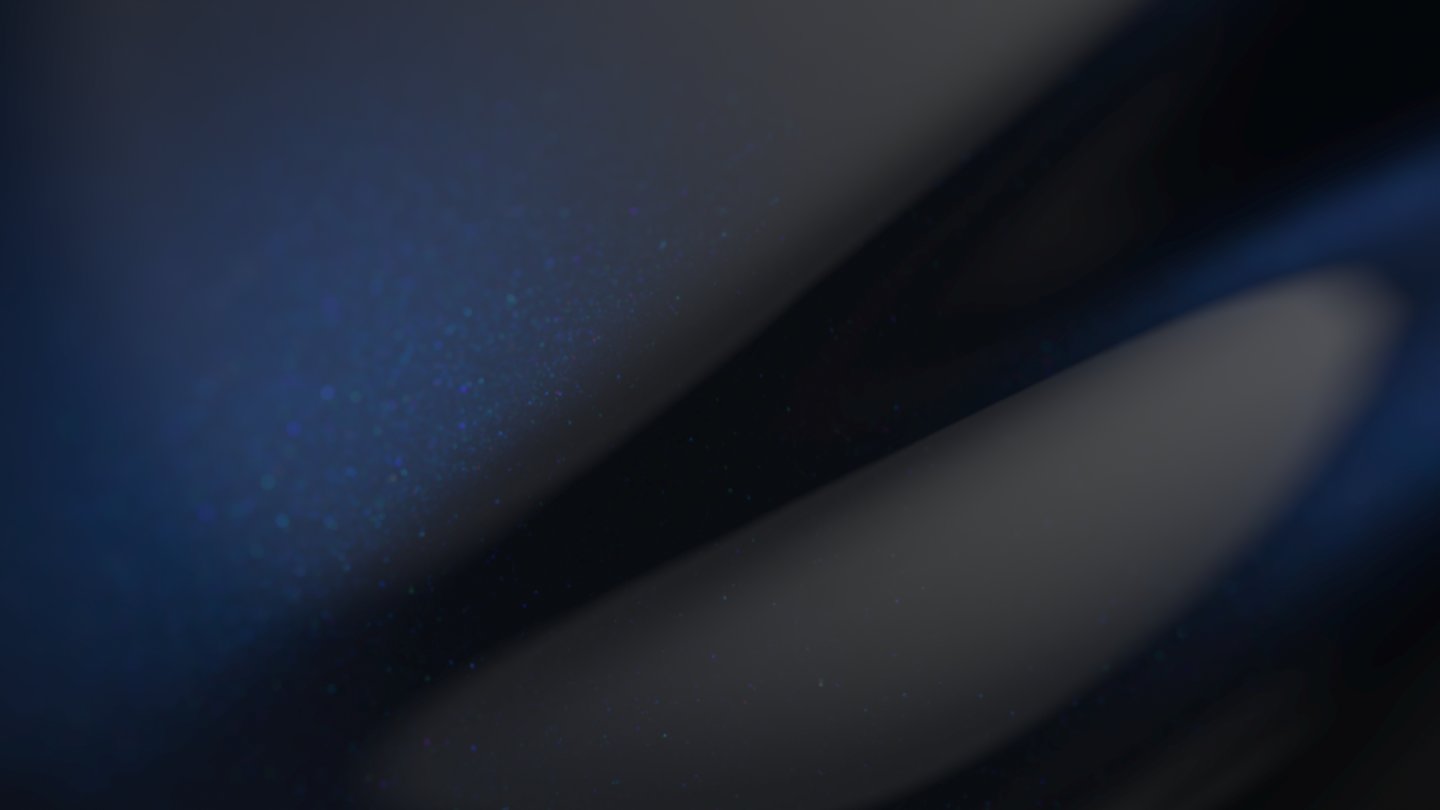
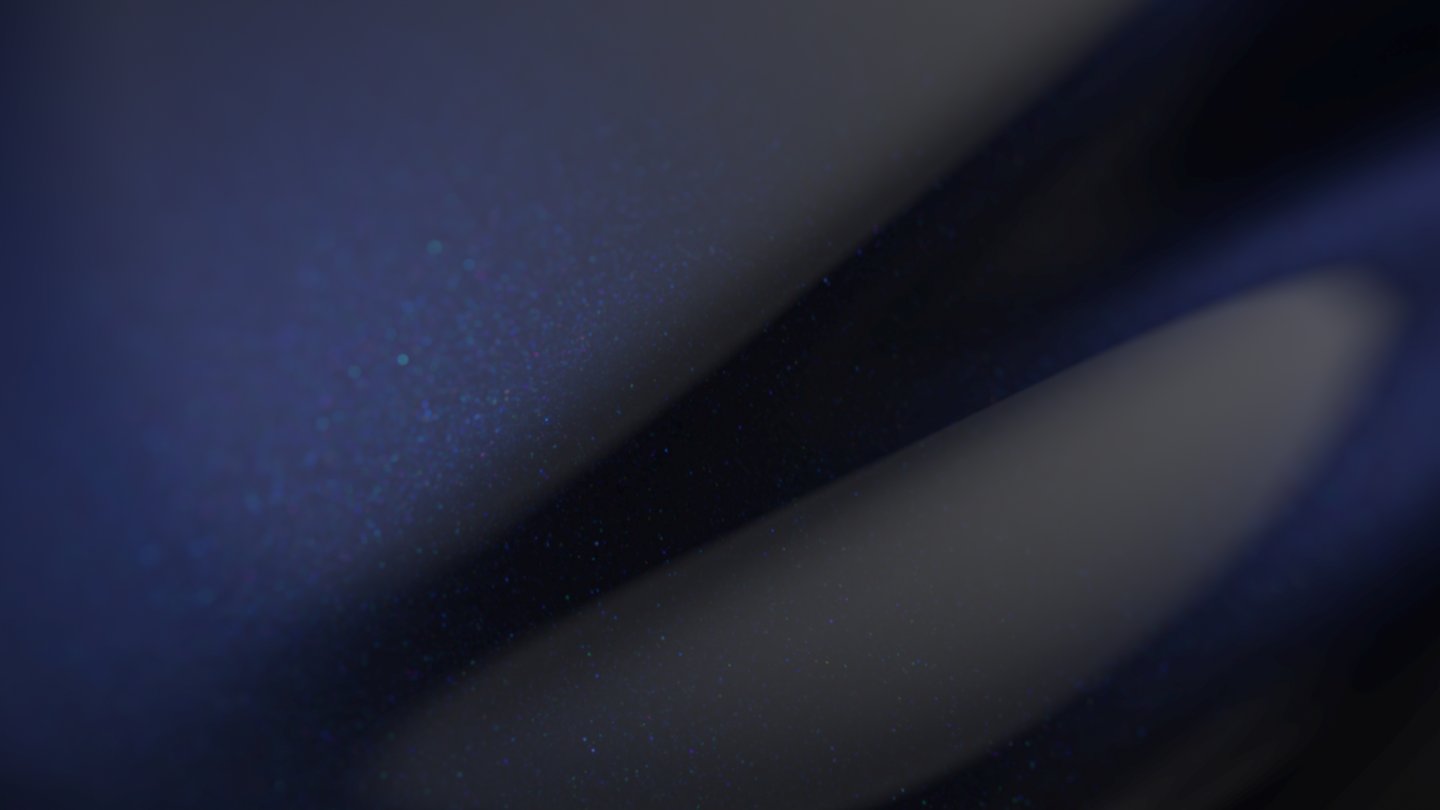
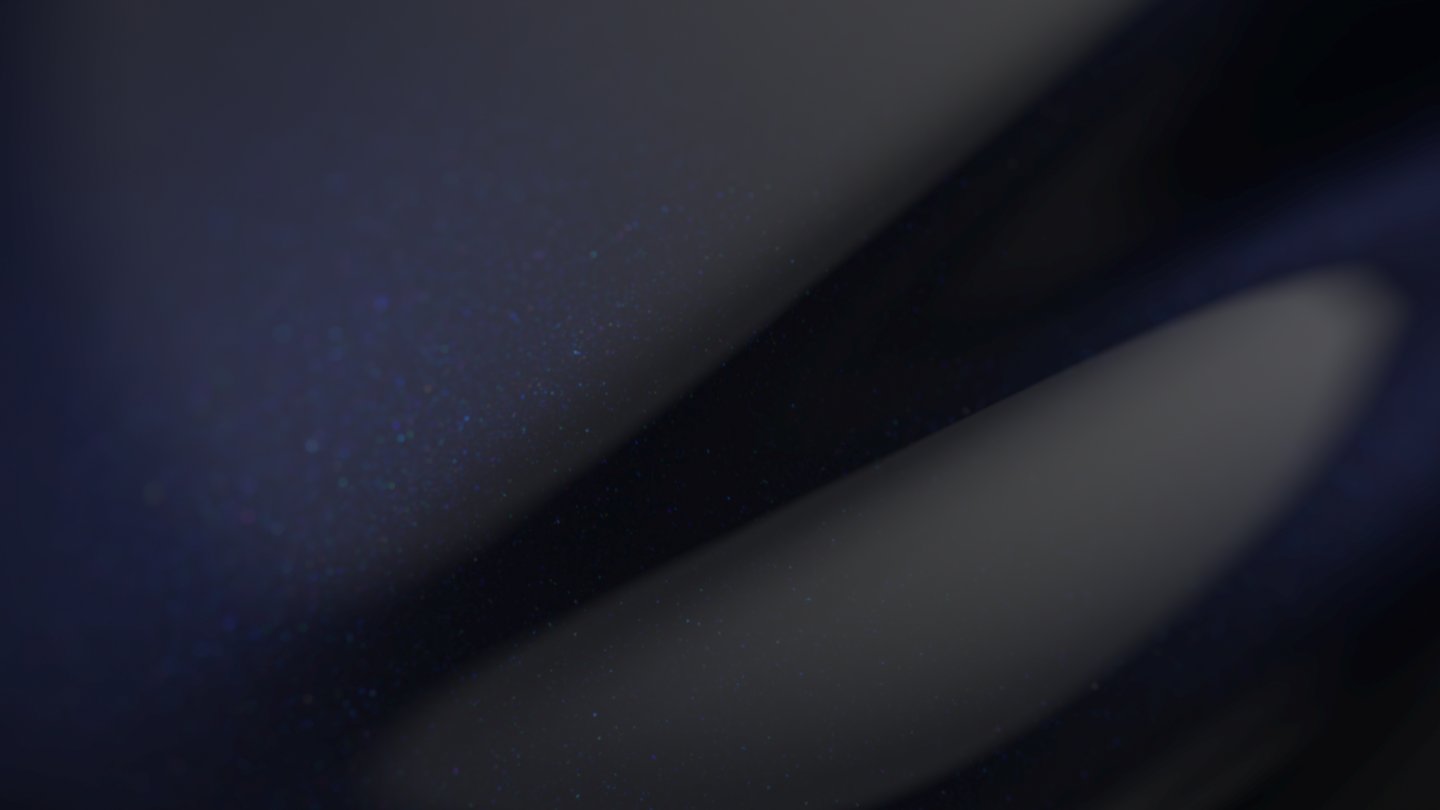
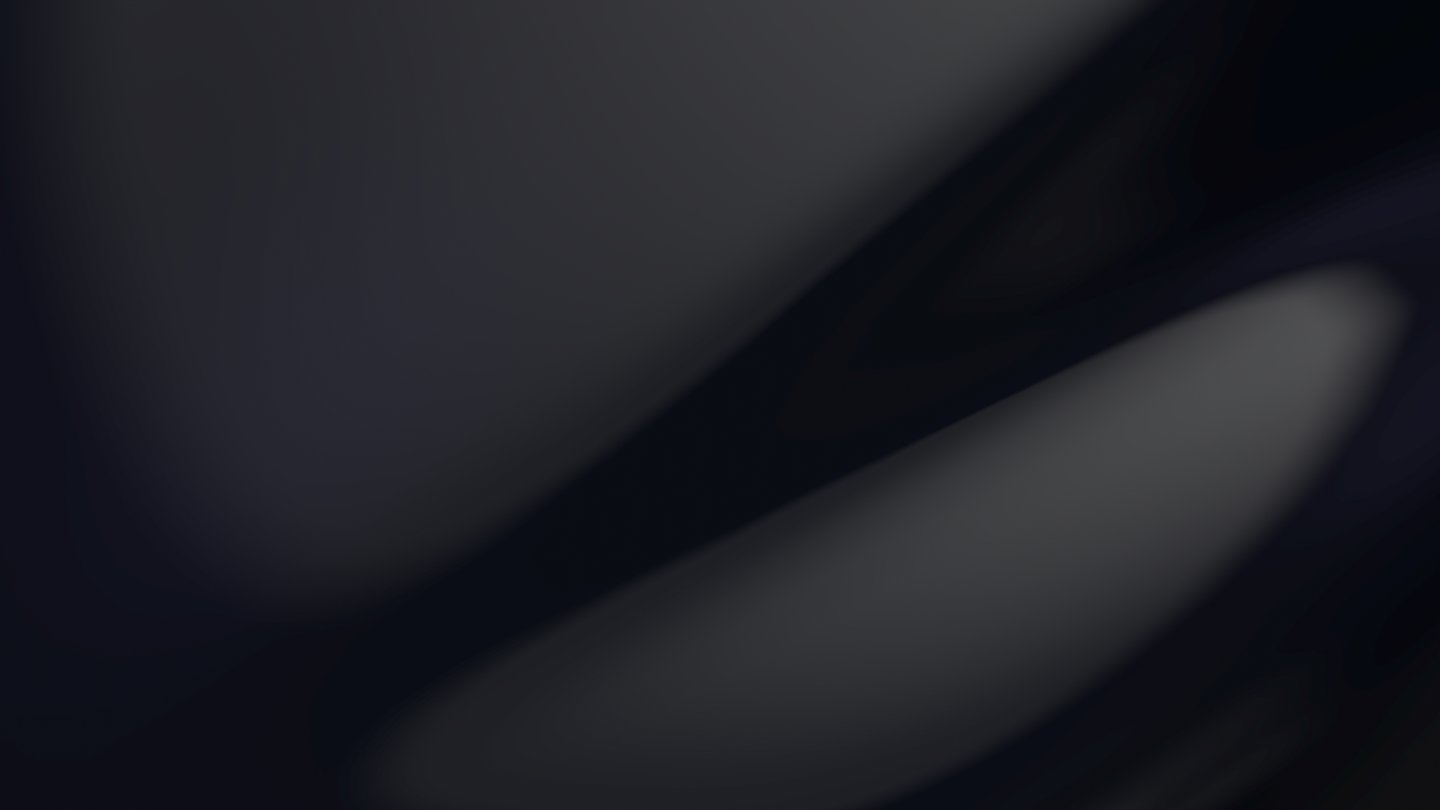
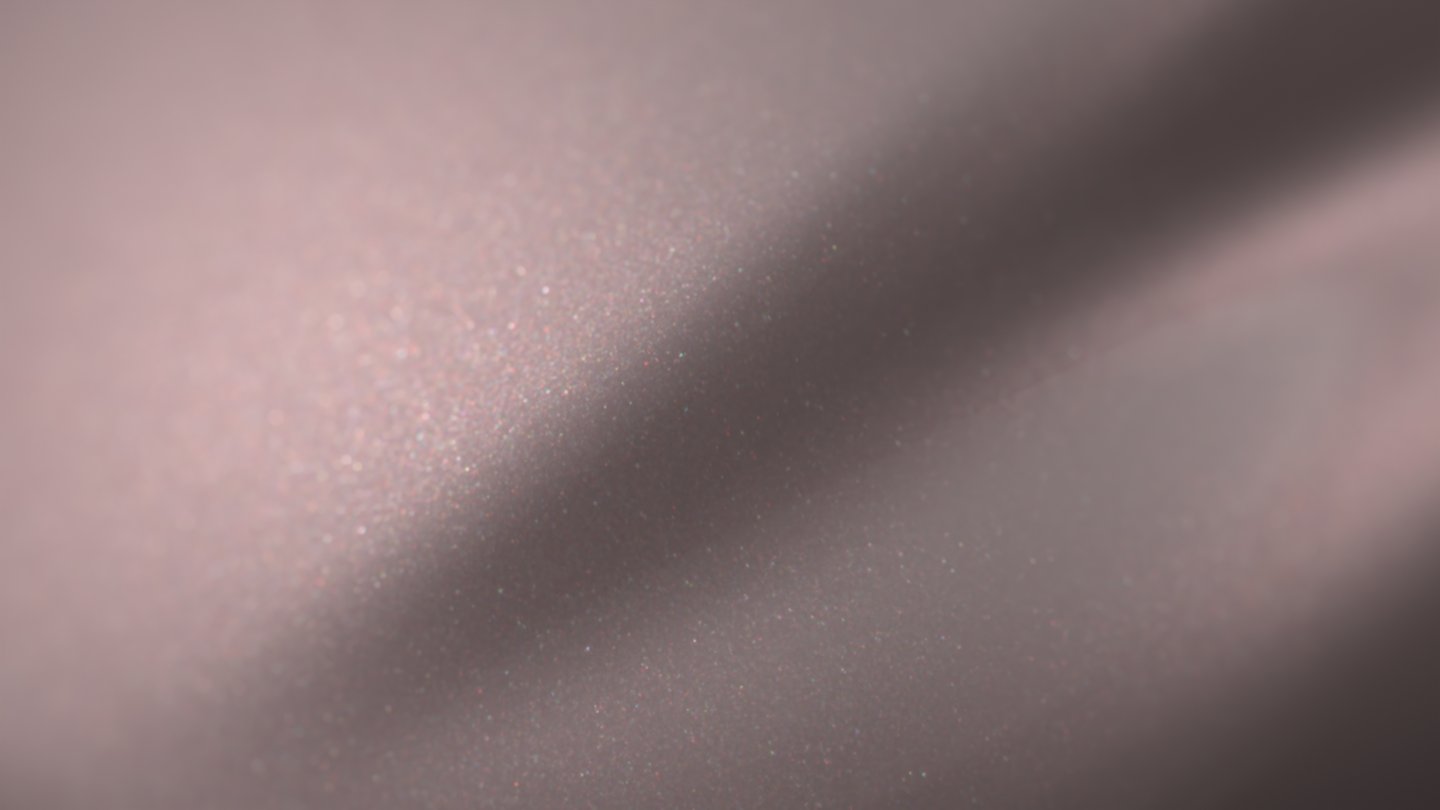
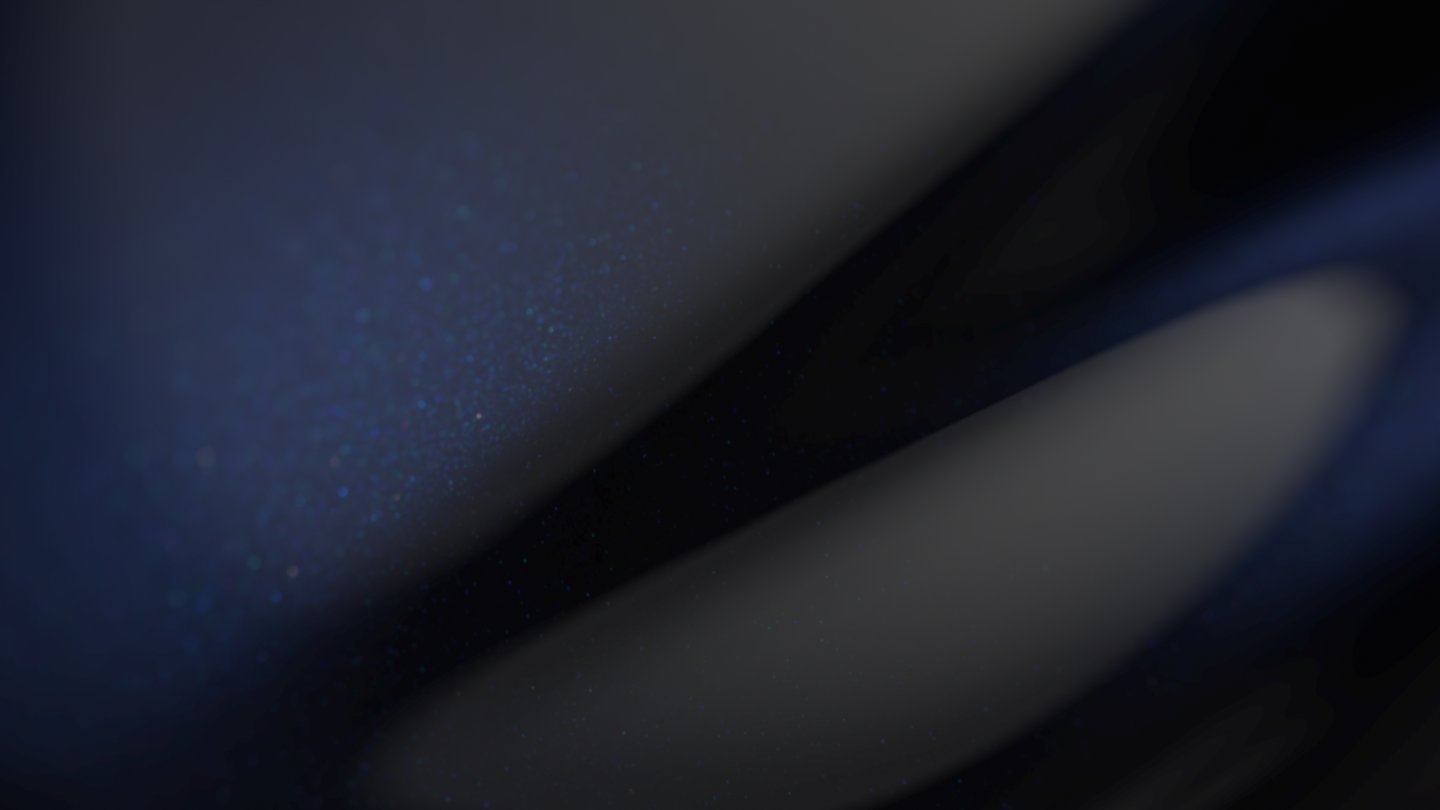
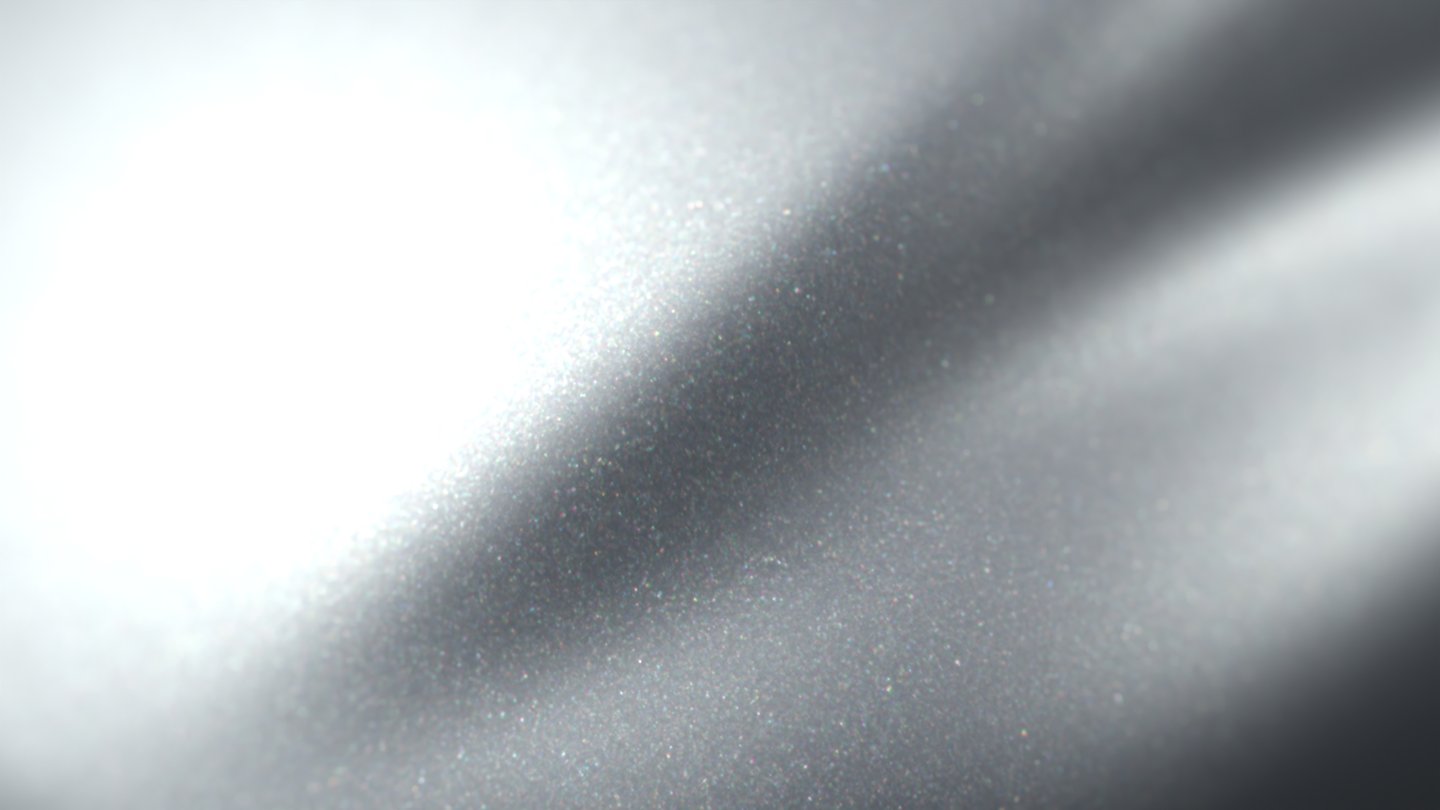
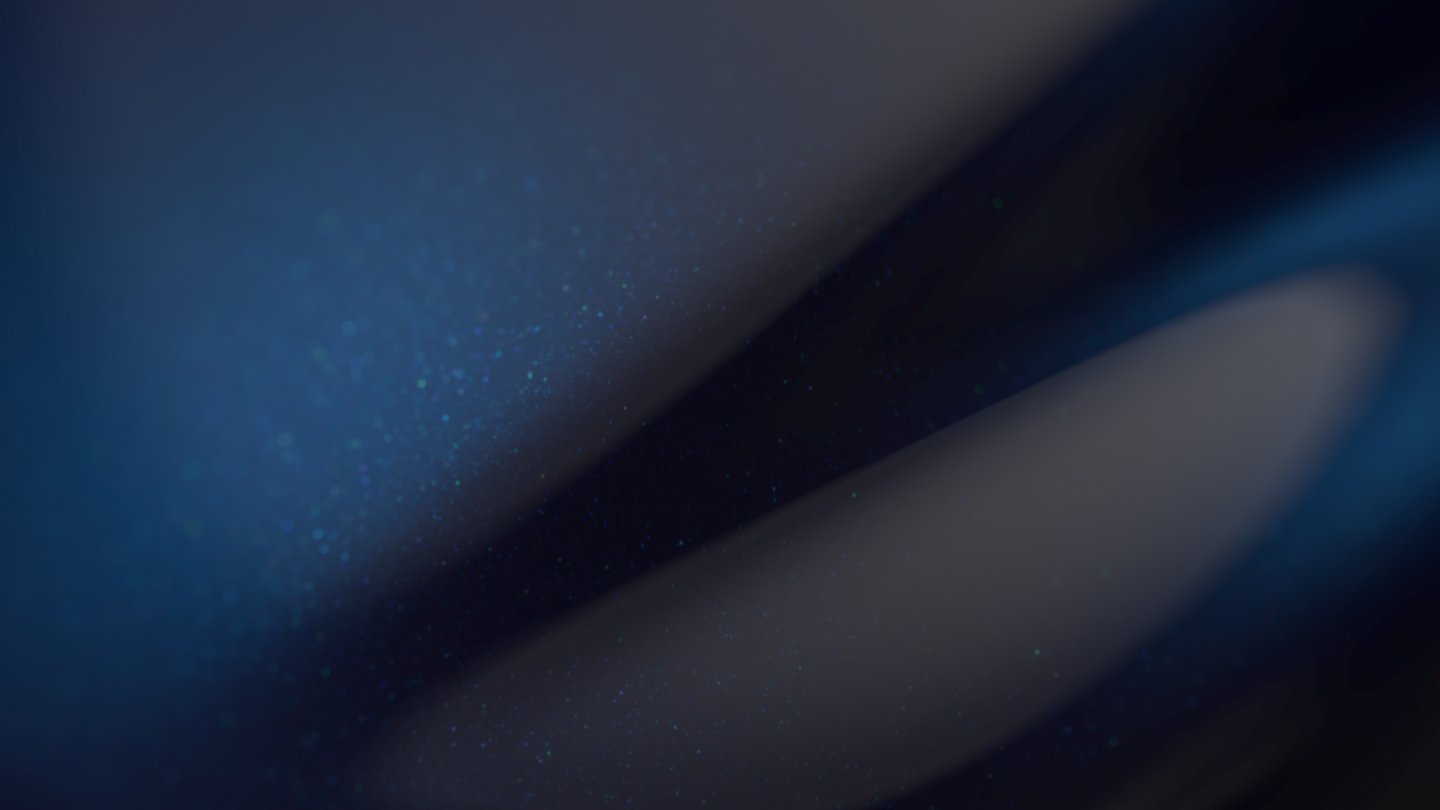
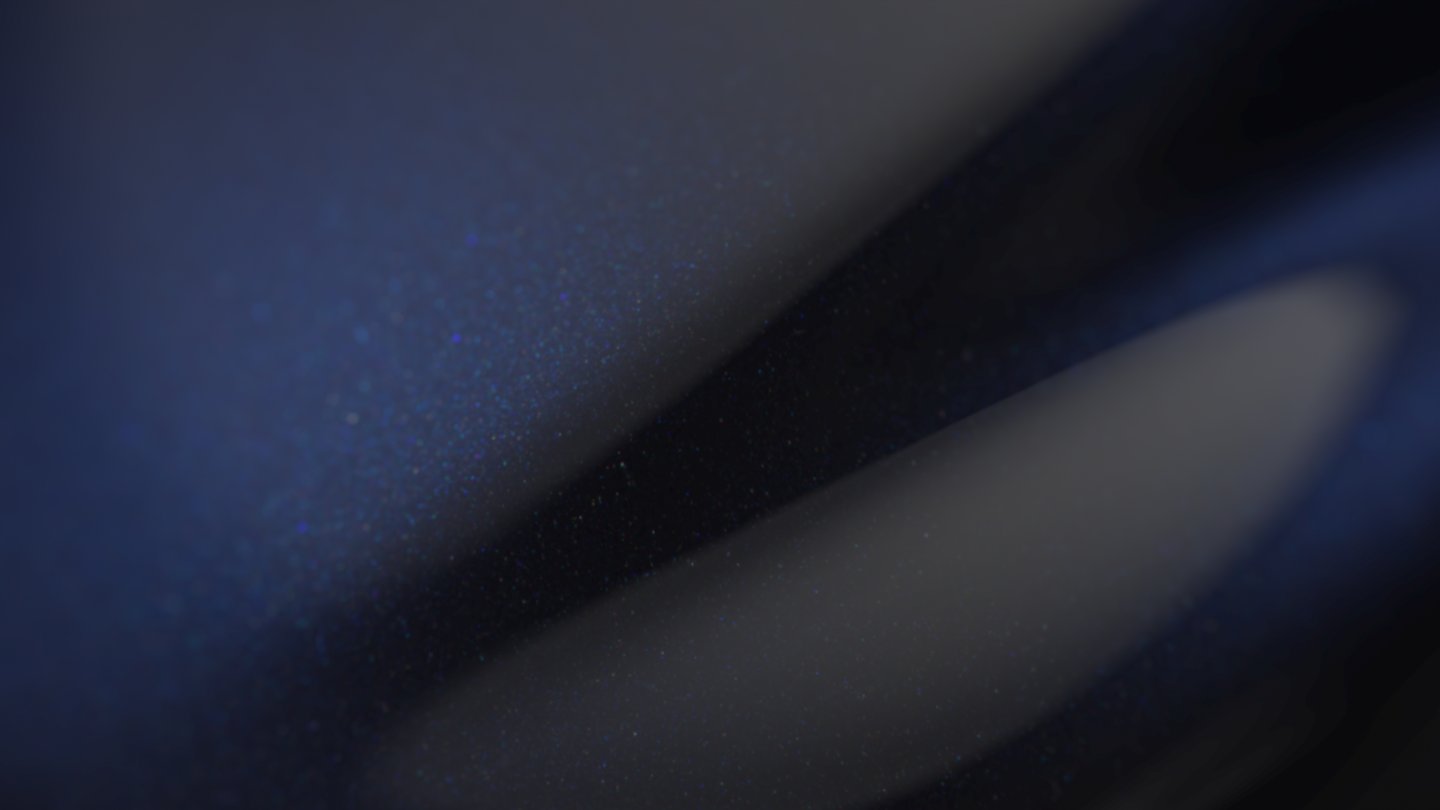
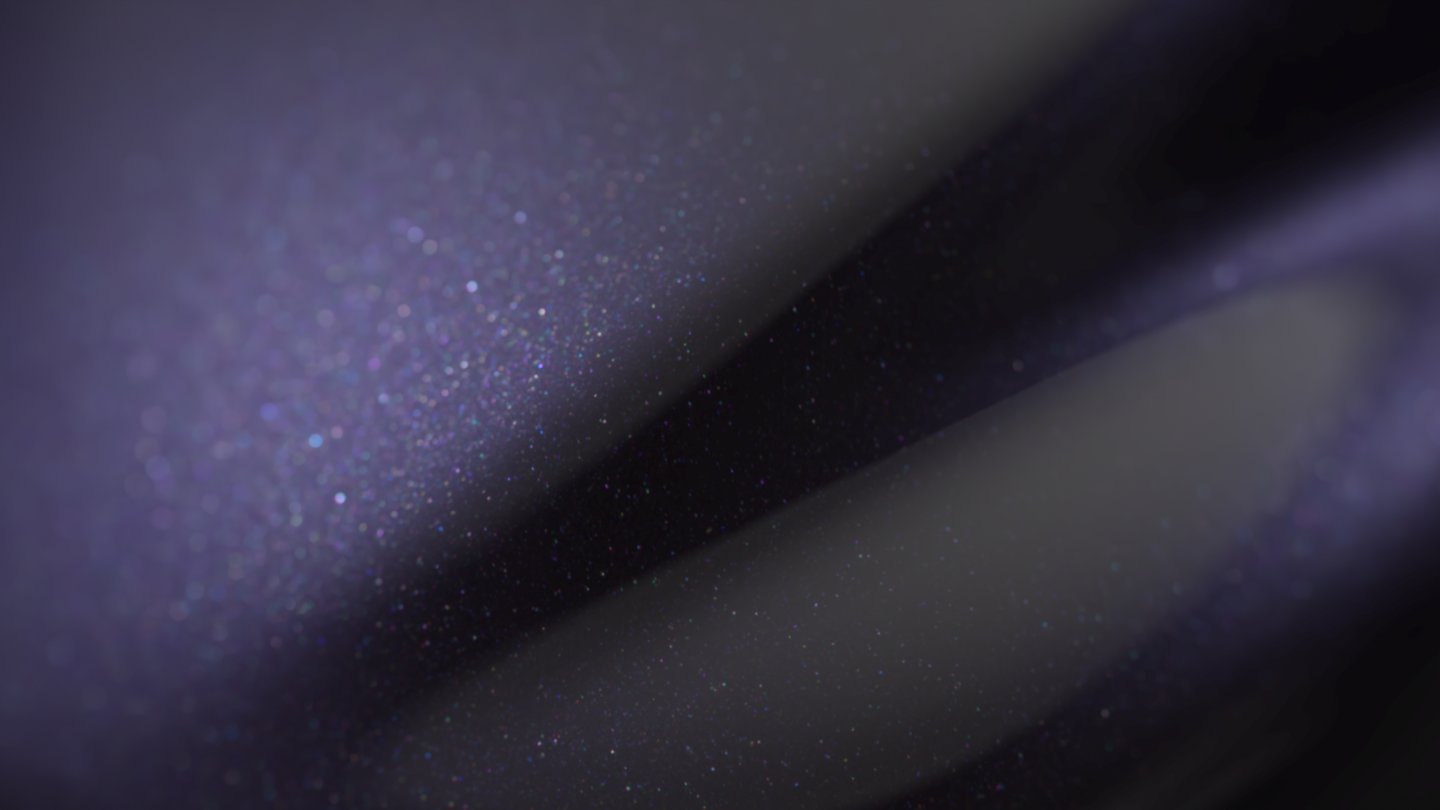
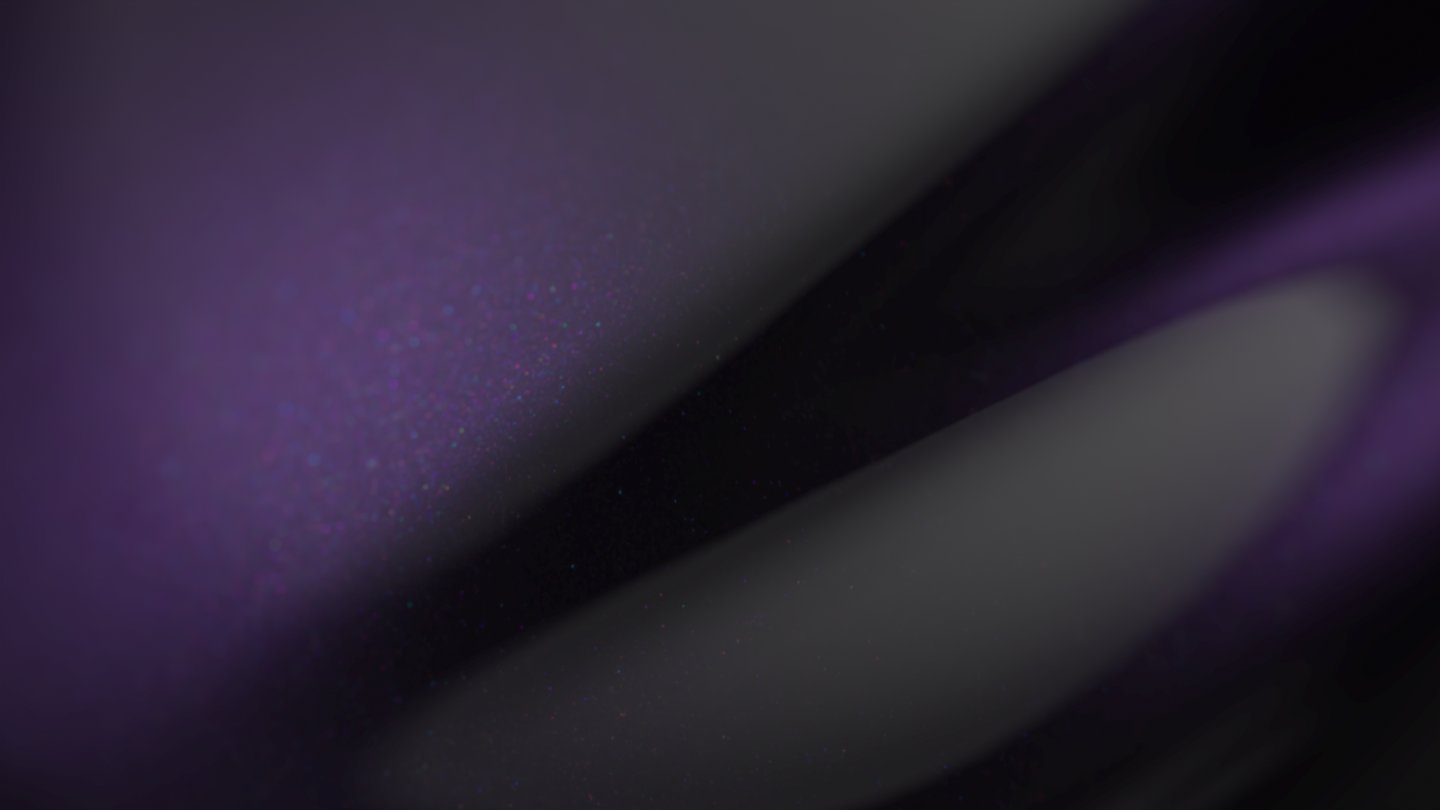
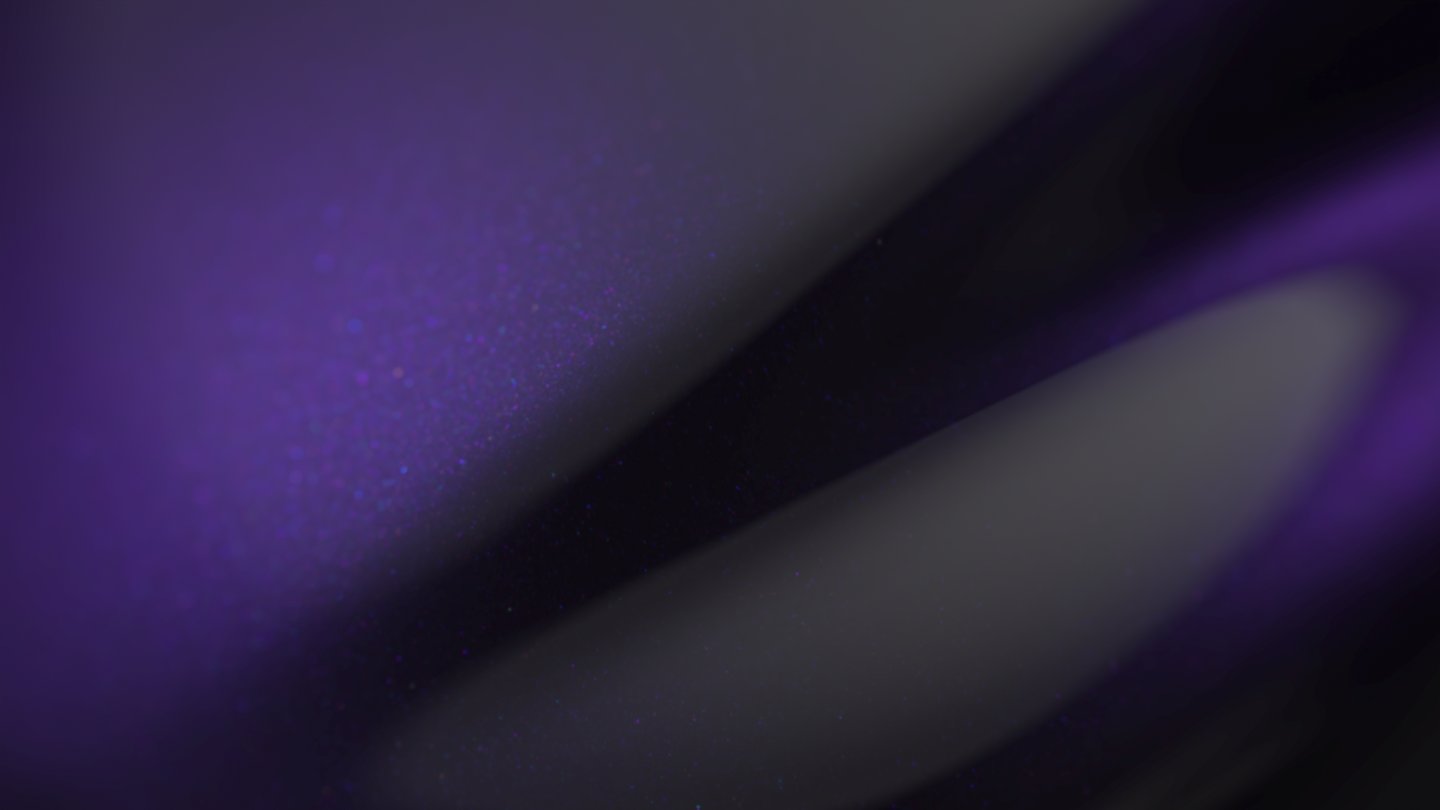
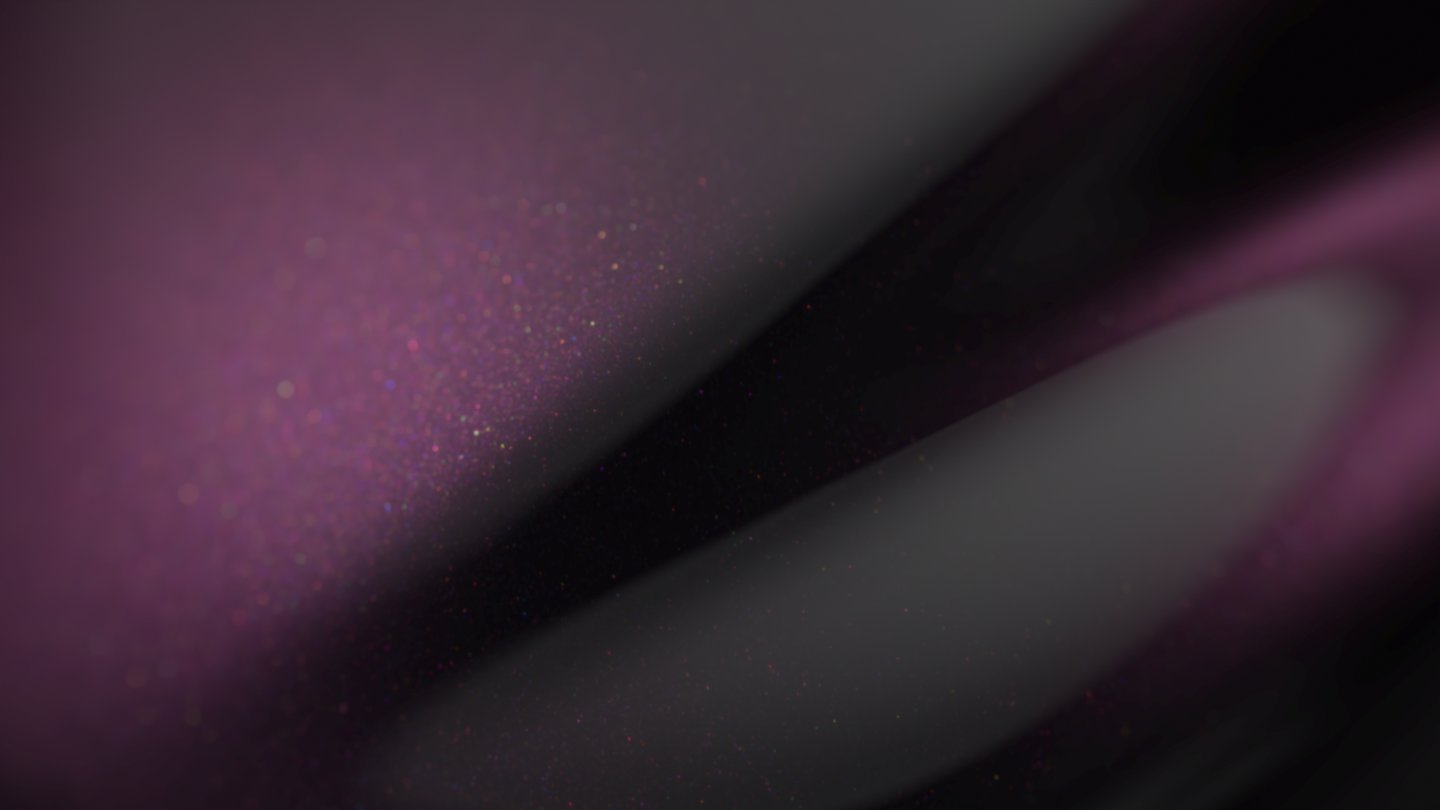
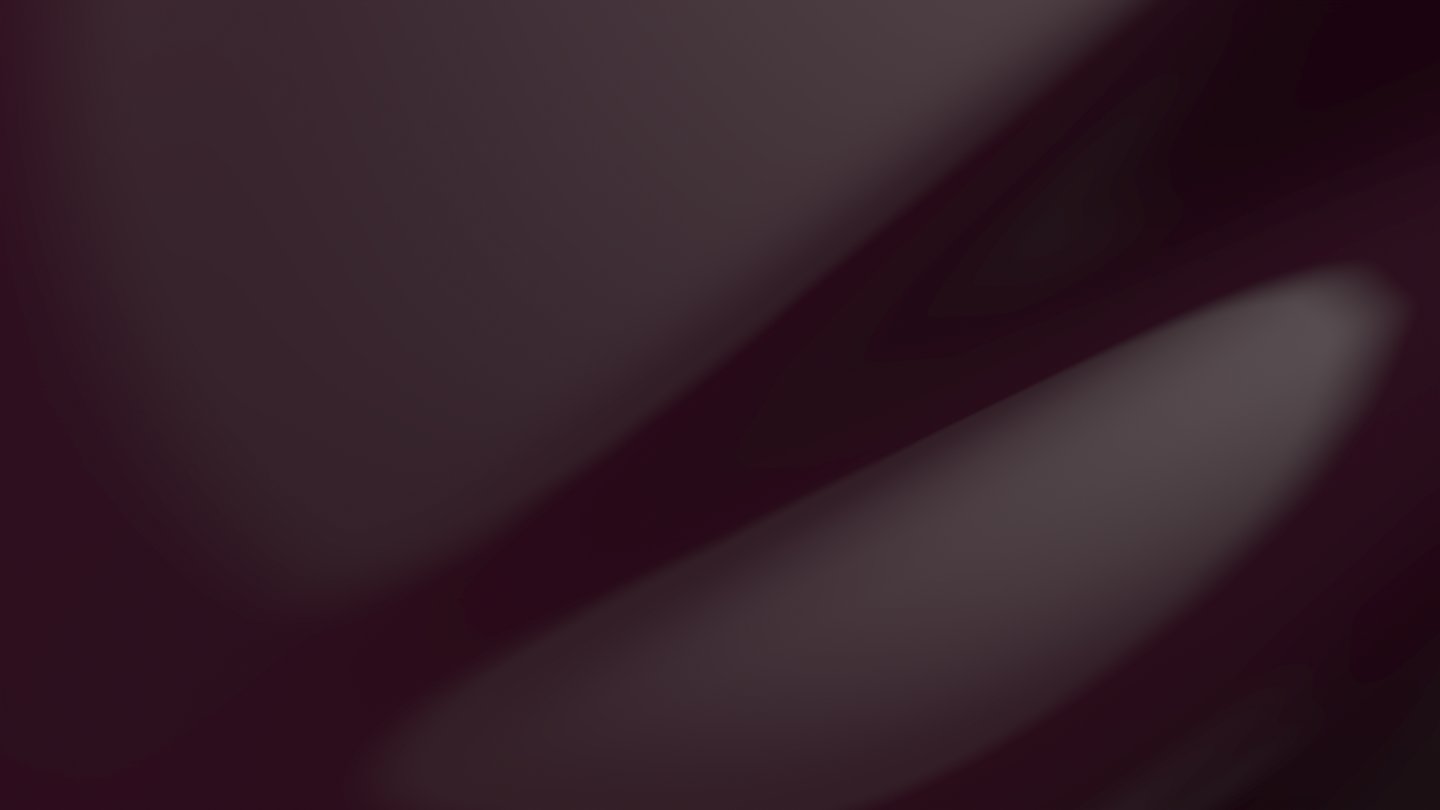
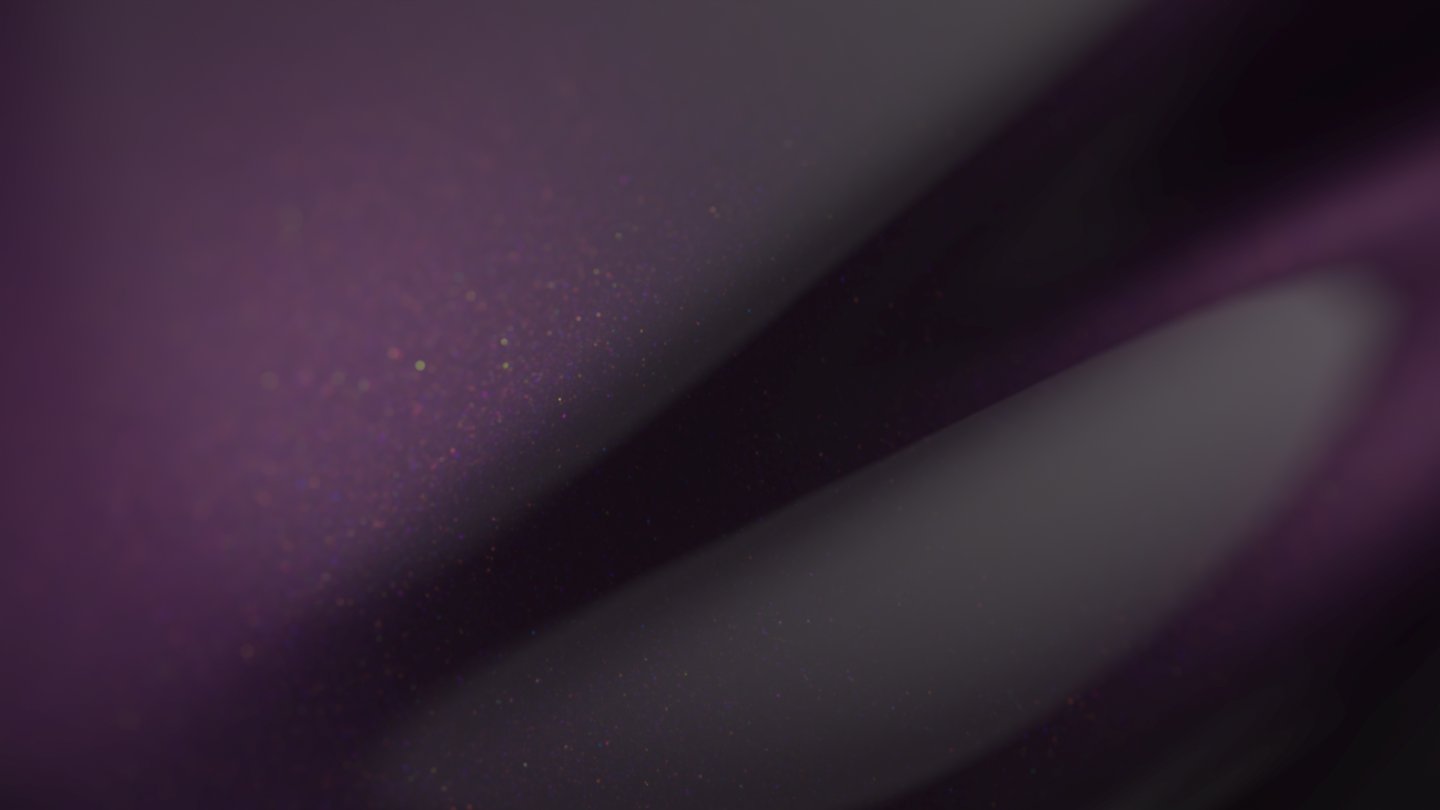
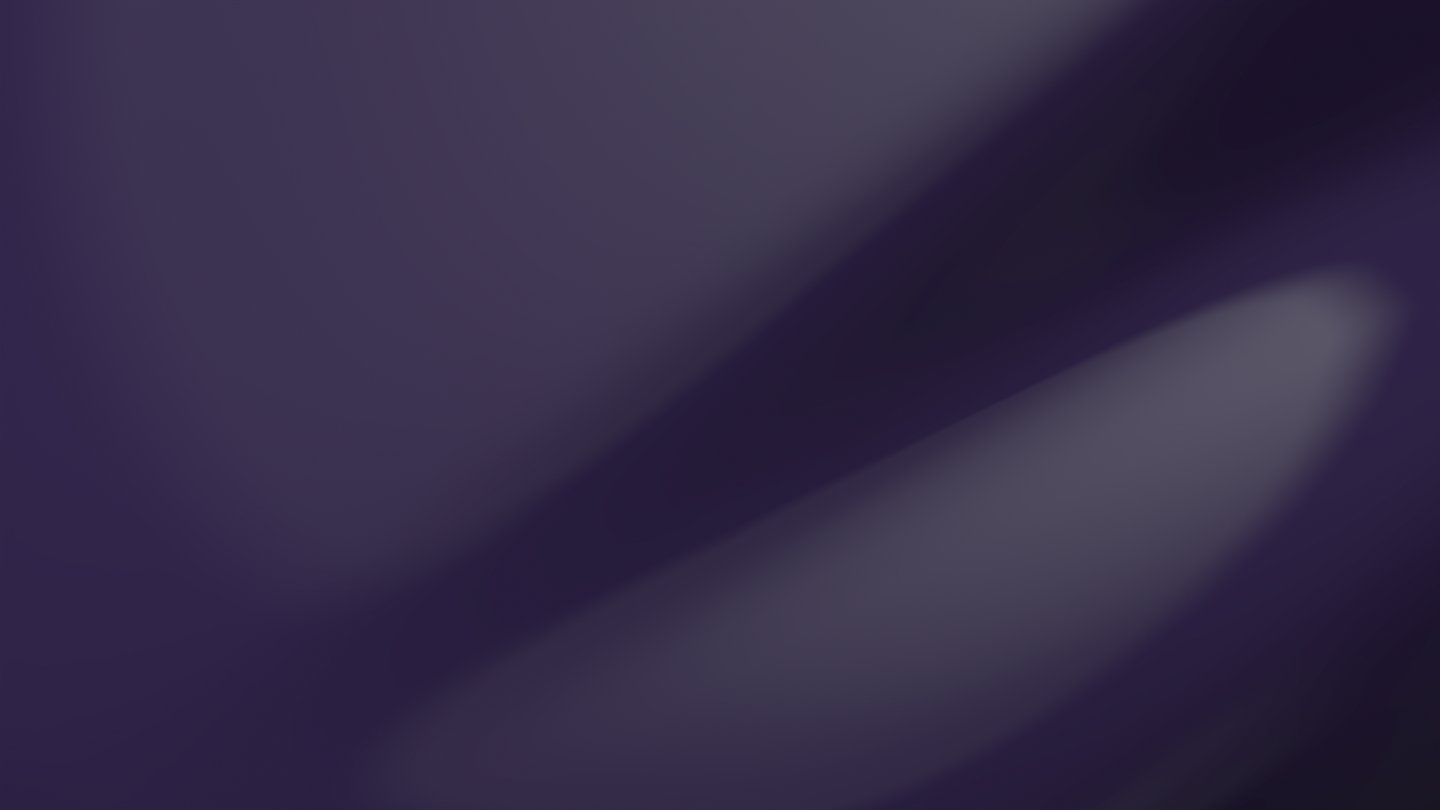
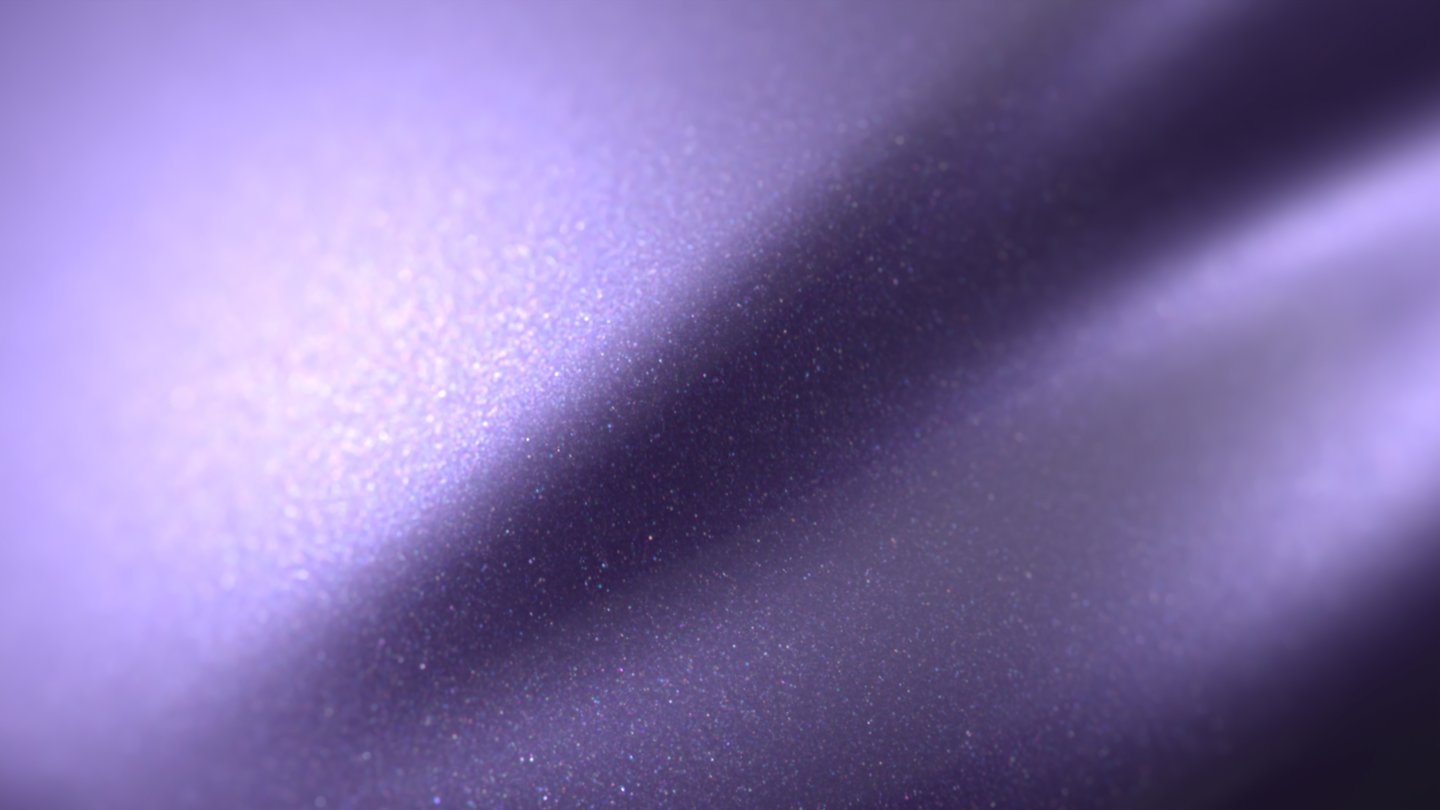
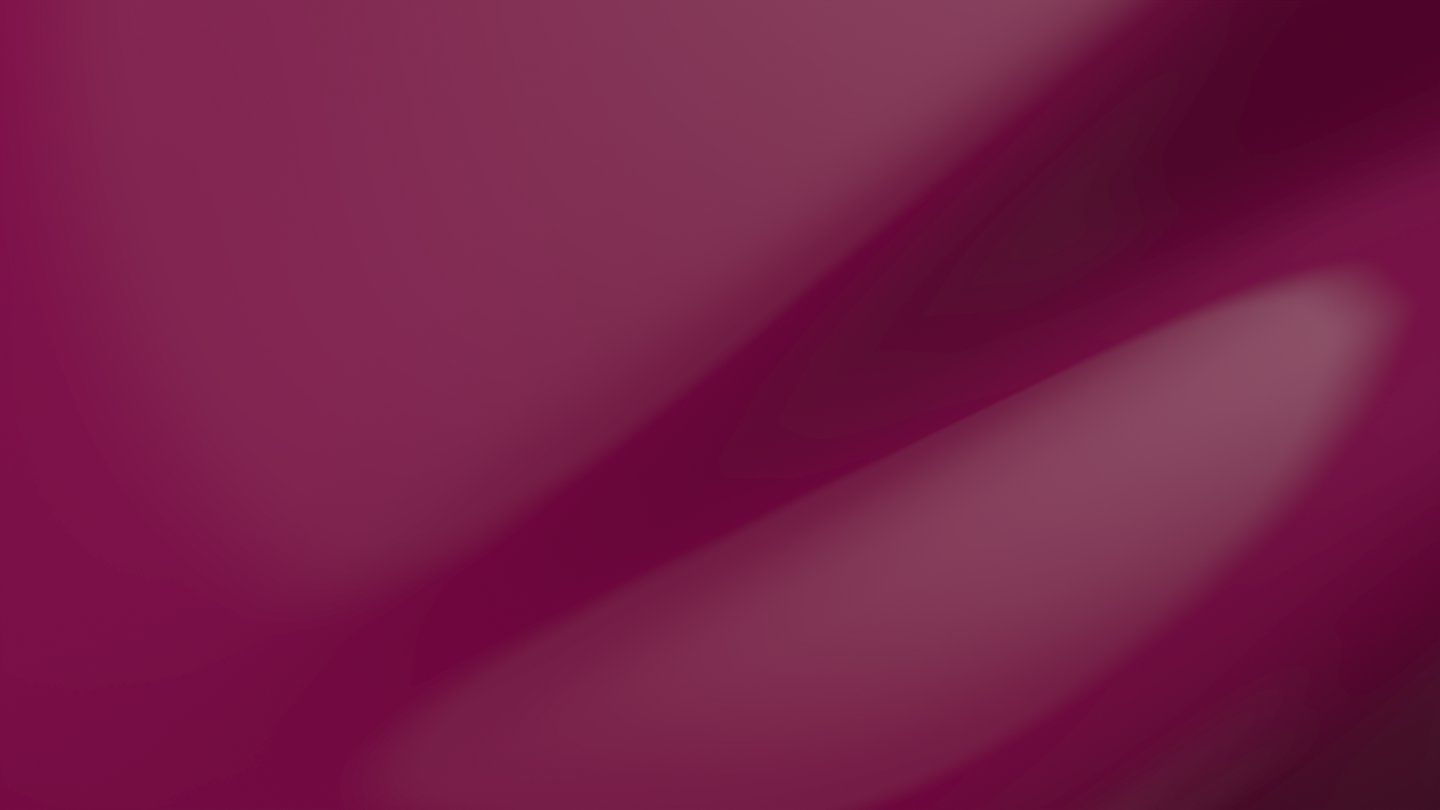
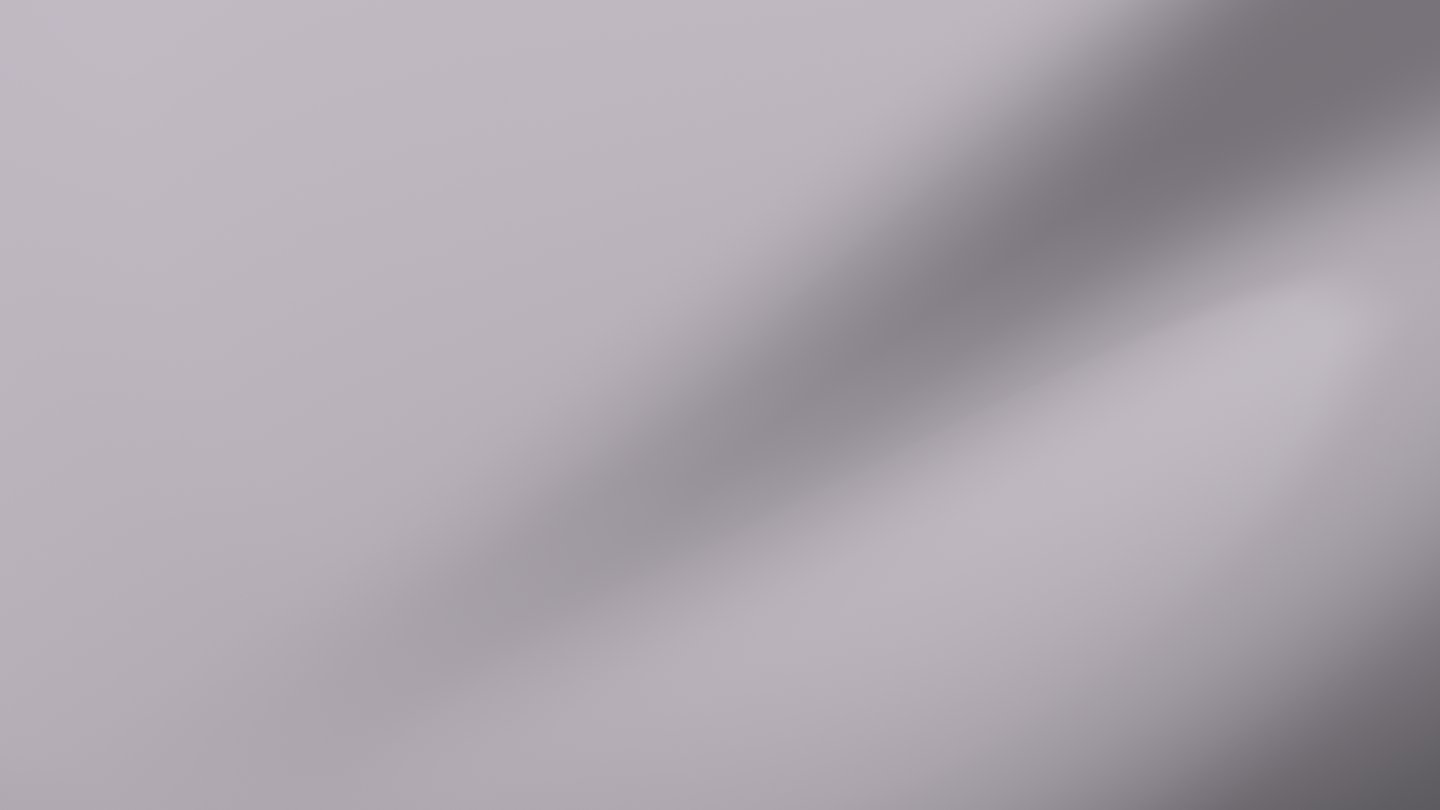
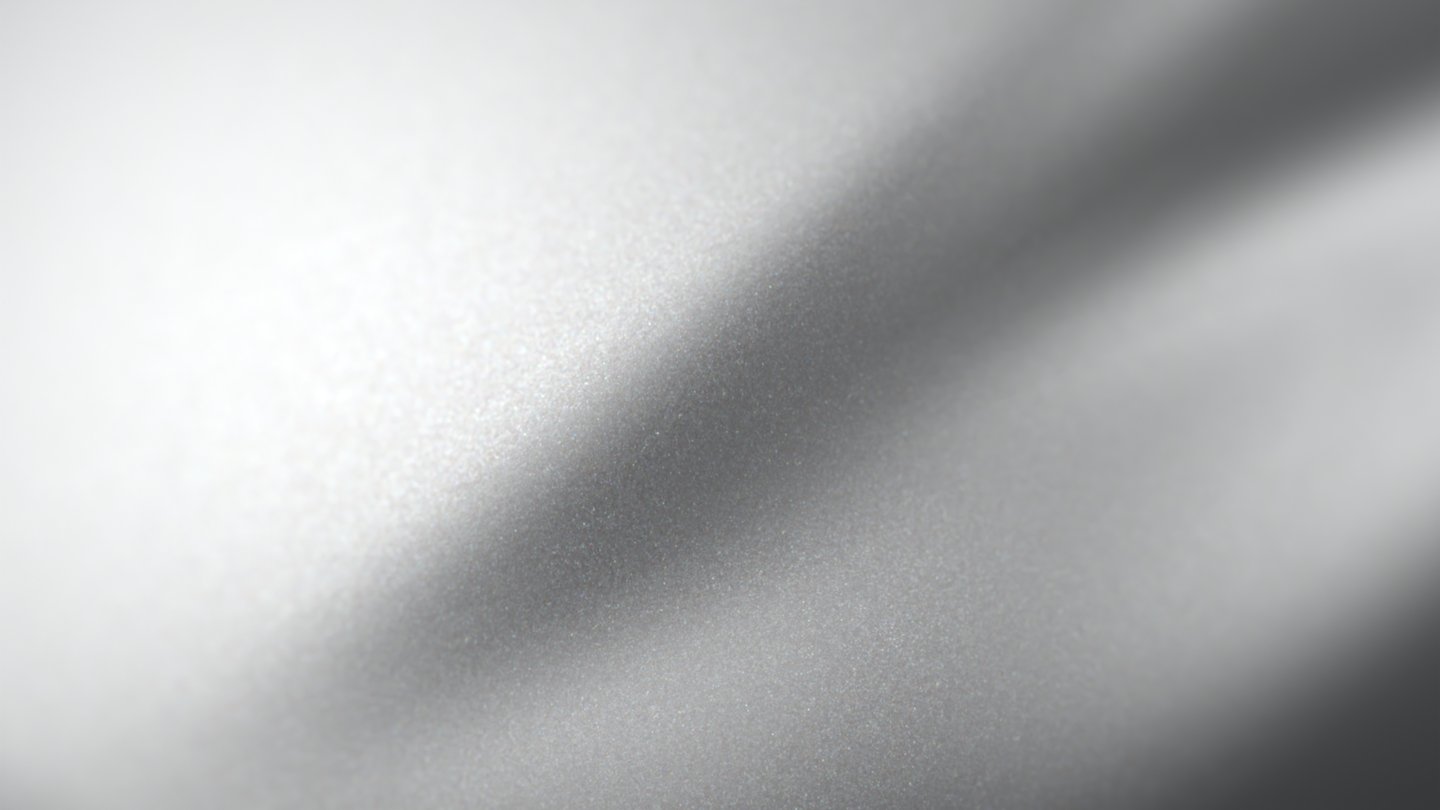
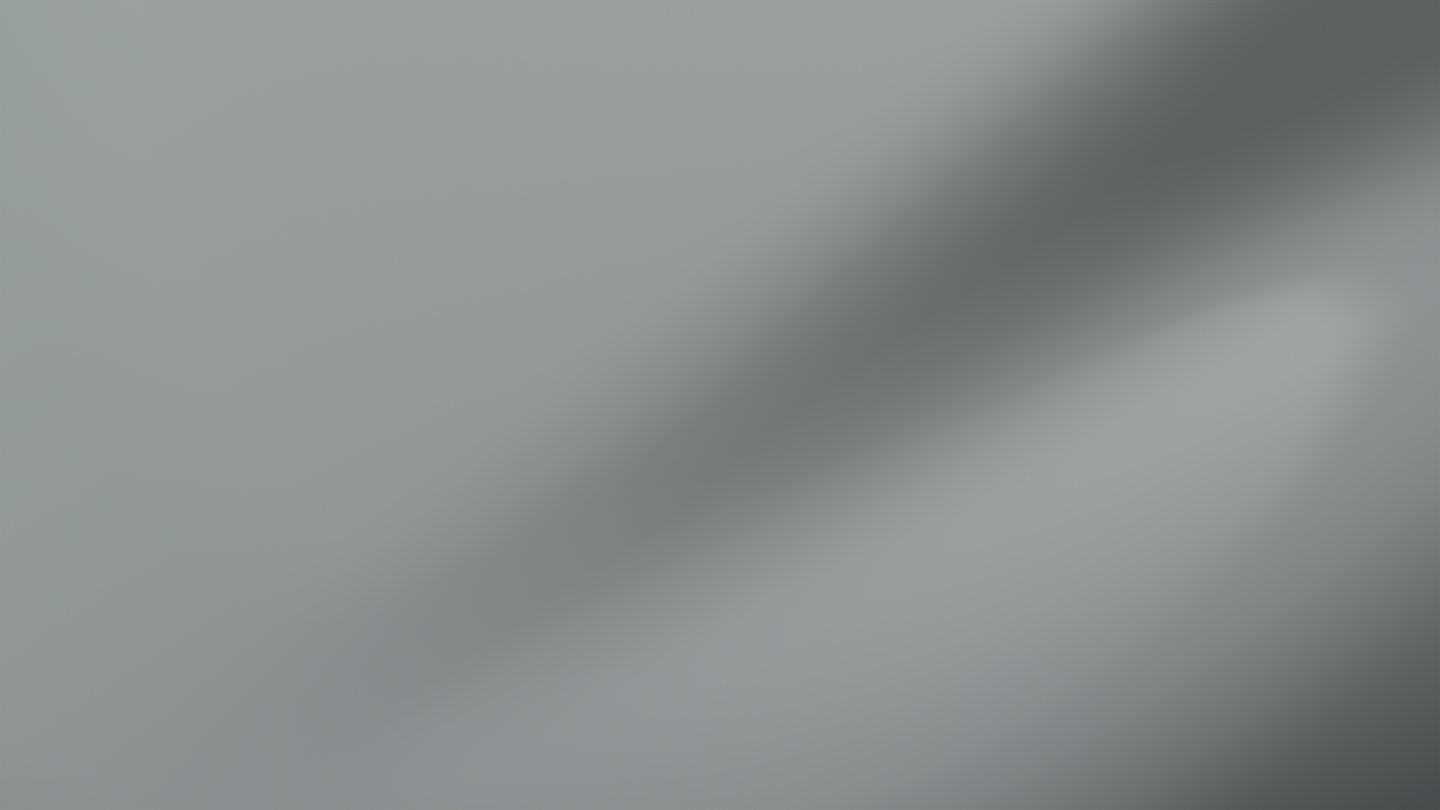
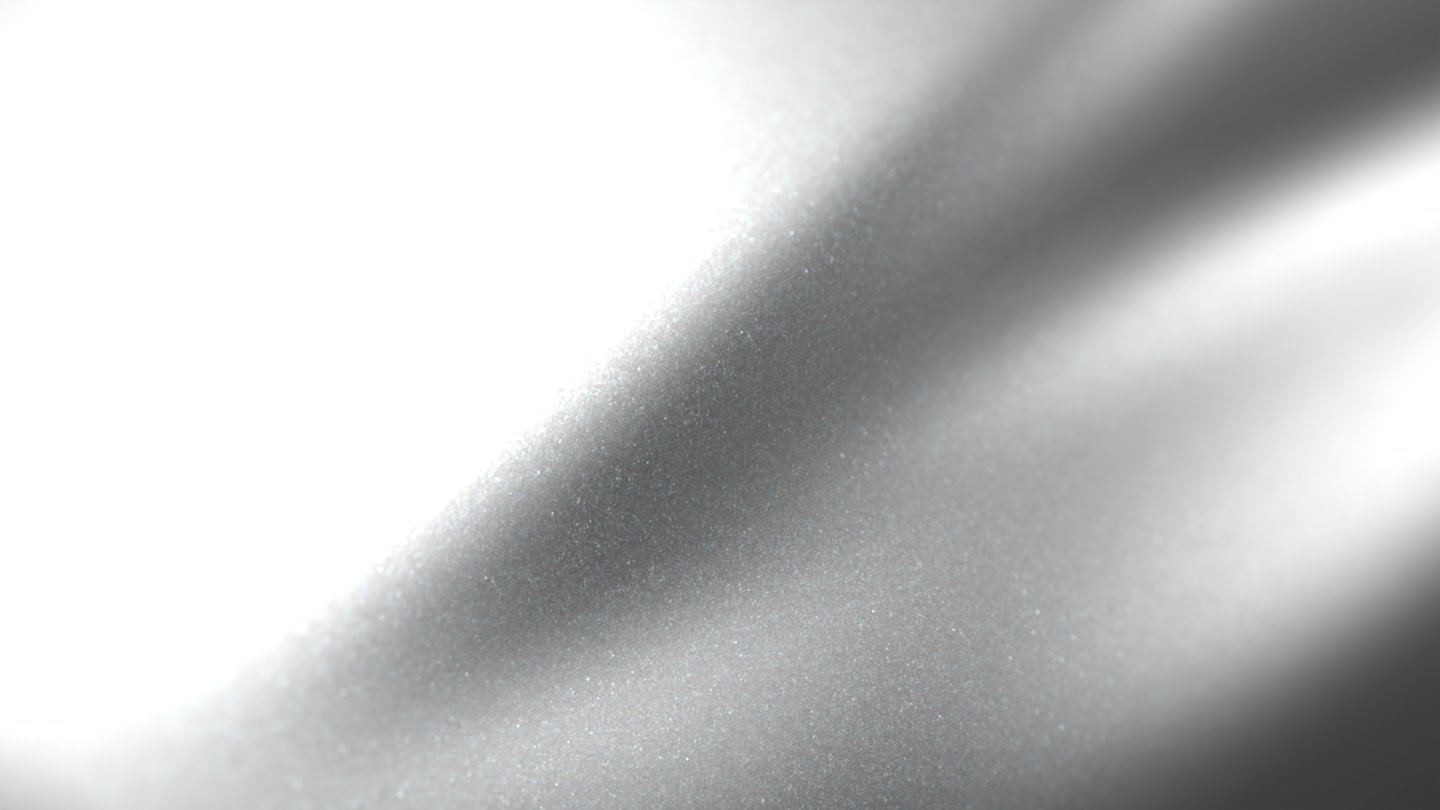
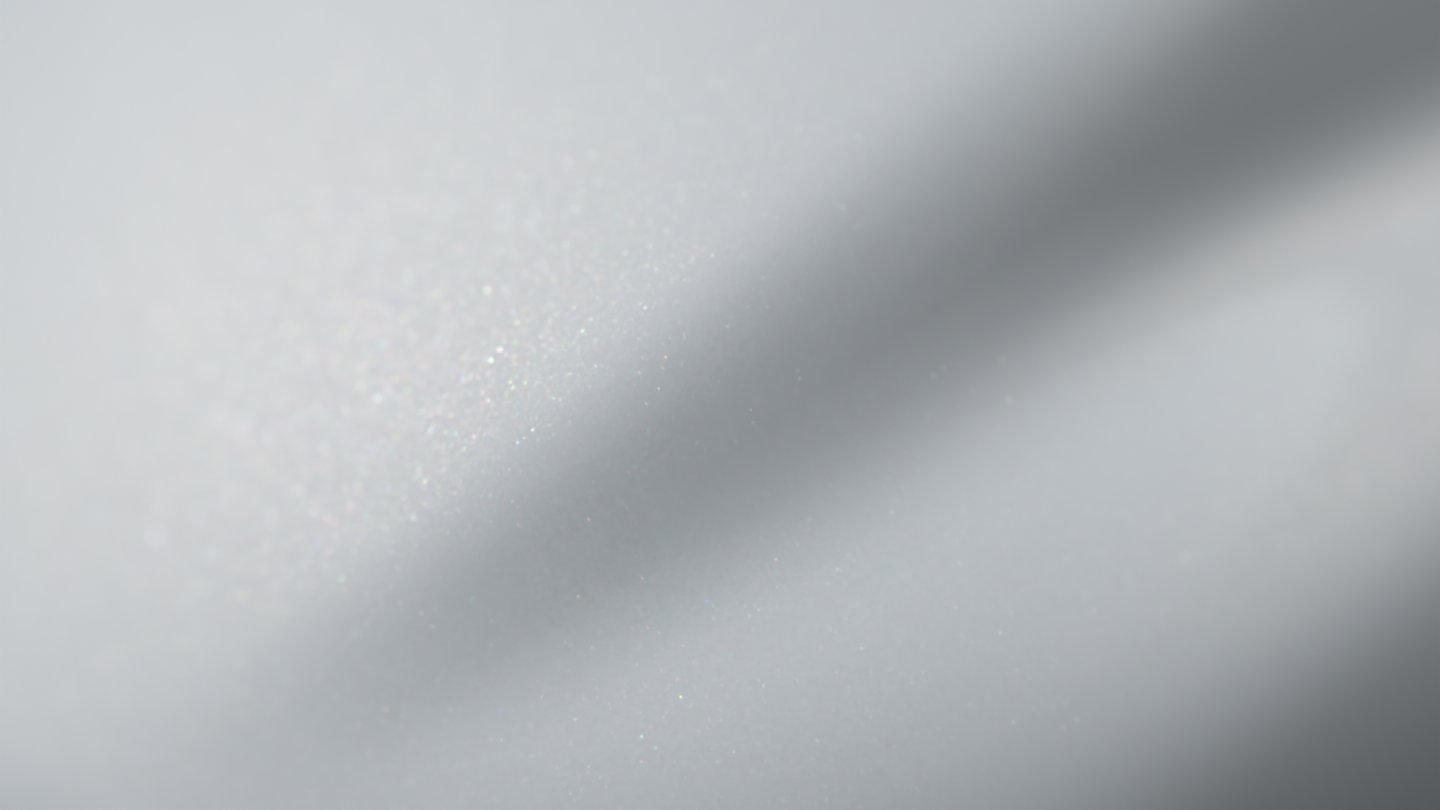
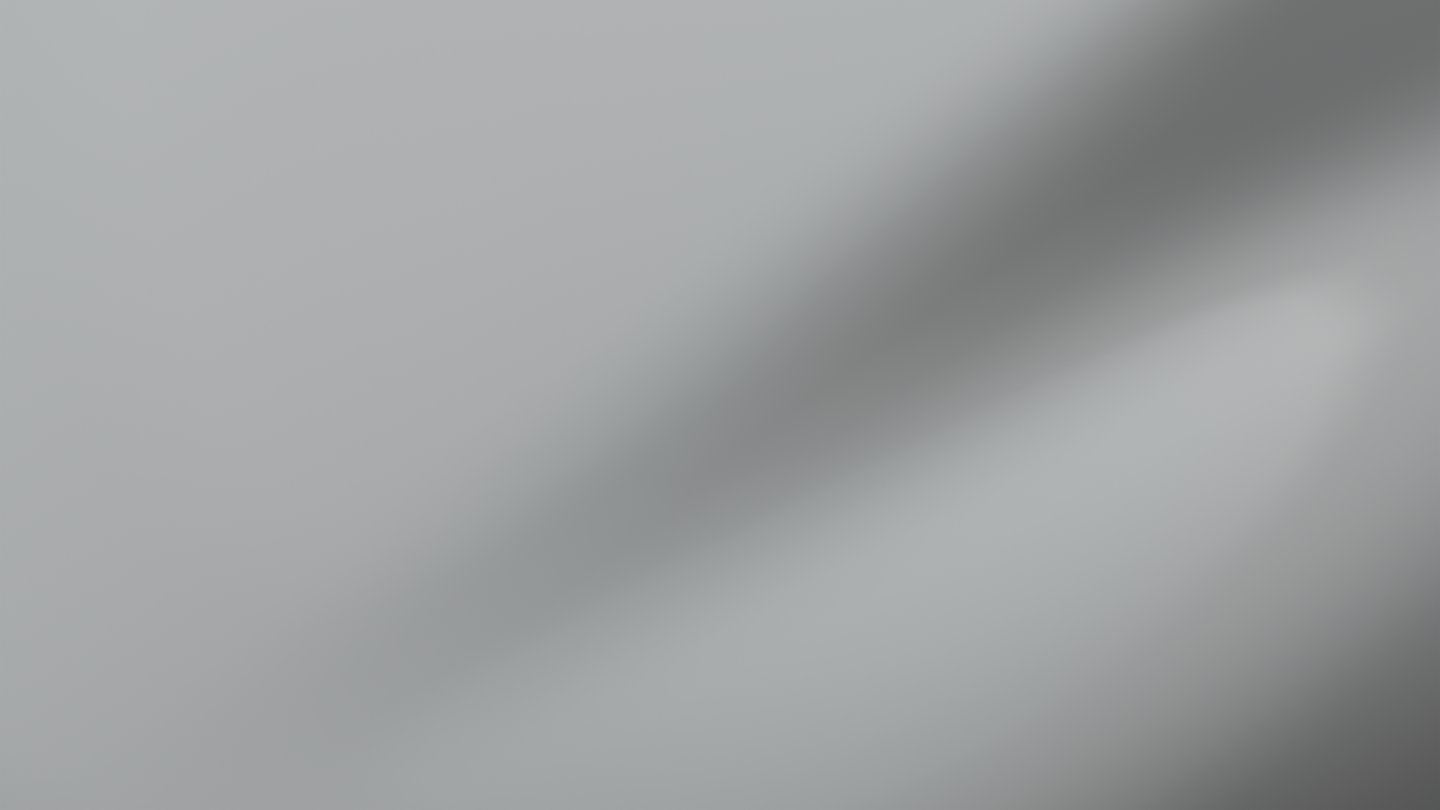
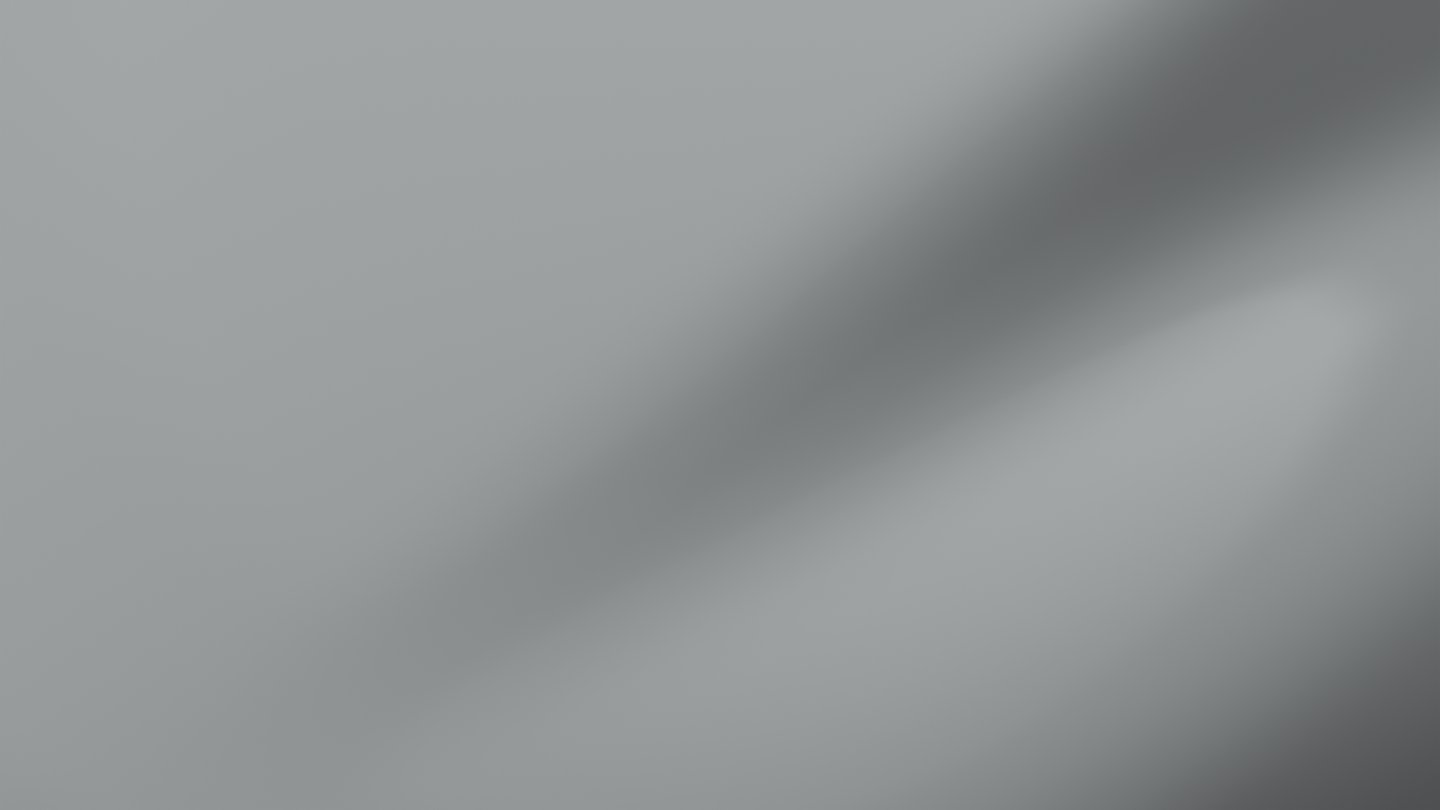
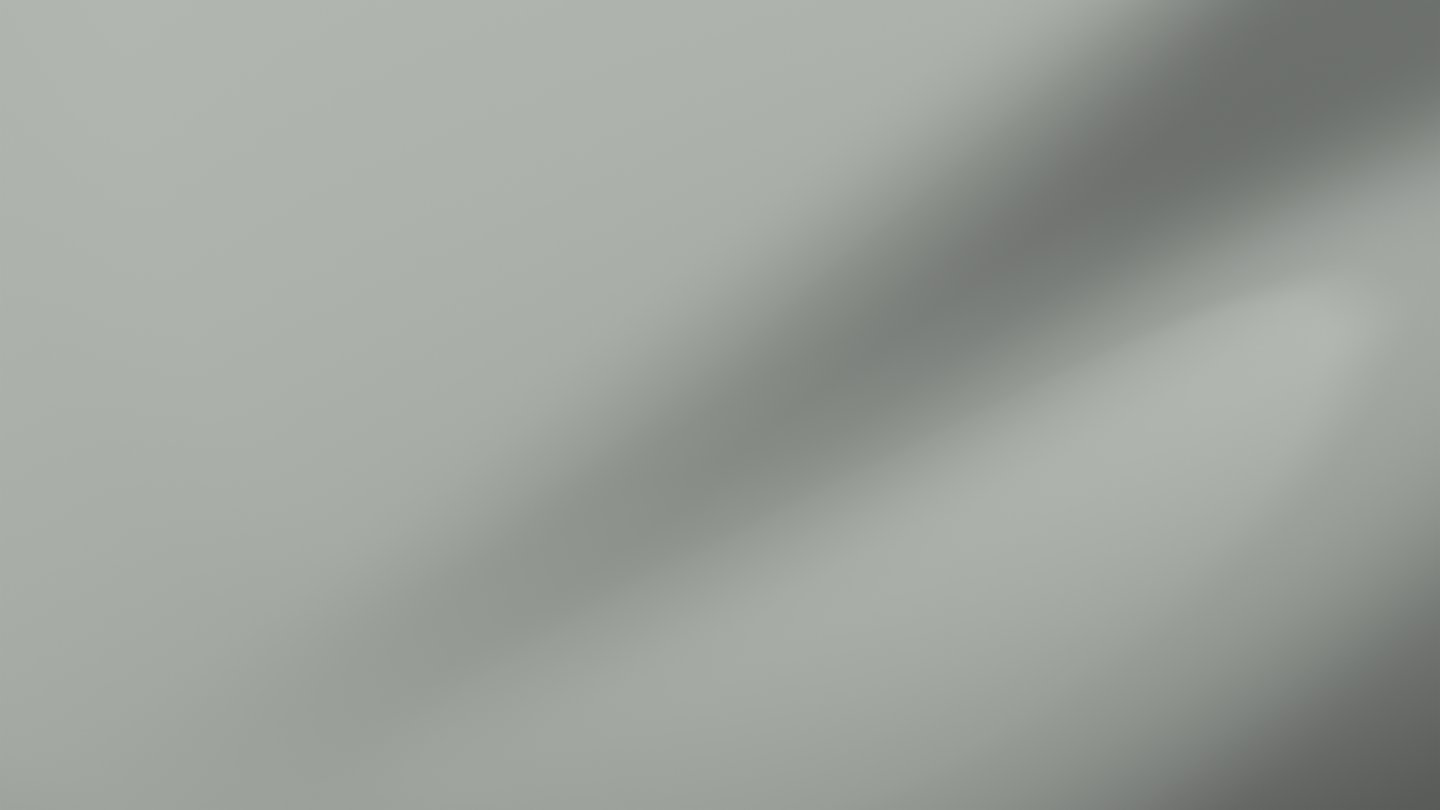
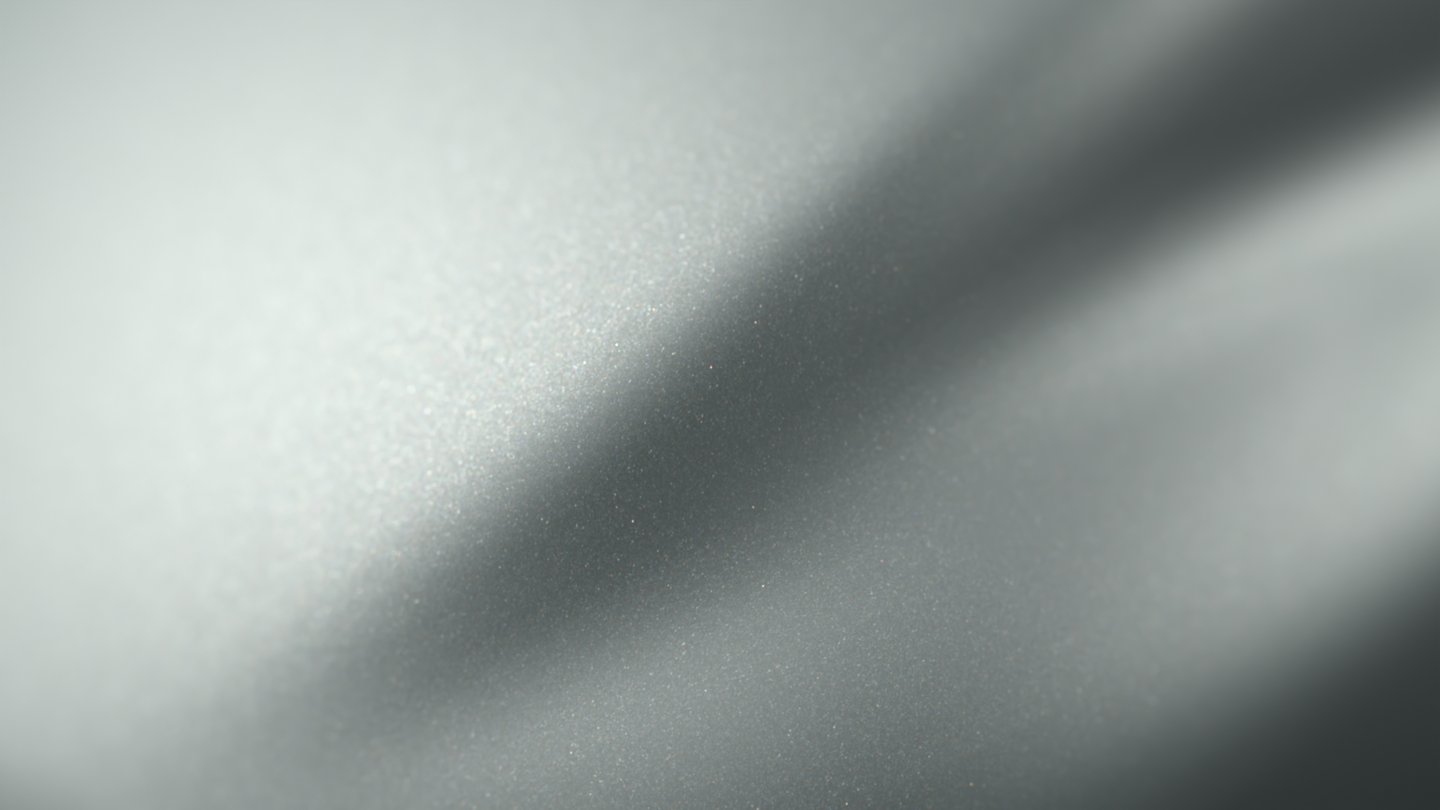
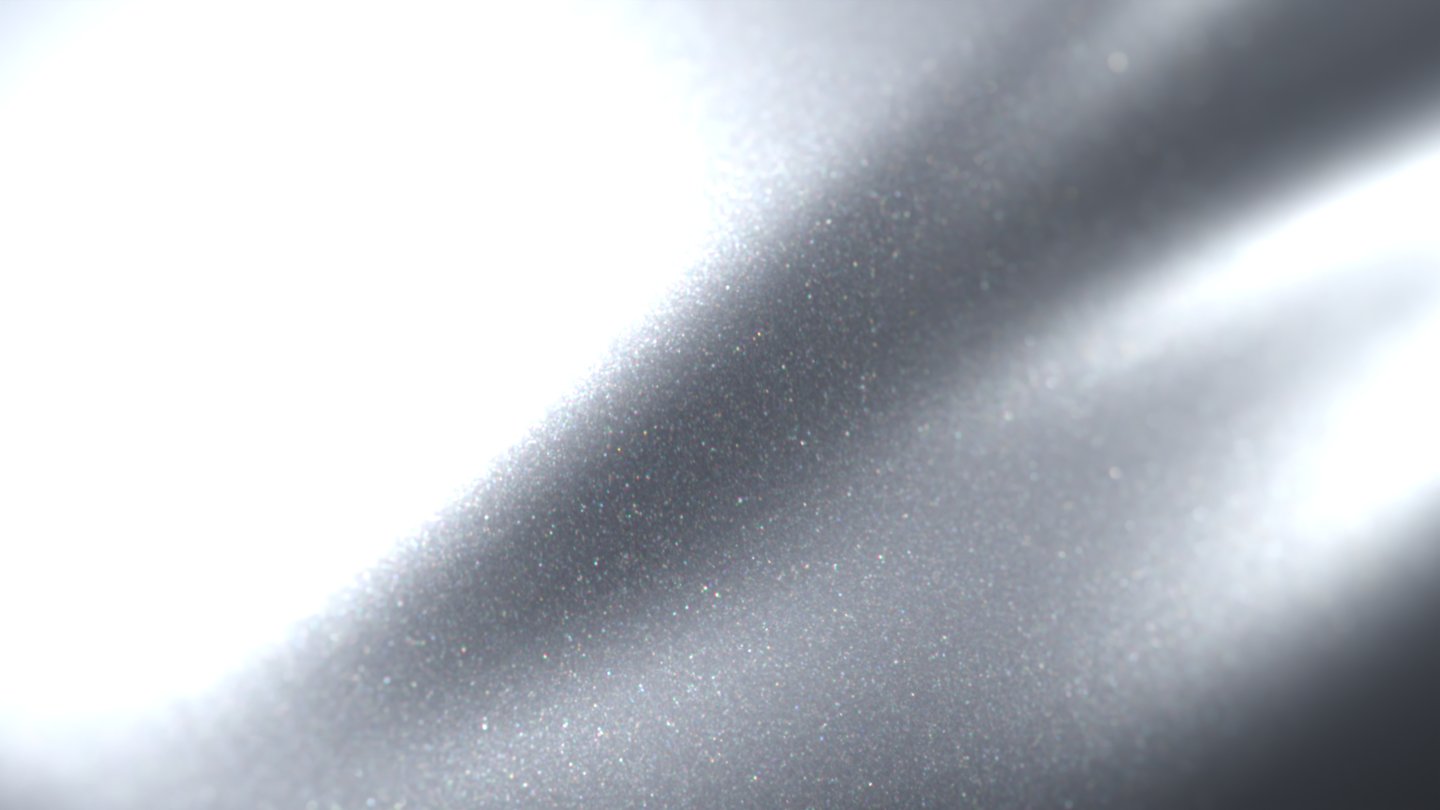
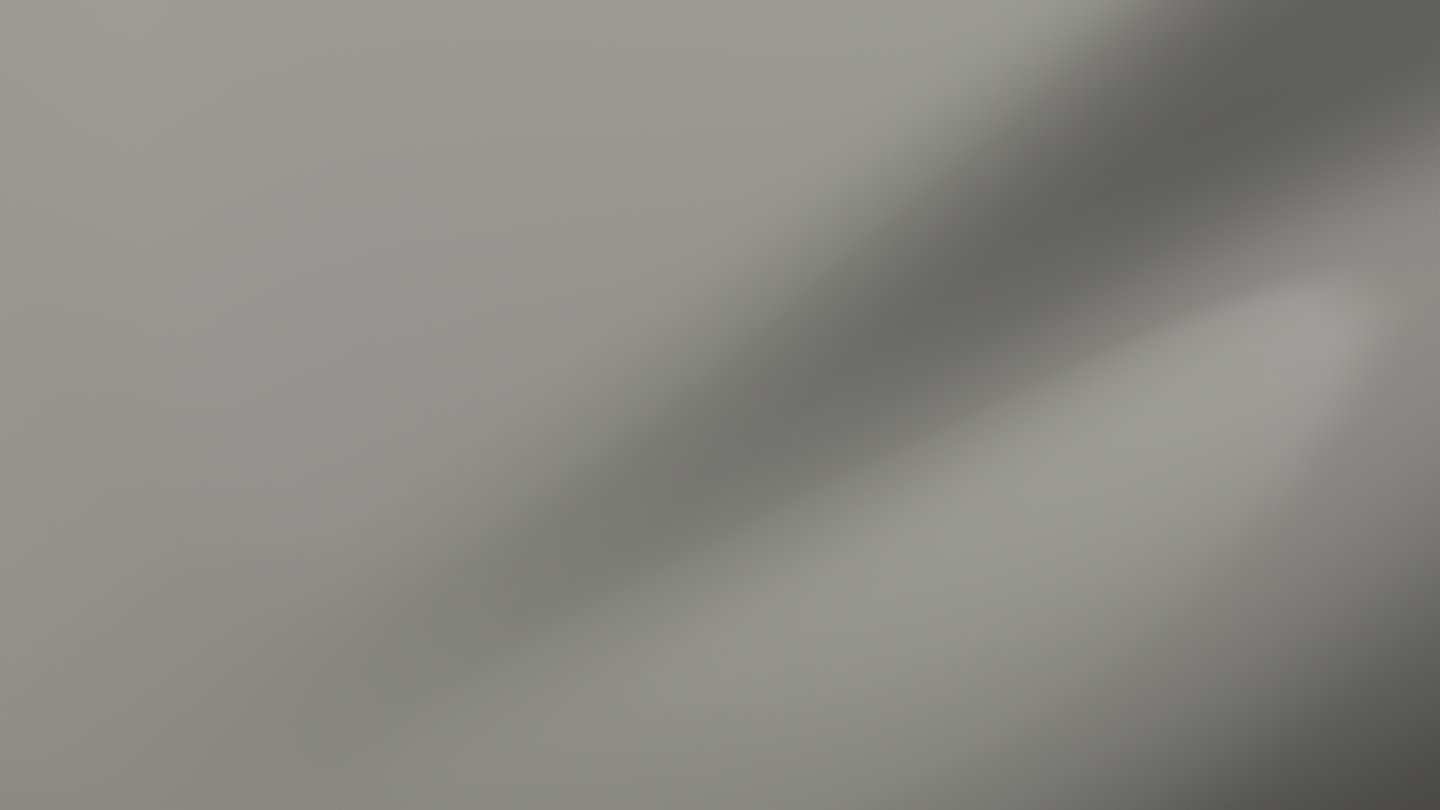
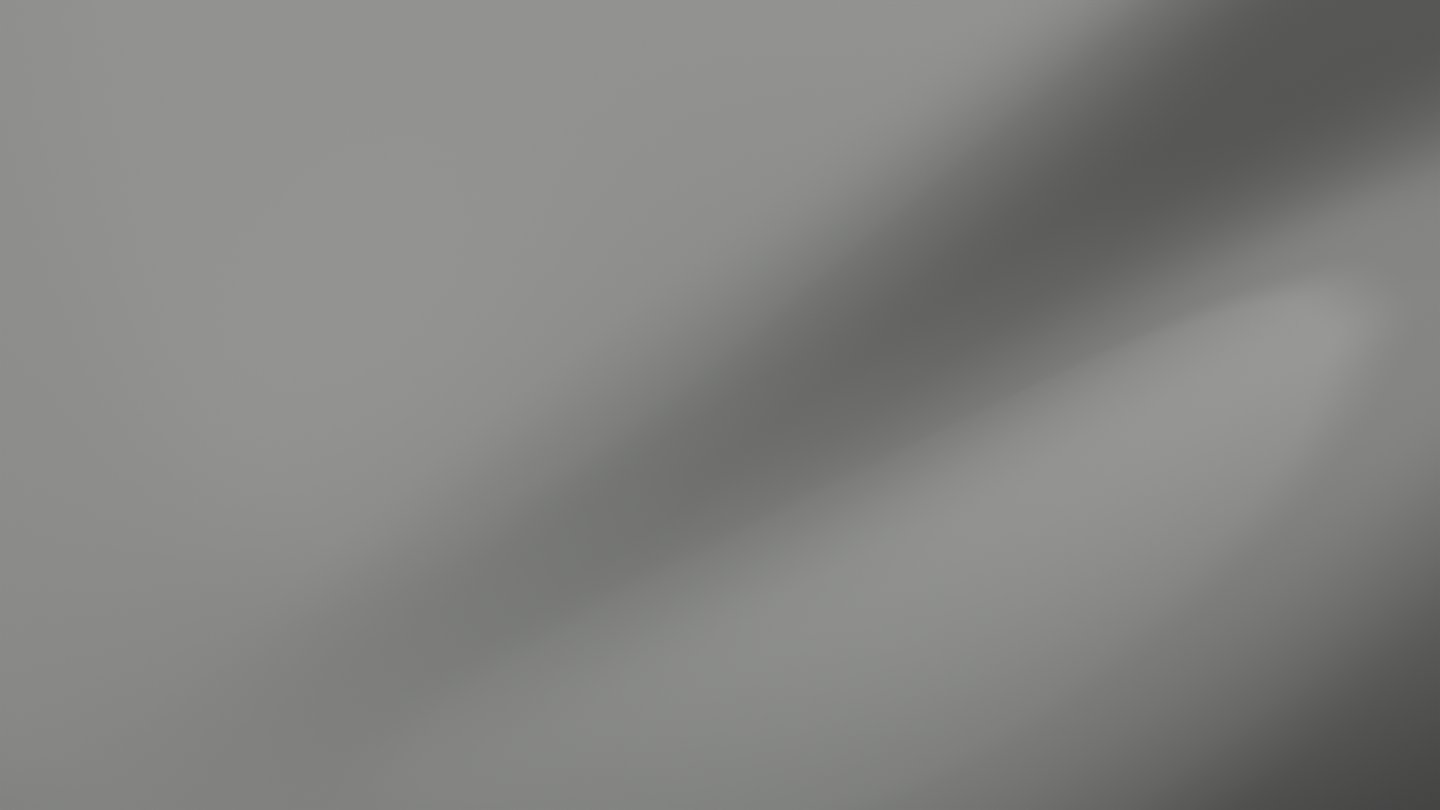
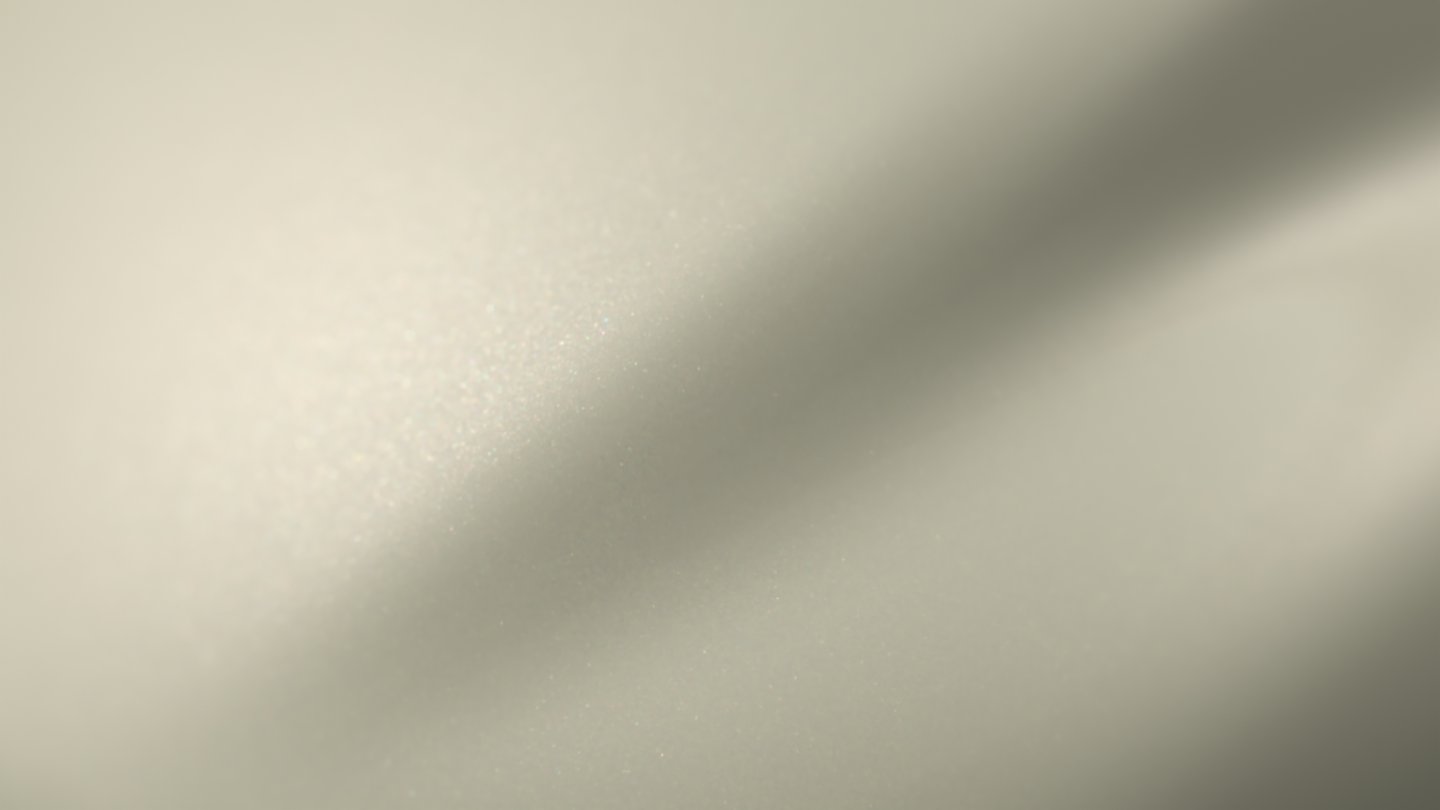
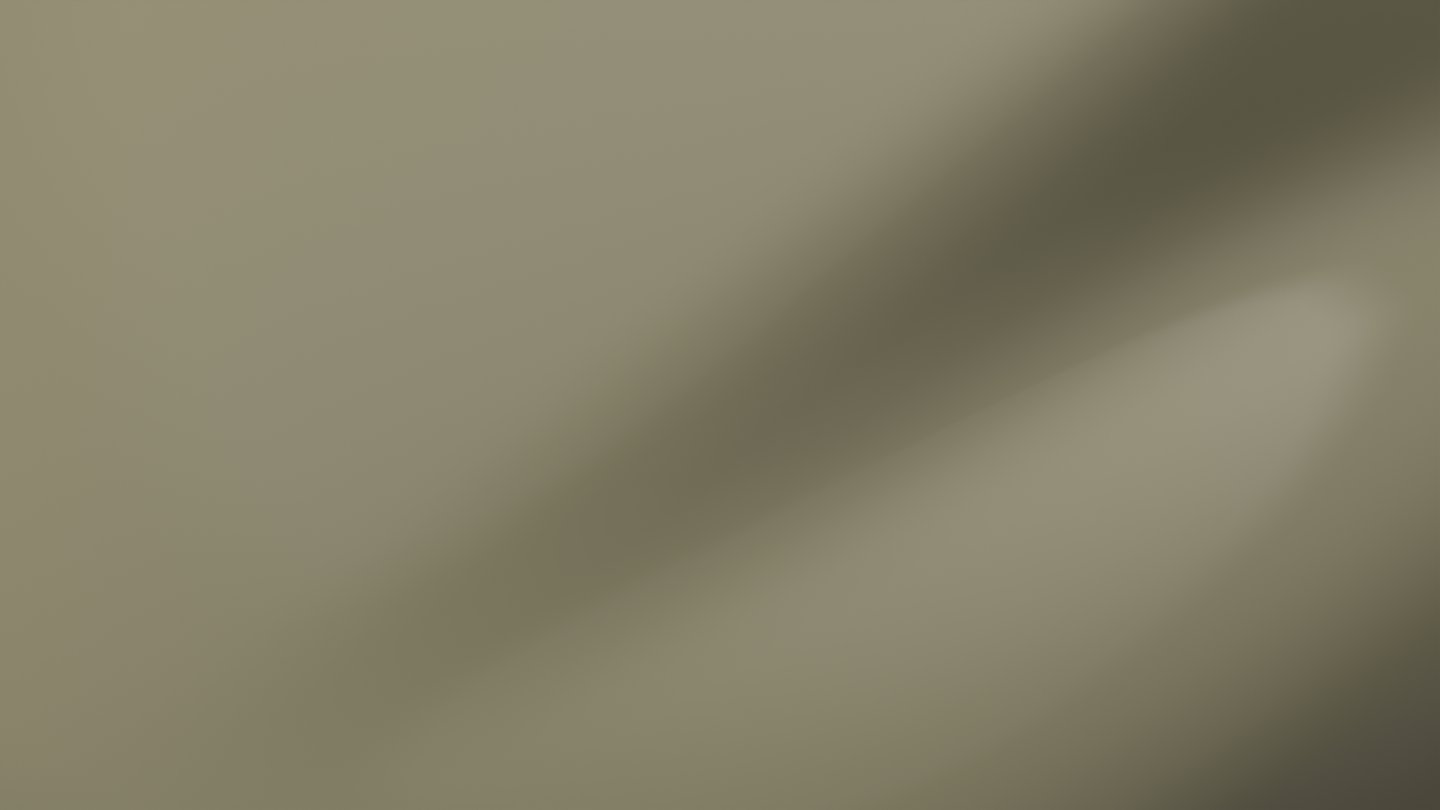
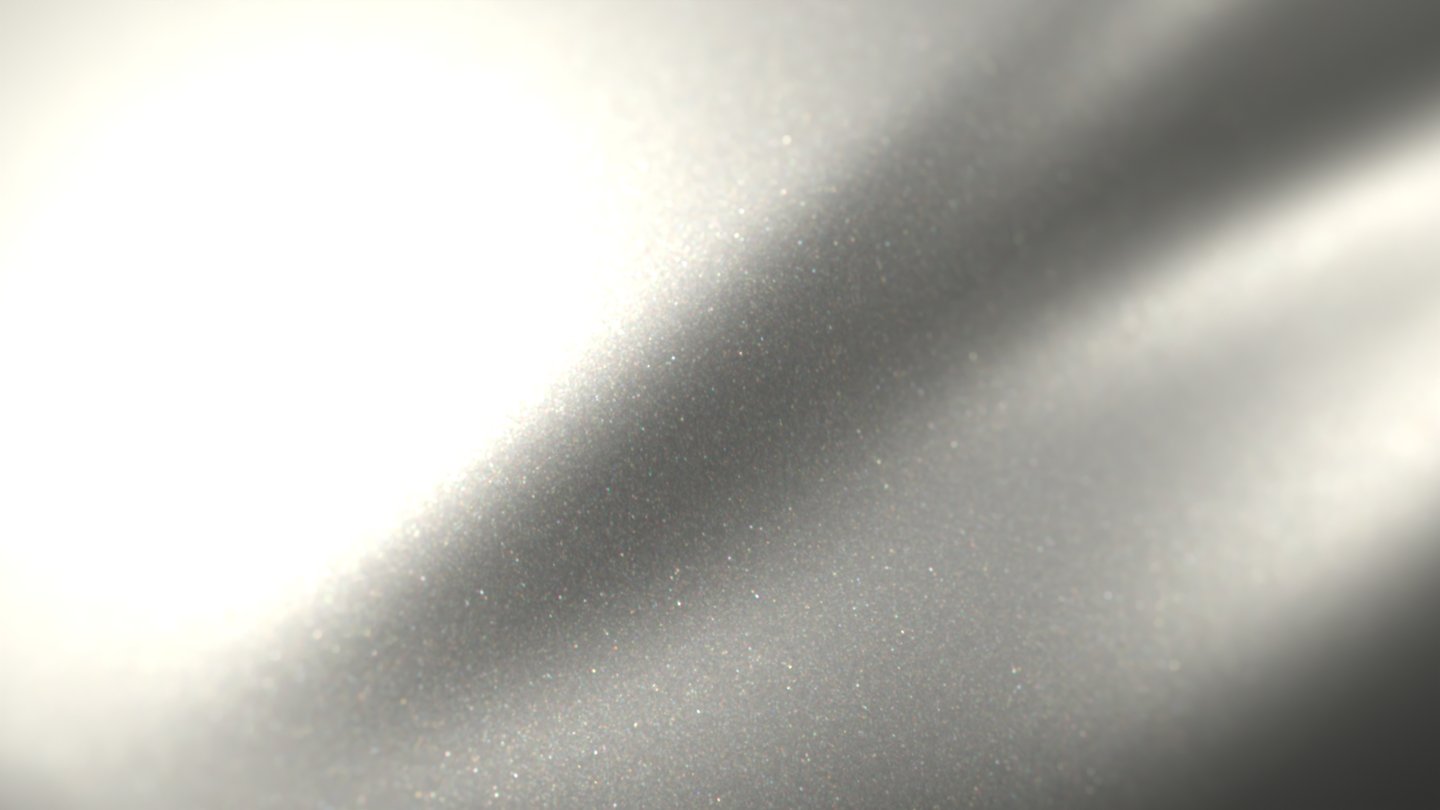

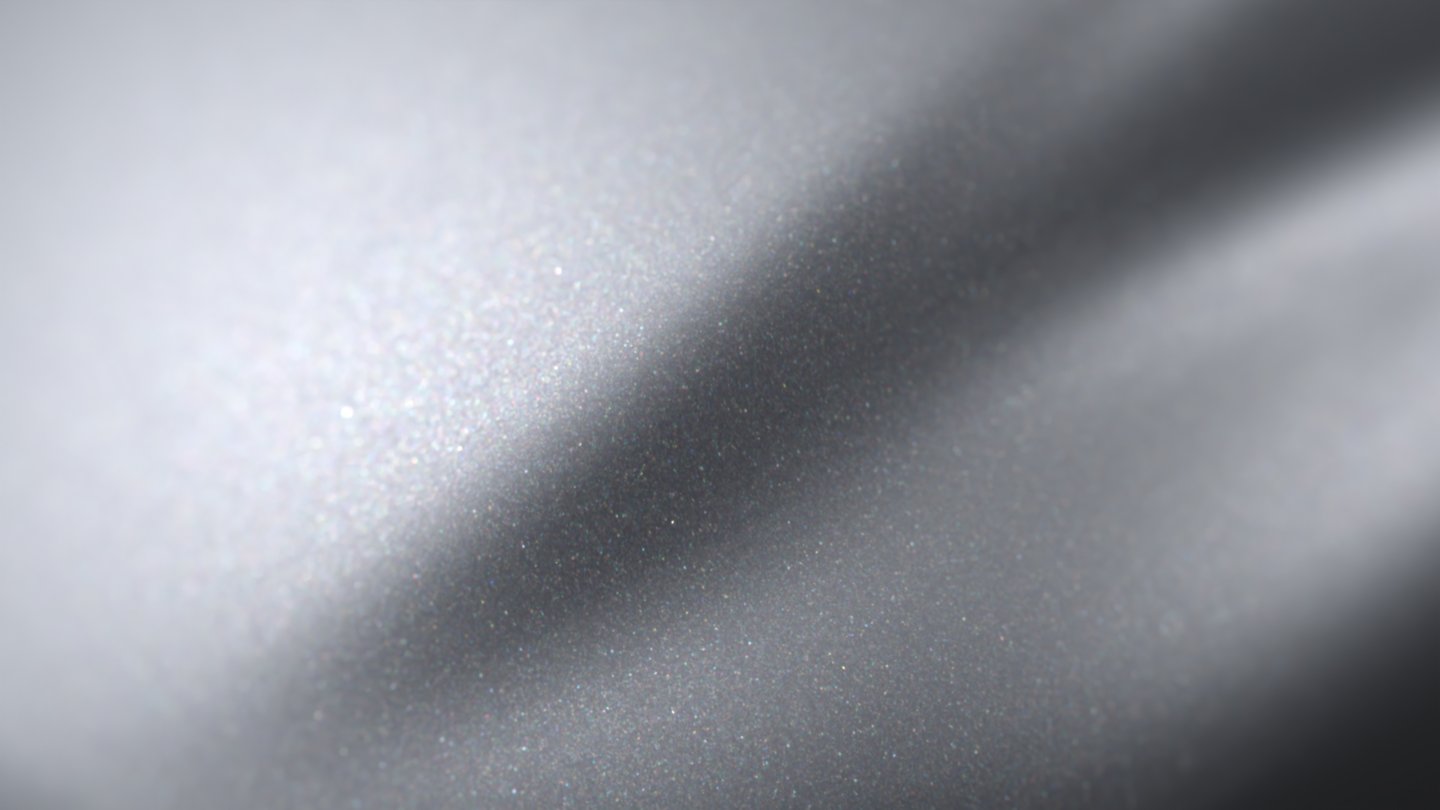
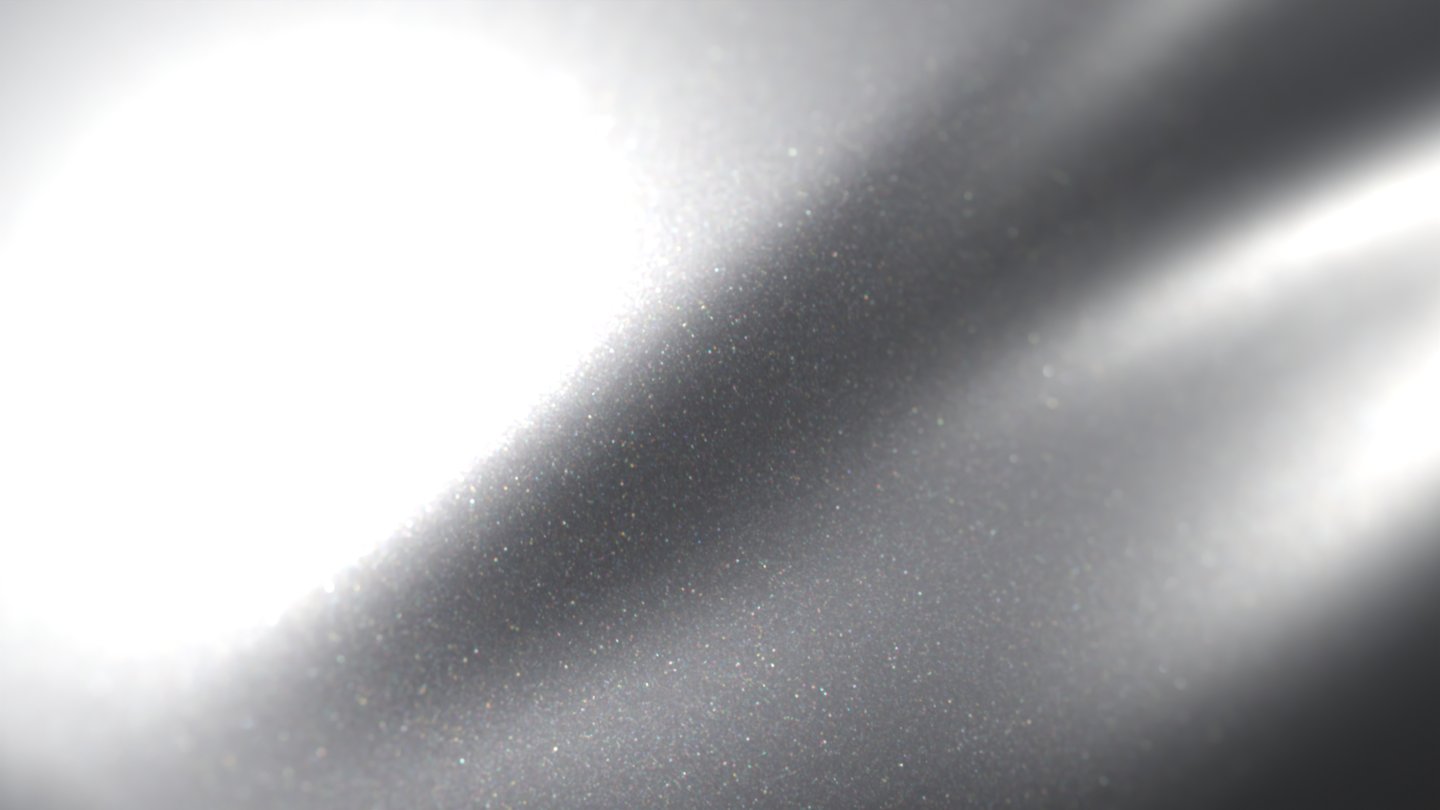
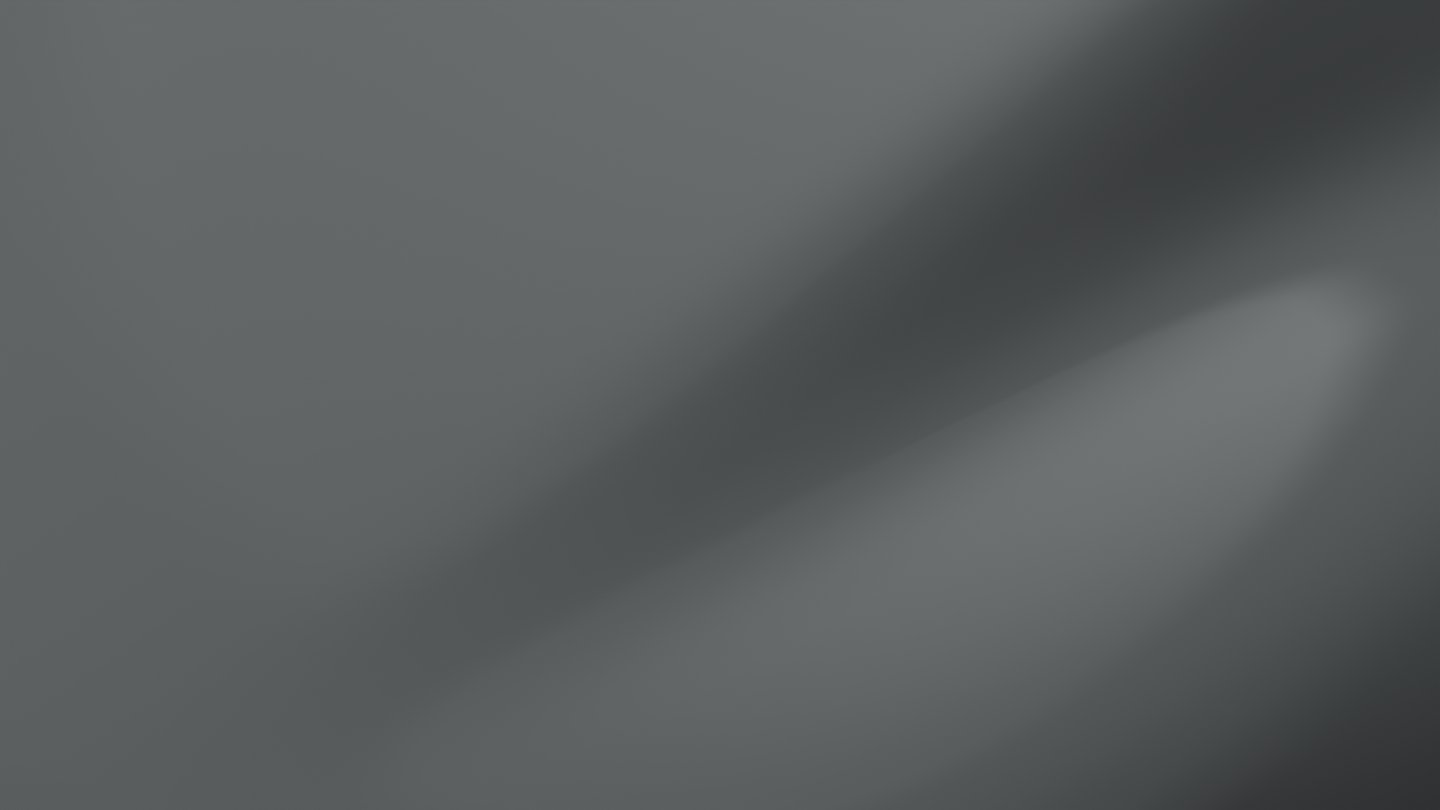

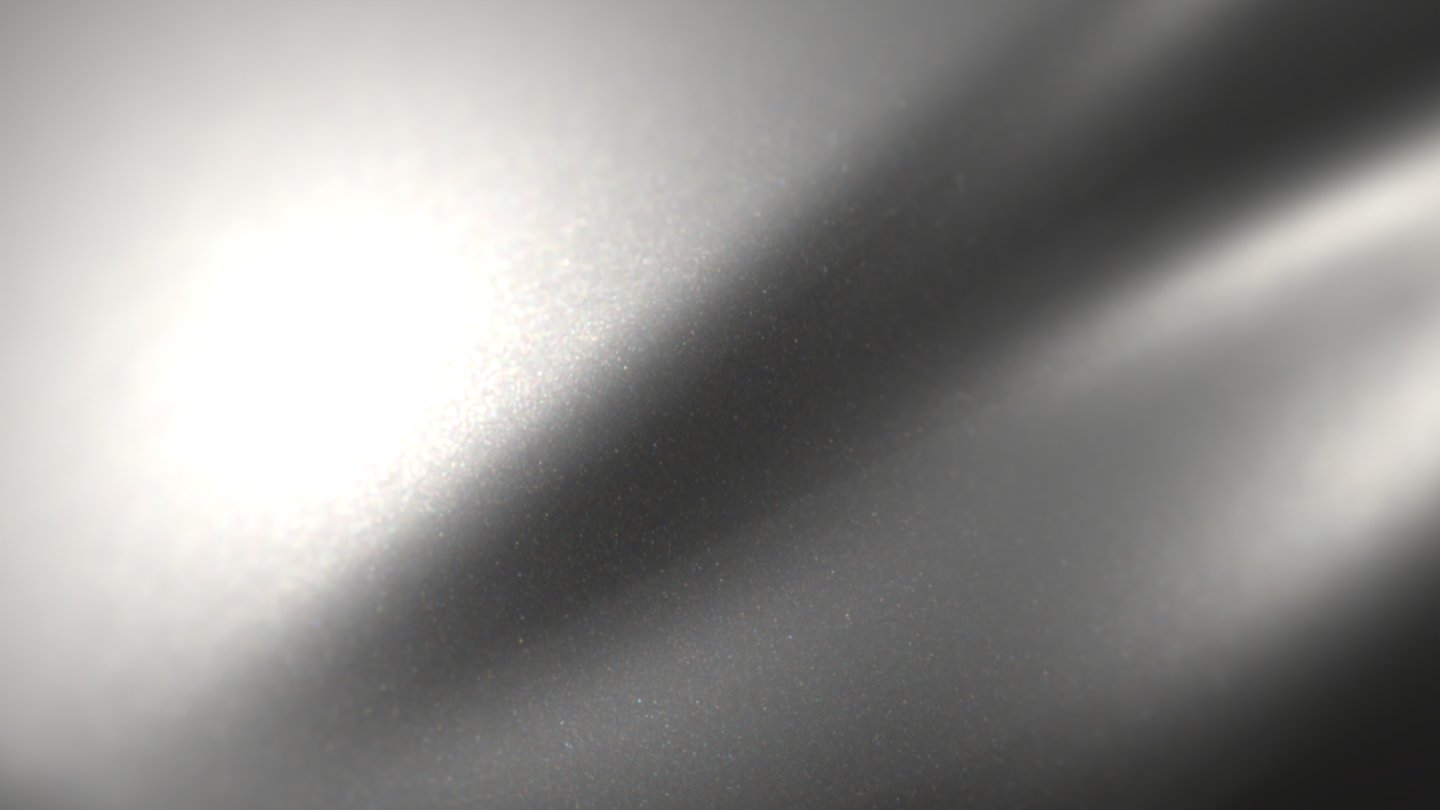
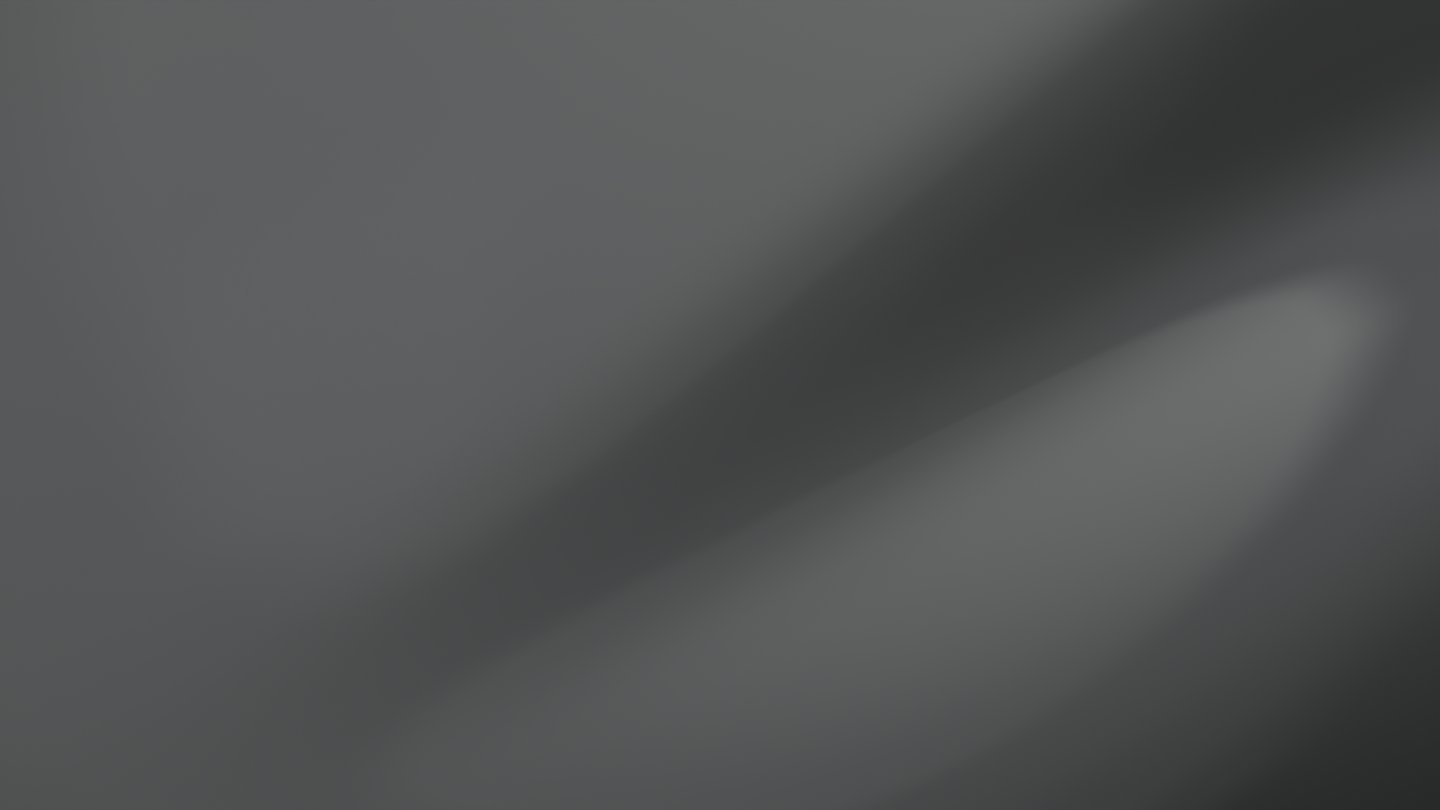
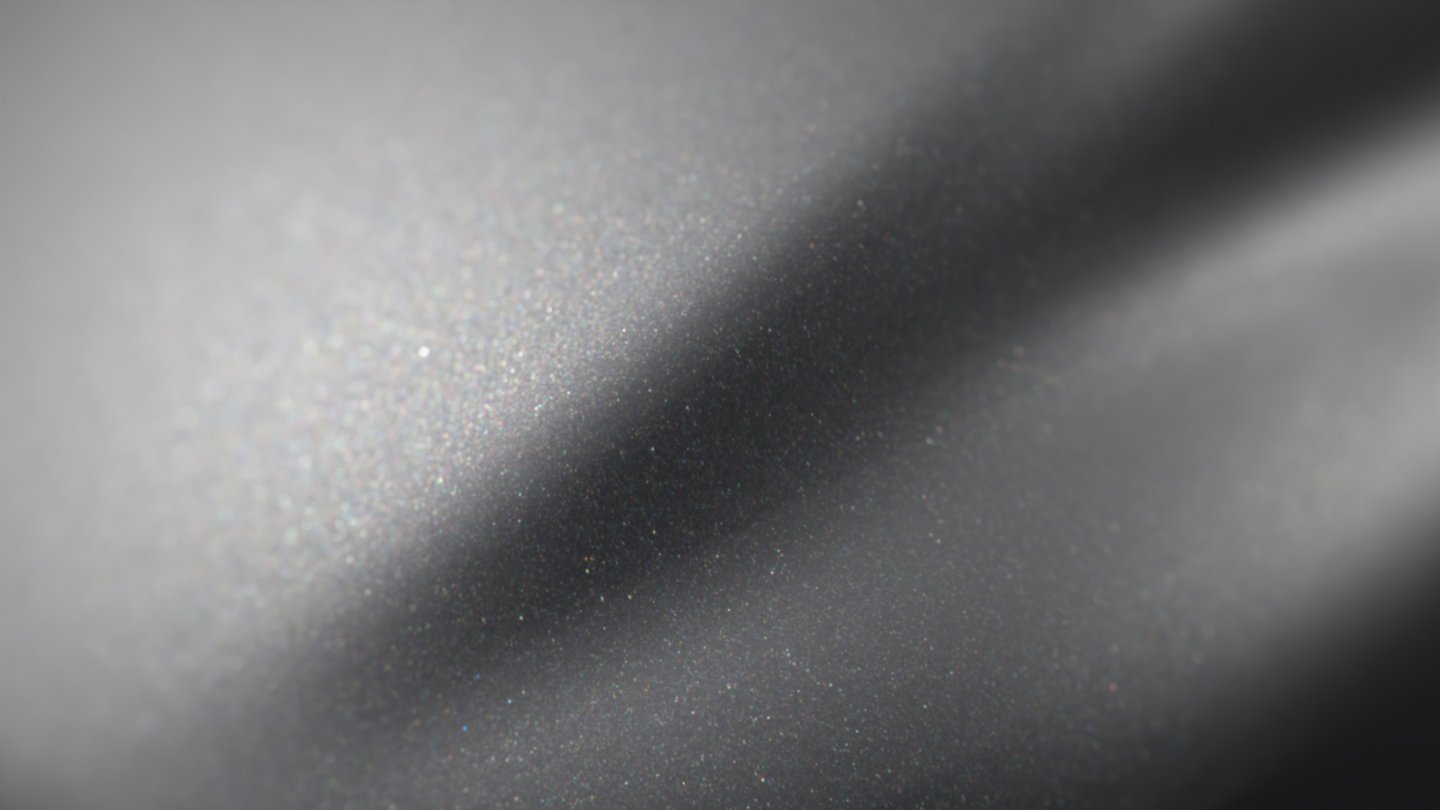
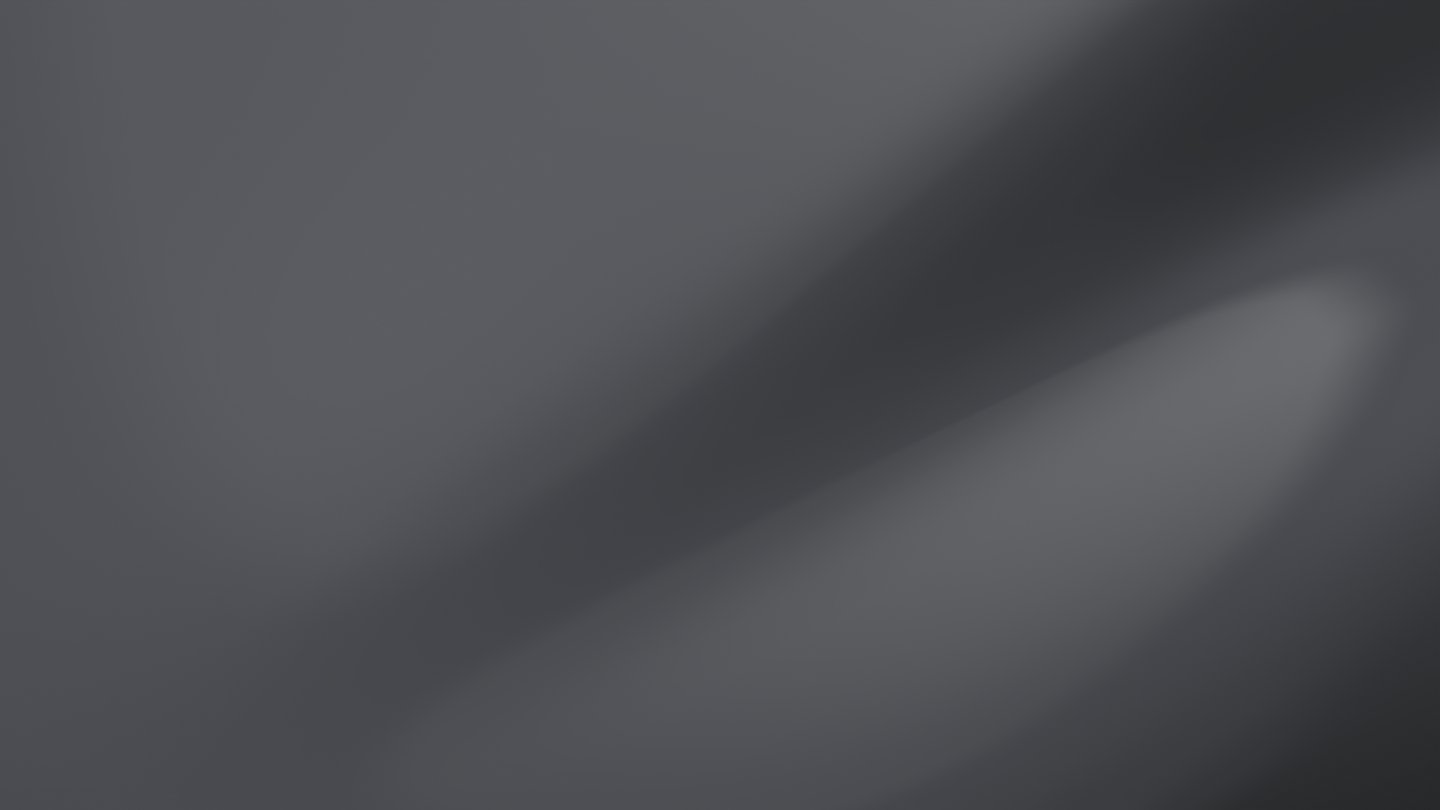
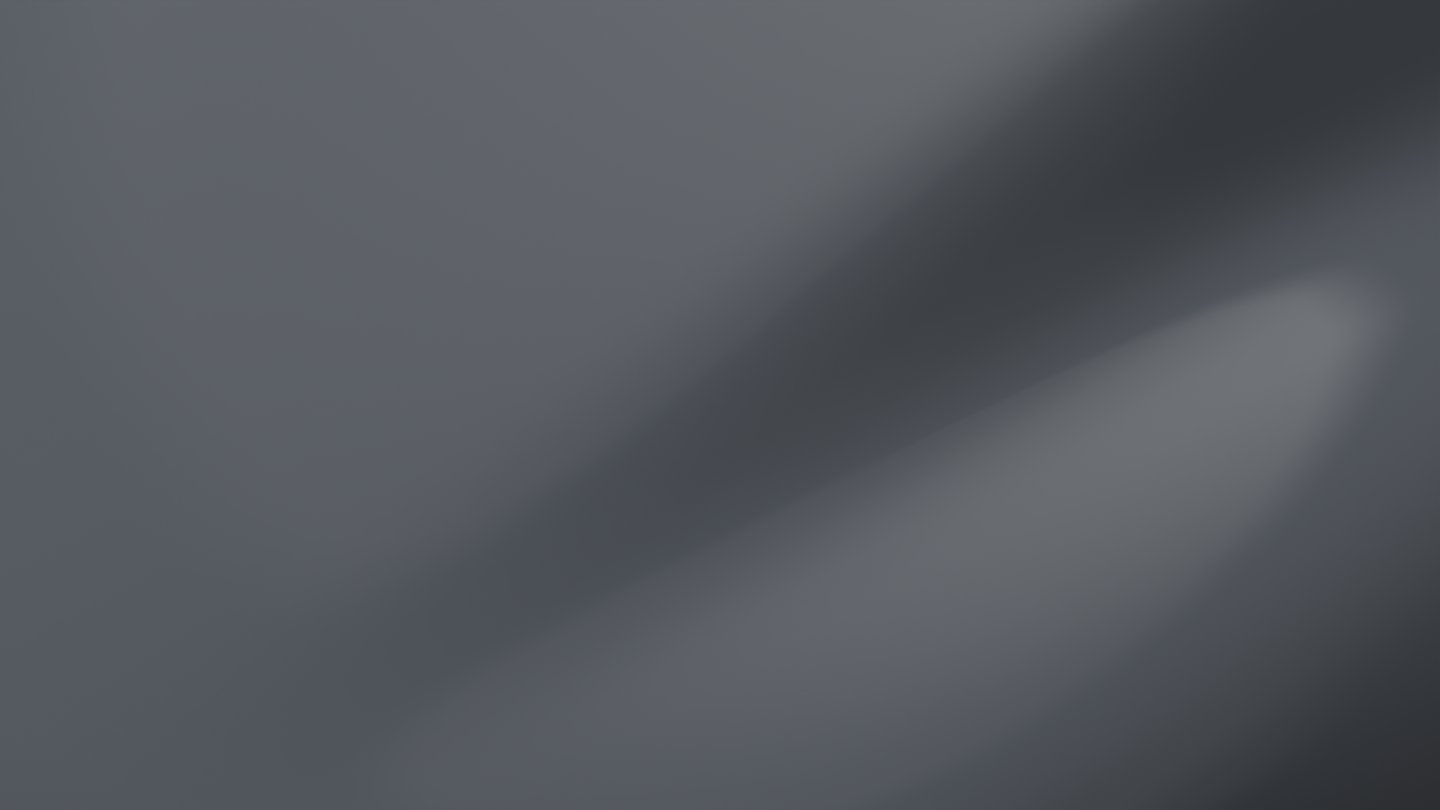
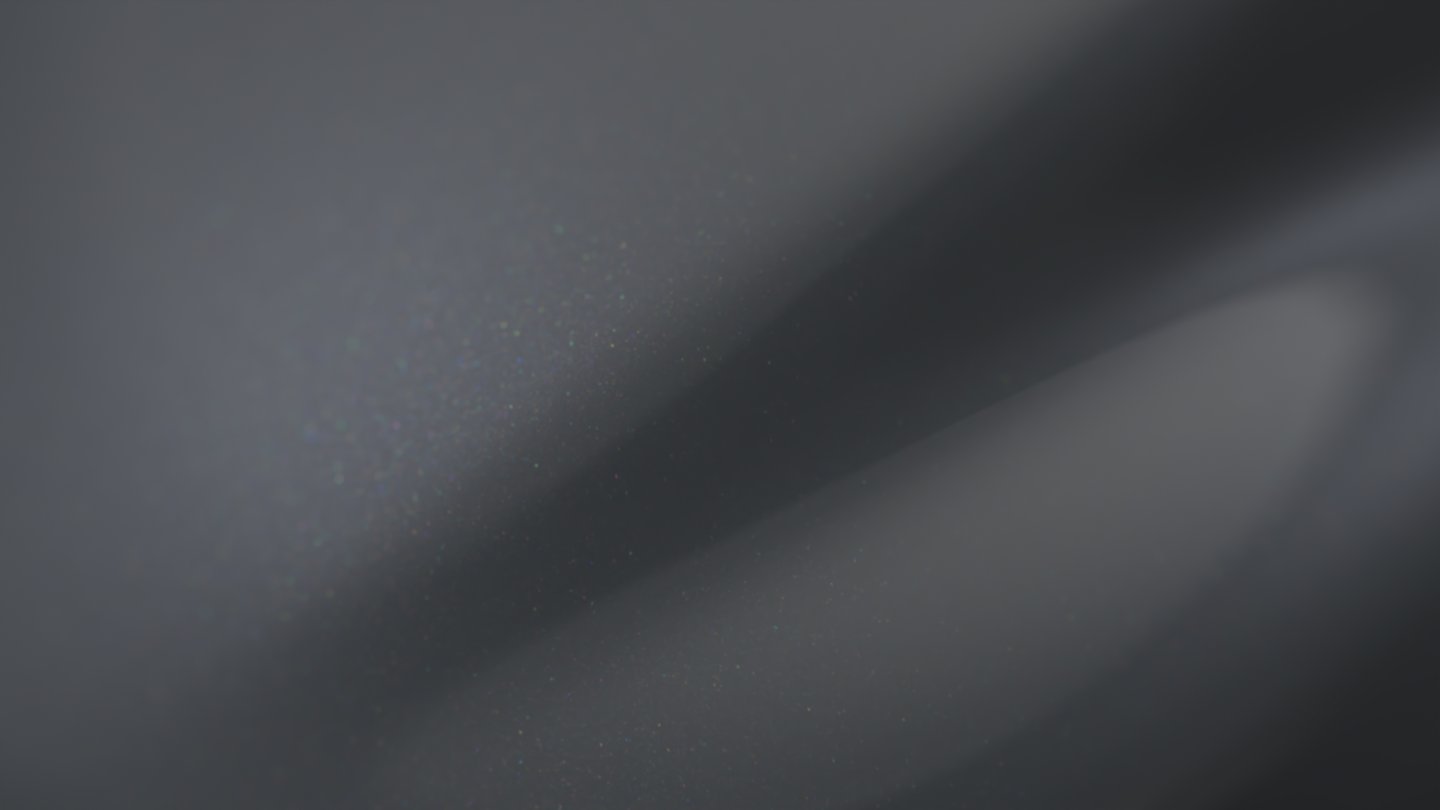
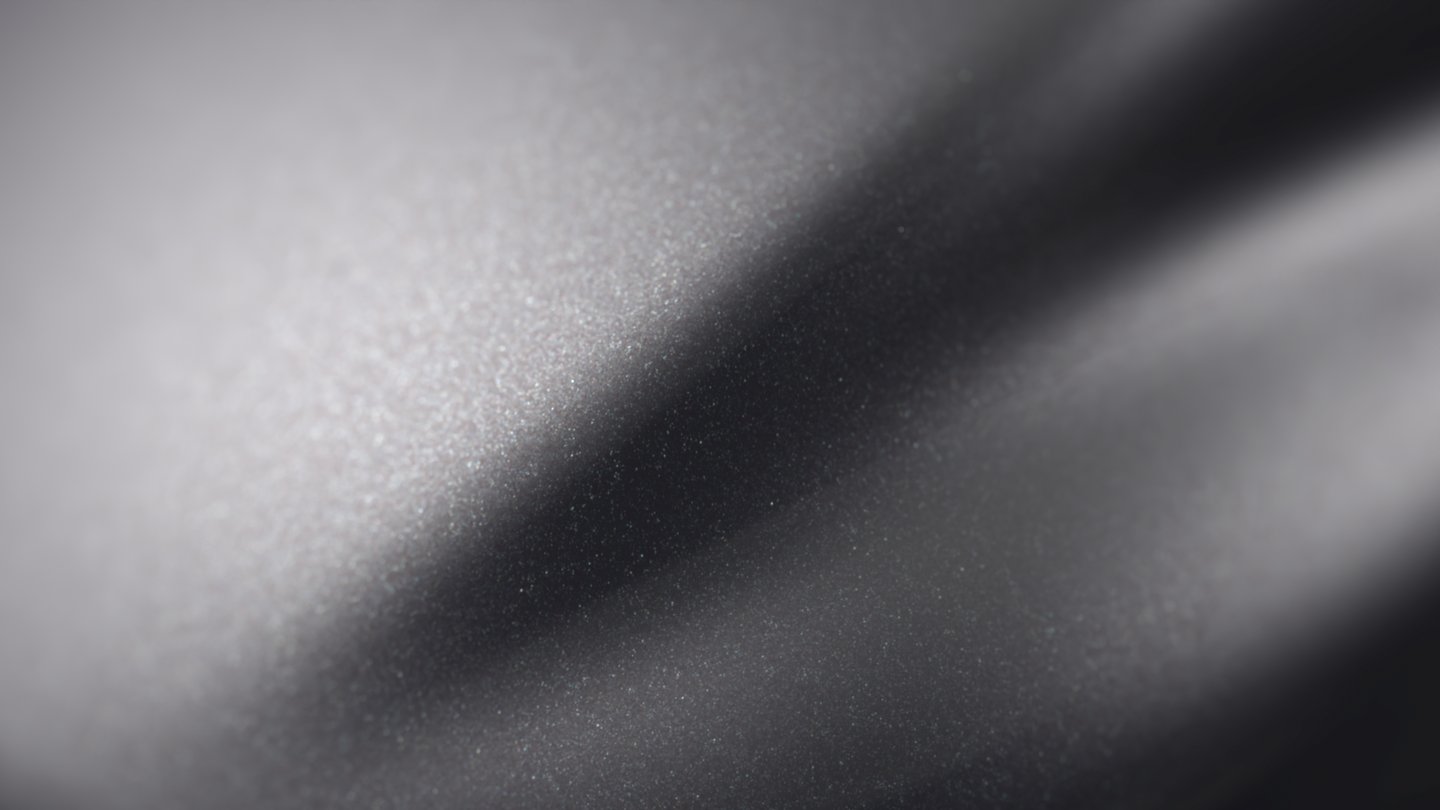
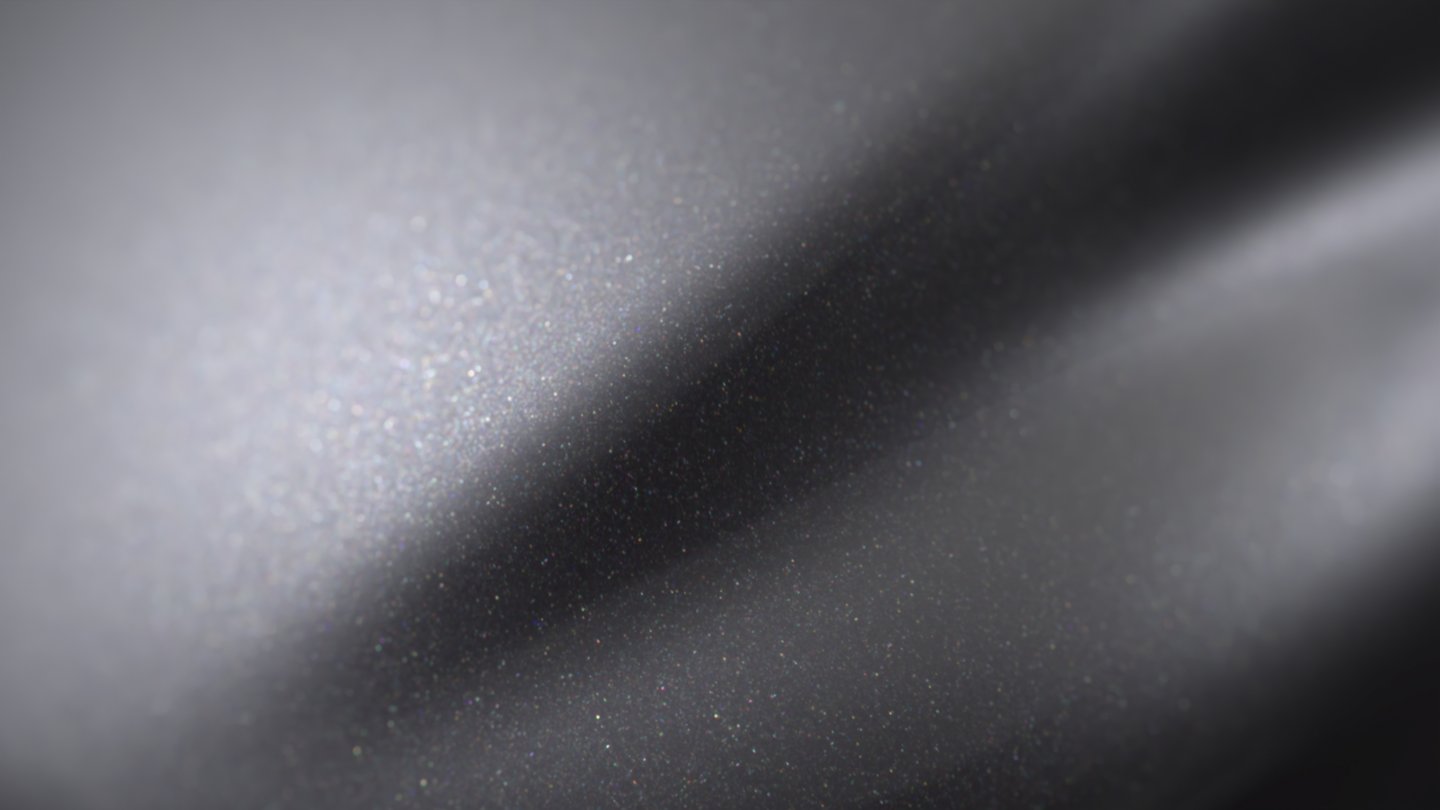
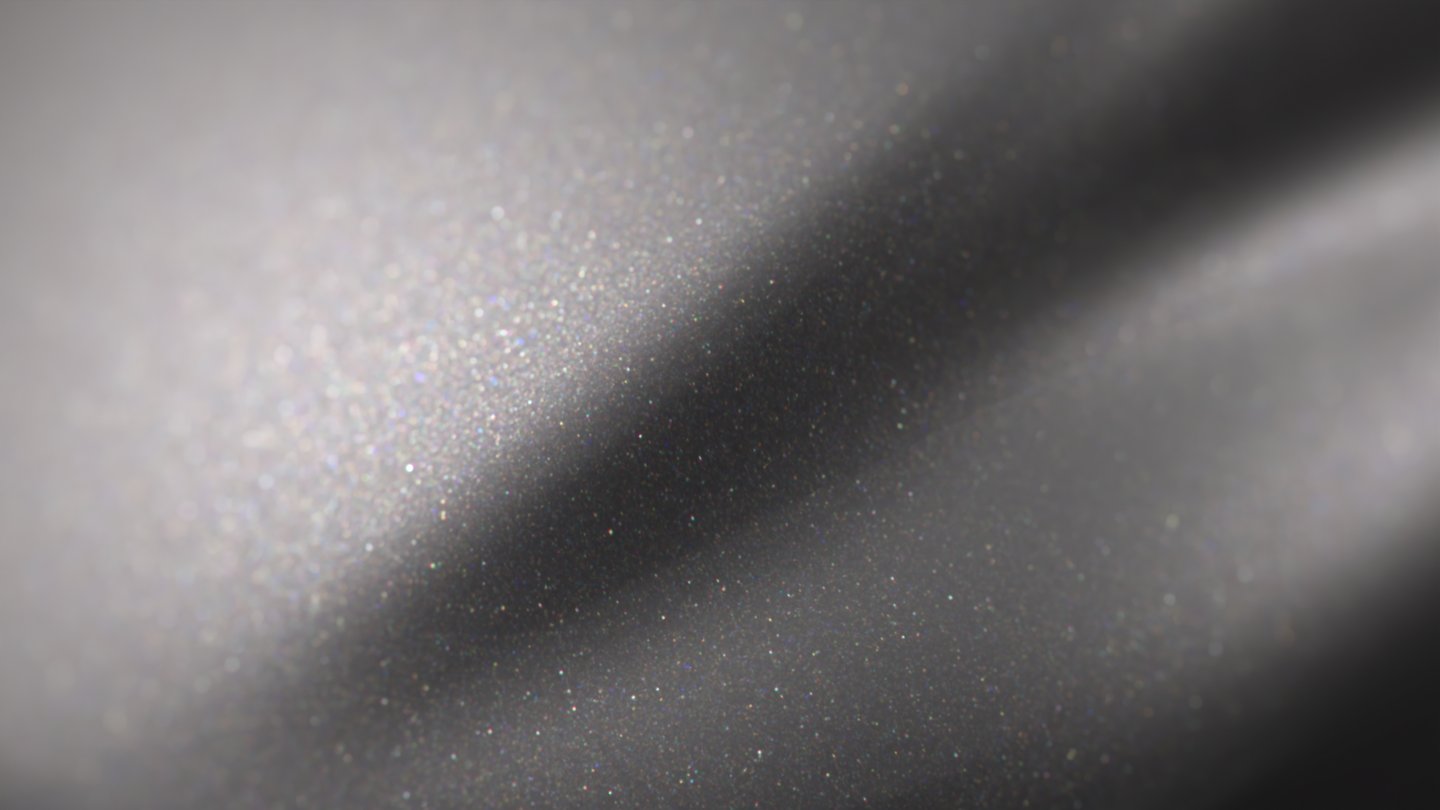

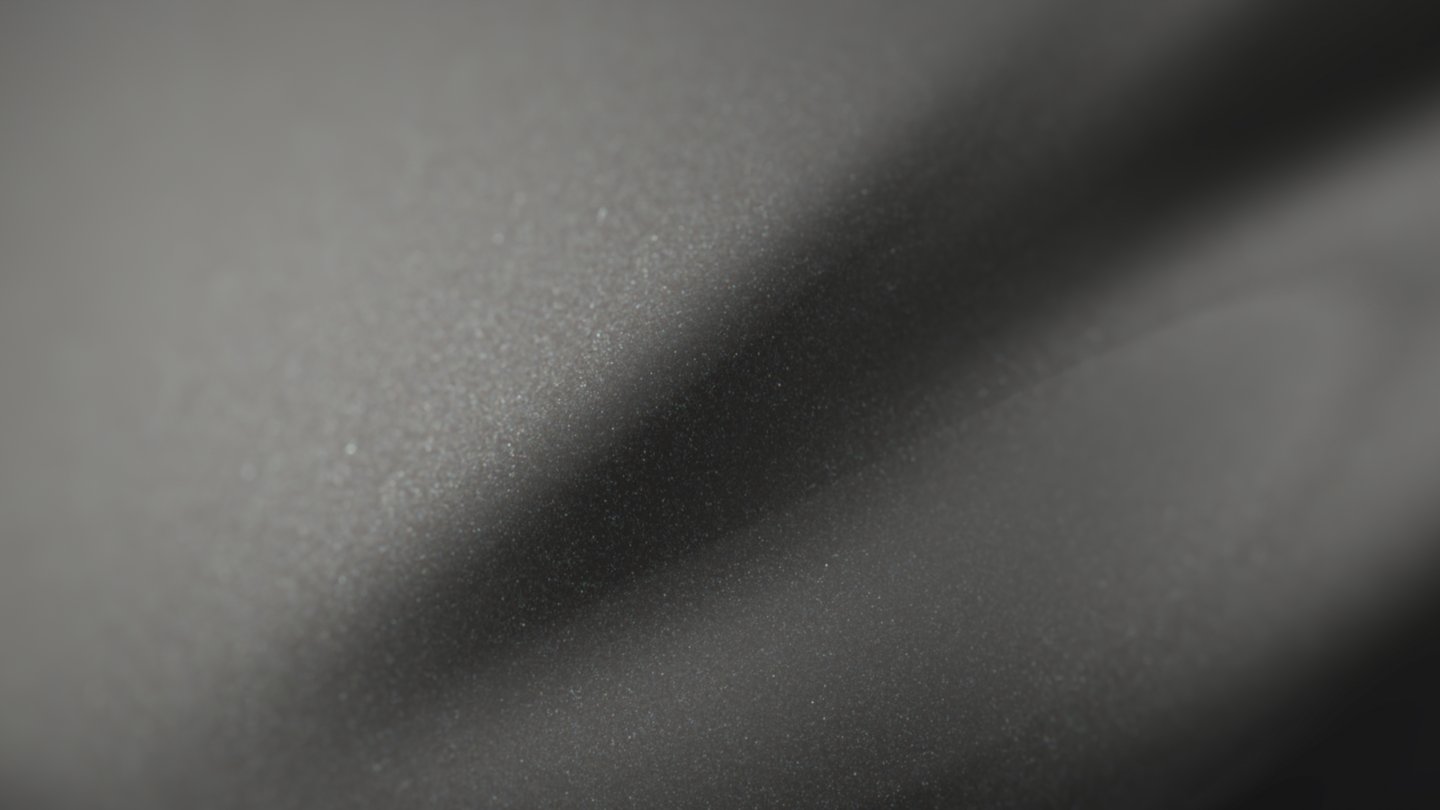
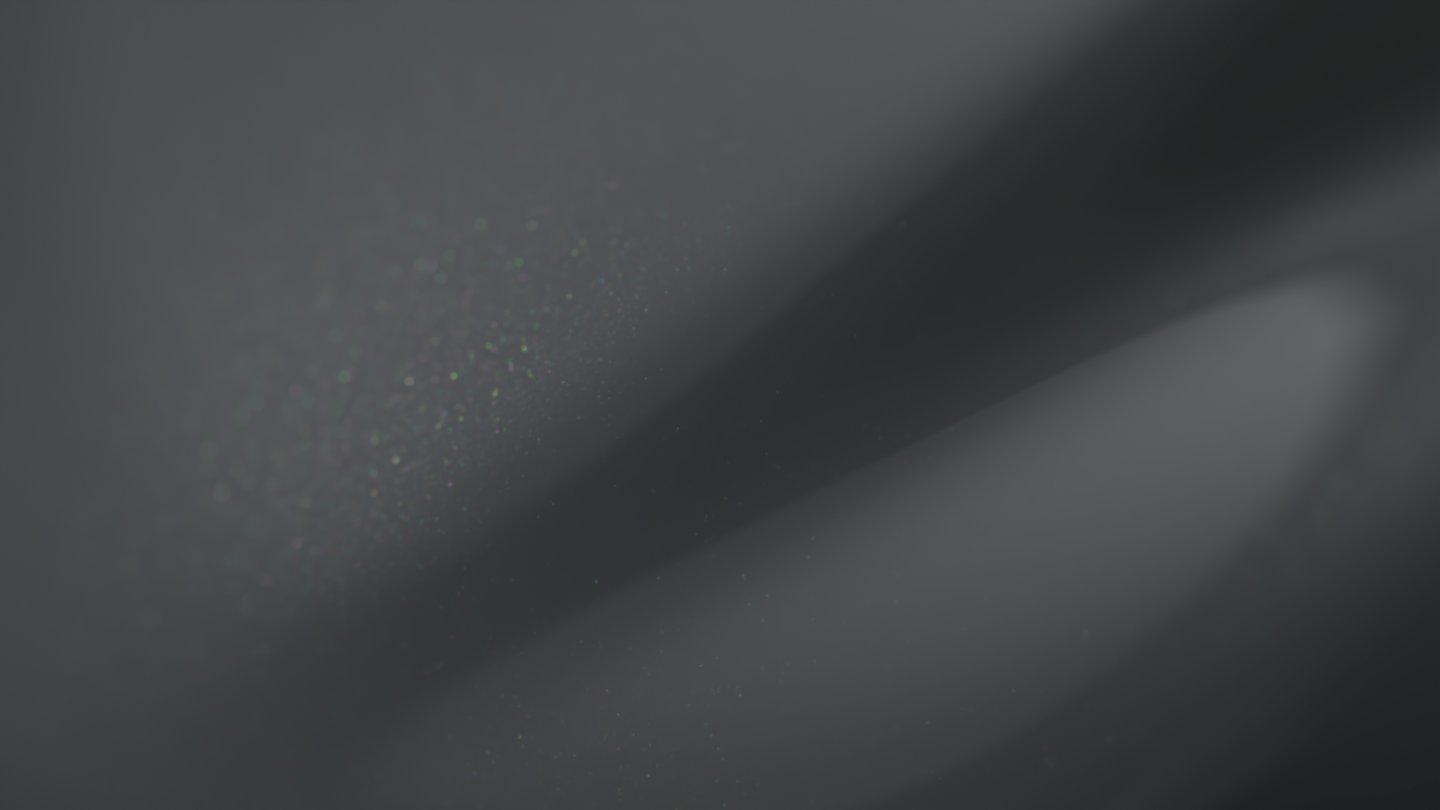
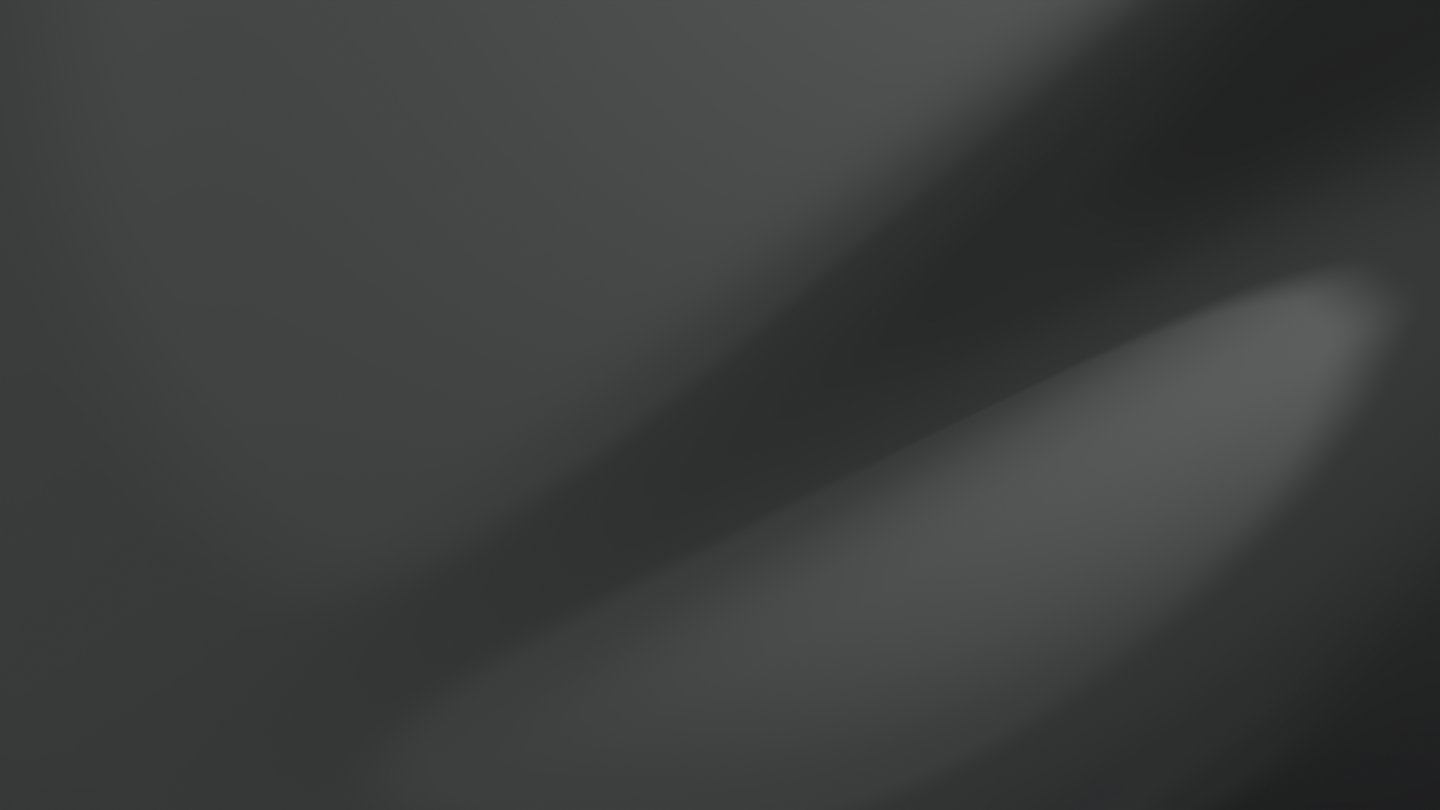
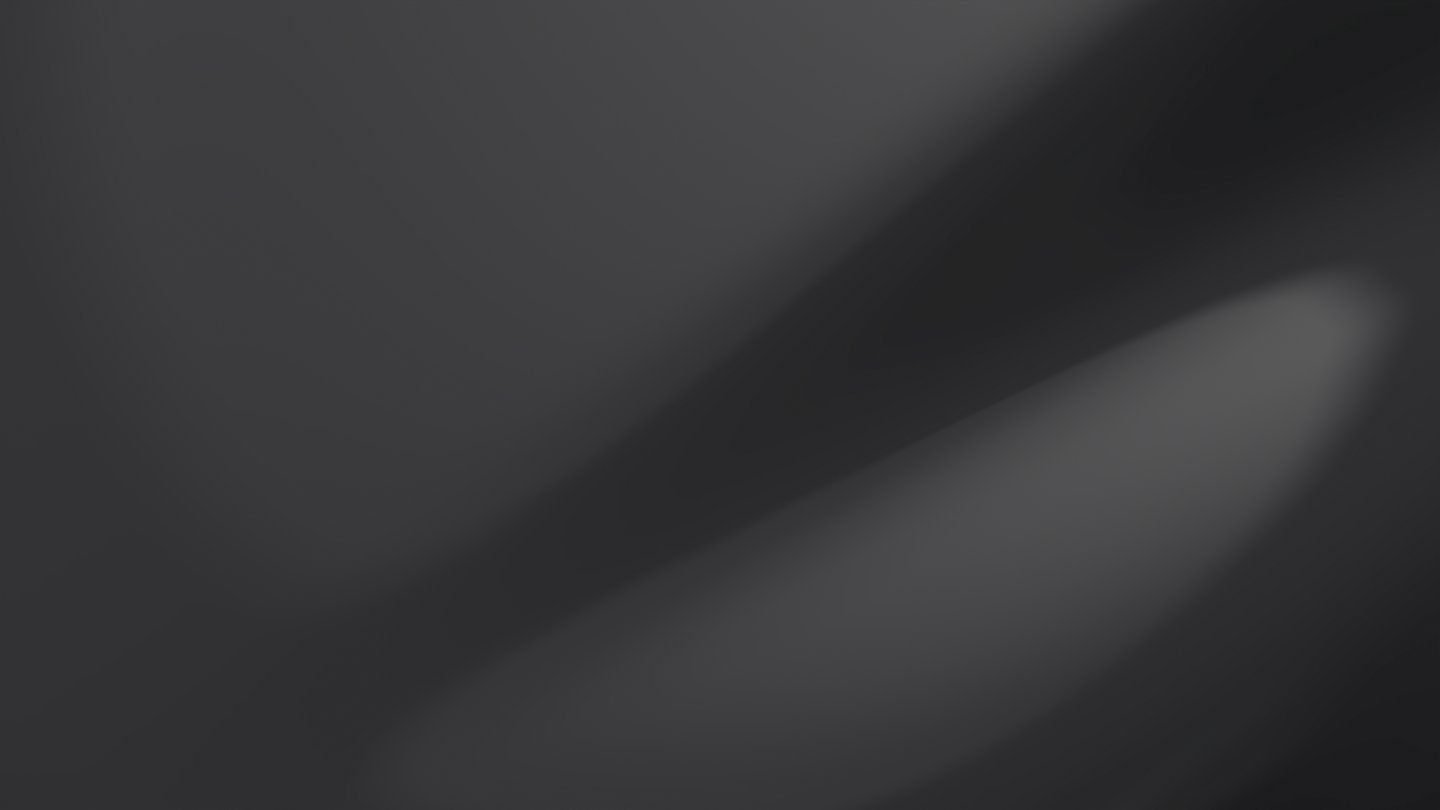

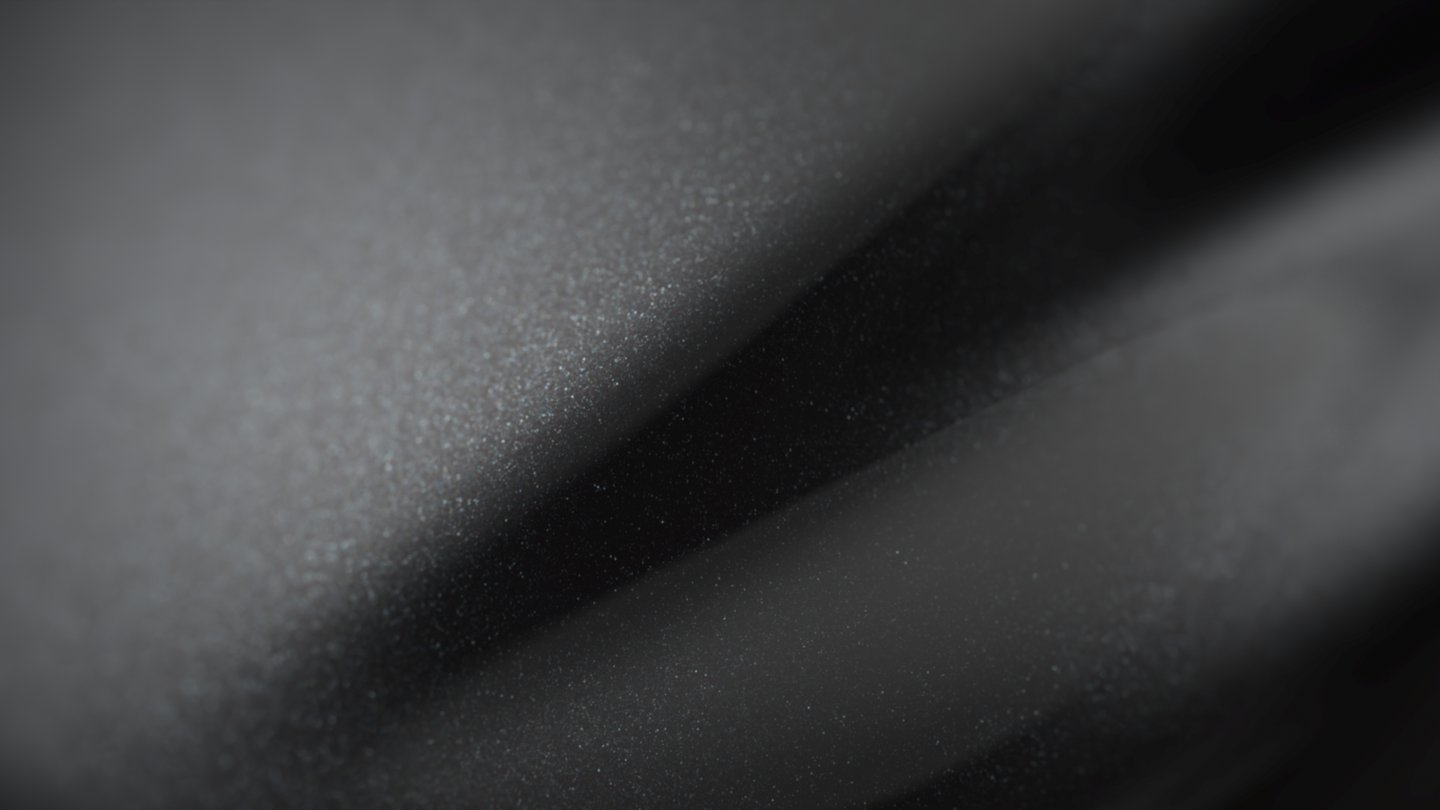
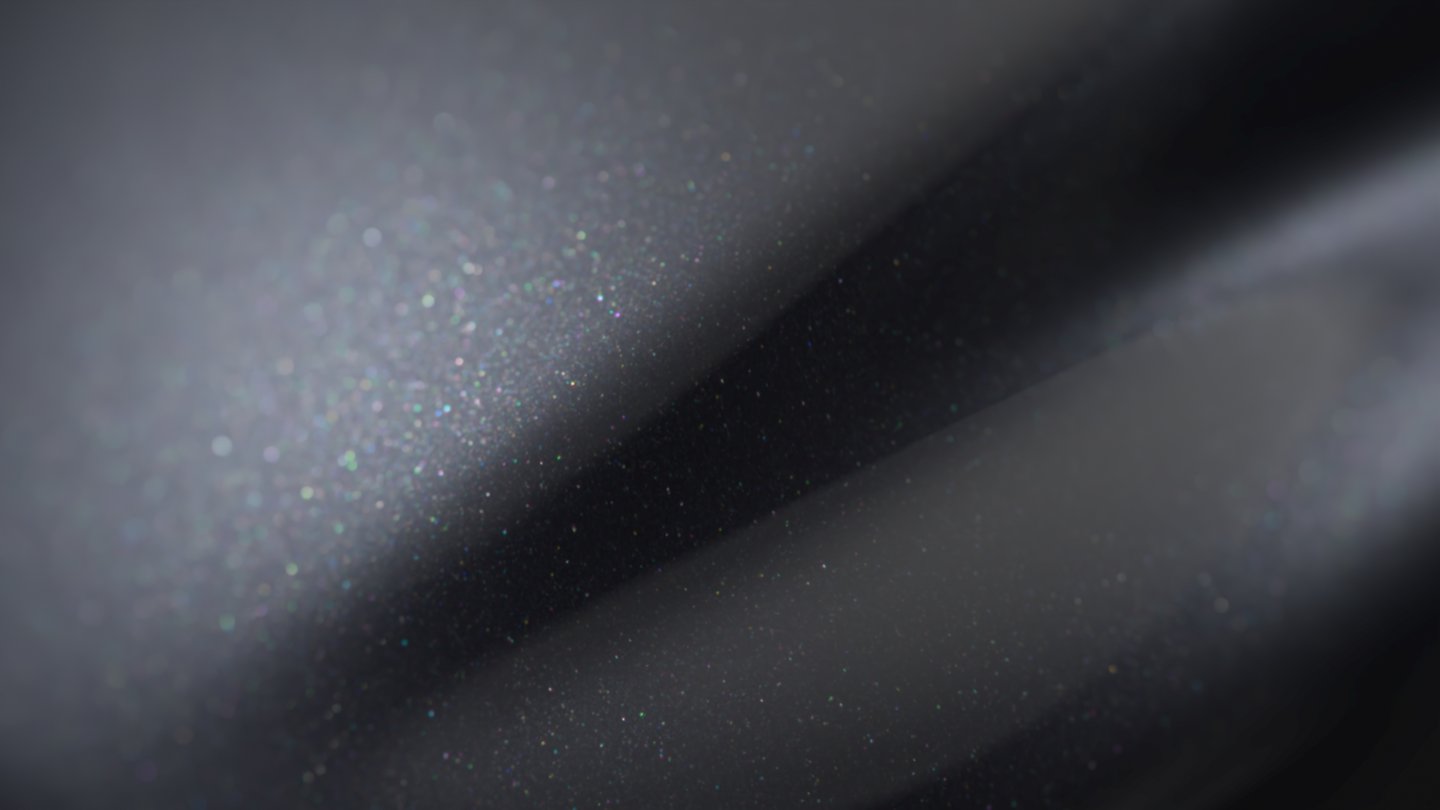
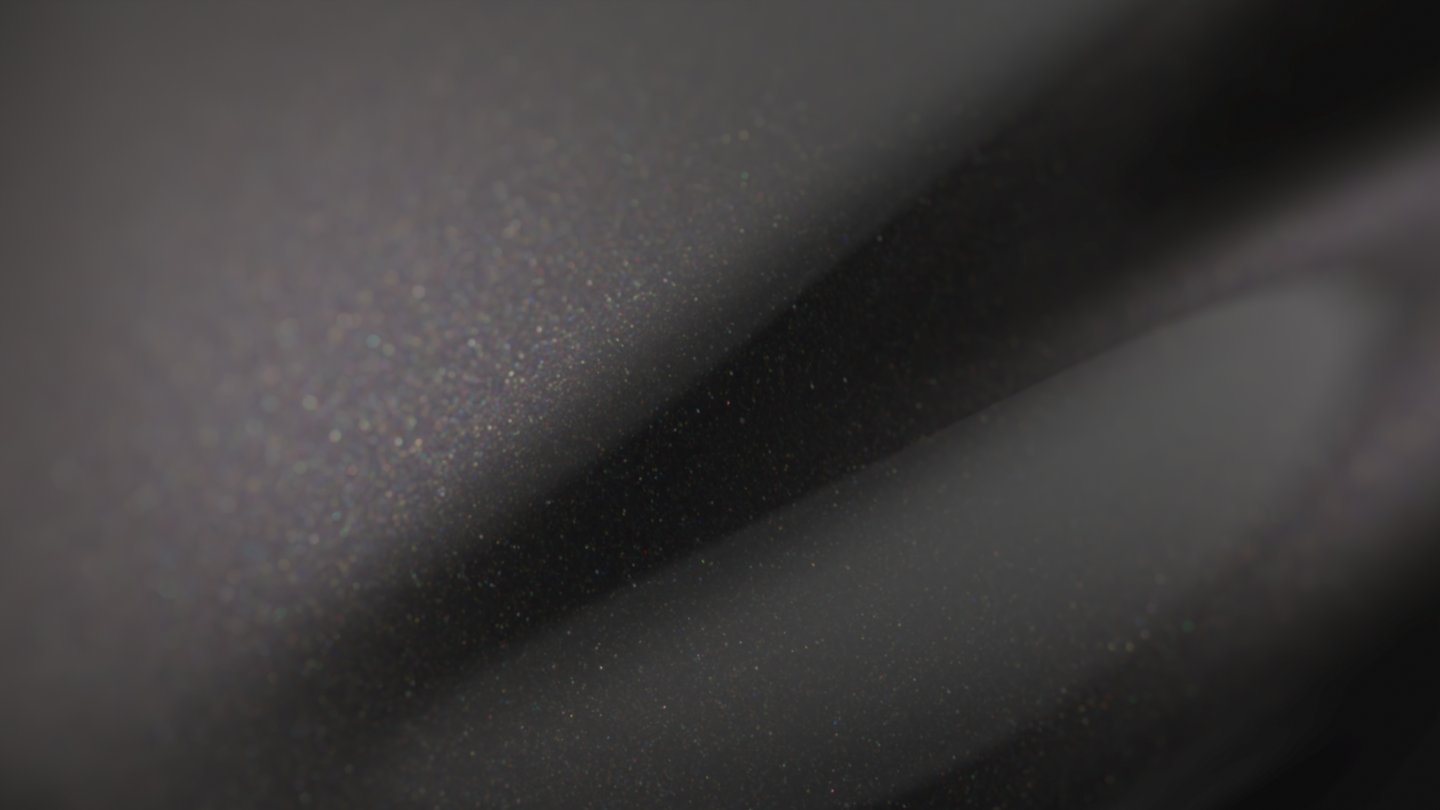
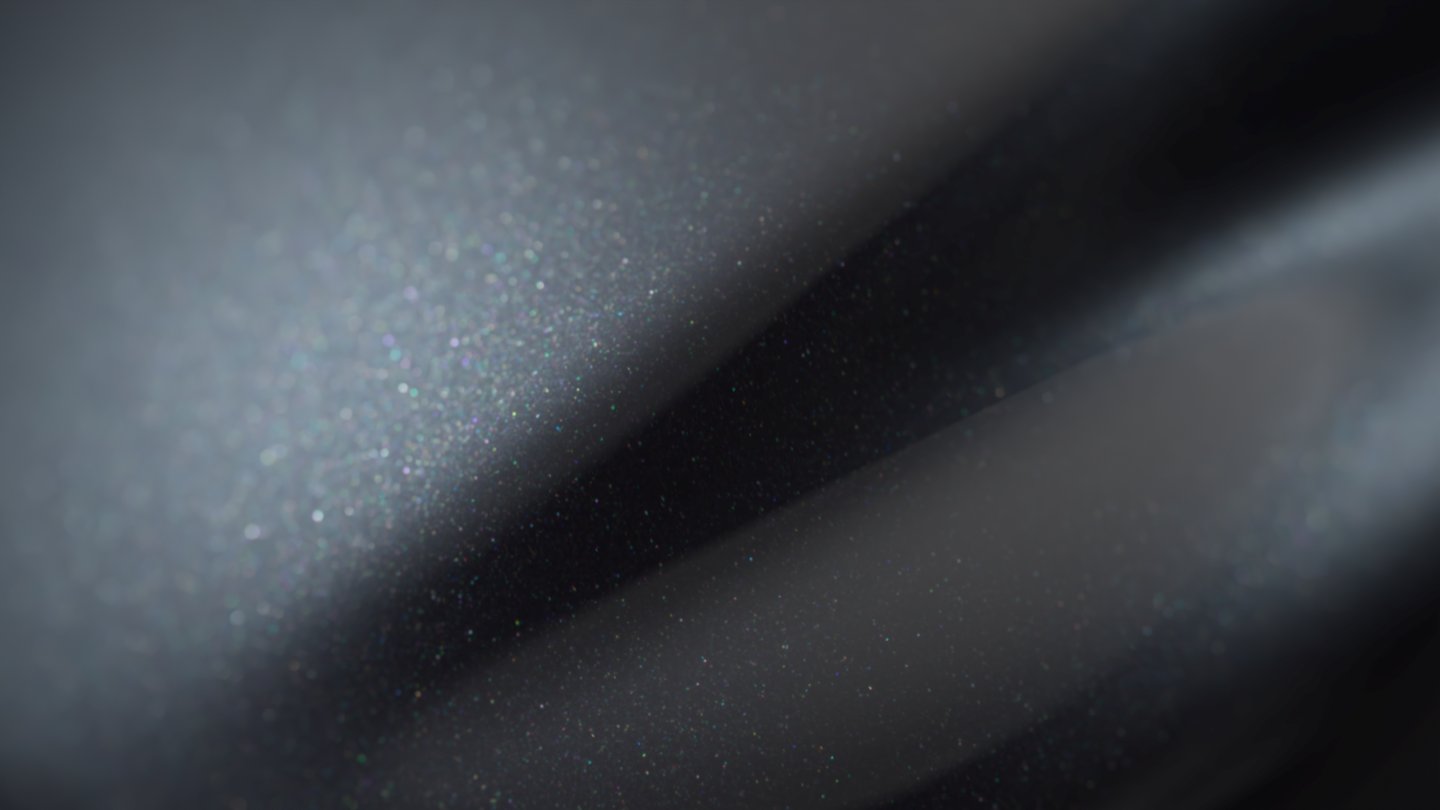
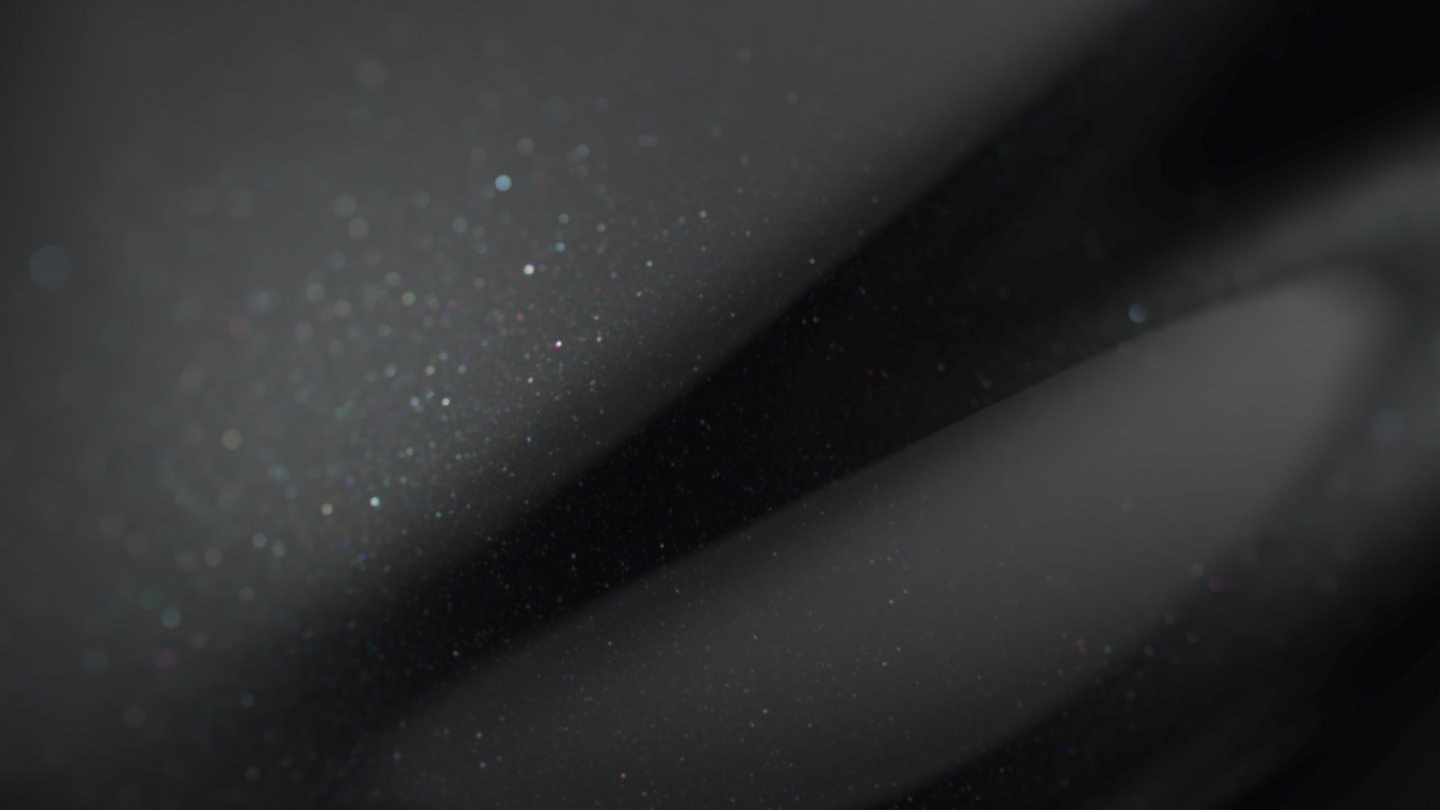
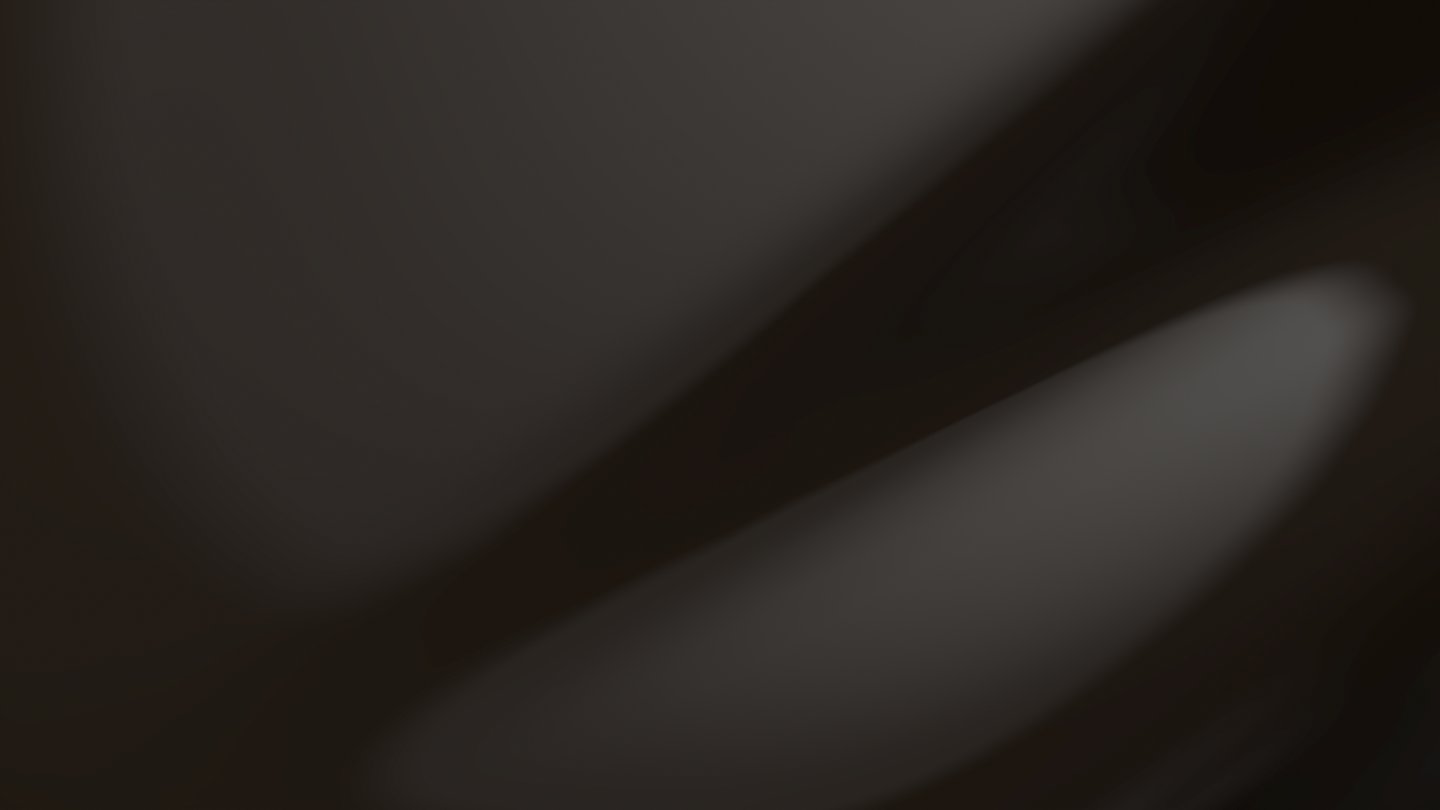
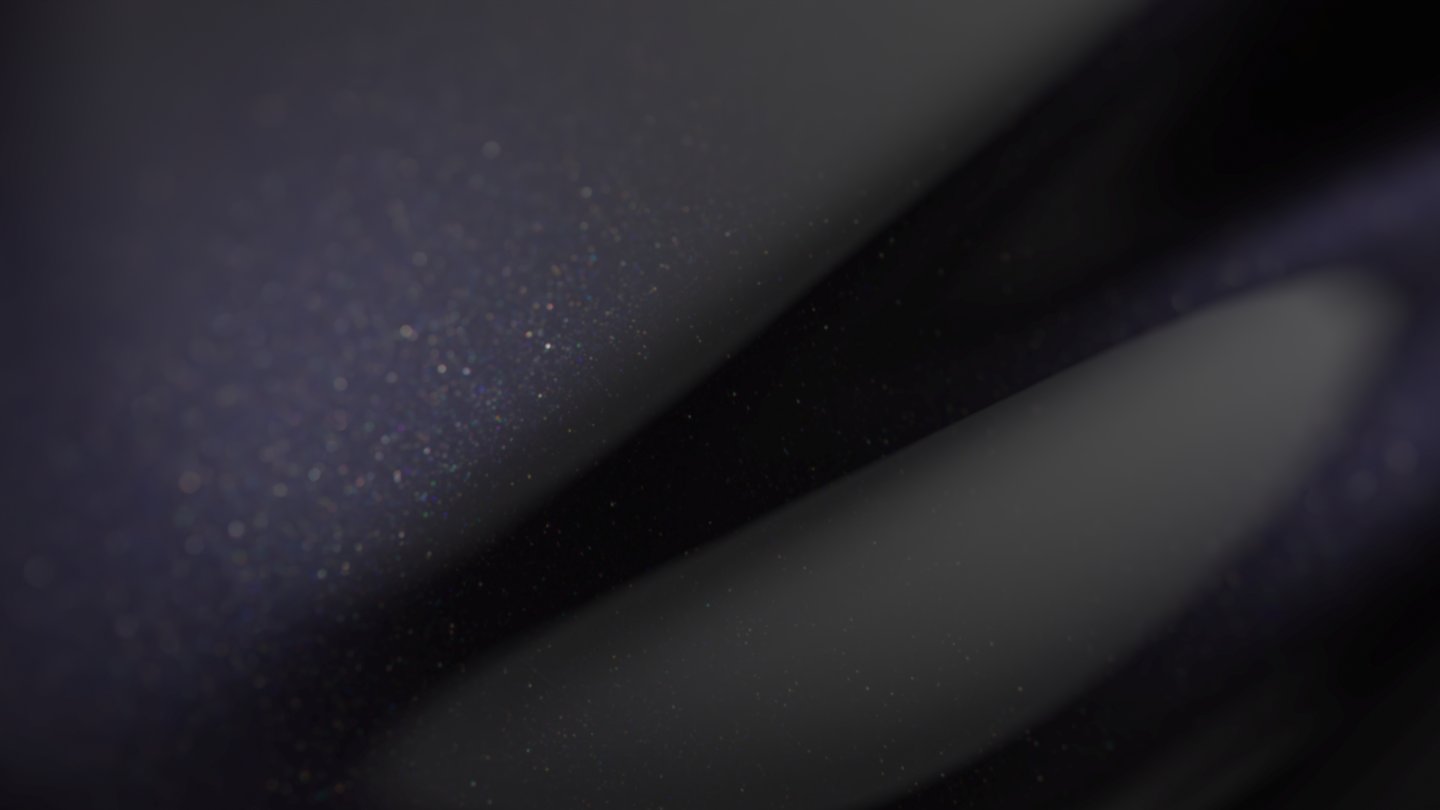
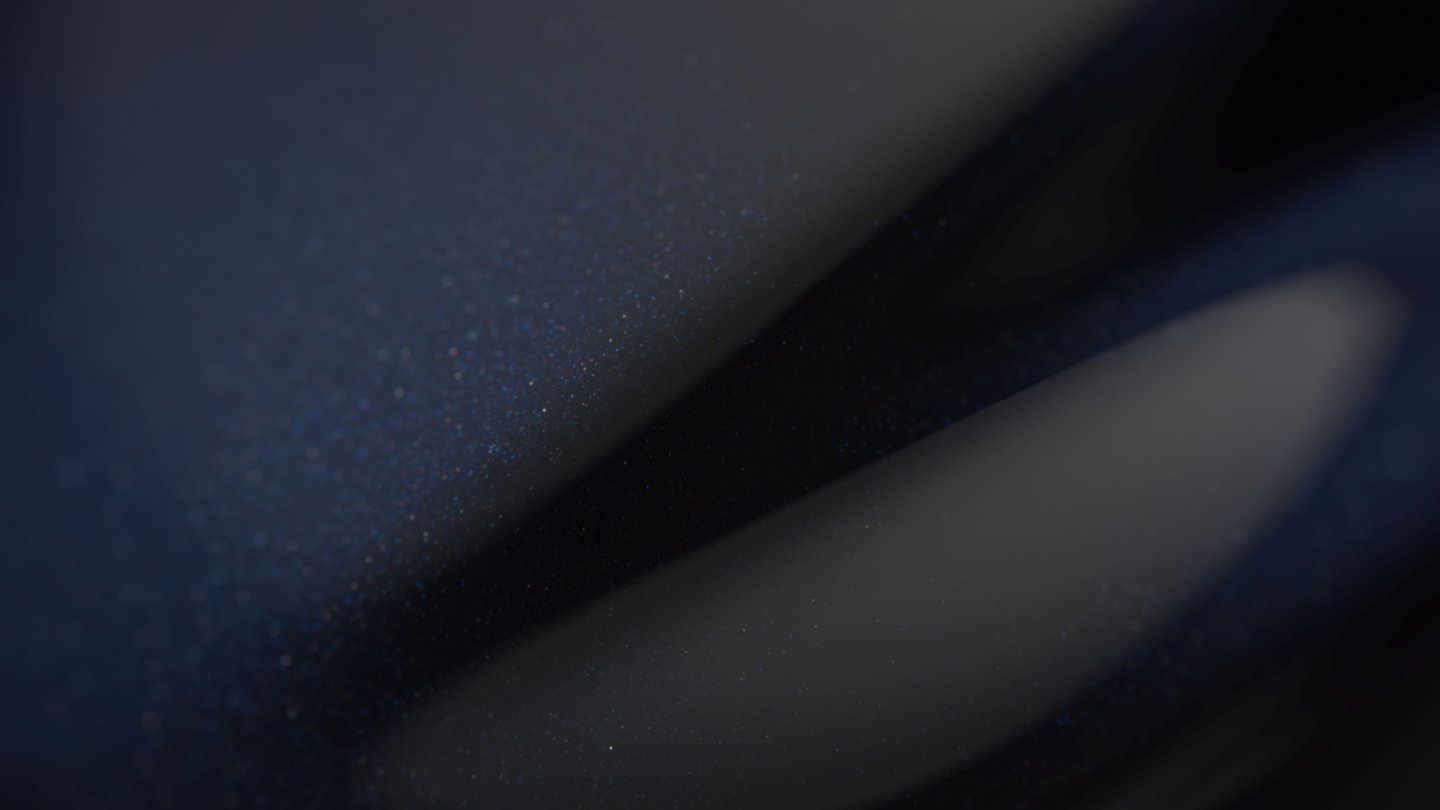
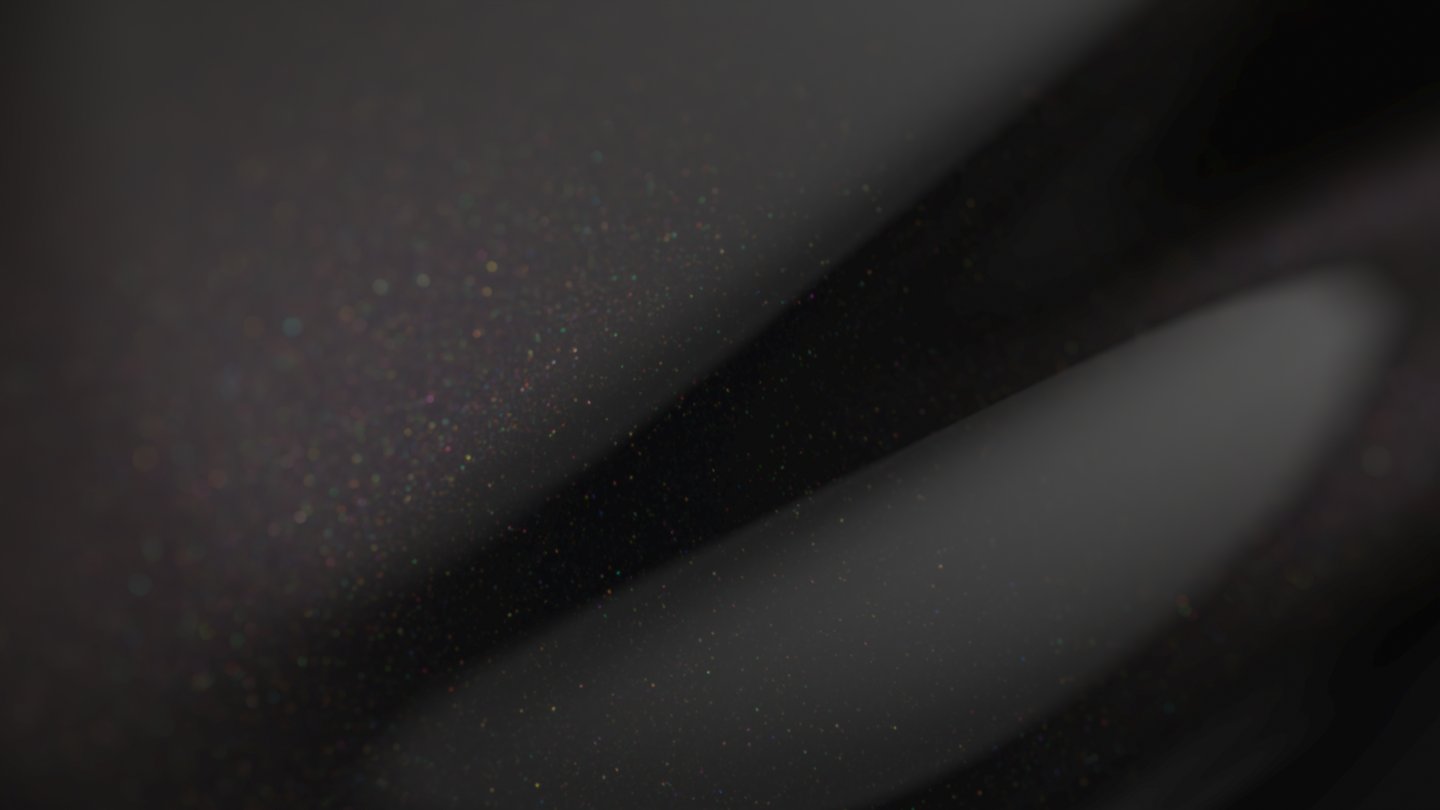
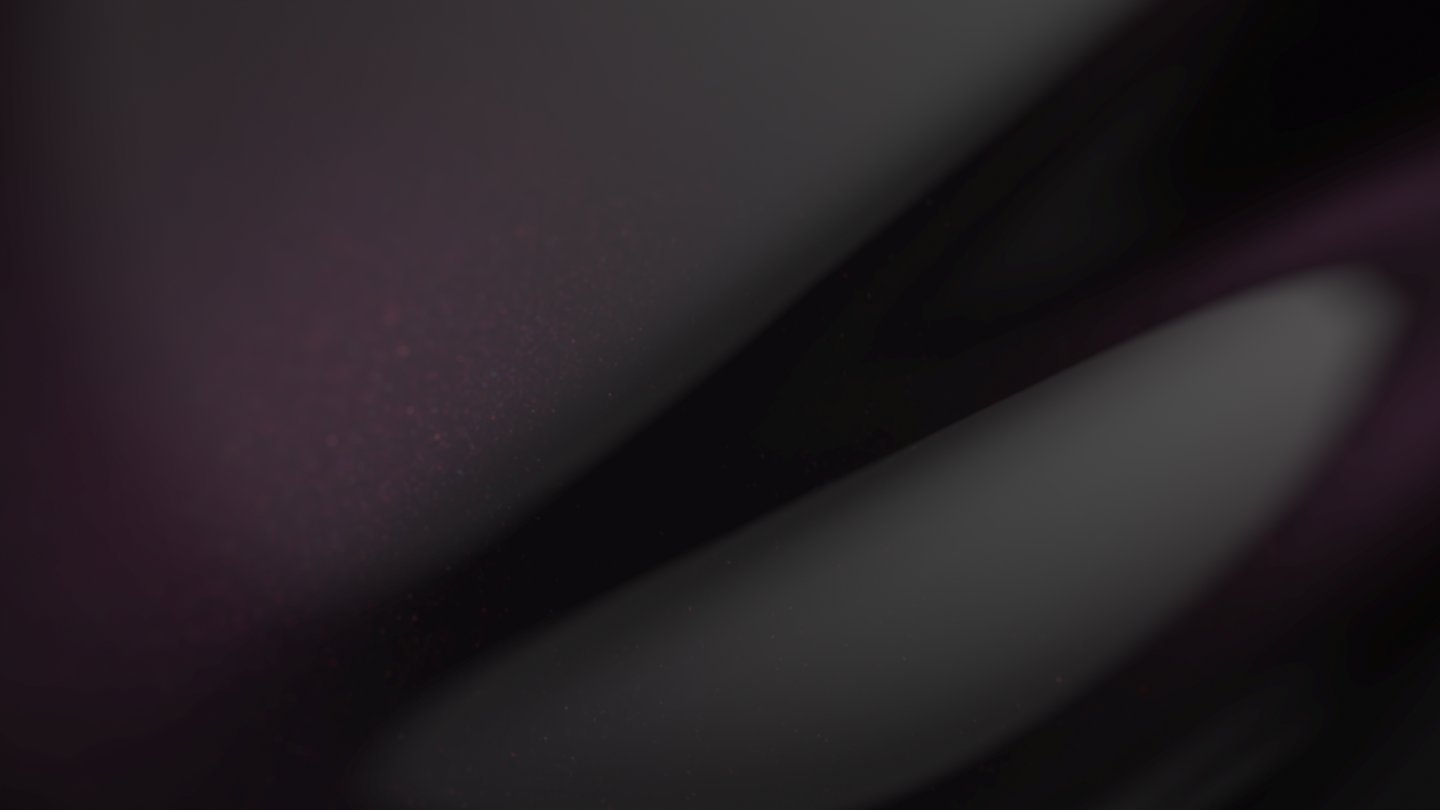
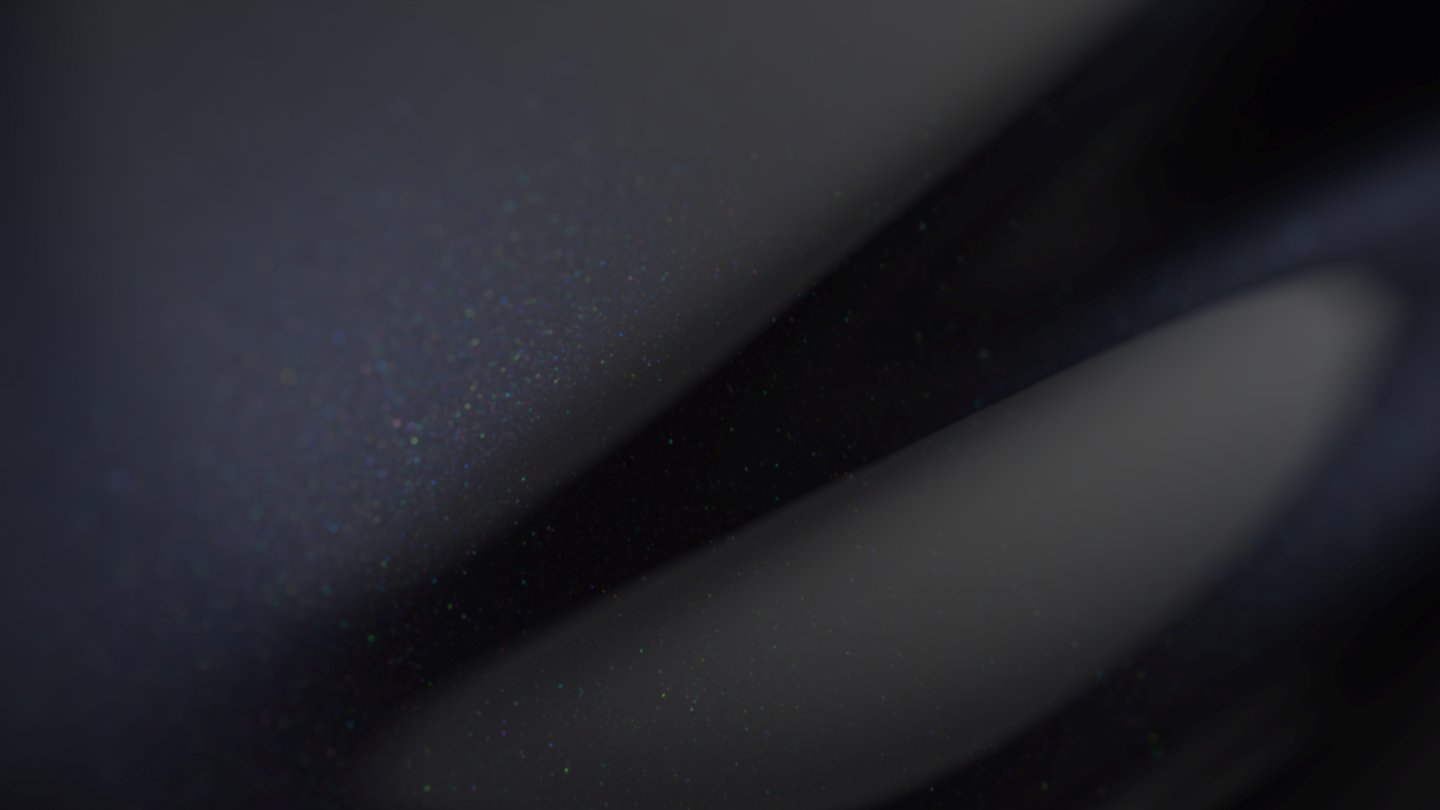
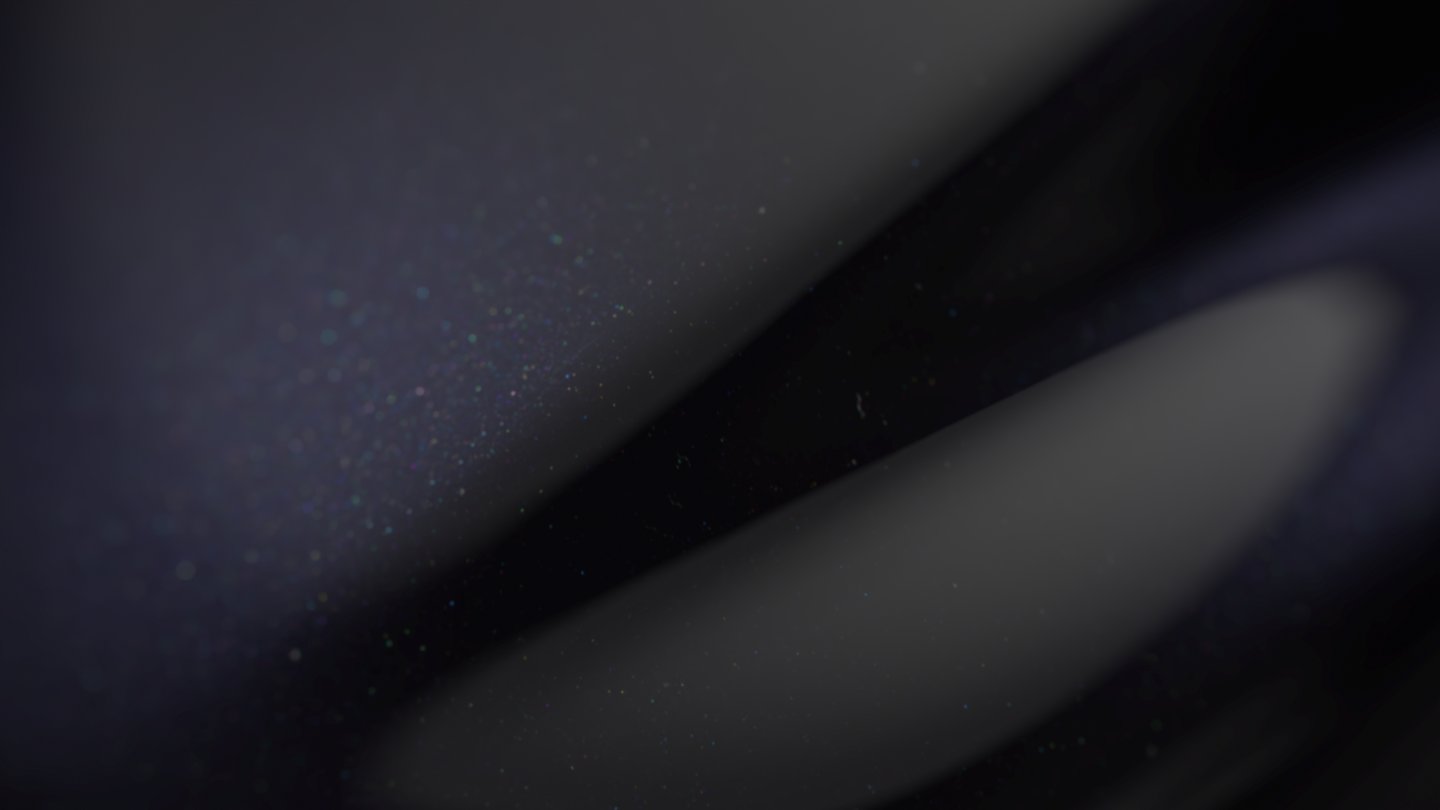

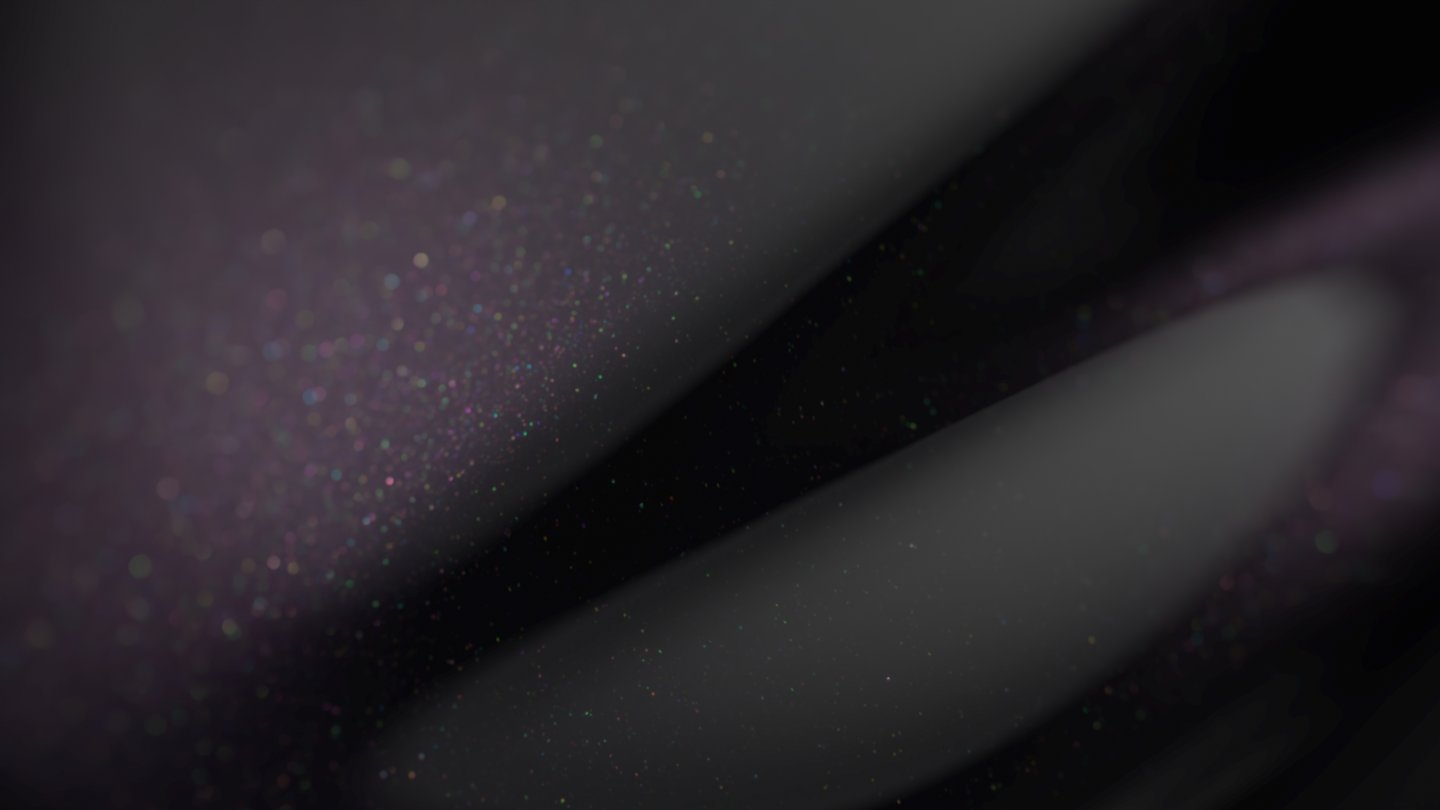
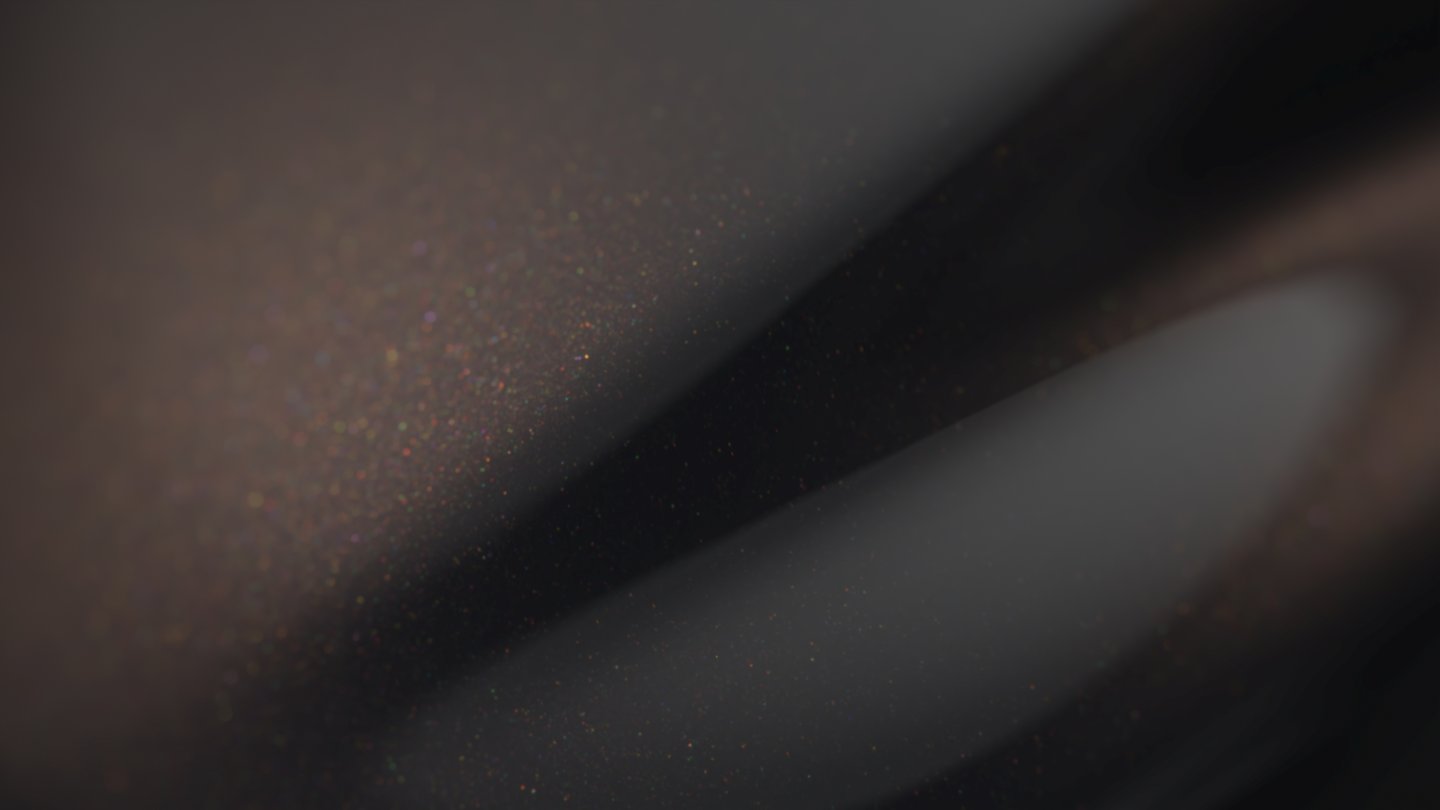
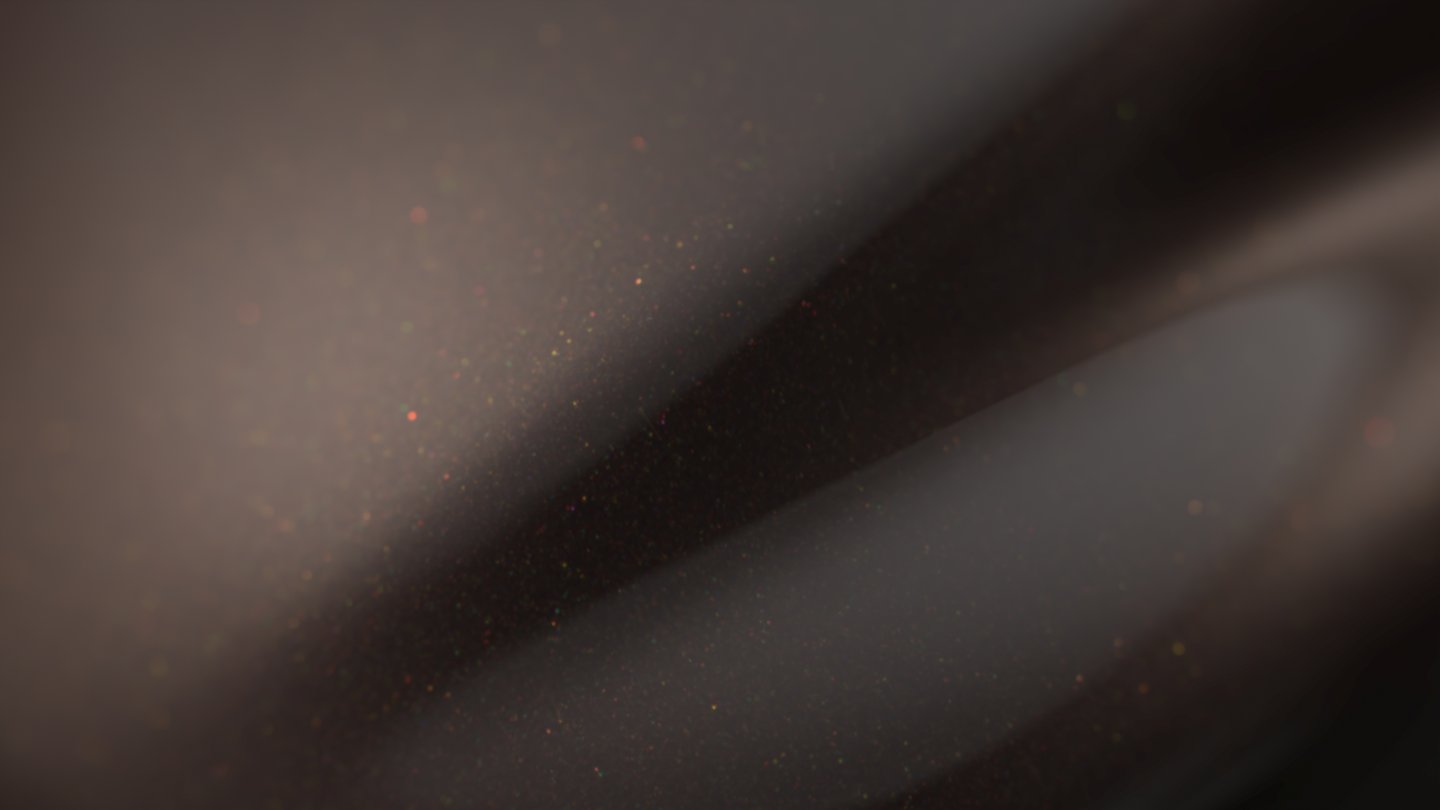
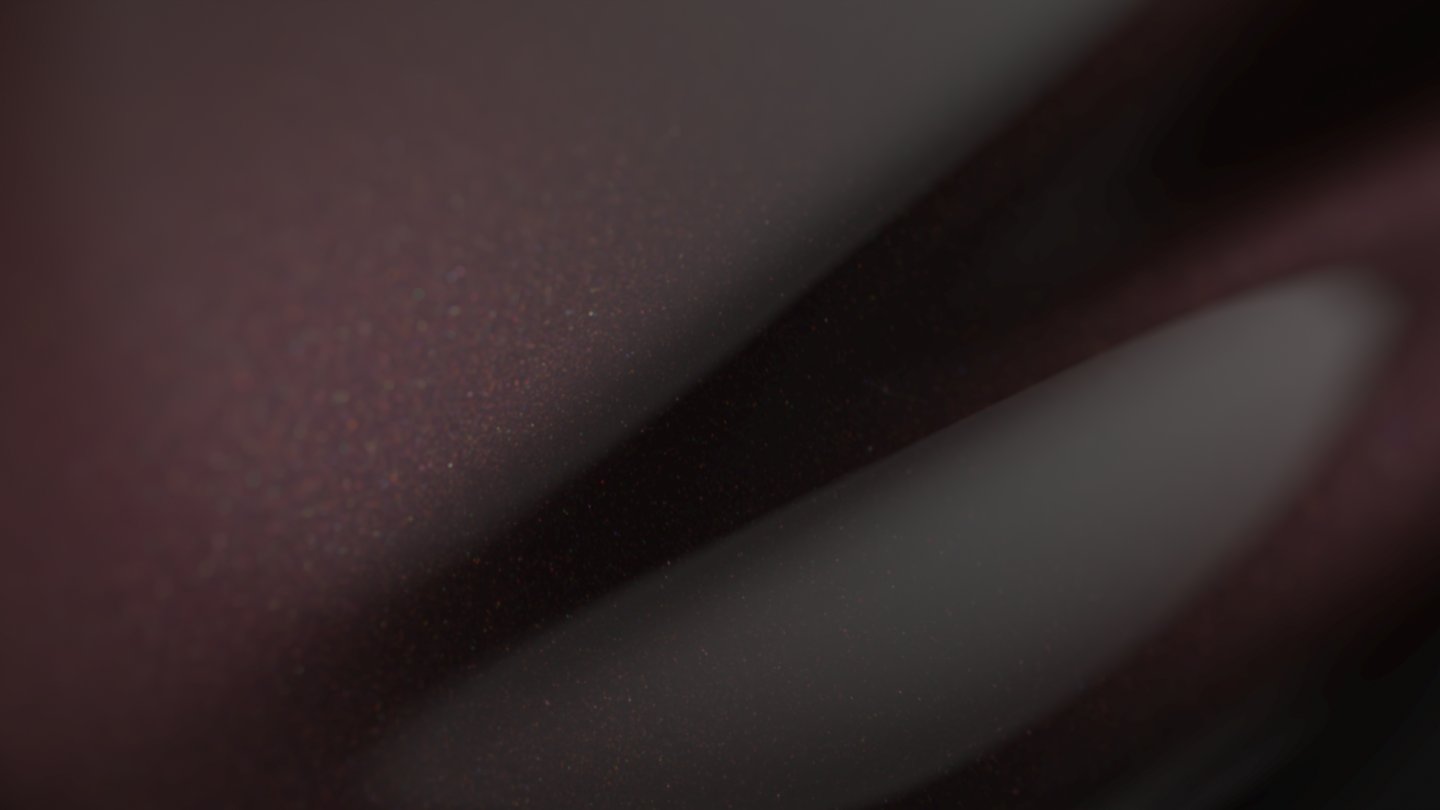
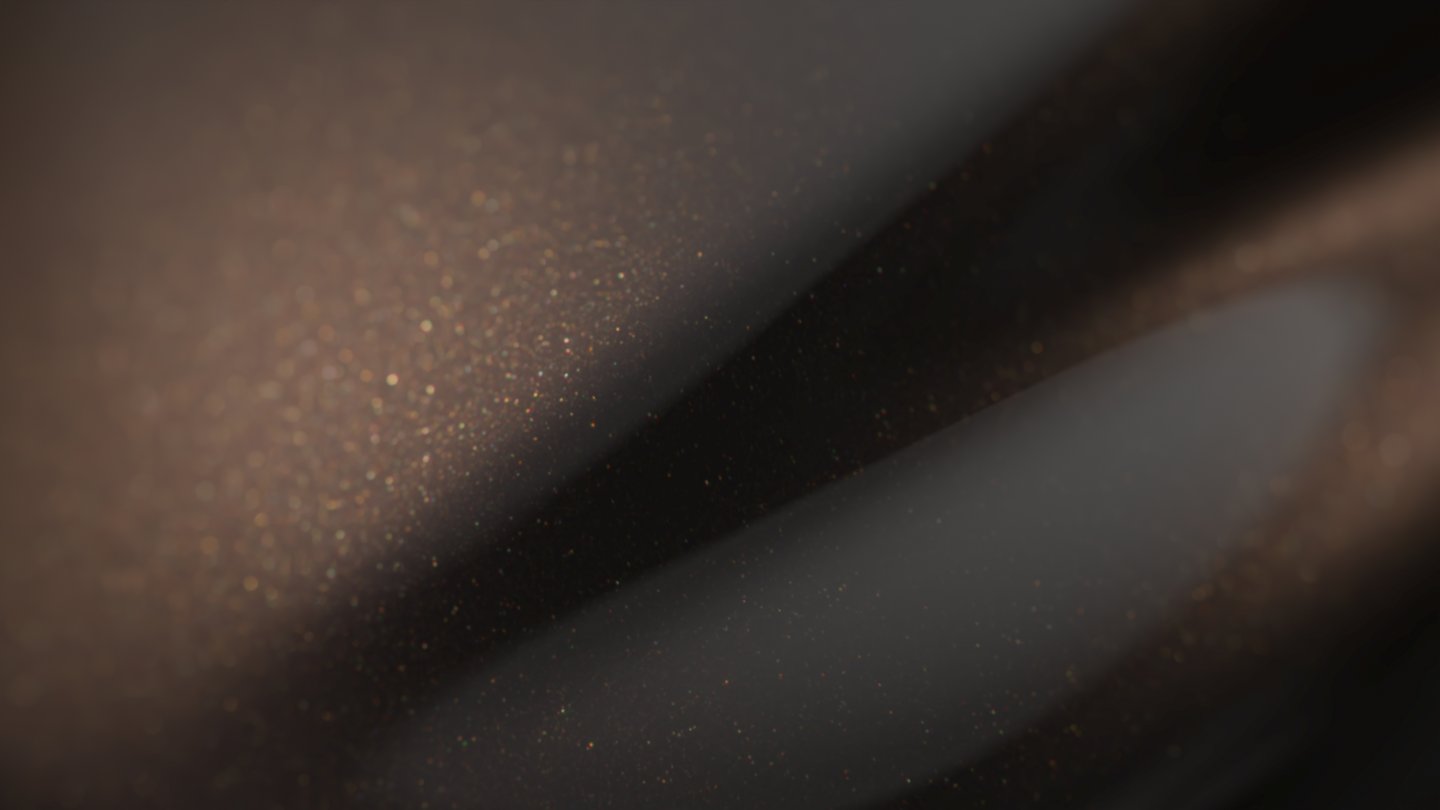
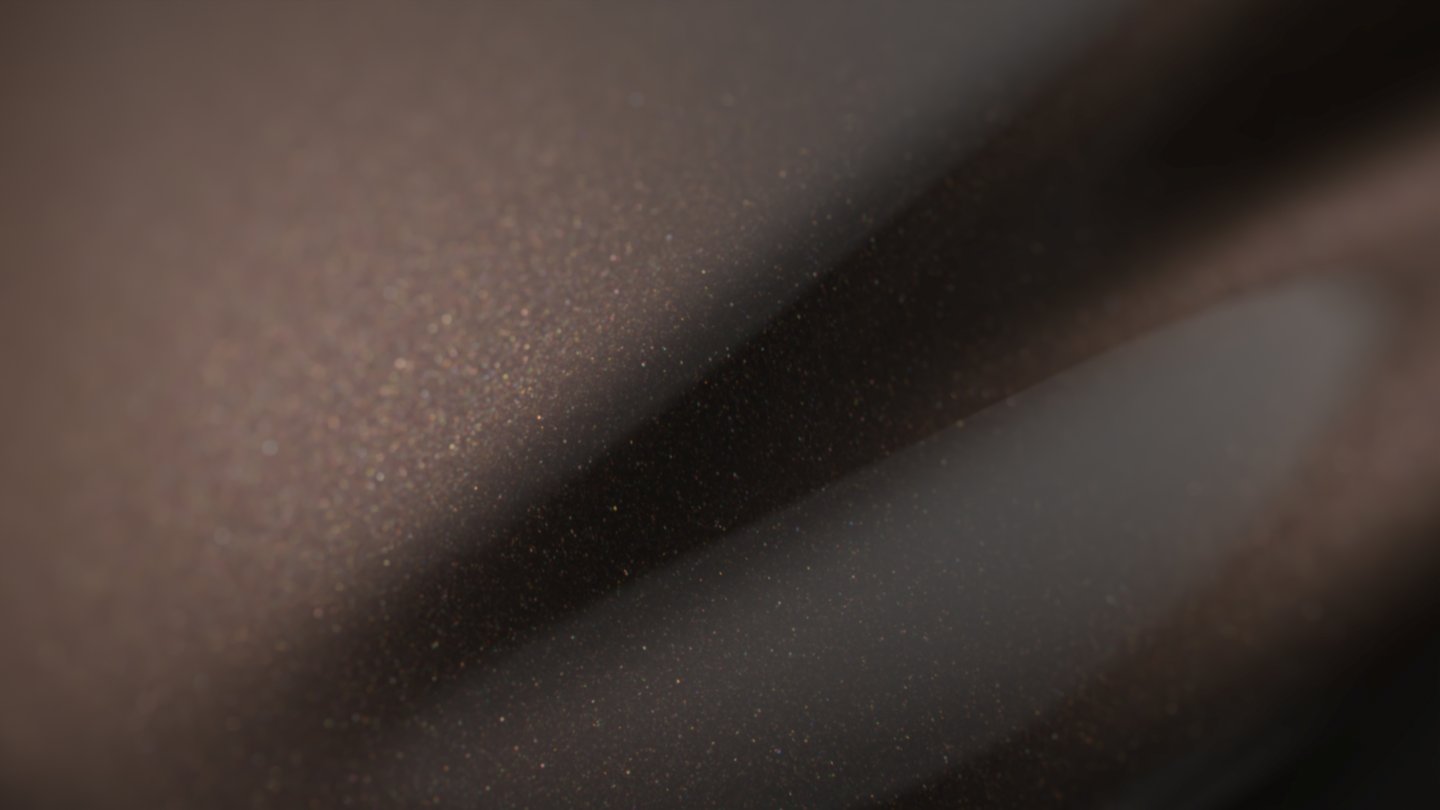
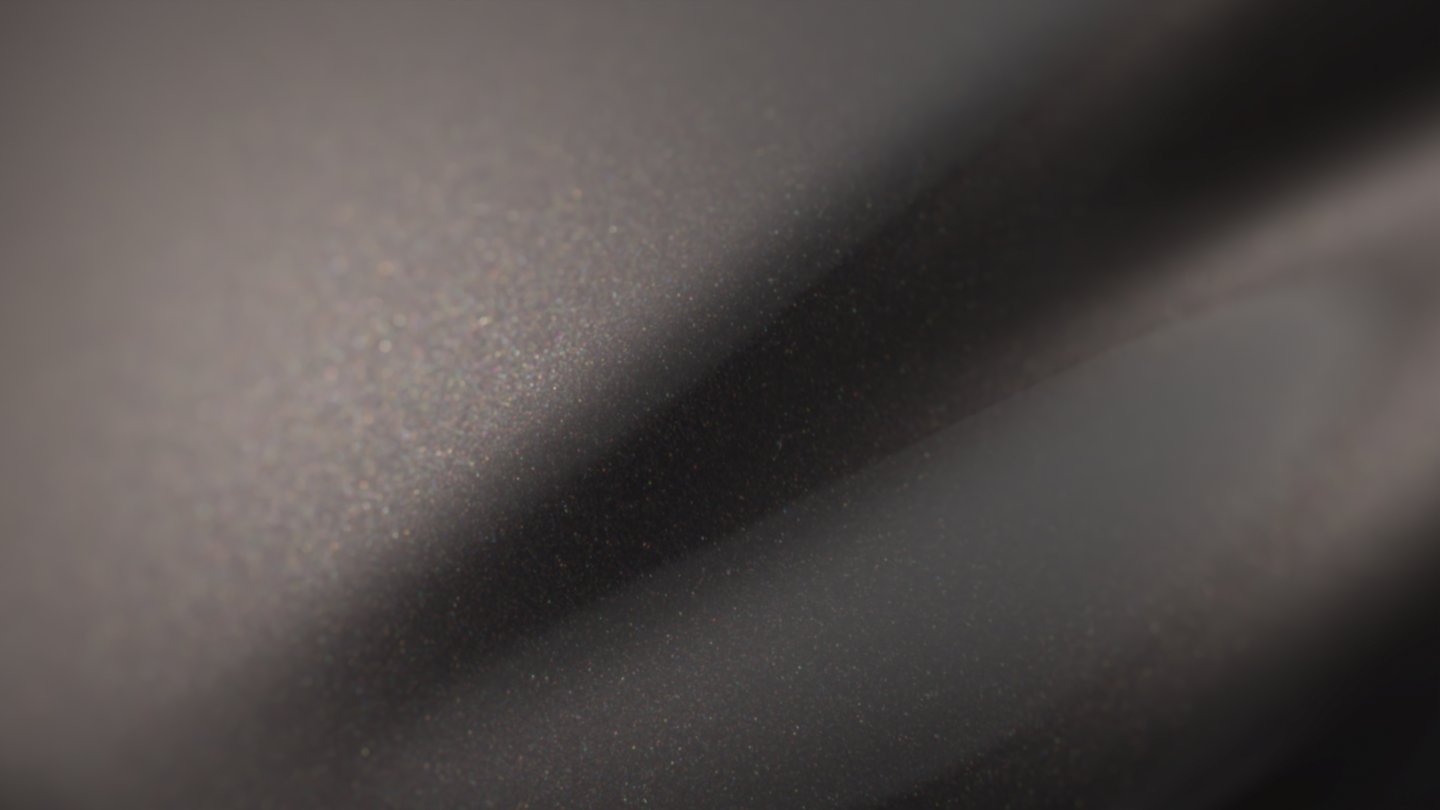
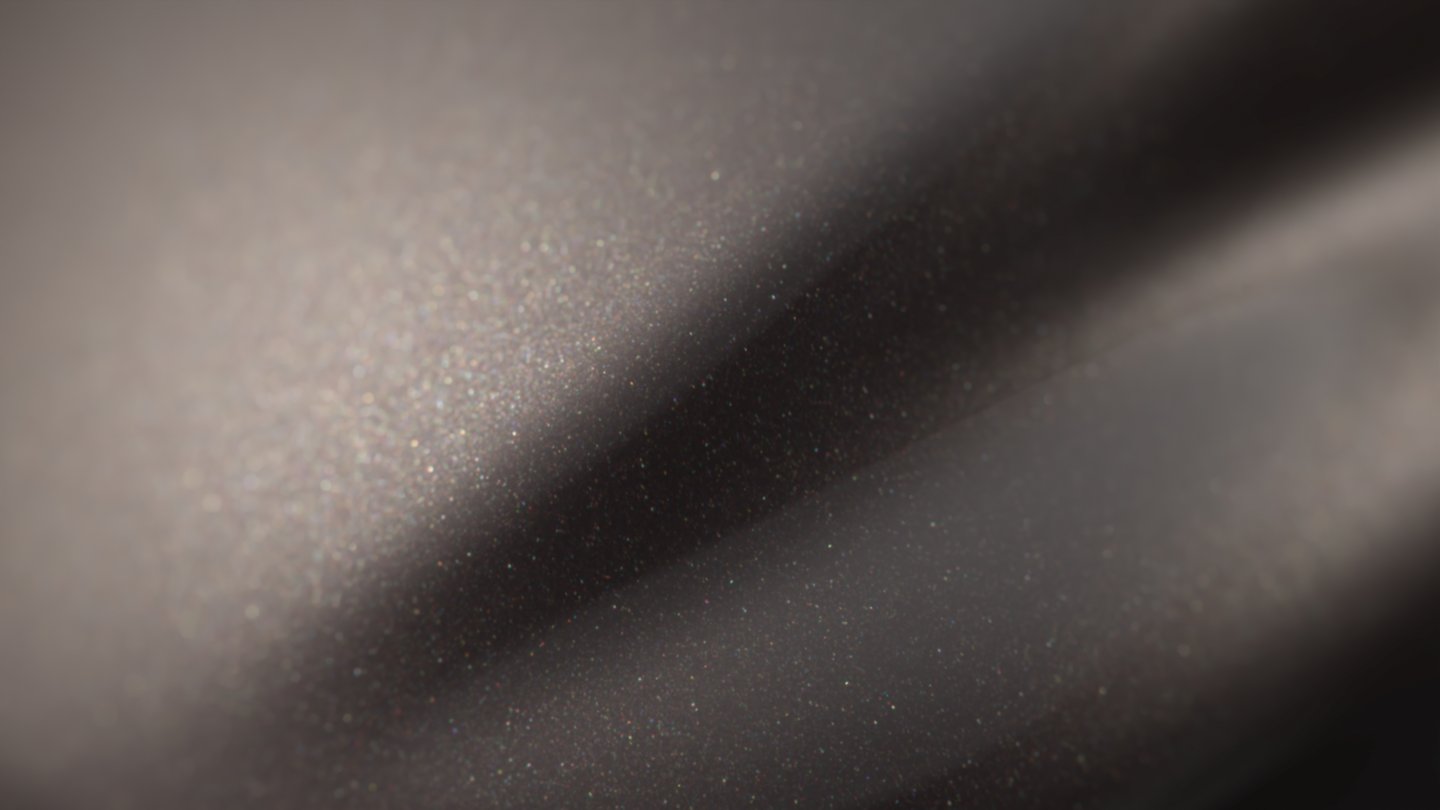
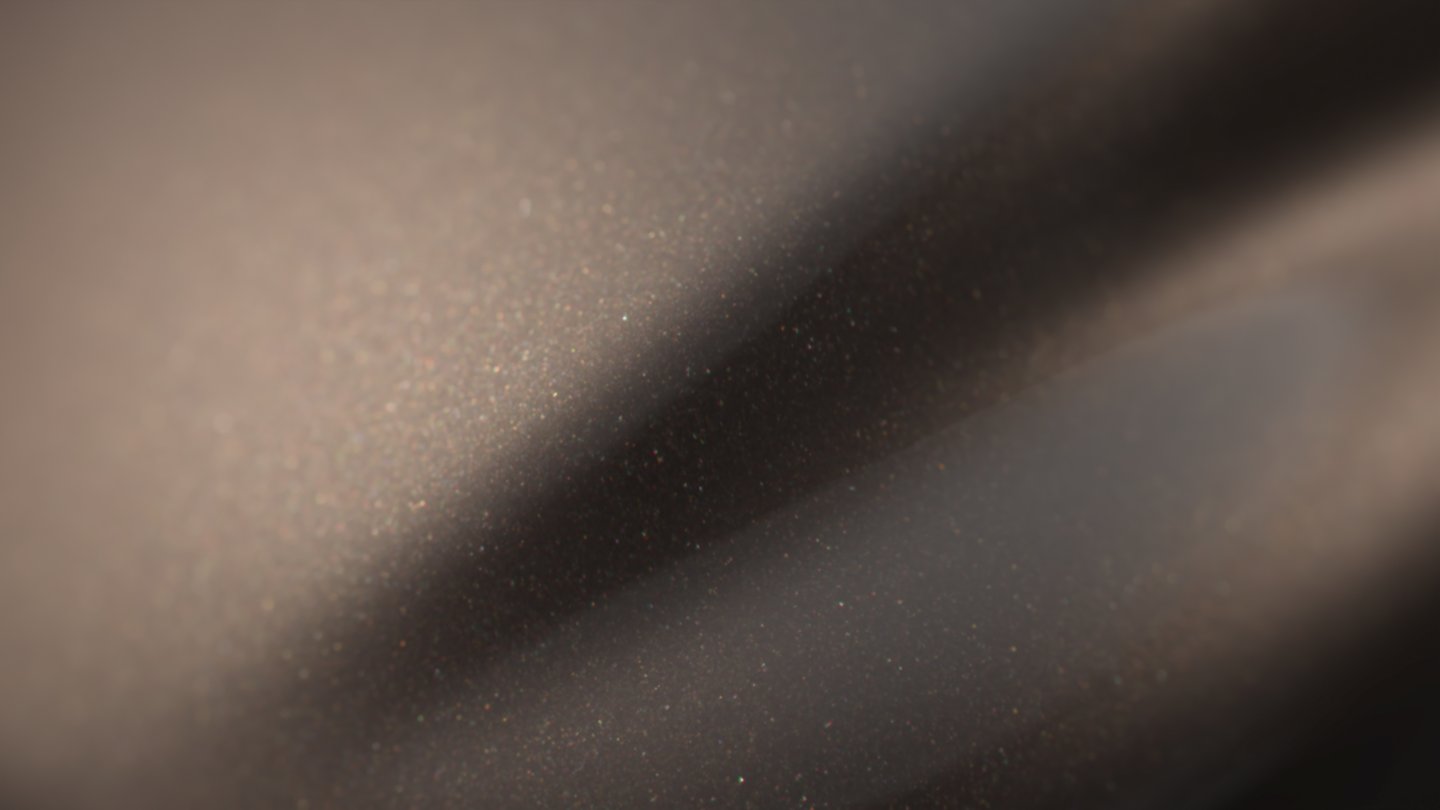
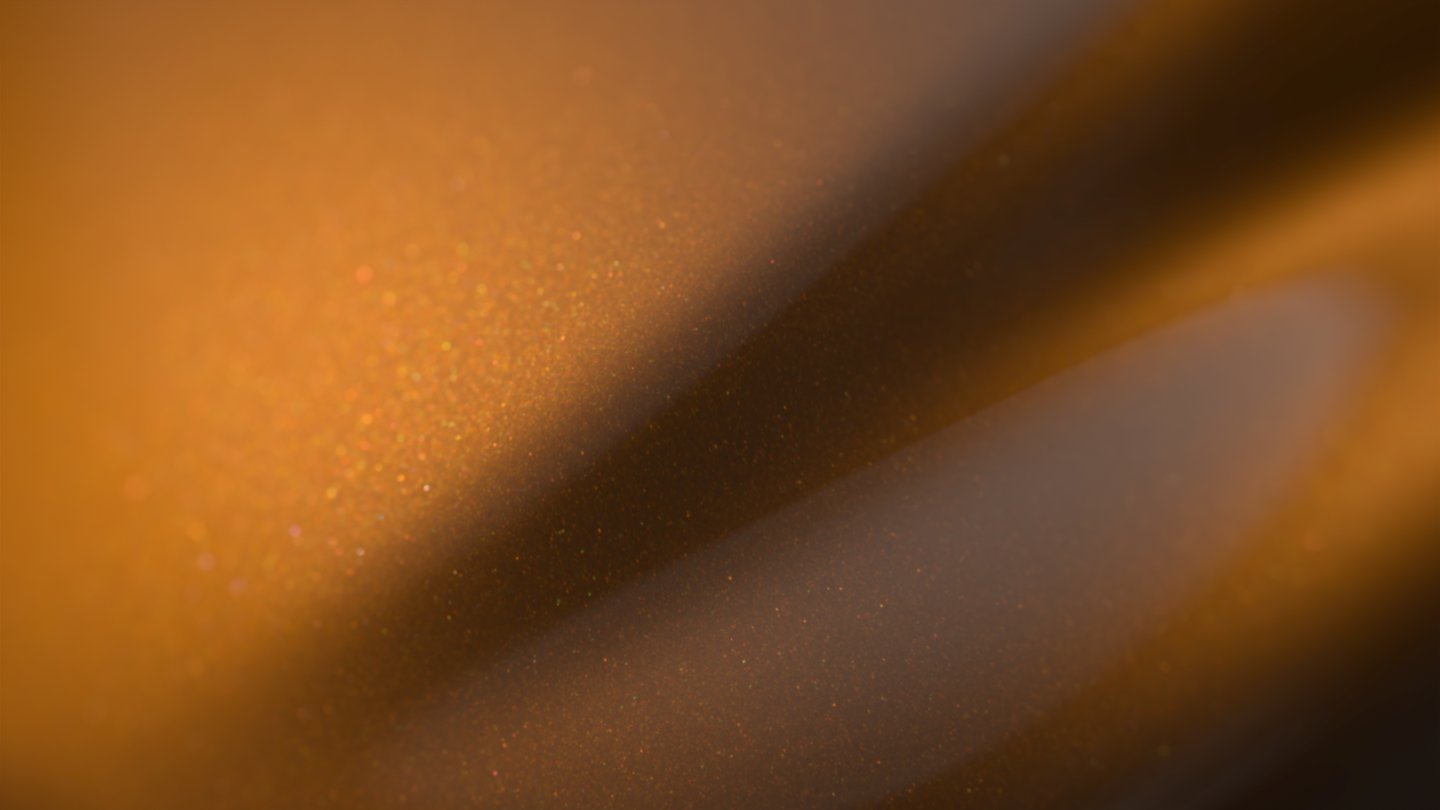
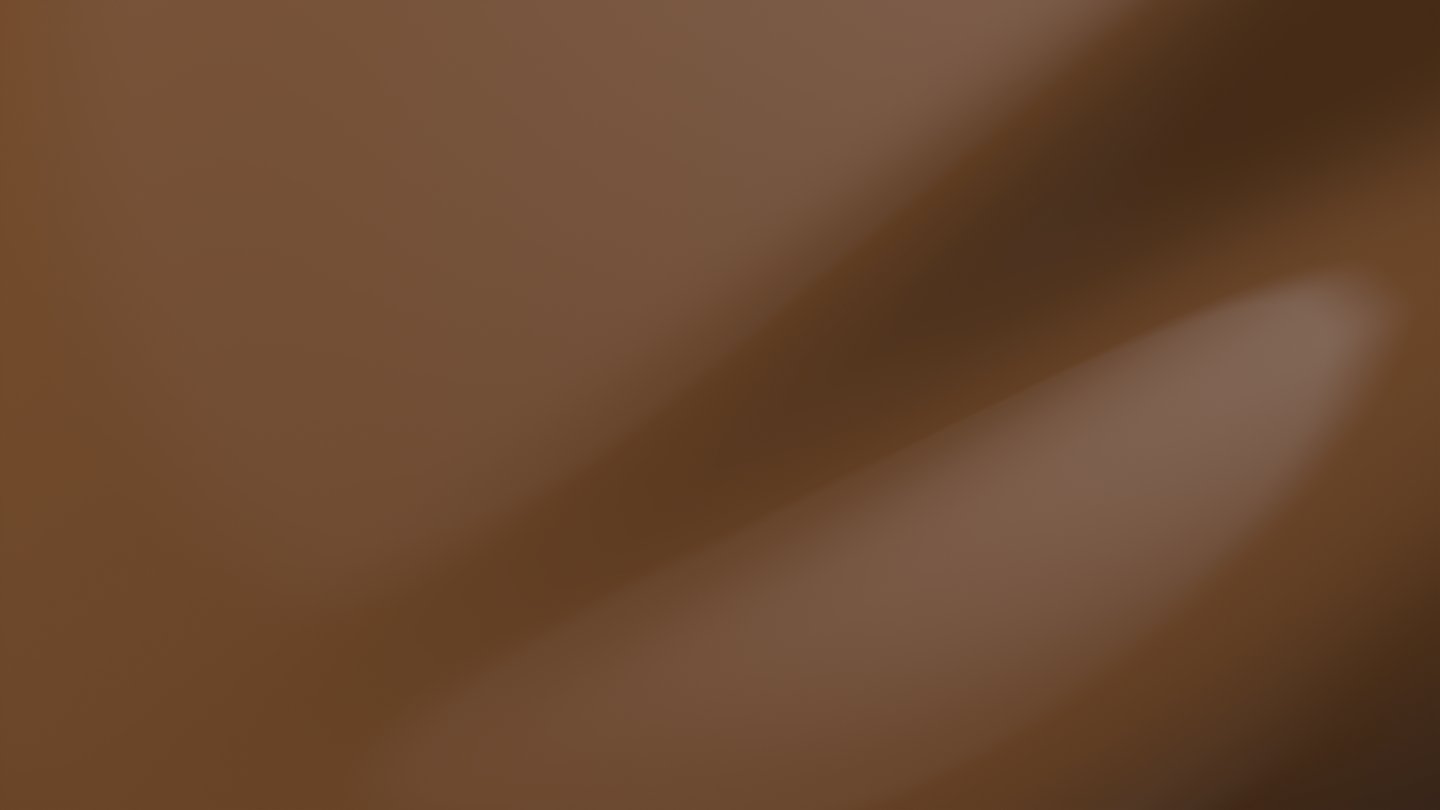
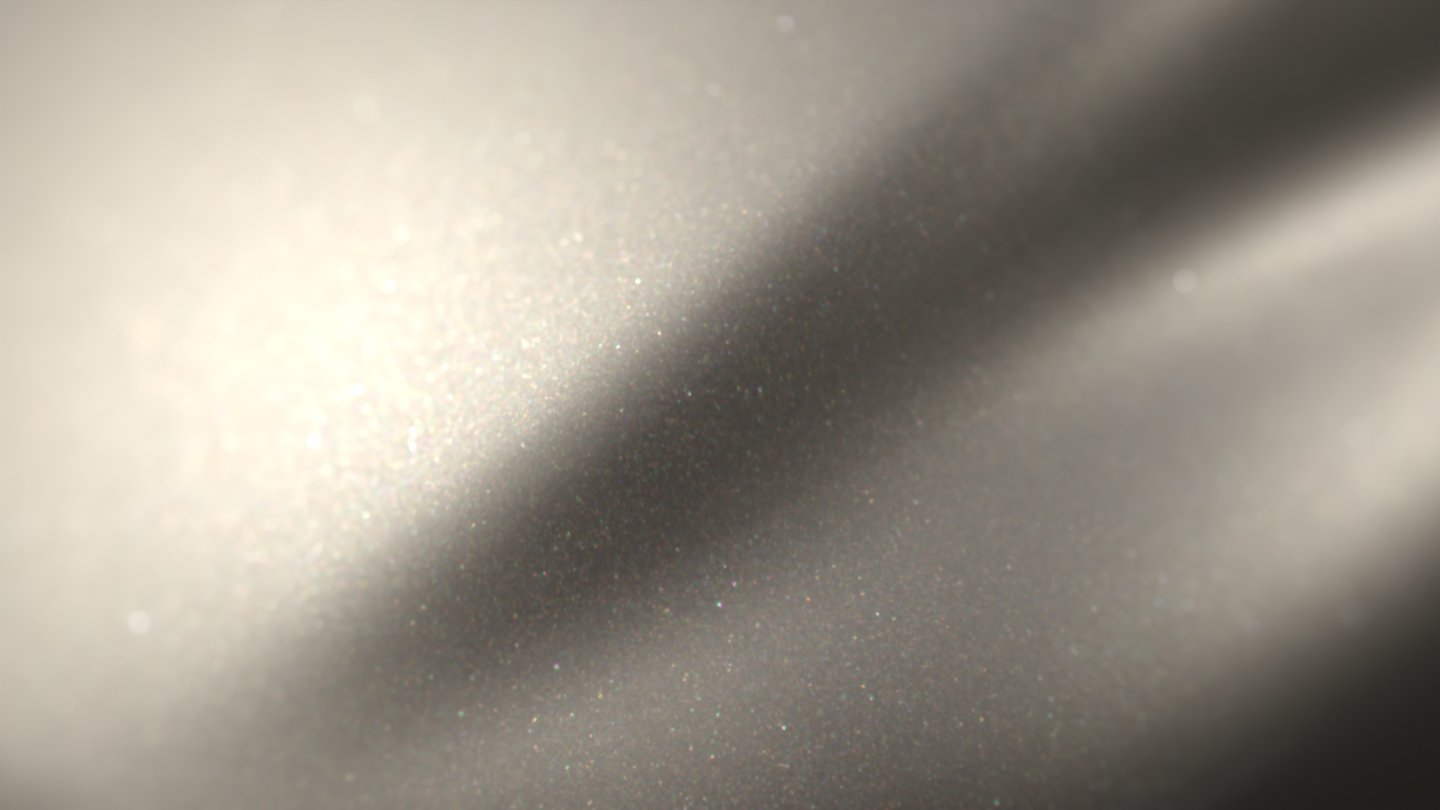
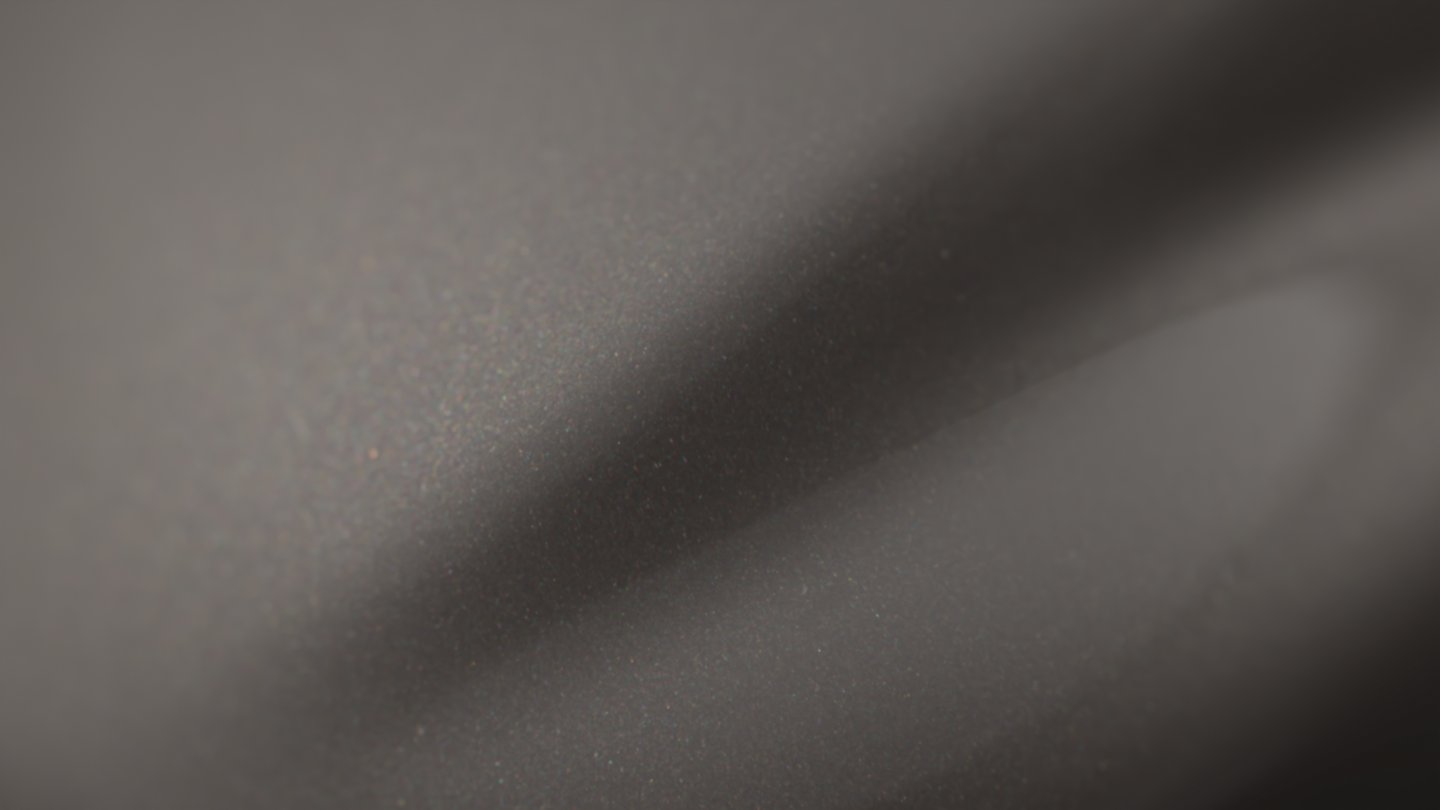
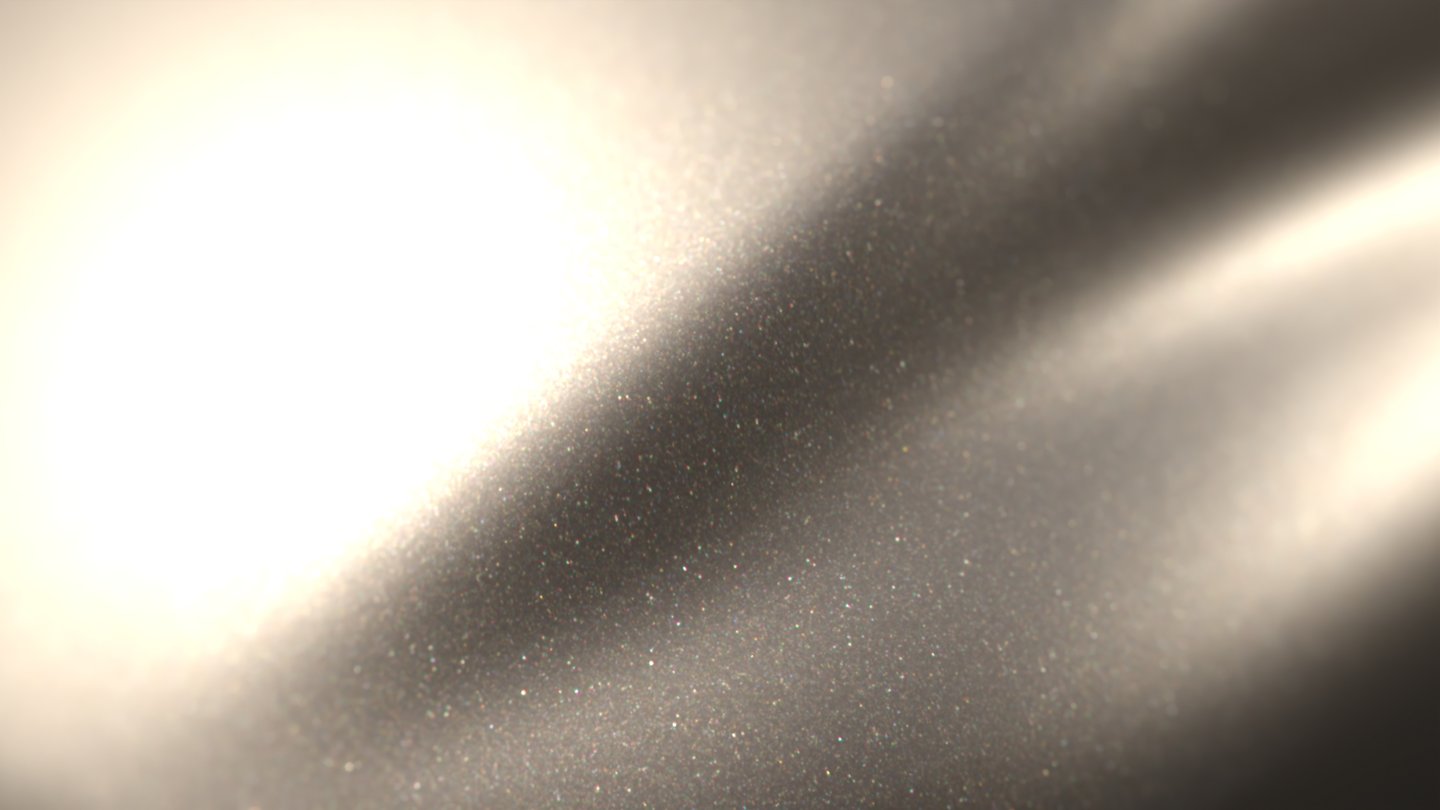
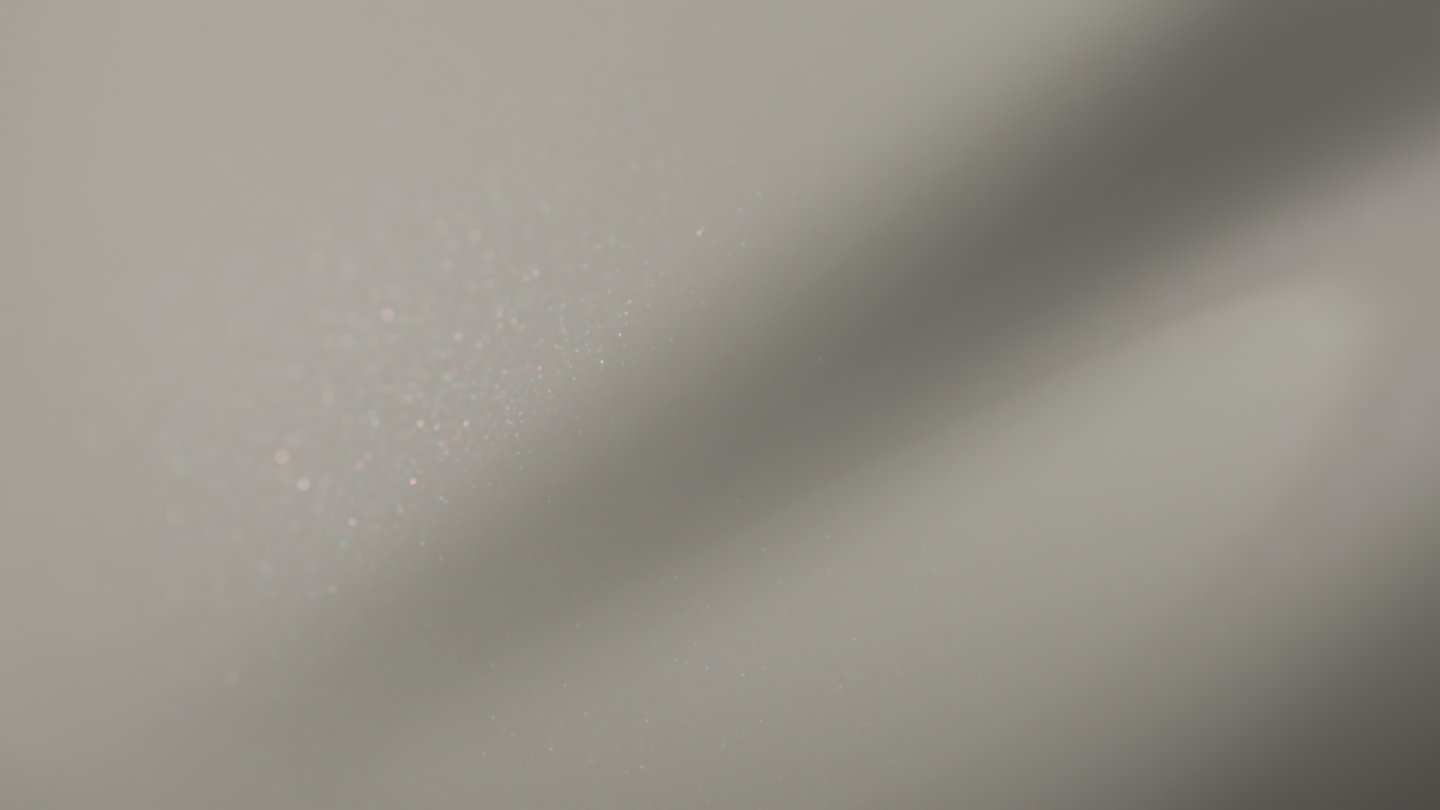
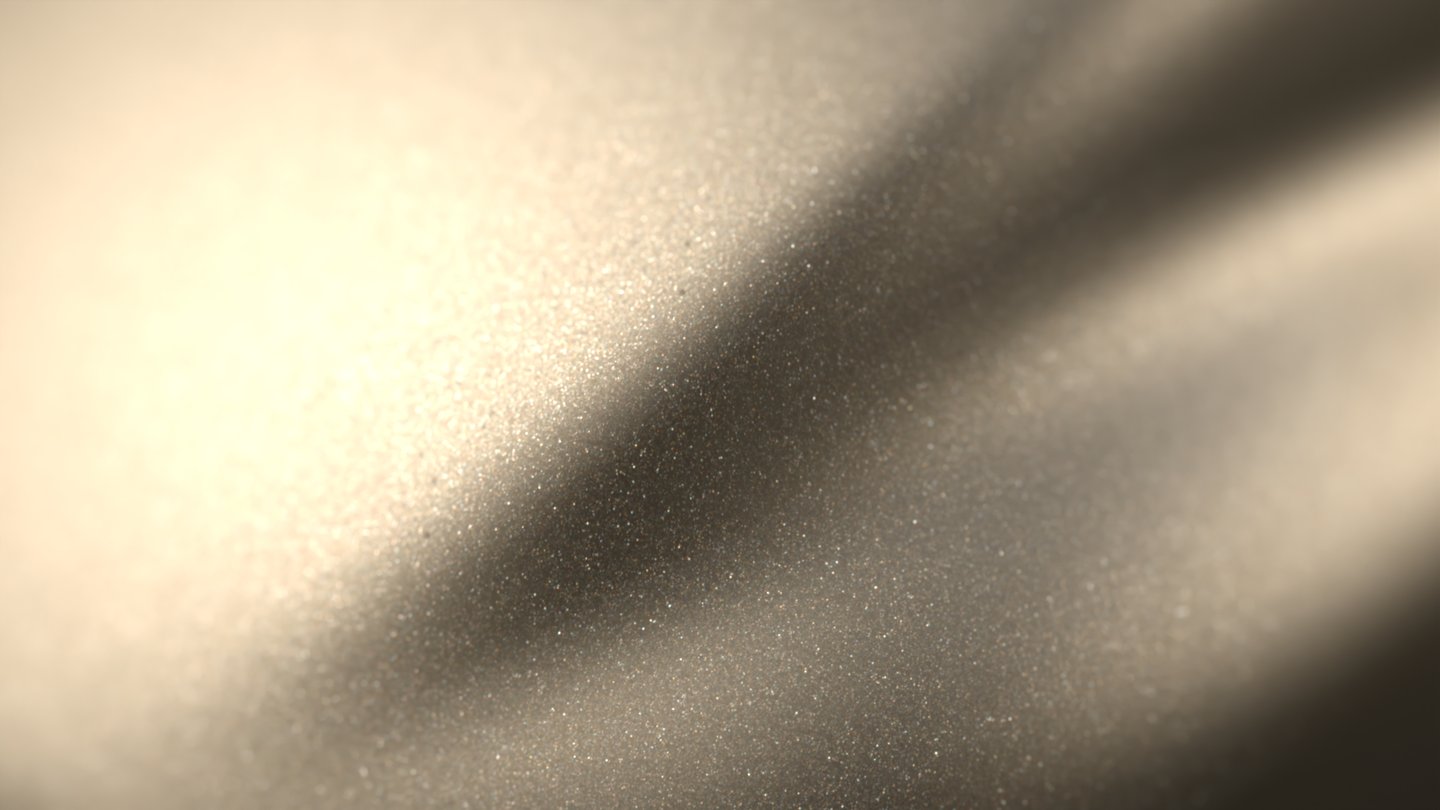
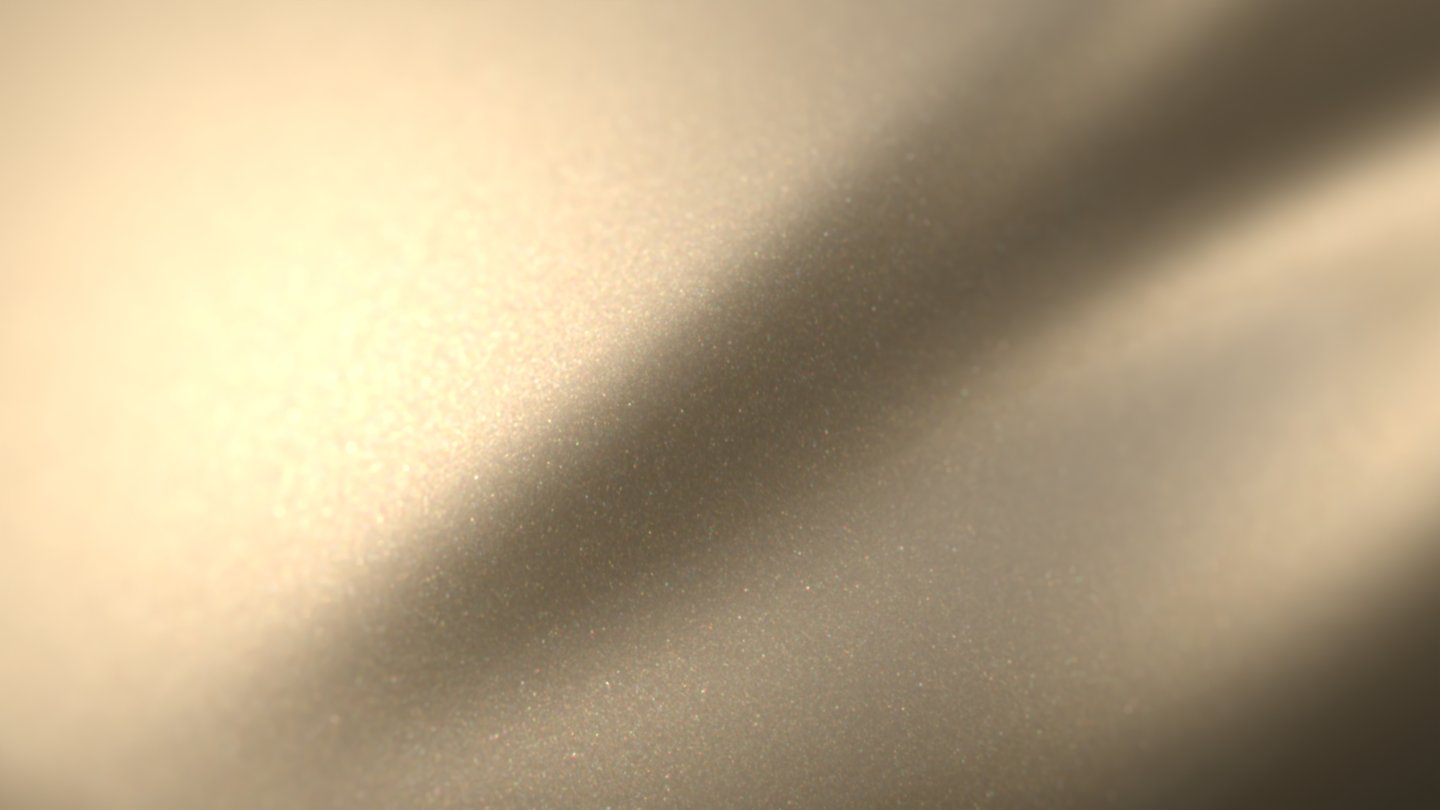
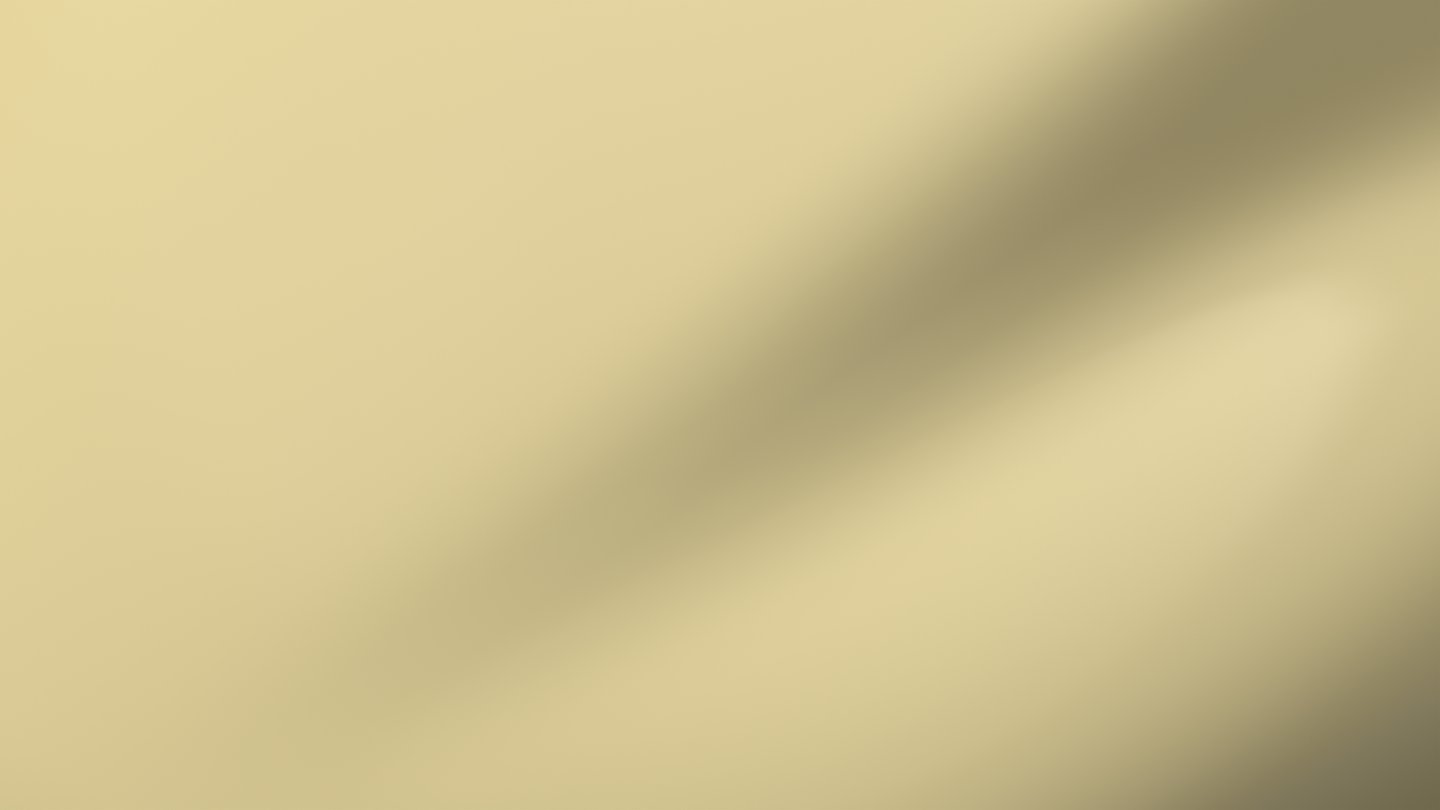
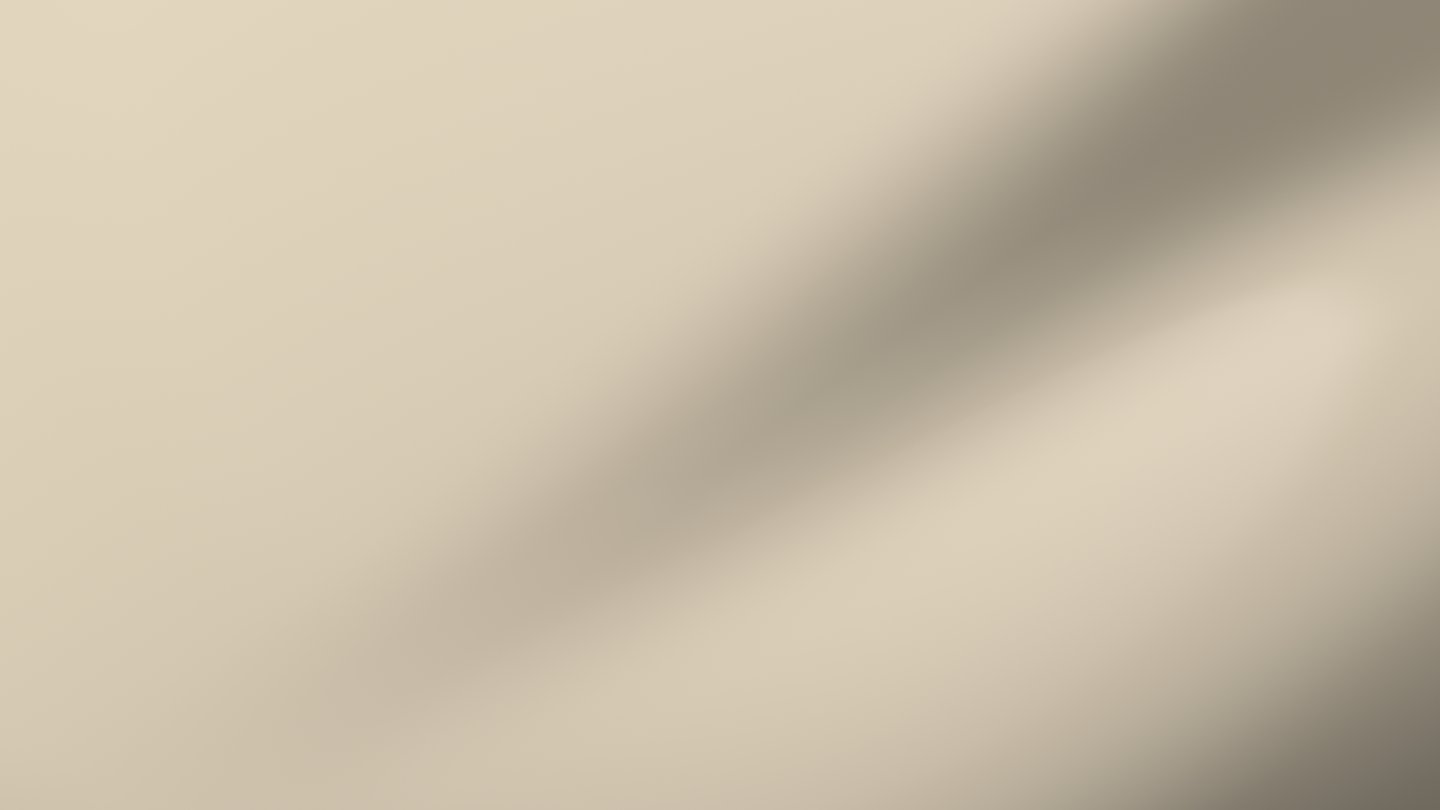
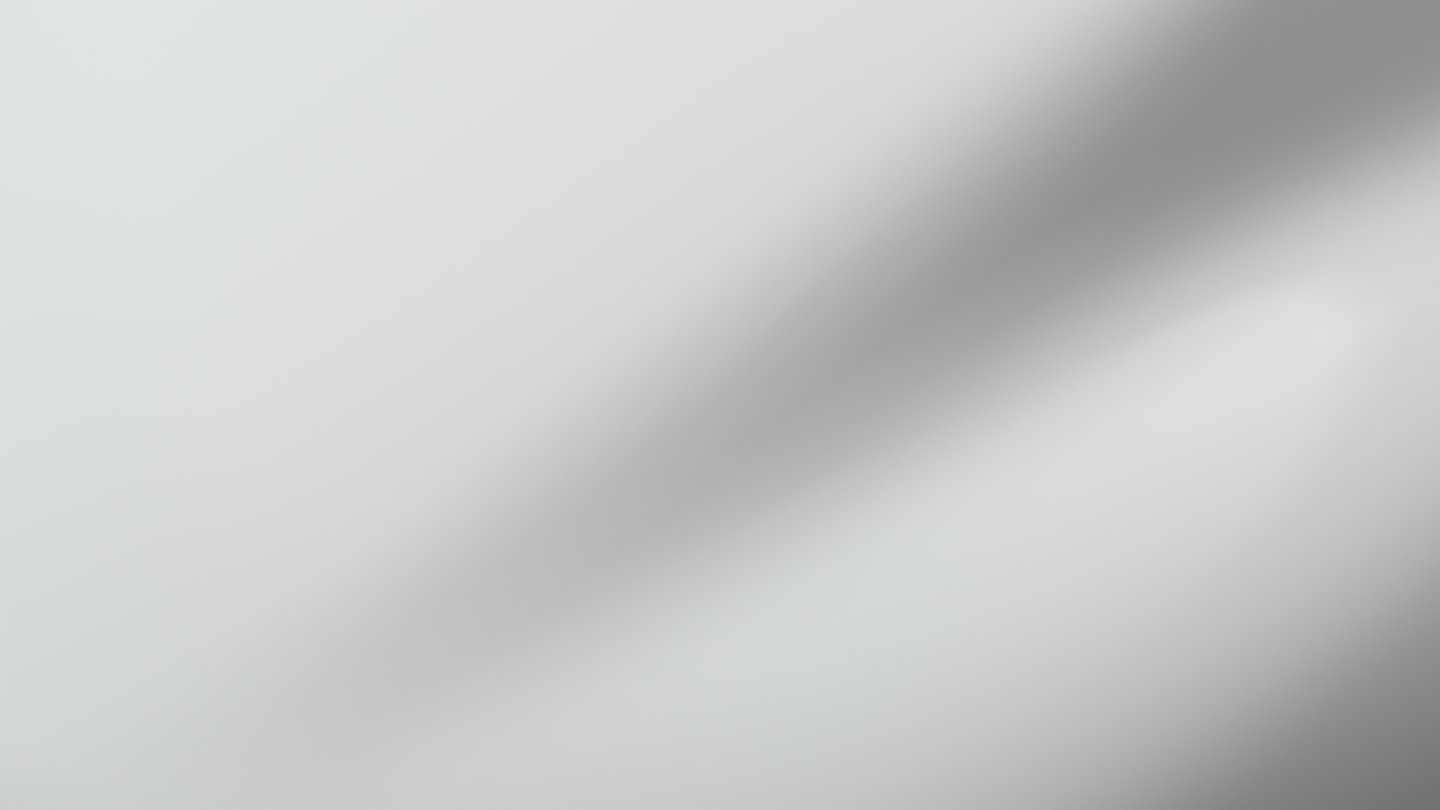
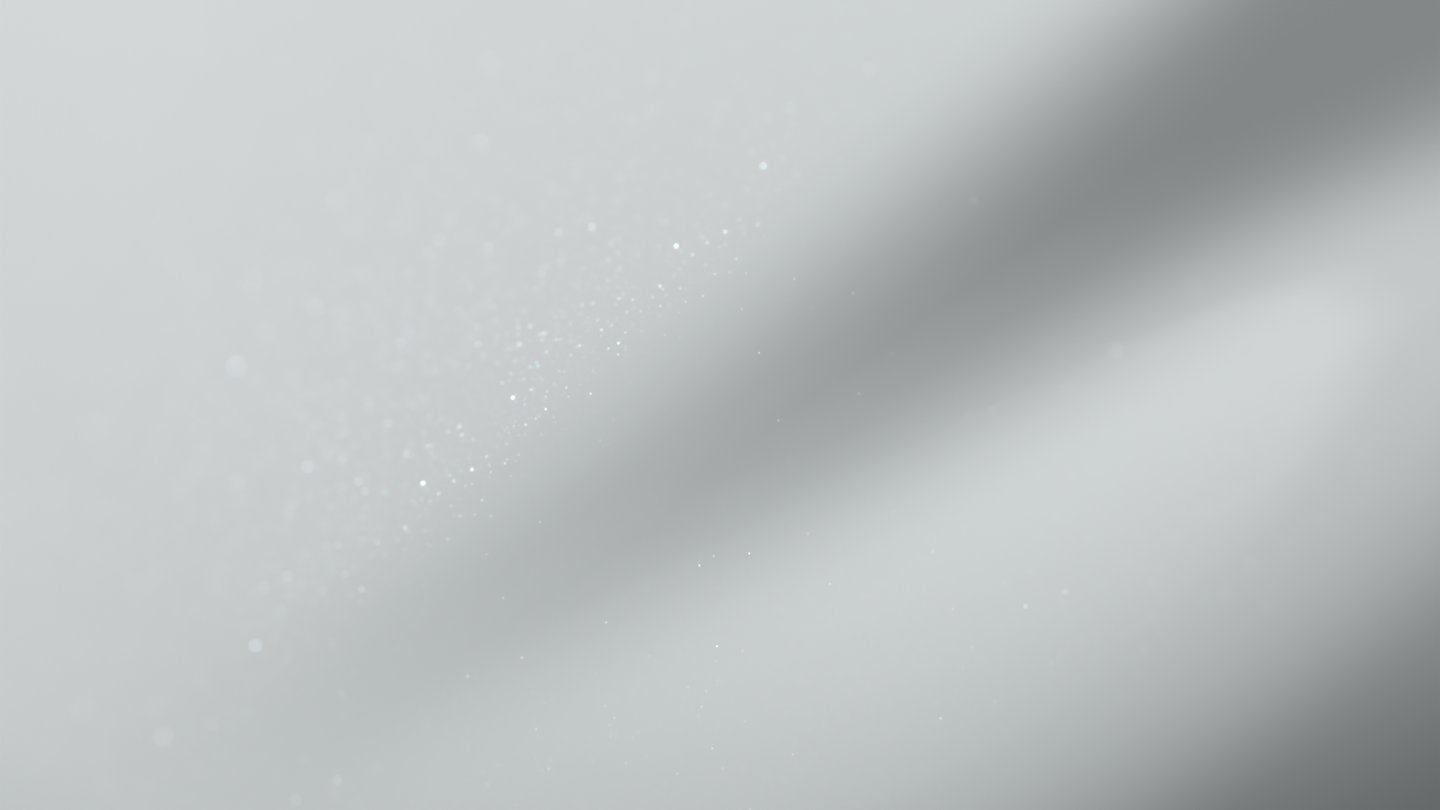
911 GT3 (2023): Fuel consumption* combined (WLTP) 13,0 – 12,9 l/100 km, CO₂ emissions* combined (WLTP) 294 – 293 g/km, CO₂ class G , CO₂ class combined G